good-to-know
How does a turbofan engine work?
High-tech down to the smallest component: modern aircraft engines are top-class technological products that must withstand extreme conditions. We explain how they work.
author: Isabel Henrich | 3 mins reading time published on: 29.01.2024
author:
Isabel Henrich
studied political science and communications. At MTU, she coordinates the editorial process of AEROREPORT and is responsible for the conception and development of its content.
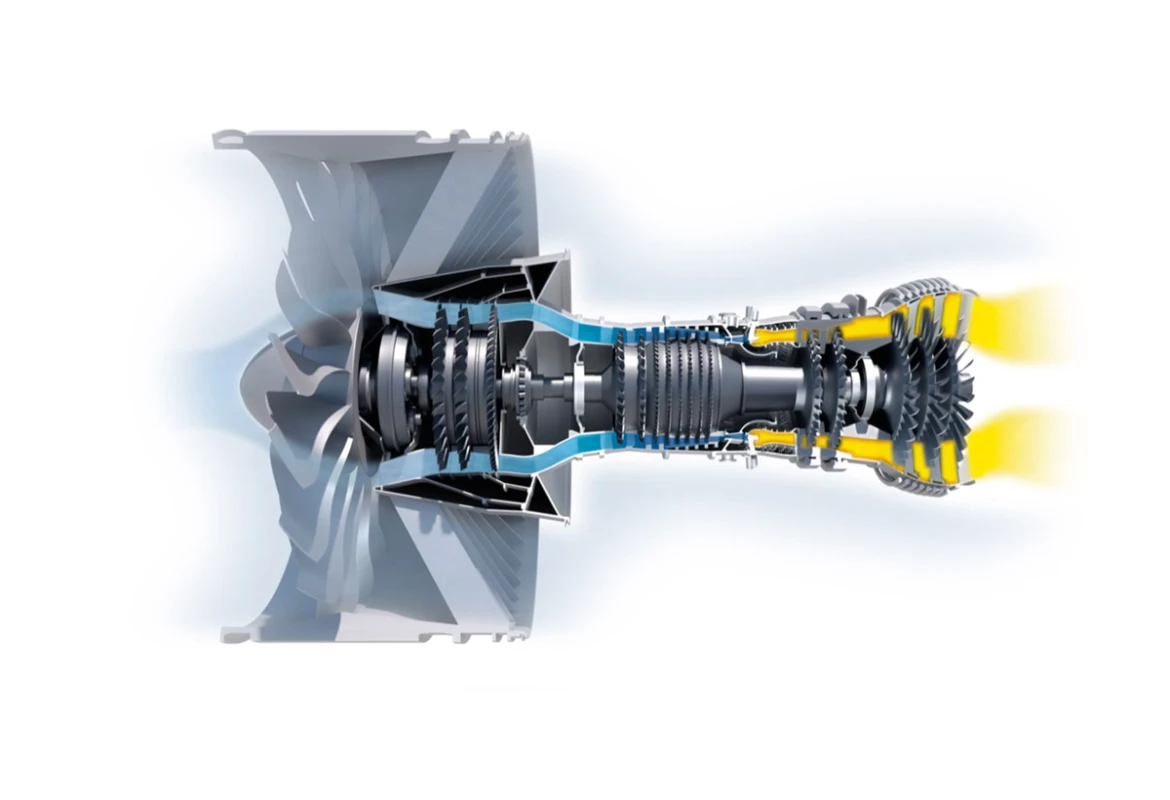
Aircraft engines are top-class technological products that must withstand extreme conditions. Different types of engine offer different advantages depending on the application. As the age of aviation dawned, piston engines with propellers were at the fore. Today, these are found almost exclusively on small and private aircraft. More power arrived in the form of the turboprop, which features a propeller driven by a gas turbine by way of a gearbox. Turboprop engines are particularly efficient at lower speeds of up to about 600 km/h, but in higher speed ranges, it is the jet engine that comes into its own.
