people
MTU’s engine makers
Keeping everything running smoothly: ten MTU specialists talk about their job, what they particularly enjoy about it and their role in making an engine.
author: Nicole Geffert | 20 mins reading time published on: 24.05.2023
author:
Nicole Geffert
has been working as a freelance journalist covering topics such as research and science, money and taxes, and education and careers since 1999.
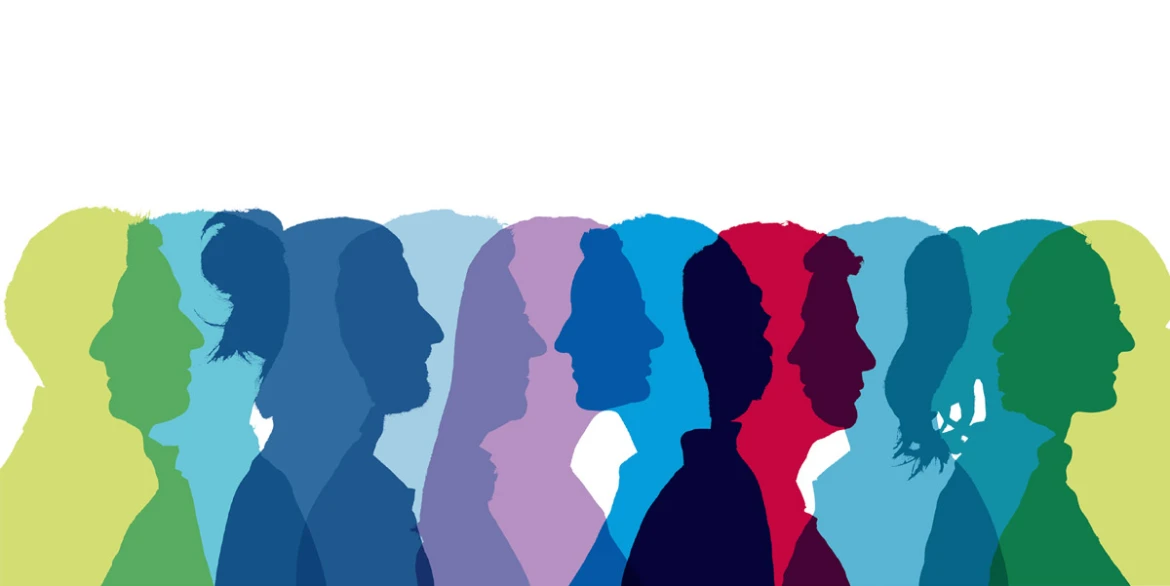
What could be more exciting than working for a technology leader? For the expert when it comes to innovative propulsion systems and revolutionary engine concepts for commercial and military aircraft? For one of the world’s major players in aviation, driven by the vision of emissions-free flight? MTU Aero Engines’ more than 11,000 employees would clearly say, “There’s nothing more exciting than working for MTU.”
MTU can rely on their experience, expertise and innovative strength—every day. Because in addition to highly complex technology and innovative production, the focus here is on people. Few companies work at such an exacting level as MTU. So enthusiastic, so focused, so successful. These are all qualities that distinguish MTU employees. Qualities that show their attitude: they identify with the company and their job on an extremely profound level.
Building a product that’s as highly complex as an engine requires teamwork and the skills of many top professionals. MTU’s engine makers each play their own important role in engine production. The much-cited dream of flying is palpable everywhere here: in the offices of the development departments, at the ultra-modern workstations in production, in the boardroom. No matter what field our people work in, they all seize their opportunity as members of the global MTU family to always lead the way.
AEROREPORT spent a day with ten MTU engine makers at the company’s Munich site who work in everything from logistics and development to production and quality assurance. Here, they talk about their job, what they particularly enjoy about it and their individual role in making an engine.
