good-to-know
How does a turbofan engine work? – The structure of an engine
What role do compressors, turbines and the like play in an advanced turbofan engine? We explain the key functions of selected engine components.
author: Isabel Henrich | 3 mins reading time published on: 29.01.2024
author:
Isabel Henrich
studied political science and communications. At MTU, she coordinates the editorial process of AEROREPORT and is responsible for the conception and development of its content.
With up to 35,000 pounds of thrust, the PW1100G-JM, the modern engines from the Pratt & Whitney GTF™ engine family, can get an A320neo into the air.
The fan rotor, the clearly visible compressor rotor at the front, provides the main thrust. It is driven by the low-pressure turbine, which runs particularly fast in the GTF engine and ensures greater efficiency. This is made possible by the gearbox installed in the GTF, which decouples the low-pressure turbine and the fan from each other. This allows both to run at their optimum speed – the fan slower, the low-pressure turbine faster. Turbine, gearbox and fan are essential components of a modern turbofan engine. And what role do the compressor and combustor actually play?
Interact with our virtual geared turbofan engine either in 3D on your desktop or by projecting the engine digitally into your room with your smartphone.
For the “View in room” function, please note:
This feature allows you to integrate the virtual engine seamlessly into your environment. The application consumes a large amount of data, so we recommend that you use it only when on a wireless network. On some Android devices, display issues may occur. We recommend using the latest version of the Android operating system and the Chrome browser for an optimal experience."
Fan rotor
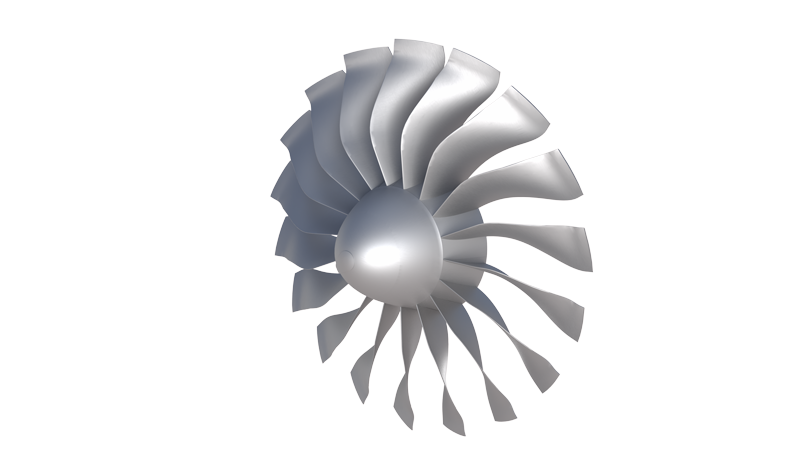
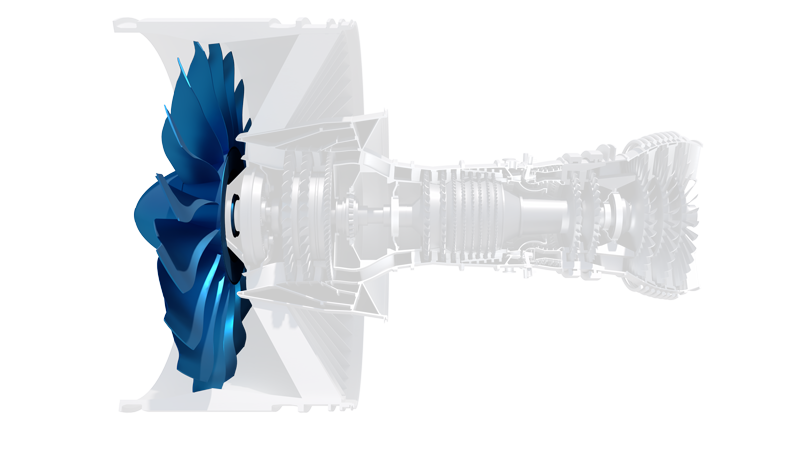
Fan rotor
The fan rotor is the first and very large rotor in the compressor. Its primary task is to accelerate a large mass flow of air in the bypass flow and thus provide the main thrust. The fan is driven by the low-pressure turbine via the low-pressure shaft. In the geared turbofan engine, the fan is optimized for maximum air flow.