The first jet engines were turbojets, also known as air-breathing jet engines with a turbine. These provided the basic design for future jet engines: air is drawn in through the engine inlet and fed into the compressor. There it is compressed by blades before being channeled into the combustor. Injection nozzles are responsible for creating a mix of fuel and air that is then combusted. The hot combustion gases expand explosively and flow at high pressure into the turbine, which in turn drives the compressor. These gases are then accelerated in a thrust nozzle, producing propulsion. Turbojet engines had their heyday in the years from the end of the Second World War to the mid-1960s, and were used for both commercial and military applications. Today, they are still occasionally used in some military aircraft types.
Achieving the desired amount of thrust relies on either greatly accelerating a small amount of air, or gently accelerating a large amount of air. The latter requires less energy, which led to the idea of the turbofan engine as a major improvement on the turbojet. In turbojet engines, all the ingested air flows consecutively through the compressor, the combustor and the turbines before being expelled at high acceleration. Turbofans, by contrast, separate the air flow so that only a fraction of the air passes through the compressor blades and into the combustor and turbines in order to drive the fan. The majority of the air gets compressed by the fan itself, generating the lion’s share of thrust at low acceleration in a separate nozzle. The ratio between these two airflows is known as the bypass ratio, which in the most advanced turbofan engines can be up to 12:1.
Huge technology leap: GTF
The geared turbofan (GTF), the latest generation of turbofan engines, has a special attribute: a reduction gearbox between the fan and the low-pressure shaft together with the low-pressure compressor and actuating low-pressure turbine. Thanks to this arrangement, all components can run at their optimum speed: the large-diameter fan slower, and the smaller-proportioned low-pressure compressor and low-pressure turbine considerably faster. This helps achieve lower fan pressure ratios, and hence higher bypass ratios. Consequently, the GTF has very high overall efficiency, substantially reducing fuel consumption and carbon dioxide emissions. In addition, the reduced speed of the GTF engine’s fan and exhaust gas stream means it has a significantly smaller noise footprint than conventional turbofan engines.
In this way, compared to the previous engine generation, the GTF family represents a reduction in fuel consumption and carbon dioxide emissions of 16 percent each and a noise footprint that is 75 percent smaller.
How a modern turbofan engine works in 4 stages
1. Ingestion
2. Compression
3. Combustion
4. Expulsion
1. Ingestion
The fan rotor, the blade wheel at the front, draws in air. While in turbojet engines, all the ingested air flows consecutively through compressors, the combustor and turbines, turbofans separate the accelerated air stream behind the fan rotor. Here, too, a certain amount of air passes through the compressor blades into the combustor. But the rest, known as the sheath flow, is not combusted; instead, it bypasses the interior assemblies and is expanded in a separate nozzle to generate the majority of thrust—up to 80 percent. This cold bypass flow surrounds the hot exhaust gases from the engine core like a sheath, ensuring a reduction in noise emissions.
2. Compression
Next, the portion of ingested air that flows into the engine core is compressed in the low- and high-pressure compressors. Also known as a booster, the low-pressure compressor is responsible for precompression. The high-pressure compressor handles main compression and offers a high degree of efficiency and low weight thanks to its innovative blisk principle, where the blades and disk are manufactured as a single part.
3. Combustion
After compression, the air flows into the combustor. This is where fuel-injection nozzles create a mix of fuel and air, which is then combusted at a temperature of approximately 1,700 degrees Celsius. The buildup of heat causes the gas to expand to several times its original volume and escape from the combustor at high energy.
4. Expulsion
The hot gas races through the high- and low-pressure turbines, each of which has several turbine wheels and numerous blades that are rotated by the exhaust gas stream. This causes the stream to expend up to 60 percent of its energy to drive the booster, compressor and fan. This happens by way of two concentric shafts—the outer shaft, which couples the high-pressure turbine to the high-pressure compressor, and the inner shaft, which connects the low-pressure turbine to the booster and fan. Only then do the combustion gases leave the thrust nozzle, generating an additional burst of residual thrust.