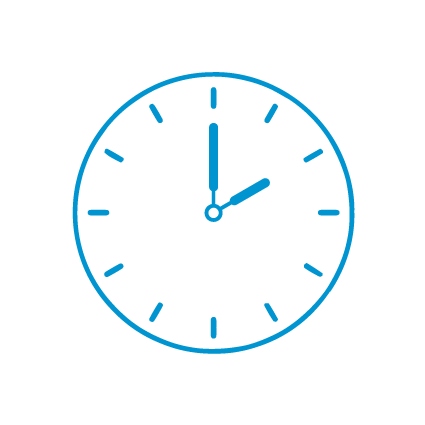
During deburring, the component is milled and cleaned up by means of an air grinder.
It’s 2 a.m. and Manfred Glas is wide awake. The machinist is holding a vane ring belonging to a low-pressure compressor for the Eurofighter’s EJ200 engine. This component needs to be deburred, which involves filing material off at the edge of the workpiece. Glas lays out the processing sheet for the component. “The drawings tell me where I have to deburr,” he says. Glas has plenty of experience doing this particular job. “Regulations say that I have to consult the sheet, even if I already know what I have to do. Safety and regulatory oversight are paramount.”
He mounts the fixture that holds the component on the deburring stand—a kind of small hoist that Glas can tilt by up to 180 degrees for optimal processing. Once the vane ring is clamped, Glas selects the correct milling cutter and begins—naturally wearing protective goggles and hearing protection. “MTU doesn’t cut any corners and that’s also true for occupational safety, which I think is both right and important. When we’re working on components, we also have an exhaust extraction system running the whole time.”
Glas works with strong focus, a steady hand and a trained eye. “I’m required to pass an eye test every year,” he says. While some components have a processing time of five or six hours, the vane ring can be deburred in two. Glas then sends it on to the next department. “Every day is packed with new challenges. I work on a broad range of commercial and military components, so I never get bored.”
Glas deburrs the components after they have been turned or milled and sends them on to be cleaned, inspected and finally installed. From time to time, he is also involved in installation. He particularly enjoys working the night shift, when MTU is quieter. “I like to focus on my work and that’s when it’s easiest to shut out what’s going on around me.” Nevertheless, he is in regular touch with his colleagues. “We process the components with a great deal of precision, following the regulations to the letter. This is essential, not least because our engines will go on to power aircraft that carry thousands of passengers.”
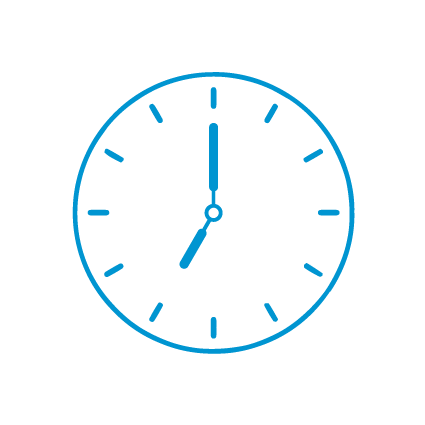
MTU's blade production facility manufactures, among other things, high-pressure turbine blades for military and commercial engines.
There are appointments that no one gets to reschedule. It’s 7 a.m., and that’s always when Florian Wutz, Team Leader in airfoil production, meets with his team on the shop floor. “We use this meeting to discuss how we can best plan, implement and optimize our production processes,” Wutz says as he welcomes his colleagues from manufacturing, operations scheduling and logistics. The eight team members are standing in front of the shop-floor board, where they have posted all the relevant data and KPIs from their department for all to see.
This daily briefing lasts no more than ten minutes. Everyone keeps their contributions short because there’s a lot to do. Wutz manages processes and HR planning for airfoil production and is really enthusiastic about this particular product. “Working on this highly complex component made of high-strength alloys is the highlight of our job,” he says. Having qualified as an industrial and mechanical engineer, Wutz knows how important such components are: “An engine can’t fly without airfoils, and we look after these key components from start to finish.”