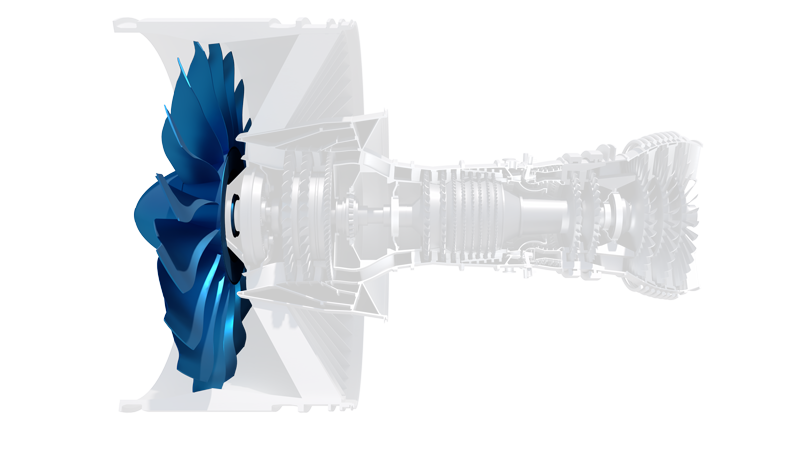
Did you know?
It’s always a special sight for the engineers when the fan blades of the Boeing 777 engine GE90 come to MTU Maintenance: these blades measure a full 1.25 meters and weigh 25 kilograms each.
Gearbox
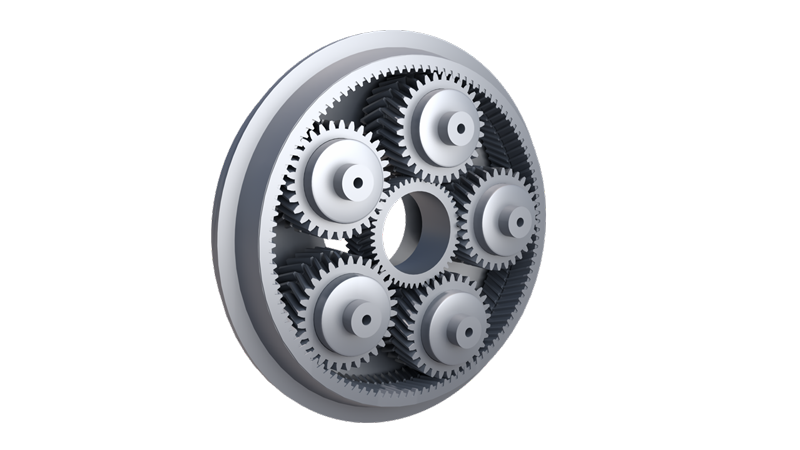
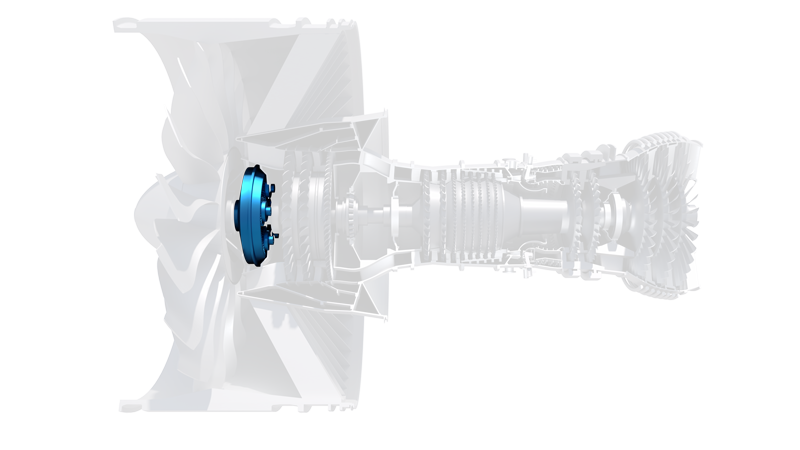
Gearbox
In conventional engines, the low-pressure turbine and the fan sit on one shaft, but here the gearbox decouples the two components. This lets the components run at their optimum speed: the large-diameter fan slower, and the smaller-proportioned low-pressure compressor and low pressure turbine considerably faster. The gearbox is a planetary gear train with a reduction ratio of 3:1 or higher.
