innovation
ScanExpress: Making 3D scans of defects in engine parts
3D ScanExpress is a measurement system that can record, in three dimensions, damage to components that’s just 20 μm deep. This technology could soon be employed throughout MTU.
author: Tobias Weidemann | 5 mins reading time published on: 06.12.2024
author:
Tobias Weidemann
has been working as a journalist and content consultant for more than 20 years. He writes about technology and business topics, often with a focus on business IT, digitalization and future technologies.
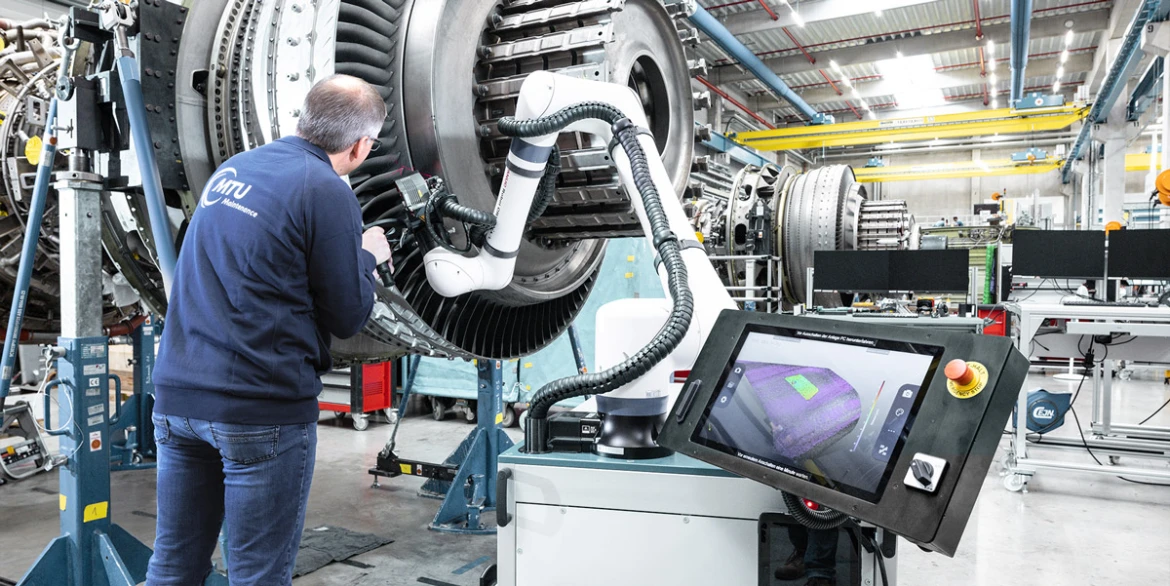
A robot arm glides over the engine component and stops where Benjamin Walter, Project Manager 3D ScanExpress at MTU Maintenance Hannover, has identified an anomaly that’s barely visible to the naked eye. From the tip of the arm hangs a white light interferometer, which can carry out 3D measurements with the help of light waves. From a height of just a few centimeters, the device inspects an area measuring 3 by 3 millimeters—and it takes its readings in mere fractions of a second. In this way, larger areas of an engine part can be recorded and visualized in a point cloud. “What’s most notable is that this process is much quicker and easier than it used to be, and can take place entirely on the shop floor,” Walter reports.
Every day, the mechanics working here encounter a wide variety of irregularities on a component’s surface. In the past, if they discovered what looked like damage to a component while dismantling and inspecting an engine, they had to use casting material to take an impression of it for evaluation and documentation purposes. This then went to the laboratory for analysis under a microscope—“which could often take three to five days and held up the maintenance process for days at a time.”
Seeking a faster and more efficient measurement method
This led Walter to develop the idea of an optical measurement process that would reduce the workload on the shop floor and shorten waiting times. He submitted the idea to the MTU Inno Lab, a department that works together with an international partner network to help take applications from idea to proof of concept as quickly as possible. The Inno Lab brought together a team of people from Munich and Hannover, who all approached the subject from very different perspectives: experts in measurement technology, measurement system approval, machine operation, operations scheduling, and inspection—all of whom encounter the topic in their daily work—plus an innovation manager to provide guidelines for the course of the project and for reporting.