Today, the team is discussing a deburring issue concerning airfoils for high-pressure turbines. “These airfoils are installed in the hot gas section of the engine, where they are subjected to temperatures of more than 1,000 degrees Celsius,” Wutz says. The quality must be first rate. Immediately after the team meeting, he inspects the airfoils right there on the production line.
“Whenever we have an issue like this, seeing firsthand what’s going on helps me come up with ideas for how to resolve it,” Wutz says. He adds that there’s no substitute for exchanging information directly with the manufacturing experts. “In airfoil production, we work together as one big team.” Wutz knows what he’s talking about. To achieve an optimum result, he makes sure that each member of his team is performing the tasks that best match their qualifications, thus preventing bottlenecks. After all, they have to manufacture airfoils in large numbers: every year, MTU produces some 70,000.
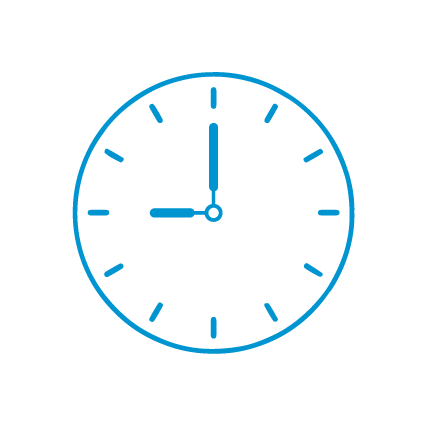
As a process specialist, one is responsible for the technology related to one or more thematically linked special processes.
In the testing room this morning, everything revolves around compressor rotors. It’s 9 a.m. and experts from production, operations scheduling, quality control and structural mechanics are inspecting a component. One of them is Lea Mainberger, Process Specialist for Work Hardening Processes. Together, they will clarify how a special cover for blisks—high-tech components that integrate blade and disk—can be optimized in the production process.
“I work at an interface to several technical departments,” Mainberger says. “We coordinate across disciplines and jointly develop solutions that keep our manufacturing processes running smoothly.” An industrial engineer specializing in materials technologies, she joined MTU’s department of chemical and nonconventional technologies in 2019.
Here she has developed into a process specialist for shot peening as well as abrasive blasting. “Shot peening extends the life of a component by introducing a compressive residual stress layer. To do this, we either blast very small steel spheres directly onto the component via a nozzle or use ultrasound to excite them so that the spheres achieve a similar effect,” she explains. “We put all rotating and highly stressed components such as disks, blades and blisks through this treatment.” Abrasive blasting is used to clean or roughen the surfaces of housing parts, for example.
Mainberger’s expertise is in demand when it comes to, say, process changes and testing, evaluating new methods for work hardening, and obtaining supplier approval for the processes. “Every day is different and I split my time between my desk and the manufacturing hall,” she says. She is also revels in the team spirit and in knowing she can rely on her colleagues one hundred percent.
“Before I took on my current role at MTU, I was trained by a senior expert who retired shortly afterward,” she says. MTU has also given her the opportunity to take external courses to gain additional qualifications. That, too, makes her job exciting: “Because the work we do is so specialized, there’s always something new to learn.”
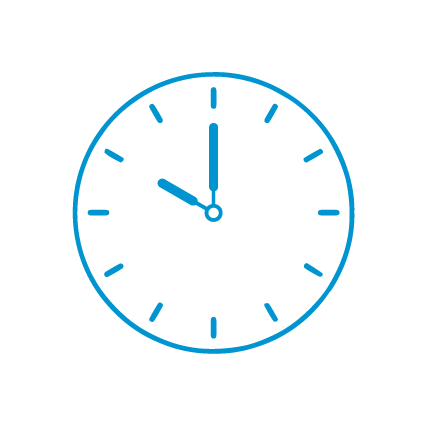
At the electroplating shop they apply and strip galvanic as well as thermal coatings.
“You can’t miss us, considering the amount of space we take up here,” Michael Blümel says, pointing to twenty large baths lined up in the electroplating shop. It’s 10 a.m. and Blümel is in his element. A newly designed fixture for the first stage of the intermediate-pressure compres-sor for the TP400-D6, which powers the Airbus A400M military transporter, is being tested.