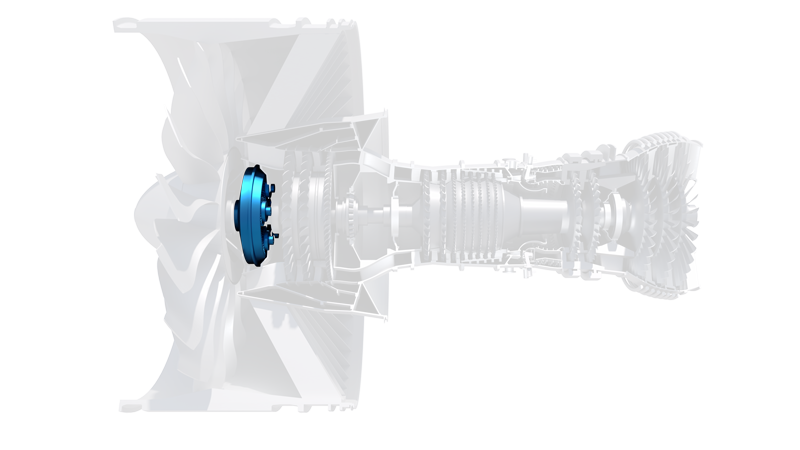
Did you know?
Pratt & Whitney, MTU and Fiat Avio began their first preliminary studies into a geared turbofan in the 1990s.
High-pressure compressor
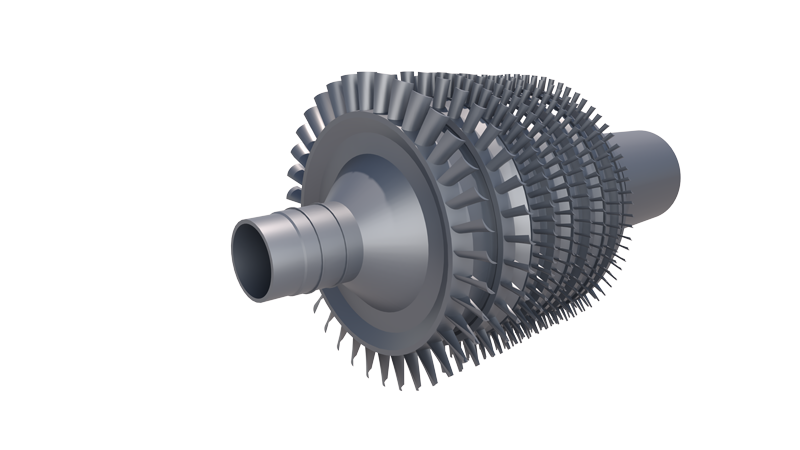
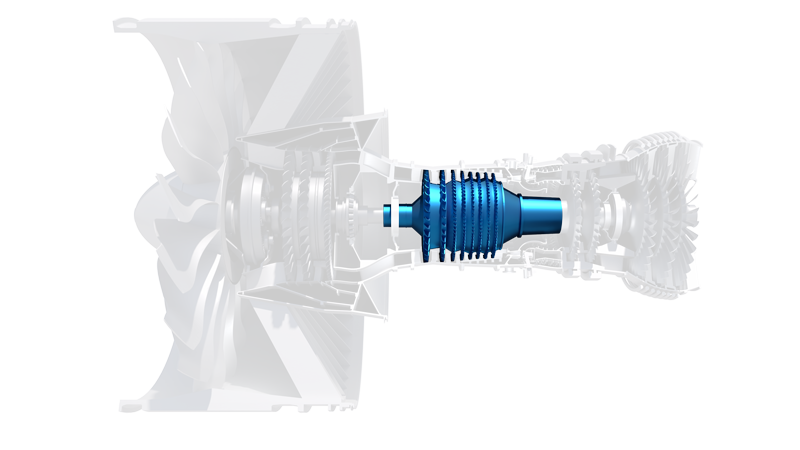
High-pressure compressor
The highly efficient high-pressure compressor handles main compression. What sets an advanced turbofan engine apart is that the blades and disk are manufactured as a single part—known as a “blisk.” These high-tech components not only save space and weigh less than conventional rotors with individual blades, but they also provide for better blade aerodynamics. Furthermore, they reduce assembly work and thus costs.
