good-to-know
A brief guide: Engine control unit
The DECMU is a fully digital engine control unit that also helps ensure safe operation. For the EJ200, it does even more.
author: Patrick Hoeveler | 4 mins reading time published on: 17.04.2024
author:
Patrick Hoeveler
is a freelance aviation journalist working for FLUG REVUE and other publications.
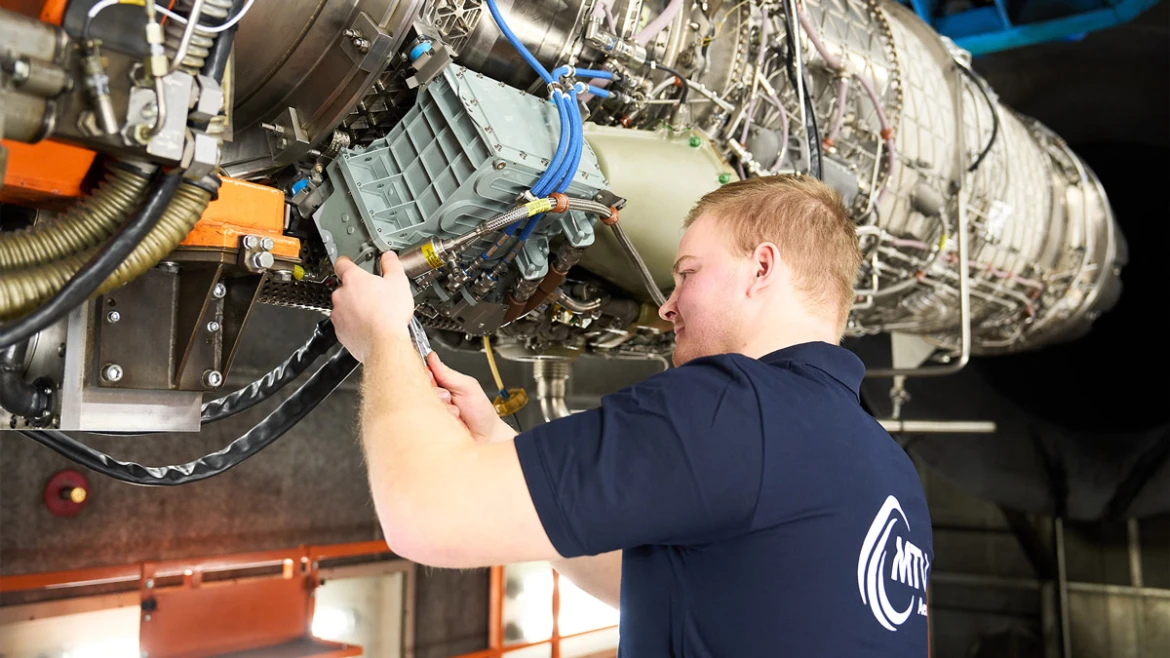
Welcome to the nerve center: not for nothing is the control unit considered the brain of an engine. Like neural pathways, numerous wires feed the system with information, which is processed in a compartment no bigger than a shoebox. Whether it’s pressure levels, temperatures, or position signals—with the help of sophisticated algorithms, the special software processes the data and creates the appropriate commands for actuators and other subunits. In other words, all matters of engine control run via the fully digital controller.
You may also be interested in following content
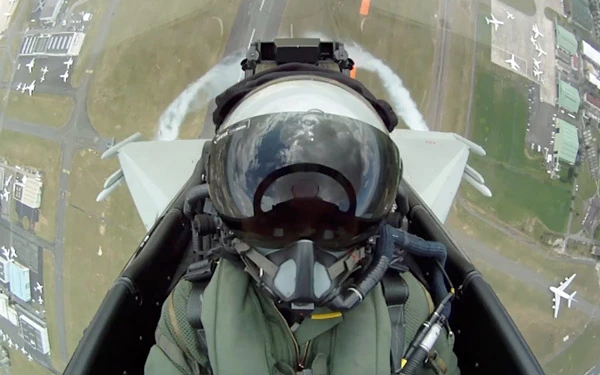
New momentum for the Eurofighter’s EJ200 engine
Thanks to new orders, production of the Eurofighter engine is gaining renewed momentum.
DECMU: Digital control unit for the EJ200
The Digital Engine Control and Monitoring Unit (DECMU) is responsible for controlling the Eurofighter engine and manages all advanced engine settings. The pilots simply specify their thrust requirements via the thrust lever; the control unit located toward the front of the engine does everything else. No matter what setting is selected, the computers ensure that everything remains within the given limit. This makes pilots’ lives a lot easier as it means they can devote their full attention to their mission.
For safety reasons, the DECMU features two parallel channels, with each one monitoring the other. If a problem arises with one channel, the system automatically switches to the other. The pilots in the cockpit are generally unaware of this; only if there’s a serious problem do they receive an error message. Otherwise, the system logs the event so that the ground crew can read out the data after the aircraft has landed.
Brain of the engine: The DECMU is attached to the front end of the engine. There, numerous wires feed the system with information, which is processed in a compartment no bigger than a shoebox. All matters of engine control run via the fully digital controller.