The fixture covers the areas that are not supposed to be coated. Blümel expertly checks whether the component fits perfectly into the new fixture. Is the tightness right for submersion into the electroplating bath? What about the fixture’s chemical resistance? It’s 85 centimeters in diameter. Large components have their own hoists to ensure safe handling of both the component and the fixture.
“In this component, we coat only a tiny groove with nickel to protect it from wear. This means we have to cover most of it with the fixture,” Blümel says. After training as a surface coater, he first became a team coordinator and then advanced to become a process improver in electro-plating.
MTU has mastered a wide range of electroplating processes for new and repair parts. “Every rotating disk has to go through the electrochemical processes in the electroplating bath to check the base material for defects,” Blümel explains. Electrolysis is used to apply metallic layers to the components, which protects them from external influences such as heat and wear.
“We can recoat worn areas over and over again, giving the components a second, third or fourth life. This helps the customer save costs and also conserves resources,” Blümel says. However, there’s no skimping on quality. “We check everything meticulously. The material must be flawless. That’s how we ensure that every component is perfectly coated and meets the high requirements for flight safety.”

At the Munich site, more than 5,000 employees are served a variety of meals in the company restaurant every day.
It’s midday and the coriander is almost gone. Claude Fini places a bowl of the freshly chopped herb next to the wok. As head chef at MTU’s company restaurant, he always knows what’s going on—even when thousands of hungry employees are pouring into the new section of MTU’s Munich site. Fini greets them with a sparkling smile. “I always make myself available to our guests,” he says. In the kitchen, his team hits the gas, but only metaphorically: all the sizzling, sautéing and steaming is done on electric and induction cooktops.
All the kitchen equipment at the recently completed site addition is top of the line. Food is served at four counters: “Local & traditional,” “Salads & grill,” “Pizza & pasta” and “Wok at work”. “We expect to serve 1,500 to 1,700 meals a day and plan accordingly,” Fini says as he organizes the refills at the “Local” counter. Today, his team has seasoned, breaded and cooked 900 schnitzels.
“Since we’re in Bavaria, schnitzel and roast pork are always favorites, but vegetarian and healthy options are also among the popular items on the menu,” Fini says. MTU’s company restaurant serves pork sourced from “straw pigs”; these are pigs raised responsibly in straw-filled stalls. The vast majority of the chicken served comes from a free-range farm just outside Munich. Priority is given to regionally sourced ingredients. Just recently, Fini visited a farm that supplies the company restaurant with potatoes and vegetables to make sure the quality of the ingredients was up to standard and to show the supplier how MTU values their long-standing relationship.
“We cook virtually everything from scratch—convenience food is a nonstarter at MTU,” Fini says. “We do our part to keep employees fit and motivated as they do their jobs.” Fini believes that sharing a meal promotes communication and strengthens group identity. This kind of team spirit is also important in the kitchen. “A restaurant kitchen is a stressful place to work,” he says, which makes good organization and planning all the more important. “I also aim to create a sense of fun around the work we do.”
The company restaurant closes at 1:45 p.m. Time for a break. Fini will be back at his desk later, though, to prepare the food orders for the next couple of days. Sweet pancakes (Kaiserschmarrn) and apple strudel are going to be on the menu. There’s always room for dessert!
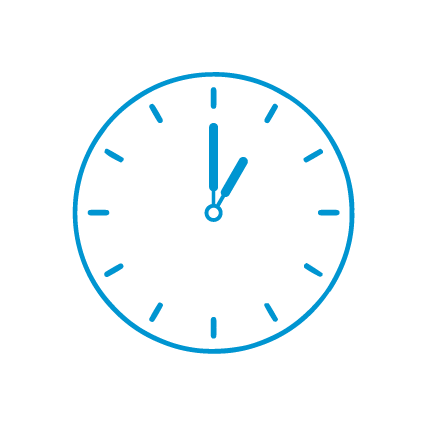
SAP Inhouse Consultant are responsible for configuring and looking after the SAP system within MTU’s IT system landscape.
