innovation
A robot for borescope inspections
Inspecting without disassembly: In the future, a flexible miniature robot will make it possible to use a borescope even in areas of an engine that were previously difficult to access.
author: Nicole Geffert | 5 mins reading time published on: 13.04.2023
author:
Nicole Geffert
has been working as a freelance journalist covering topics such as research and science, money and taxes, and education and careers since 1999.
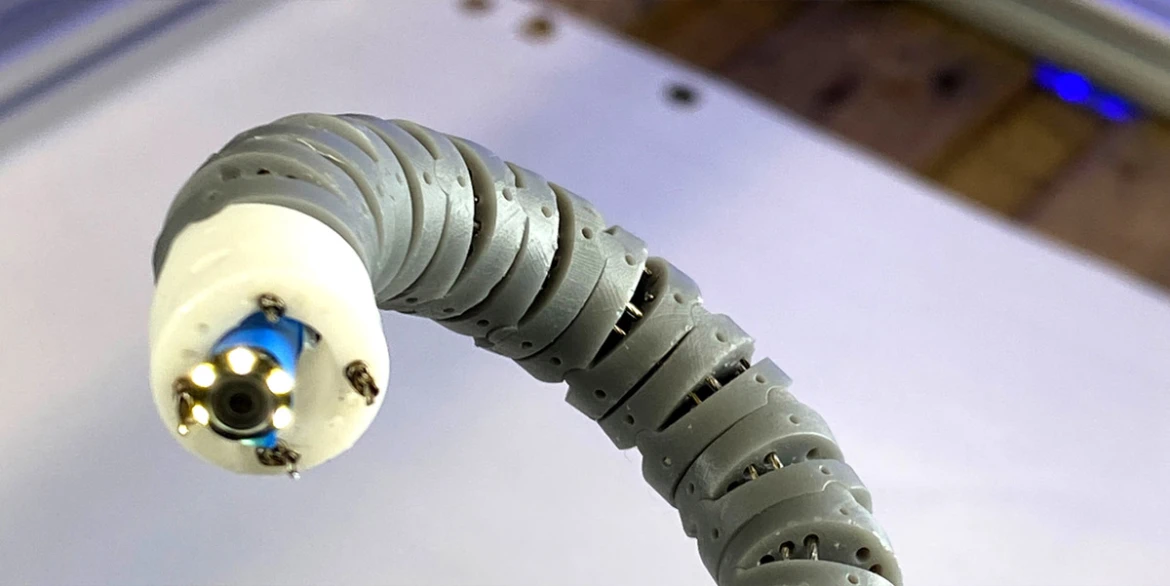
With a steady hand and a trained eye—that’s the only way to inspect the inside of an engine using a borescope in order to check the quality of components or the wear and tear on them. This visual inspection of cavities that are difficult to access is called borescopy, from the word “bore” meaning “to drill into.” The procedure is very complicated and requires experienced inspectors.
One of them is André Laukart, a borescope inspection expert at MTU Maintenance Hannover. “Before disassembling an engine, we use a borescope to identify any hidden damage inside, so we can more precisely estimate how much of the engine we have to take apart and how much effort the repairs will entail,” he says. “This allows us to clarify the scope of work with the customer at an early stage before disassembly starts.”
“The borescope lets us get to rotating components such as rotor blades, but we can reach the stator of a high-pressure compressor only with difficulty, if at all.”
Borescope inspection expert at MTU Maintenance Hannover
But the experts are reaching their limits. “The borescope is a flexible instrument, but the probe head with the camera can move in only four directions. That’s not flexible enough to get the camera into all the positions we need,” Laukart says. It’s also not possible for the stiffened tube to make several turns inside the engine, although this is precisely what would be needed to access the deeper components in the more highly compact engines.
Laukart gives an example: “The borescope lets us get to rotating components such as rotor blades, but we can reach the stator of a high-pressure compressor only with difficulty, if at all.” But to inspect any damage there, the probe has to get as close to the component as possible. In addition—despite all the care and expertise—there’s always the risk the borescope will get hung up on a component in a narrow space as it’s being retracted.
Multi-jointed segments instead of conventional joints
Scientists Tim-David Job and Martin Bensch from the Institute of Mechatronic Systems at Leibniz University Hannover are also interested in this topic. The two robotics specialists learned from Laukart’s firsthand experience and from viewing the engine themselves where the borescope technique is reaching its limits. “For us, these insights and direct discussions with the expert are enormously important,” Job says. That’s because they believe their research can provide a remedy.
In cooperation with MTU, the scientists are developing a robot-assisted borescope nicknamed “RoBokop.” Dr. Manuel Voit and Jörg Windprechtinger, experts in automation and production processes at MTU Aero Engines, and their team are in close contact with the scientists. “The first prototype of the miniature robot was created after a year and a half,” Voit says.
