innovation
MTU digitalizes a 50-year-old engine
Augmented reality is simplifying maintenance on the propulsion system for the CH-53G transport helicopter.
author: Thorsten Rienth | 4 mins reading time published on: 09.02.2021
author:
Thorsten Rienth
writes as a freelance journalist for AEROREPORT. In addition to the aerospace industry, his technical writing focuses on rail traffic and the transportation industry.
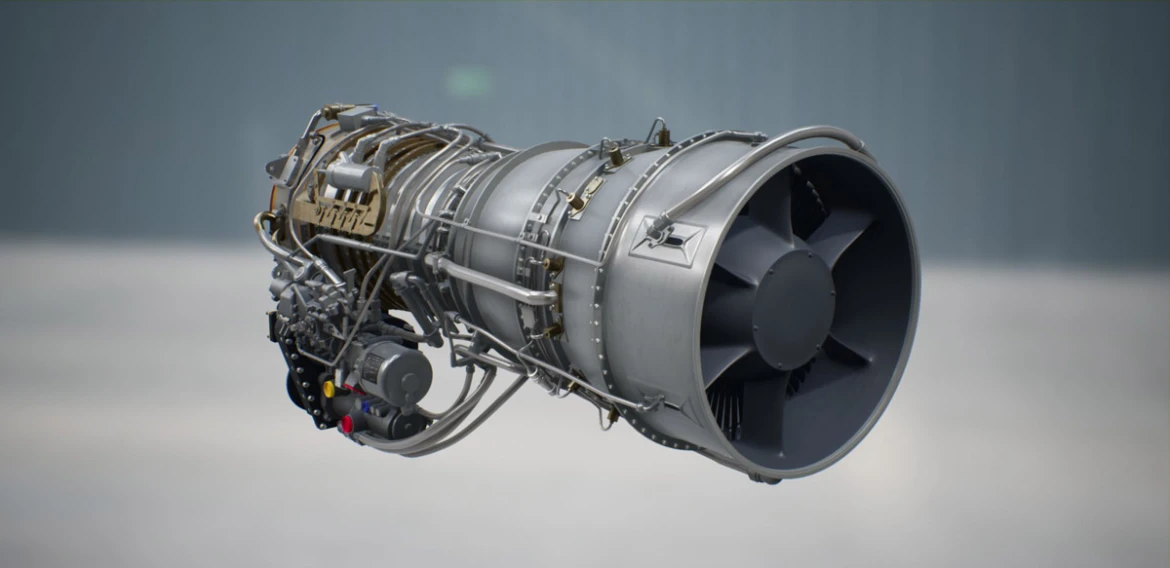
Before the “bearing 4” seals on the two T64 engines that power a Sikorsky CH-53G can be changed, the helicopter must first be taken out of operation. Next, the two engines must be removed and transported to the shop, where the seal is replaced on each. Then the whole process is repeated in reverse. “These kinds of seal changes are very few and far between,” says Bernhard Niklas, program manager T64/T62 services at MTU Aero Engines. “But when they do have to be done, it’s a huge job.” The German Armed Forces had a couple of suggestions: How about using animation to support the task? And why not then integrate it into their technical documentation process?
Hundreds of photos replace meter-long scanner
This is where Thomas Staak, who heads the Technical Documentation department at MTU Aero Engines, comes in. For several years now, he’s been looking at ways to take maintenance measures, assembly steps and quality inspections to a whole new level. Augmented reality, mixed reality and virtual reality, or AR, MR and VR, are three approaches already showing promise.
Initial proofs of concept have already established the feasibility of using AR to support the repair of thrust nozzles. AR applications have also been tested for use in quality inspection for certain work steps in the assembly of the PW1100G-JM engine that powers the Airbus A320neo—specifically to check the correct positioning of brackets. Plus, an animation for the assembly of the T408 engine with interactive commands is currently under development. Another project in commercial assembly of the A320neo engine is looking to introduce HoloLens mixed reality glasses. Once internal approval is granted to use the AR glasses in-house at MTU, a pilot project will begin. The application of AR technology is expected to reduce assembly errors, increase the efficiency of the process and speed up certification on the engine. What it comes down to is whether the assembly mechanics can see AR adding significant value to their work.
But as so often is the case, what sounds simple in theory is a whole different ball game in practice. Not because Staak and his team don’t know how to create animations, but because when the CH-53G went into production back in the 1960s, no 3D data was created using computer aided design (CAD) as would usually be the case today. This leaves the team without a data basis from which to start. They can, however, create the data themselves by working backwards—and that is precisely what they did.
This alternative approach took several days and involved taking hundreds of individual and overlapping photos of the engine from every conceivable angle. To capture the components inside the engine that are of key relevance to replacing the seals, the engineers partially dismantled the engine. “We then used software to convert the 2D images into a 3D model of the engine to make a kind of ‘light’ version of a digital twin,” Staak explains.
Fortunately, the developers don’t (yet) require full depth of detail. “This isn’t about millimeter precision. What matters most is that the engine mechanics can grasp what’s going on in the aminations at first glance without any scope for misunderstanding,” Artificial intelligence (AI) software is also a great help here. “Today’s technology makes it possible to rework a lot of things automatically, such as unfavorable lighting or shadowing,” Staak says.
Correct measurement: The animation explains each step for correctly measuring the carbon seal in the sump cover of the T64.
The next stage: interactive electronic technical manual (IETM)
At the end of their joint development project, the German Armed Forces and MTU put together step-by-step instructions on how to change the seals. “These are a useful aid that mechanics can refer to at any time, helping to facilitate and speed up the work steps they perform while also reducing the scope for error,” Niklas explains. Displayed on a tablet or similar device next to the mechanic, the animation shows the correct assembly location, the position of the next component, which tool to use, and parameters such as the necessary and permissible torque. If anything is unclear, the mechanic can simply replay the work step. An interactive electronic technical manual, or IETM, makes all the difference.
Looking further into the future, Staak says: “When we take things to the next stage, the tablet might even become surplus to requirements if, say, we play the animations through augmented reality glasses and make them voice-controlled.” Creating the animation in the first place naturally ties up a great deal of resources, he explains. “But the advantages for the repair shop are huge.”
In the case of the T64 seal replacements, the German Armed Forces and MTU have now reached the next, possibly even final step: “We’re already looking at how to integrate the animations into our partner’s operations,” Niklas says. He’s convinced that all the time and resources invested will be worth it. “An engine like the T64 is expected and likely to remain in service for another decade or so, which leaves us plenty of time to amortize the costs.”