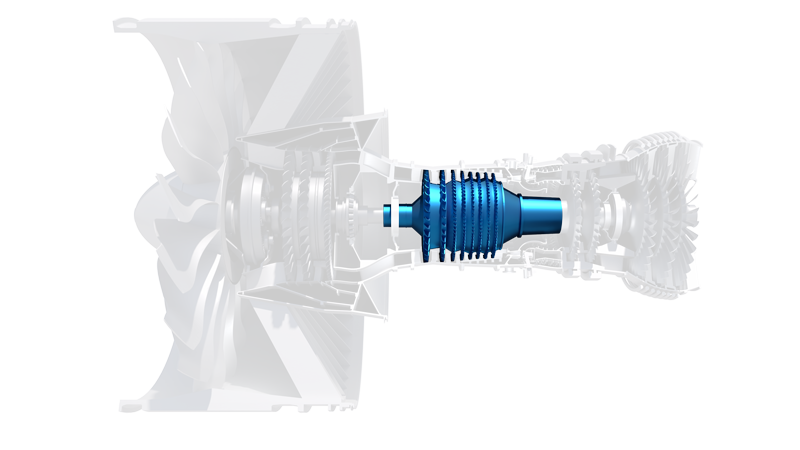
Did you know?
MTU built a specially designed shop for blisk production at its Munich site, where it manufactures up to 5,000 blisks a year.
Low-pressure compressor
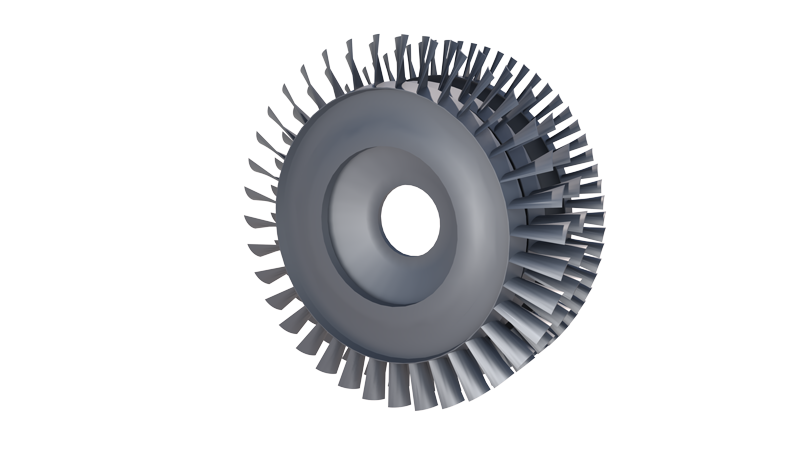
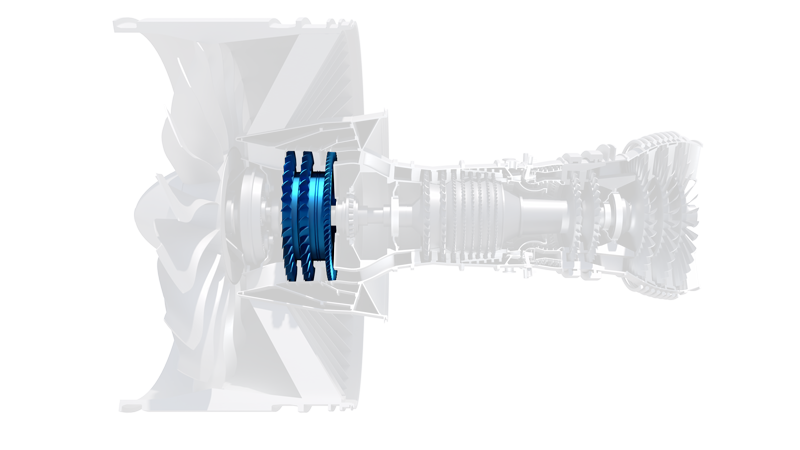
Low-pressure compressor
The task of this compressor is to ingest air and compress it before it is fed into the combustor. Advanced engines have both a low-pressure and a high-pressure compressor. Also known as a booster, the low-pressure compressor is responsible for precompressing the air. Developing the technology to extend the operating range and manufacturing the blades out of composite materials to reduce the overall weight will deliver further improvements.