“We realized that white light interferometry is the most accurate, versatile, and, in many respects, expandable system—and that a solution developed by our collaboration partner 3D.aero in Hamburg could fit the problem and the requirements”
MTU specialist for nondestructive testing methods
White light interferometry
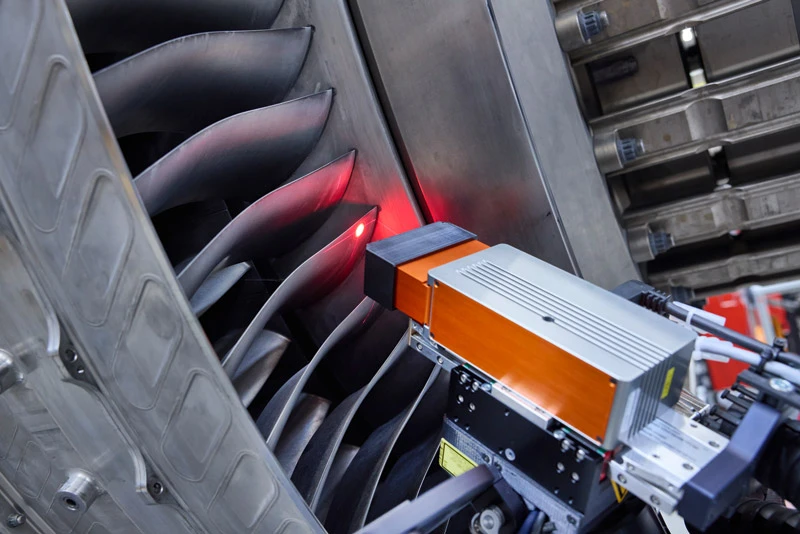
White light interferometry is an optical measurement technique for three-dimensional surface measurement. It utilizes interference effects created by the superimposition of reflected light and light from a reference mirror to generate a digital point cloud of the component surface. White light interferometry is precise and insensitive to reflective surfaces – ideal for engine maintenance.
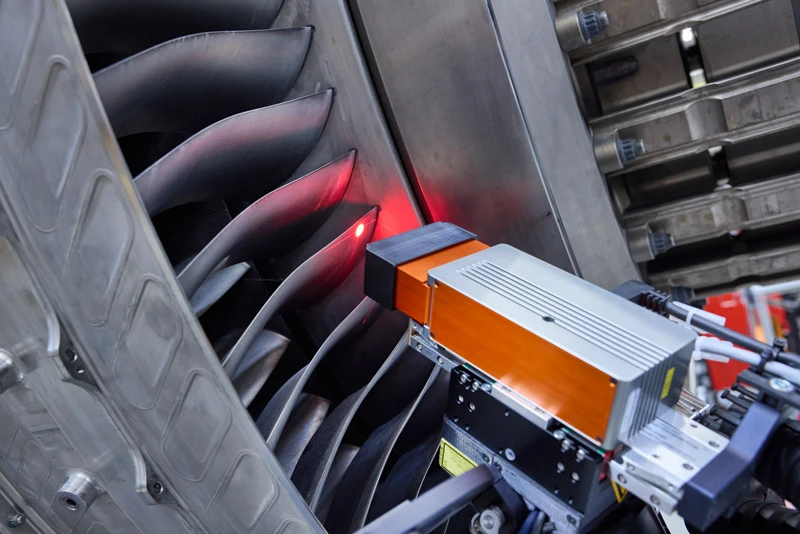
3D.aero delivers the right know-how
With its background in aviation, and with a history of working with MTU to implement automation solutions such as a bolting robot in Hannover, 3D.aero provided a measurement system that works with white light interferometry. This powerful optical technique can be used to measure surfaces and convert them into 3D data sets. “Light reflected from the component surface is superimposed on light reflected by a reference mirror. The resulting interference effects create a digital point cloud that represents the actual component surface,” explains Stefan Necker, MTU expert for geometric measurement technology. White light interferometry enables surface measurements on a wide range of materials. Unlike many other technologies, it’s insensitive to reflective surfaces—a decisive advantage in engine maintenance.
The six-axis robot arm can either be moved manually as a collaborative robot (“cobot”) or can automatically bring the interferometer together with the component to be examined. This also makes it possible to measure larger components beside the measuring table. A detachable tablet can be used to review or present the readings straight away.
From idea to operational system in eight months
Within eight months, the system developed for MTU made its way from idea to prototype and finally to industrial application. “We managed to develop the interferometry measurement system in a very agile way for MTU’s custom requirements, meaning we worked toward them step by step. This agility, which can’t be taken for granted in technical development, quickly led us to a good result that can now form the basis for further innovations,” reports Tomas Domaschke, founder and head of research at 3D.aero.
