people
Die Triebwerksmacher der MTU
Für sie läuft es rund im Job: Zehn MTU-Fachkräfte berichten über ihre Arbeit, was ihnen daran besondere Freude macht und welchen Beitrag sie zum Triebwerk leisten.
Autorin: Nicole Geffert | 20 Min. Lesezeit veröffentlicht am: 24.05.2023
Autorin:
Nicole Geffert
arbeitet seit 1999 als freie Journalistin mit den Themen Forschung und Wissenschaft, Geld und Steuern, Ausbildung und Beruf.
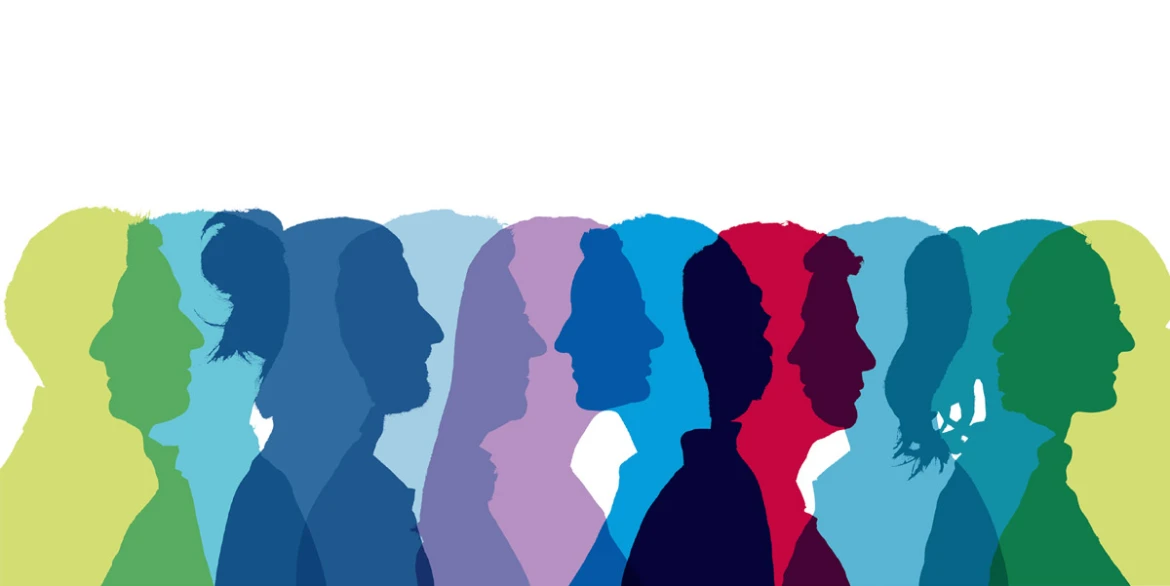
Was gibt es Spannenderes, als für einen Technologieführer zu arbeiten? Für den Experten, wenn es um innovative Antriebe und revolutionäre Triebwerkskonzepte für zivile und militärische Flugzeuge geht? Für einen der weltweit großen Akteure in der Luftfahrt, den die Vision vom emissionsfreien Fliegen antreibt? Die mehr als 11.000 Mitarbeiter:innen der MTU Aero Engines würden klar sagen: „Es gibt nichts Spannenderes, als für die MTU zu arbeiten.“
Auf ihre Erfahrung, Expertise und Innovationskraft kann die MTU bauen – Tag für Tag. Denn neben hochkomplexer Technologie und innovativer Produktion stehen hier die Menschen im Mittelpunkt. In nur wenigen Unternehmen wird auf so hohem Niveau gearbeitet wie bei der MTU. So begeistert, so konzentriert, so erfolgreich. Alles Eigenschaften, die die MTU-Mitarbeiter:innen auszeichnen. Eigenschaften, die ihre Einstellung zeigen: eine extrem hohe Identifikation mit dem Unternehmen und mit ihrem Job.
Um ein so hochkomplexes Produkt wie ein Triebwerk zu bauen, ist Teamarbeit und das Können vieler Spitzenkräfte gefordert. Die Triebwerksmacher:innen der MTU tragen alle ihren ganz eigenen, wichtigen Teil zur Triebwerksproduktion bei. Der vielzitierte Traum vom Fliegen ist hier überall spürbar – in den Büros der Entwicklungsabteilungen, an den hochmodernen Arbeitsplätzen in der Fertigung, in der Vorstandsetage. Egal, in welchem Bereich sie arbeiten: Sie alle nutzen die Chance, als Mitglied der weltweiten MTU-Familie immer stets vorn dabei zu sein.
Der AEROREPORT hat zehn Triebwerksmacher:innen der MTU am Standort München einen Tag begleitet – von der Logistik über die Entwicklung und Fertigung bis zur Qualitätssicherung. Hier berichten sie über ihre Arbeit, was ihnen besondere Freude daran bereitet und welchen individuellen Beitrag sie zum Triebwerk leisten.
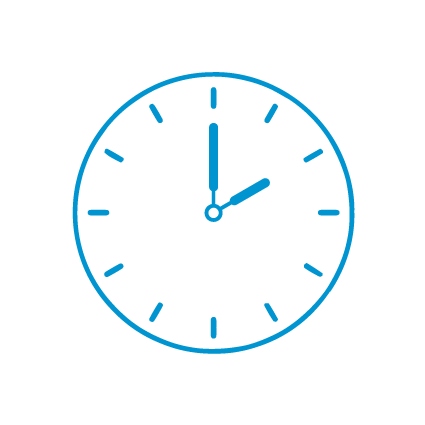
Beim Entgraten wird das Bauteil mittels eines Druckluftschleifers gefräst und versäubert.