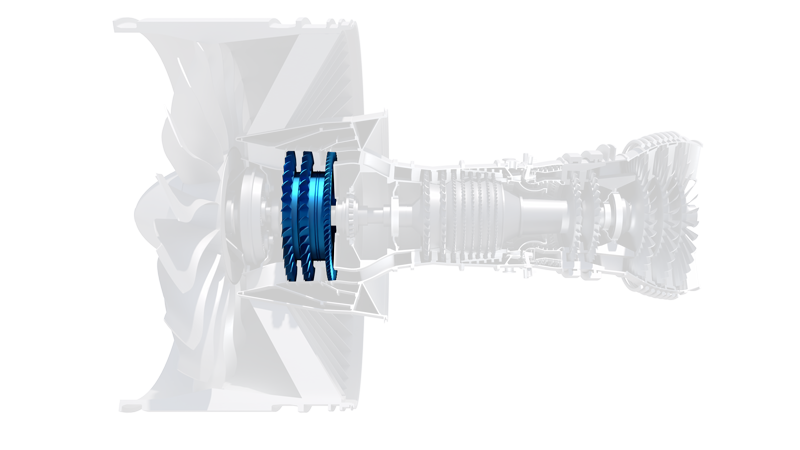
Did you know?
The low-pressure compressor of the EJ200, the Eurofighter's engine, is the first compressor with a blisk design ever to go into production. MTU developed linear friction welding at that time specifically for manufacturing the blisks.
Combustor
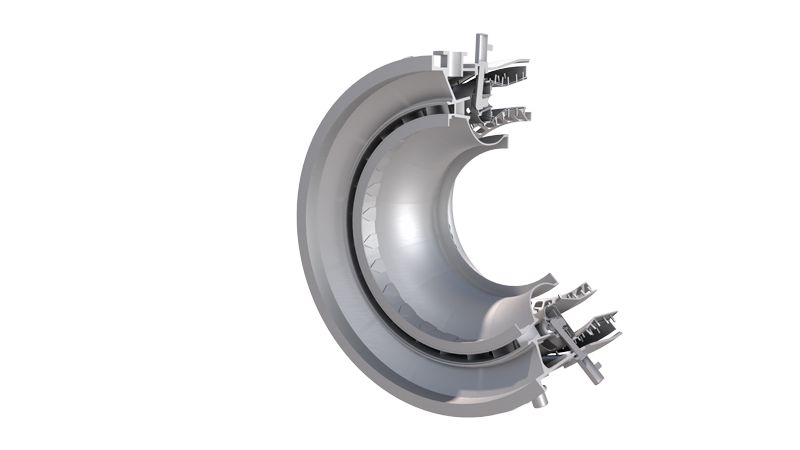
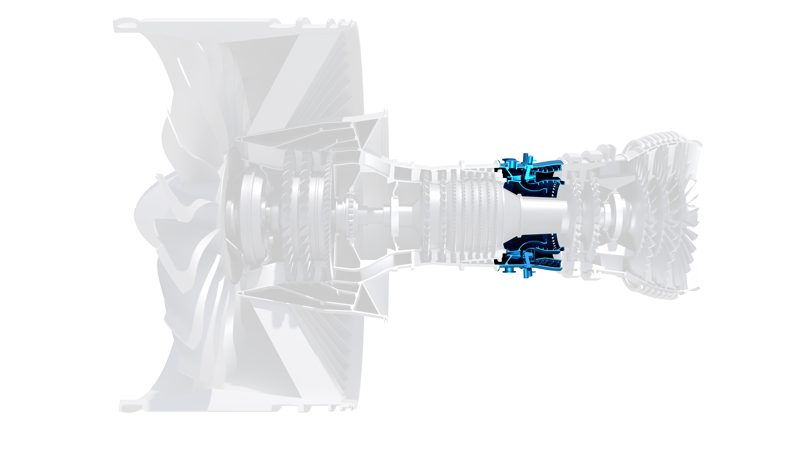
Combustor
Inside the combustor, the compressed air flowing into the chamber is mixed with fuel, where it burns at a temperature of about 1,700 degrees Celsius. New combustor concepts with lean combustion are being developed to reduce nitrogen oxide emissions; they require advanced cooling concepts.