It’s 1 p.m. and Lisa Schneider is immersed in an IT concept for operations scheduling. “During my first job, I quickly realized that I had an aptitude for IT and SAP,” says Schneider, whose main task at MTU is to look after the operations scheduling SAP module. “The SAP system extends into every corner of MTU. In my area, we tailor it to the specific requirements of manufacturing.”
Schneider joined MTU at the beginning of 2022. “I actually got my start in process management for purchasing before switching to IT,” she says. As an IT expert, she also belongs to a competence team that meets regularly. This has her working directly with her colleagues from the technical departments involved in production. “Being an IT planner doesn’t mean you sit in front of a computer all day long,” she says. “Quite the opposite: the close collaboration with the technical departments really makes this job about communication and teamwork.”
Schneider draws extra motivation from having the autonomy to implement solutions on her own authority. “What I really like is getting to see orders through from concept to finished product.” Some projects are so complex that they take months to complete. But sometimes, she can complete modifications to existing functions in just two weeks. “Not every technical manufacturing concept can be translated one to one into an IT concept. It takes creativity to come up with workable alternatives.”
The pace of life in MTU’s IT department is fast—especially considering the company’s increasing use of intelligent digital connectivity for machines and processes, also known as Industry 4.0. “I’m always acquiring new knowledge, which is another reason why this job is so exciting,” Schneider says. “By ensuring that current and future production requirements are implemented as successfully as possible in the system, I play my part in helping MTU manufacture top-quality engines.”
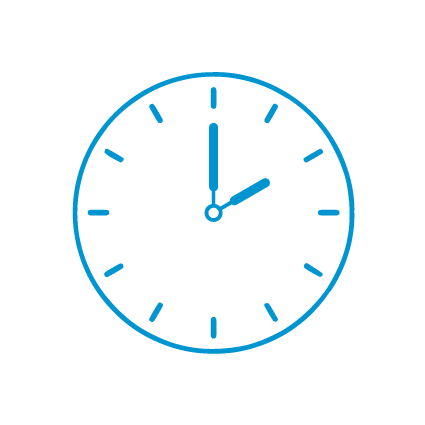
Quality controllers ensure that the products are made in accordance with the fundamental rules of quality and safety.
Although the tiny deviation in the turbine blade is barely visible to the naked eye, the visual inspection was good enough to detect it. It’s 2 p.m. and Marc Rehermann, Quality Controller for assembly, is notified immediately. There’s no time to waste: “My office is only one floor away from the assembly line—a short distance for quick decisions."
The experts for this component work on-site. “That’s a major advantage. We can contact our design and manufacturing specialists directly to agree on further actions. Product deviations are now always discussed as a team,” Rehermann says. Alongside improving processes, managing deviations is one of the quality controller’s most important tasks. “We assess every anomaly, no matter how small,” he says. “I help decide whether a component will be installed, reworked or rejected. That’s quite a responsibility.”
Rehermann, who is 26, studied aerospace engineering at FH Aachen and joined MTU in 2022. “During my studies, I completed an internship at MTU Maintenance Hannover,” he says. “That experience was so fascinating, I realized that my idea of working as an engineer meant really getting my hands on the engines.”
At MTU, Rehermann’s theoretical knowledge is just as important as the real-world experience and expertise that his production and assembly colleagues have built up. “We examine the component from many different angles to ensure maximum quality,” he says. “We make sure that any assembly stamped with the MTU logo has MTU quality underneath.”
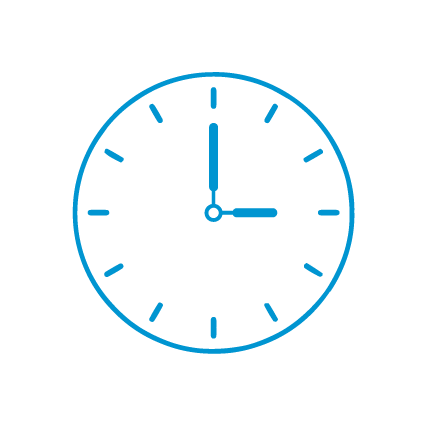
Outbound logistics is responsible for shipping and transport processing as well as shipping control and quality assurance.
