innovation
Ein Roboter für die Boroskopie
Inspektion ohne Demontage: Ein flexibler Miniatur-Roboter soll künftig das Boroskopieren auch in bisher nur schwer zugänglichen Bereichen eines Triebwerks ermöglichen.
Autorin: Nicole Geffert | 5 Min. Lesezeit veröffentlicht am: 13.04.2023
Autorin:
Nicole Geffert
arbeitet seit 1999 als freie Journalistin mit den Themen Forschung und Wissenschaft, Geld und Steuern, Ausbildung und Beruf.
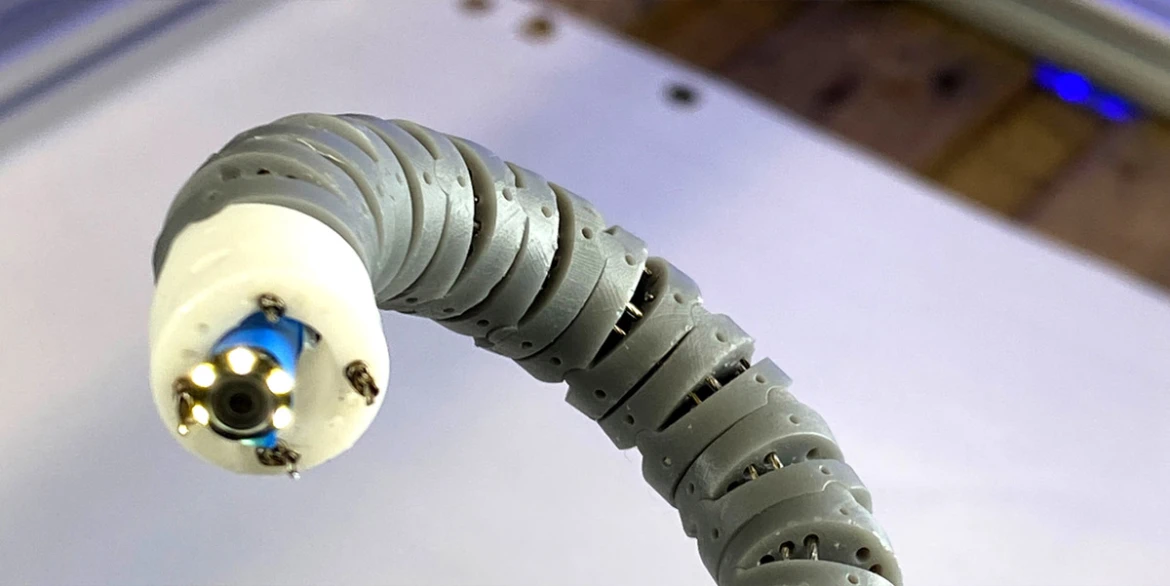
Mit ruhiger Hand und geschultem Blick – nur so gelingt es, unter Einsatz eines Boroskops das Innere eines Triebwerks zu inspizieren, um Qualität oder Verschleiß von Bauteilen prüfen zu können. Boroskopie (englisch: Borescope; bore „Bohrloch/Bohrung“) heißt diese Sichtprüfung schwer zugänglicher Hohlräume. Das Verfahren ist sehr kompliziert, nur erfahrene Inspekteur:innen gehen hier ans Werk.
Einer von ihnen ist André Laukart, Boroskopie-Experte bei der MTU Maintenance Hannover: „Bevor ein Triebwerk zerlegt wird, ermitteln wir mit Hilfe der Boroskopie verdeckte Schäden im Triebwerk, um so Zerlegungstiefe und Reparaturaufwand detaillierter abschätzen zu können. So können wir vor der Demontage frühzeitig mit dem Kunden den Arbeitsumfang abstimmen.“
„Rotierende Bauteile wie Rotorschaufeln erreichen wir mit dem Boroskop, an den Stator eines Hochdruckverdichters kommen wir mit dem herkömmlichen Verfahren nur schwer bis gar nicht heran.“
Boroskopie-Experte bei der MTU Maintenance Hannover
Doch die Expert:innen stoßen an Grenzen. „Das Boroskop ist zwar ein flexibles Instrument. Der Sondenkopf mit der Kamera lässt sich aber nur in vier Richtungen bewegen. Das Boroskop ist nicht flexibel genug, um die Kamera in alle benötigten Positionen zu bringen“, sagt Laukart. Ein mehrfaches, gezieltes Abwinkeln des versteiften Schlauchs im Innern des Triebwerks ist ebenfalls nicht möglich – dabei wäre gerade das erforderlich, um an die tiefer liegenden Bauteile in den sehr kompakt gebauten Triebwerken zu gelangen.