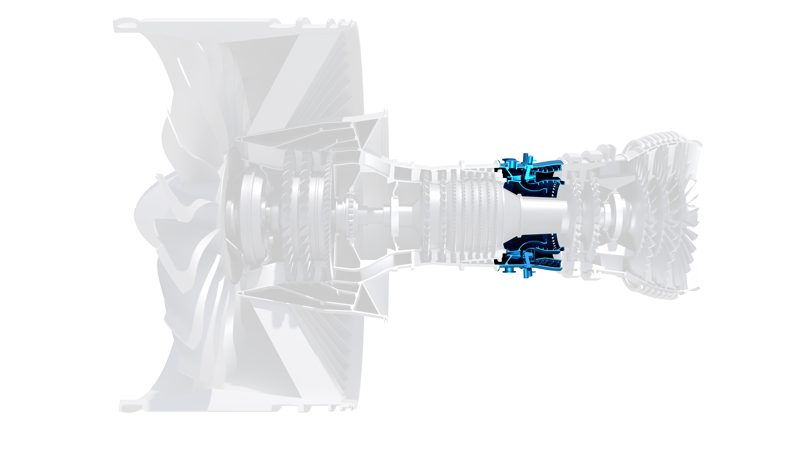
Did you know?
MTU developed a special laser-welding technique for repairing the combustor insert for the T64 engine, which is used, for example, in the Sikorsky CH-53 transport helicopter. This method was then adapted to other engine programs.
High-pressure turbine
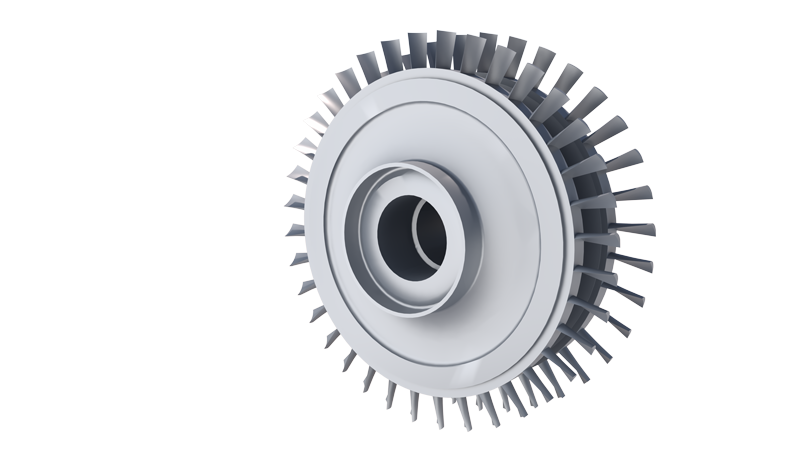

High-pressure turbine
In a turbine, the energy contained in the gas flow emerging at high pressure and temperature from the combustor is converted into mechanical energy. The turbine is divided into high pressure and low-pressure sections: the high-pressure turbine drives the high-pressure compressor. Advanced technologies such as new materials, new cooling concepts and air cooling will help to further increase the engine’s efficiency in the future.

Did you know?
MTU has been manufacturing high-pressure turbine parts for the GP7000 since the program was launched in 2005. The two-stage design of the high-pressure turbine powering the A380 mega-liner is based on the GE90 - the engine for the Boeing 777.