Most importantly, the process had to be reliable for the purposes of the application, its handling had to be intuitive, and engineers had to be able to change the measuring point quickly using the cobot. As of today, the software determines the measurement reference surfaces itself and carries out the measurement independently, lightening inspectors’ workload. The system generates 3D data that can also be used to provide much better documentation of a situation for the customer than a tabular report. “Day by day, the team is gaining new insights, and these flow into the software’s further development,” Piorun says.
For internal metrological approval, a calibration routine from the manufacturer first had to be adjusted so that it met MTU’s strict specifications, Necker explains. The subsequent measurement system analysis validated the conditions under which the system can reliably deliver effective results. “This ensures that the system is really suitable and usable for our application.” In the meantime, the system has been approved for measuring surface defects that are as little as 20 micrometers (μm) deep—that’s roughly the size of a white blood cell. “Proving that the system is able to measure defects of this size on the shop floor was a real milestone,” Necker says.
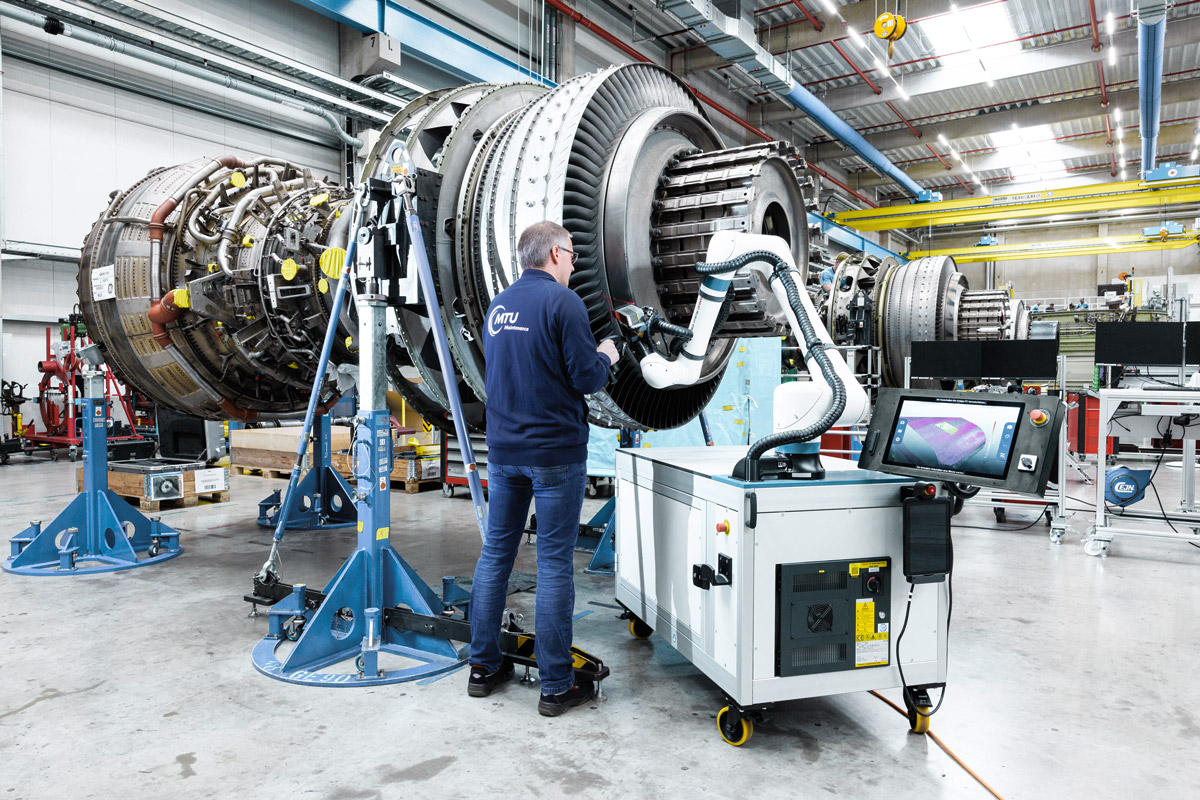
MTU Award for the best new technology in the company
One system is currently in use at MTU Maintenance Hannover in disassembly. Another is currently being industrialized for the inspections area. Discussions are ongoing with other MRO sites around the world to evaluate potential applications. “On average, the system saves the company a whole day in turnaround time,” Walter says.
The new measurement system has already set new standards in the three-dimensional measurement of surfaces. For their joint launch with 3D.aero, the development team received the MTU Award in the Technology and Future category, an innovation prize with which the company recognizes outstanding achievements by employees.