Laukart nennt ein Beispiel: „Rotierende Bauteile wie Rotorschaufeln erreichen wir mit dem Boroskop, an den Stator eines Hochdruckverdichters kommen wir mit dem herkömmlichen Verfahren nur schwer bis gar nicht heran.“ Um Beschädigungen begutachten zu können, müsste die Sonde allerdings so nah wie möglich am Bauteil positioniert werden. Zudem besteht – trotz aller Sorgfalt und Expertise – stets die Gefahr, an einem Bauteil hängenzubleiben, sobald das Boroskop in den engen Bauräumen wieder zurückgezogen wird.
Mehrgelenkige Segmente statt klassische Gelenke
Davon bekamen auch die Wissenschaftler Tim-David Job und Martin Bensch vom Institut für Mechatronische Systeme der Leibniz Universität Hannover einen Eindruck. Die beiden Spezialisten für Robotik erfuhren von Laukart aus erster Hand und direkt am Triebwerk, wo der Boroskopie aktuell Grenzen gesetzt sind. „Für uns sind diese Eindrücke und der direkte Austausch mit dem Experten enorm wichtig“, sagt Job. Denn mit ihrer Forschungsarbeit wollen sie Abhilfe schaffen.
In Kooperation mit der MTU entwickeln die Wissenschaftler ein roboterunterstütztes Boroskop, kurz RoBokop genannt. Dr. Manuel Voit und Jörg Windprechtinger, Experten für Automatisierung und Produktionsprozesse bei der MTU Aero Engines, stehen dabei mit ihrem Team im engen Austausch mit den Wissenschaftlern. „Der erste Prototyp des Miniatur-Roboters ist nach eineinhalb Jahren entstanden“, sagt Voit.
Was unterscheidet den RoBokop vom herkömmlichen Boroskop? „Der Miniatur-Roboter hat bionische Strukturen und erinnert in seiner Beweglichkeit an eine Schlange. Statt klassischer Gelenke hat er mehrgelenkige Segmente, die kontinuierliche Bewegungen ermöglichen. Deshalb wird er auch als Kontinuumsroboter bezeichnet“, erläutert Windprechtinger. Im Vergleich zu den starren Boroskopen ist der RoBokop also viel flexibler. „Somit kann er Bauteile im Innern des Triebwerks erreichen und mit der Kamera erfassen, die bisher nicht zugänglich waren.“
Doch bevor der RoBokop erstmals in Betrieb gehen kann, wird das innovative Verfahren im deutlich größeren Labormaßstab erforscht. Das Modell, das Job und Bensch eigenhändig aufgebaut hat, ist um den Faktor 2,5 hochskaliert – das erleichtert den Wissenschaftlern auch die Durchführung von Versuchen. Im nächsten Schritt soll der RoBokop miniaturisiert werden. „Die Herausforderung ist die geforderten Dimensionen“, sagt Bensch. „Der RoBokop soll einen Durchmesser von nur sechs Millimetern und eine Länge von bis zu 1,80 Meter haben.“
Skelettaufbau mit Seilen
Die geforderten Dimensionen beeinflussten auch die Entscheidung, wie das Skelett des Kontinuumsroboters aufgebaut ist. „Es gibt unterschiedliche Konzepte wie beispielsweise Mikromotoren oder Fluide“, sagt Job. Die Wissenschaftler haben sich für Seile als Aktuatoren entschieden, weil sie sich gut miniaturisieren lassen. Über diese Seile wird eine Kraft auf Metallstäbe ausgeübt, die das „Rückgrat“ – auch Backbone genannt – des RoBokops bilden. Die Führung der Seile erfolgt über Scheiben, sogenannte Discs. Im Innern ist der Miniatur-Roboter hohl, damit Kabel und Leitungen für die Kamera inklusive Messsystem verlegt werden können.
Nicht nur im Shop, wie der Instandhaltungsbereich auch genannt wird, sondern ebenso bei On-Site-Einsätzen könnte der Miniatur-Roboter künftig wertvolle Dienste leisten. Wann immer möglich, führen die mobilen Teams der MTU Maintenance Boroskop-Inspektionen und Reparaturen am Triebwerk direkt am Flügel aus. Das verhindert unvorhergesehene Kosten und ist daher besonders attraktiv für Kunden.