Low-pressure turbine
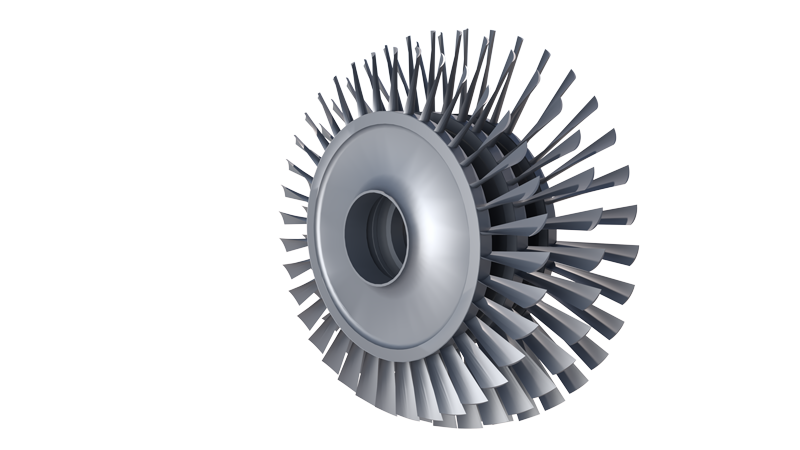
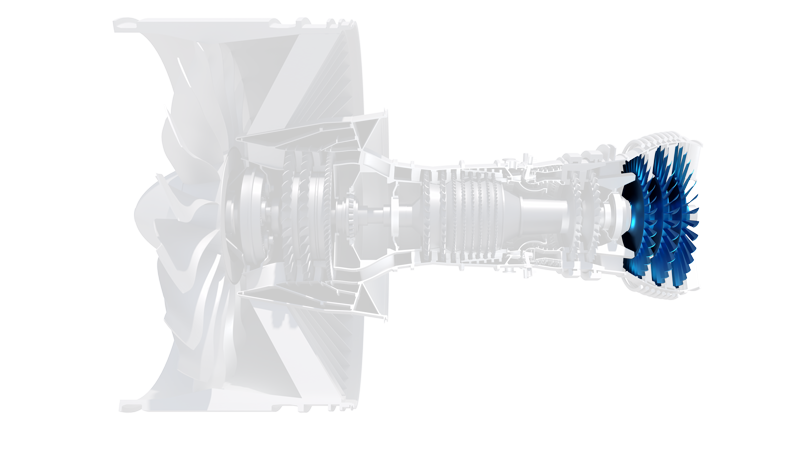
Low-pressure turbine
The low-pressure turbine drives the low-pressure compressor and the fan that in turn generates the bulk of the thrust. The GTF’s low-pressure turbine rotates much faster than that of a conventional turbofan engine. This makes it possible to significantly reduce the number of stages and thus the size and weight of the engine.
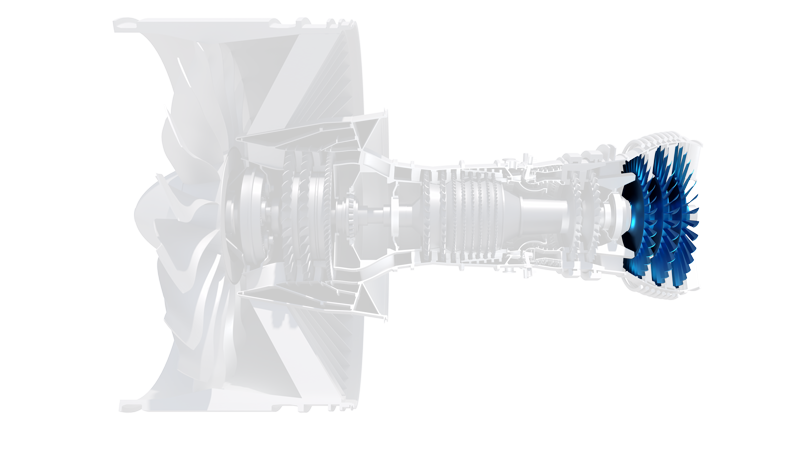
Did you know?
MTU has won two German innovation awards for the high-speed low-pressure turbine. It is the only company in the world to have mastered this technology in series production.