What distinguishes the RoBokop from a conventional borescope? “The miniature robot has bionic structures that let it move like a snake. Instead of conventional joints, it has multi-jointed segments that allow continuous movement. That’s why it’s also called a continuum robot,” Windprechtinger explains. As a result, the RoBokop is much more flexible than the rigid borescope. “That means we can reach components deep inside the engine and have the camera capture areas that were previously inaccessible.”
But before the RoBokop can go into operation for the first time, this innovative process will be researched on a much larger scale in the lab. The model that Job and Bensch built themselves has been scaled up by a factor of 2.5, making it easier for the scientists to conduct their experiments. Miniaturizing the RoBokop is the next step. “The challenge is the dimensions required,” Bensch says. “The RoBokop is supposed to have a diameter of only 6 millimeters and a length of up to 1.80 meters.”
Skeleton structure with wire ropes
The required dimensions also influenced the decision on how to build the continuum robot’s skeleton. “There are a few different concepts to choose from, such as micromotors or fluids,” Job says. The scientists settled on wire ropes as actuators because they are easy to miniaturize. Guided by disks, these wire ropes are used to exert a force on the metal rods that form the backbone of the RoBokop. On the inside, the miniature robot is hollow to provide space for the camera cables and leads plus the measurement system.
In the future, the RoBokop could provide valuable services not only in the maintenance shop but in on-site operations as well. Whenever possible, MTU Maintenance’s mobile teams perform borescope inspections and engine repairs directly on the wing. Since this avoids unexpected costs, it is particularly attractive for customers.
Another major advantage of the RoBokop is that it lets components such as blades be examined in a reproducible manner. In other words, the miniature robot can be used to target specific points on a blade multiple times. This is much more difficult with the stiff tube of the conventional borescope. Bensch explains it like this: “Anyone who’s ever tried to pull a long cable out from under a sofa or cabinet and then push it back to exactly the same position knows how such a job ranges from tricky to impossible.”
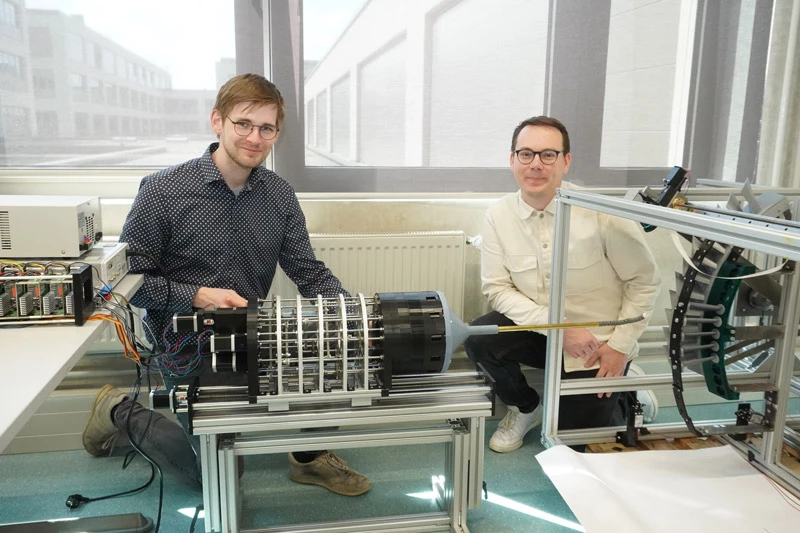
Robotics specialists: Scientists Martin Bensch (left) and Tim-David Job from the Institute of Mechatronic Systems at Leibniz University Hannover are developing the robot-assisted borescope in cooperation with MTU.
Automated inspection process
As soon as it’s ready for use in engine maintenance, the RoBokop will be controlled by the borescope experts at MTU Maintenance. “We still have a classic human-machine interface here,” Voit says. MTU Maintenance experts could operate the RoBokop using, say, a joystick or a tablet, while they concentrate on the monitor to assess the damage. “Evaluating an engine’s condition and analyzing any damage are demanding tasks that will continue to be performed by our maintenance specialists,” he says.
But research teams are already targeting more distant goals. One is to completely automate the currently subjective inspection process, including damage analysis and damage repair. A prerequisite for this is also an advanced measurement method. Here, too, MTU is looking to its collaboration with Leibniz University Hannover, specifically with the Institute of Measurement and Automatic Control.
“3D Endoscopy and Damage Detection in Narrow Structural Spaces” is the name of the transfer project that launched in 2023. It is funded by the Deutsche Forschungsgemeinschaft (DFG, German Research Foundation) and originated from Collaborative Research Centre 871. MTU Maintenance Hannover is an industrial partner in this transfer project. “We make sure that the results from the basic research are fleshed out in more detail and transferred into industrial application,” says Dr. Jörn Städing, who is responsible for MRO technology and digitalization management at the MTU Maintenance network.
Technology development certainly isn’t standing still in maintenance either, as Städing points out: “On the contrary, we’re going to further optimize our overall process in the MRO sector and make it even more efficient. What’s more, technological progress can also enable entirely new MRO offerings—for example, in the form of special maintenance services with RoBokop and an innovative measurement system.”