It’s 3 p.m. and the entire outbound logistics team knows what to do. Together, they work like a well-oiled machine. The truck that transports MTU components to Munich Airport once a day is standing by; it must be fully loaded by no later than 3:45 p.m. “Work gets more intense in the afternoons,” says Benedikt Buchner, Head of Outbound Logistics and Quality Control, as he enters the hall. But everything’s going according to plan, and Buchner knows that he can count on his team. “I value being able to work independently and so do the members of my team,” he says.
Customs clearance is a complex business. Buchner has checked all the necessary documents, certificates and other paperwork. Everything has to be in order. Today, it’s blisks that are being dispatched. “Blisks are transported in specially designed packaging,” he says. “In addition to saving us time and money, this packaging is sustainable and doesn’t need to be wrapped in plastic.”
Buchner knows a lot about packaging and doesn’t underestimate its importance. “We ship goods worth millions, so they have to be packed with great care. Flight safety is our top priority and we have a zero-tolerance policy for faults. Our partners want to receive their goods undamaged—and on time!” And that’s what Buchner and his team achieve day in, day out with zero customer complaints. “In terms of quality, we’re the final link in the engine production chain. We make sure that each component is perfectly packaged and always reaches its destination.”
To keep things running smoothly, Buchner is in direct contact with suppliers, logistics providers and customers around the world. He knows what each one’s transport requirements are. Next morning, he receives an e-mail from a customer in the U.S. telling him that the components were delivered on time—proof that his team’s processes are effective.
Buchner joined MTU back in 2001, and his enthusiasm for the job has been a constant source of motivation. After all, logistics is a dynamic business. Buchner even goes a step further: “My team has a real passion for logistics. We make sure that the quality requirements for engine production extend to delivery,” he says with a glance into the hall. He gives a thumbs-up. The truck leaves the loading zone and sets off for the airport.
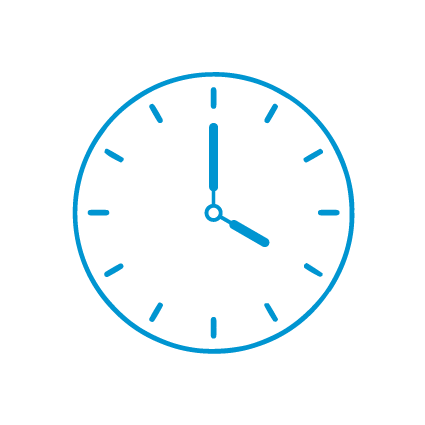
In the development for structural mechanics, the structural integrity of the components is ensured.
Dr. Saskia Lessig glances up at the clock. It’s 4 p.m., which means she still has time to go through her notes from the previous meeting. The components team responsible for the blades of the TP400 engine’s intermediate-pressure turbine meets once a week. “We follow an interdisciplinary approach,” Lessig says. In the meeting, experts from engineering, production, quality assurance and program management, for example, discuss the integrated product development. “When we get to the structural integrity of the blades, everyone looks expectantly at me,” she says with a chuckle. “I leave our meetings with a list of tasks and I look at these in my own time once I’m back at my desk.”
The questions put to Lessig and her colleagues in structural mechanics are complex and highly technical. “We always works through such questions as a team,” she says. “Together, we make sure that our surrogate models are error-free and fulfill the most stringent quality standards. Flight safety is our top priority.” This is why all calculations are reviewed by at least two members of the team prior to approval. “We’re specialists, yes, but we’re also team players—our discipline is simply too broad for us not to be. Each of us has their particular niche, so together we find the answer.”