Control and monitoring in one
As the name suggests, the DECMU combines engine control with the monitoring and gathering of data relevant to maintenance activities. The top priority is naturally to ensure safe operation during flight. To this end, the sensors recapture the signals every ten milliseconds on average to check that engine parameters are always set correctly for the prevailing conditions. As a result, impending problems can be addressed as quickly as possible and in extreme cases the engine can be shut off before it can suffer severe damage. The DECMU also stores a wealth of operational data that can be evaluated after landing to gain valuable information pertaining to engine maintenance.
Interestingly, the current version of the control unit requires less computing power to perform its tasks than is available in a contemporary mobile phone. However, all calculations must be completed quickly and with a high degree of precision and certainty.
Fit for the future
Despite the undisputed performance of the existing DECMU, MTU Aero Engines is currently working on an upgraded version. The reason for developing the DECMU-NG (NG stands for next generation) is really the age of the electronic components. Many components are simply no longer available, which comes as no surprise given the rapid pace of development in the electronics industry. After all, the design for the original DECMU will soon be 20 years old. The next generation of the DECMU will solve this obsolescence problem.
“The old DECMU is equipped largely with military electronic components, but the importance of these is fading worldwide. More and more, the entire military industry is opting for the kinds of industrial components found in cars,” says Werner Oberndorfer, Head of Project and Order Management for Engine Control Unit Development at MTU. “In this regard, the lifecycles of aeronautical equipment and of electronics couldn’t be less compatible. This is especially true of military equipment, which can have a service life of up to 60 years. Meanwhile, in the electronics market, development cycles are getting shorter all the time and fundamental shifts occur every couple of years.”
This is why MTU’s engine experts check all components every six months and divide them into risk categories. The higher a component’s risk category, the closer it is to the end of its service life and thus its availability. This helps identify any problems early on with a view to proactively finding replacement components while these are still available. As the DECMU is made up of up to 20,000 electronic components, this is no mean feat.
The new DECMU is now being given a completely new interior, with features including more computing power, larger memory, and enhanced interfaces. This paves the way for incorporating additional maintenance functions into the software in the future. “These will include improvements that can help further reduce the engine’s maintenance costs,” says Stephan Lang, DECMU Chief Engineer at MTU. Nevertheless, the DECMU-NG will retain full backward compatibility. This means that in the future, it will be possible for a Eurofighter to be equipped with one engine featuring the old control unit and the other featuring the new control unit. Initial tests of the new version in an EJ200 are scheduled to take place on the MTU test stand over the coming year.
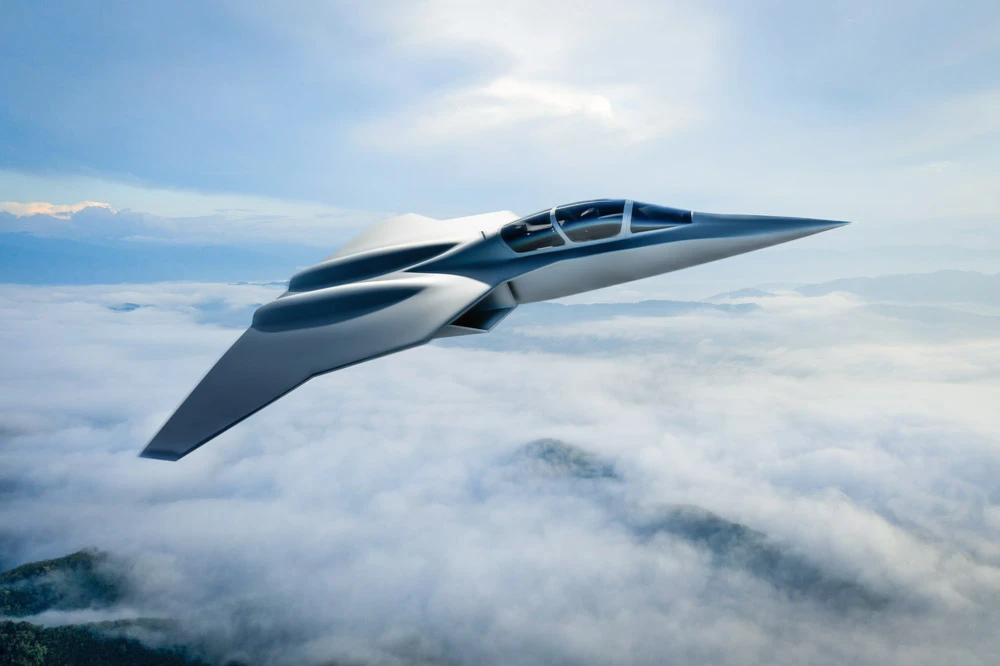
©EUMET
New Generation Fighter: A sixth-generation fighter jet that enables connectivity between the fighter and unmanned components. It uses more advanced key technologies—particularly in the field of electronics and sensors.
The next “next generation”
Europe’s New Generation Fighter (NGF) is being developed as part of the Future Combat Air System (FCAS). For this fighter jet’s engine, the New Generation Fighter Engine (NGFE), the DECMU-NG used in the EJ200 will once again provide the technological basis for multiple functions. However, the system being developed in collaboration with Safran Aircraft Engines is essentially entirely new. Here, the engineers are also exploring concepts that use distributed intelligence, which means that computing operations no longer all flow into one box, but rather take place closer to the sensors or in smart actuators. This would offer the benefit of shorter control loops and thus even faster response times.