Ein weiterer großer Vorteil des RoBokops ist, dass Bauteile wie beispielsweise Schaufeln reproduzierbar untersucht werden können. Das heißt: Mit dem Miniatur-Roboter lassen sich bestimmte Stellen an einer Schaufel gezielt wieder ansteuern. Mit dem versteiften Schlauch des herkömmlichen Boroskops ist das weitaus schwieriger. Bensch zieht einen Vergleich: „Wer je versucht hat, ein langes Kabel unter Sofa und Schränken hervorzuziehen, um es anschließend wieder an exakt dieselbe Position zurückzuschieben, weiß, wie knifflig bis unmöglich das ist.“
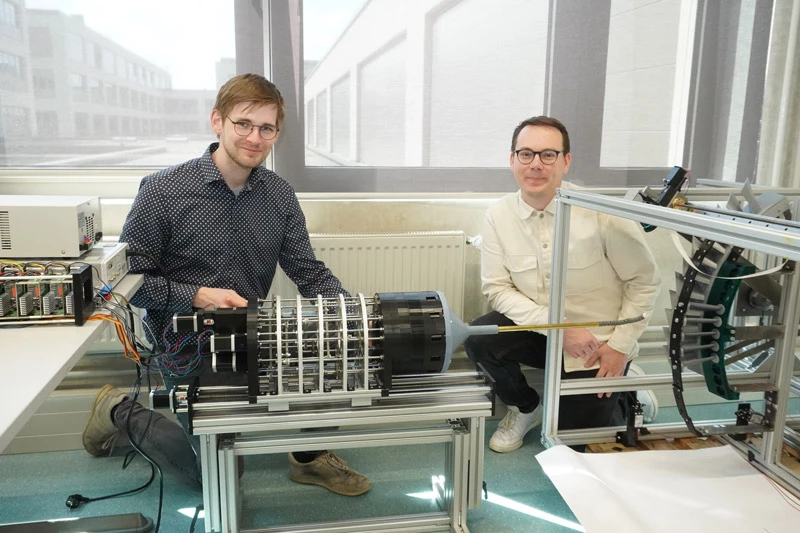
Spezialisten für Robotik: Die Wissenschaftler Martin Bensch (links) und Tim-David Job vom Institut für Mechatronische Systeme der Leibniz Universität Hannover entwickeln in Kooperation mit der MTU das roboterunterstützte Boroskop.
Automatisierter Inspektionsprozess
Gesteuert wird der RoBokop, sobald er in der Triebwerksinstandhaltung eingesetzt werden kann, von den Boroskopie-Expert:innen der MTU Maintenance. „Wir haben hier noch eine klassische Mensch-Maschine-Schnittstelle“, sagt Voit. Mit einem Joystick oder per Tablet beispielsweise wäre es möglich, den RoBokop zu bedienen, während sich die Expert:innen der MTU Maintenance auf die Schadensbegutachtung am Monitor konzentrieren können. „Den Zustand eines Triebwerks bewerten und Schäden analysieren – diese anspruchsvollen Aufgaben werden weiterhin noch unsere Spezialist:innen in der Instandhaltung übernehmen“, so Voit.
Doch die Forschungsteams peilen bereits weiter entfernt liegende Ziele an: So könnte der bislang noch subjektive Inspektionsprozess in Zukunft komplett automatisiert werden inklusive Schadensanalyse und Schadensbehebung. Voraussetzung hierfür ist auch eine fortschrittliche Messmethodik. Auch hier setzt die MTU auf die Kooperation mit der Leibniz Universität Hannover, konkret mit dem Institut für Mess- und Regelungstechnik.
„3D-Endoskopie und Schadensdetektion in schmalen Bauräumen“ heißt das 2023 gestartete Transferprojekt, gefördert von der Deutschen Forschungsgemeinschaft und hervorgegangen aus dem Sonderforschungsbereich 871. Die MTU Maintenance Hannover ist in diesem Transferprojekt industrieller Partner. „Wir stellen sicher, dass die Ergebnisse aus der Grundlagenforschung weiter vertieft und in die industrielle Anwendung gebracht werden“, sagt Dr. Jörn Städing, zuständig für das Maintenance, Repair & Overhaul (MRO) Technologiemanagement im MTU Maintenance-Netzwerk.
Auch in der Instandhaltung gibt es keinen Stillstand in der Technologieentwicklung. „Im Gegenteil“, so Städing, „Unser Gesamtprozess im Bereich MRO soll weiter optimiert und noch effizienter werden. Darüber hinaus kann technologischer Fortschritt auch gänzlich neue MRO-Services für unsere Kunden ermöglichen – beispielsweise in Form spezieller Instandhaltungsdienstleistungen mit dem RoBokop und einem innovativen Messsystem.“