As a mathematician, Lessig’s expertise is in high demand when it comes to numerical analysis or stochastic problems. She did her PhD in contact mechanics, which “provided me with a bridge between theoretical mathematics and mechanical engineering,” she says. It was her professor who first told her about MTU, which she calls a “happy coincidence.” She came to the company through her PhD and has remained here. Lessig minored in IT, and she can also apply that knowledge at MTU—for instance, when integrating processes and procedures.
The challenges that come with the job are what she finds exciting about it. “The requirements that our engine programs need to meet are becoming more exacting all the time—especially when it comes to the innovative propulsion technologies that we’re developing to ensure an emissions-free future for aircraft.”
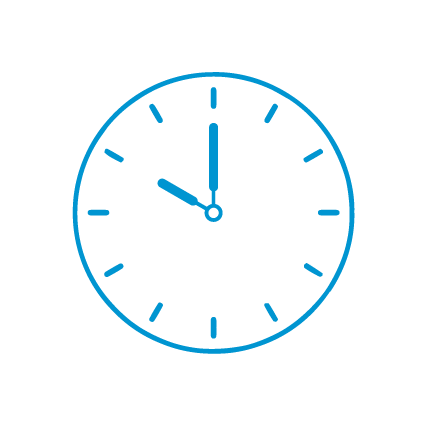
In the thermal spray shop they coat complex engine parts with materials to protect them against heat and wear and tear.
It’s 10 p.m. Half an hour ago, Maximilian Bayer started his night shift in the thermal spray shop without a trace of fatigue. The 27-year-old closely inspects a disk for the PW1100G-JM GTF engine. Where flying, and extremely safety-critical, parts are processed, careful scrutiny is the first duty. The visual inspection reveals no anomalies or deviations: the new component is perfect. Bayer covers it with heat-resistant silicone rings, explaining, “That way, only the areas that are supposed to be coated will be coated.”
In 2010, Bayer started his career at MTU as an industrial mechanics apprentice. Now he is an expert in the thermal coating of engine components. He takes the disk to a blasting facility, where “the surface is roughened so that the adhesive layer sticks better.” Next, he pushes the component into the coating line. There, the heat and wear protective layer is applied to the disk with the help of a robot and a plasma torch. Bayer deburrs the resulting edges with a brush and a file: “Even though we use state-of-the-art machinery here on the shop floor, my job requires craftsmanship.”
“I machine about 25 different components. Every workday is different, and I like that,” Bayer says. Independent work is key, but so is teamwork. “In any case, we apply the two-person principle, for example when it comes to measuring the coated component. The dimensions have to be right—we deliver nothing but first-class quality.”
Bayer likes everything about his job, from the team, which includes many young people, to the development opportunities at MTU. And there’s something else that excites him: the product. “Recently, I flew on an A320neo with the PW1100G-JM. A short time later, when I held a component of this engine type in my hands at my workplace, I thought: Cool, I just flew with that engine. It’s possible that I even coated a component for it.”
There’s more than 11,000 of us. Who are we still looking for? You!
Help us raise digitalization at MTU to a whole new level as an IT expert. Manage and monitor our finances and play a role making strategic corporate decisions as a controller. Ensure that our products and processes meet the most stringent standards as a quality controller. Help us assemble or maintain our extensive engine portfolio as an aircraft maintenance engineer.
And that’s just the tip of the iceberg: whether your talents lie in design, purchasing, human resources, electroplating, or testing, and whether you’re looking to enter as a trainee, dual-track student, graduate, seasoned professional or manager—MTU has something to offer.
Our strong team ensures that our partners and customers around the world can always count on MTU quality. As an aviation company, we’re helping shape a massive transformation. Our vision is emissions-free flight. And turning this vision into reality hinges on developing revolutionary new engine concepts. That’s why we’re looking for bold, knowledge-hungry engineers who want to be part of this transformation.
And did you know? We don’t just manufacture aircraft engines, we also train cooks in the company restaurant at our Munich site. So our job market is definitely worth a visit.