Es ist zwei Uhr nachts und Manfred Glas ist hellwach. Der Zerspanungsmechaniker hält einen Leitkranz eines Niederdruckverdichters für das Eurofighter-Triebwerk EJ200 in seinen Händen. Das Bauteil soll entgratet werden. Mit einer Feile wird Material an der Kante des Werkstücks abgetragen. Glas legt sich das Bearbeitungsblatt für das Bauteil bereit. „Anhand der Zeichnung sehe ich, was ich zu entgraten habe.“ Er ist erfahren in diesem Job. „Das Blatt ist Vorschrift, auch wenn ich weiß, was ich zu tun habe. Sicherheit und Kontrolle haben höchste Priorität.“
Er montiert die Vorrichtung, die das Bauteil hält, auf den Entgratstand – eine Art kleine Hebebühne, die sich bis zu 180 Grad neigen lässt, damit Glas das Bauteil optimal bearbeiten kann. Der Leitkranz wird aufgespannt, Glas sucht den passenden Fräser raus und legt los – mit Schutzbrille und Gehörschutz. „Auch bei der Arbeitssicherheit werden bei der MTU keine Kompromisse gemacht, was ich wichtig und richtig finde. Auch eine Absauganlage läuft dauerhaft beim Bearbeiten der Teile.“
Glas arbeitet hochkonzentriert, mit ruhiger Hand und geschultem Blick. „Jedes Jahr absolviere ich den vorgeschriebenen Sehtest.“ Manche Bauteile erfordern fünf bis sechs Stunden Bearbeitungszeit. Der Leitkranz ist nach zwei Stunden fertig entgratet. Glas schickt ihn in die nächste Abteilung. „Jeder Tag ist mit neuen Herausforderungen gespickt. Ich bearbeite ein großes Spektrum an zivilen und militärischen Bauteilen. Das wird nie langweilig.“
Glas entgratet die Teile, nachdem sie vom Drehen oder Fräsen kommen, danach werden diese gereinigt, geprüft und schließlich montiert. Auch beim Montieren wird er von Zeit zu Zeit eingesetzt. Besonders gern arbeitet er nachts, wenn es in der MTU ruhig ist. „Ich vertiefe mich gern in meine Arbeit, ich kann dann alles um mich herum völlig ausblenden.“ Trotzdem ist er auch immer im Austausch mit den Kolleg:innen. „Wir bearbeiten die Bauteile sehr präzise und beachten exakt die geltenden Vorgaben. Das ist wichtig, denn schließlich bewegen unsere Triebwerke später Tausende Passagiere durch die Luft.“
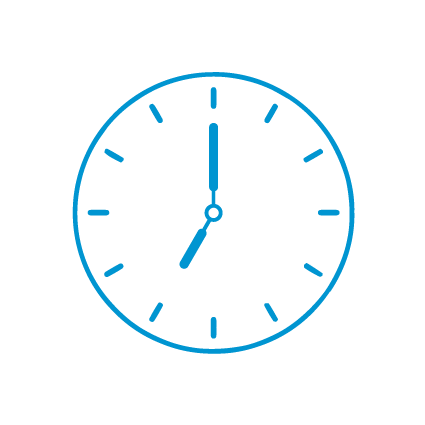
In der Schaufelfertigung der MTU werden unter anderem Hochdruckturbinenschaufeln für militärische und zivile Triebwerke hergestellt.
Es gibt Termine, an denen wird nicht gerüttelt. Es ist sieben Uhr und Florian Wutz, Teamleiter in der Schaufelfertigung, trifft sich wie jeden Morgen um diese Zeit mit seinem Team auf dem Shopfloor, wie der Produktionsbereich genannt wird. „In dem Meeting besprechen wir, wie wir unsere Fertigungsprozesse bestmöglich planen, umsetzen und optimieren“, sagt Wutz und begrüßt die Kolleg:innen aus der Fertigung, Arbeitsvorbereitung und Logistik. Die acht Teammitglieder stehen vor der Shopfloor-Tafel, auf der sie sämtliche relevanten Daten und Kennzahlen aus ihrem Bereich für alle gut sichtbar notiert haben.
Maximal zehn Minuten dauert der tägliche Informationsaustausch. Jeder fasst sich kurz, denn es gibt viel zu tun. Wutz kümmert sich um Prozesse und Personalplanung in der Schaufelfertigung – und er begeistert sich für das Produkt. „Dieses hochkomplexe Bauteil aus hochfesten Legierungen ist das Spannende in unserem Job“, sagt der gelernte Industriemechaniker und Maschinenbau-Ingenieur. „Ohne Schaufel fliegt kein Triebwerk, und wir betreuen dieses wichtige Bauteil vom Rohling bis zum Fertigteil.“
Heute spricht das Team über ein Detail beim Entgraten von Hochdruckturbinen-Schaufeln. „Diese Schaufeln werden im Heißgasbereich eines Triebwerks eingesetzt und sind Temperaturen von mehr als 1.000 Grad Celsius ausgesetzt“, erklärt Wutz. Die Qualität muss top sein. Die Schaufeln begutachtet er direkt im Anschluss an das Team-Meeting, und zwar dort, wo sie gefertigt werden.
„Ich mache mir in einem solchen Fall mein eigenes Bild, um dann zur Lösungsfindung beizutragen“, sagt der Teamleiter. Der direkte Austausch mit den Expert:innen aus der Fertigung sei durch nichts zu ersetzen. „Wir arbeiten in der Schaufelfertigung als großes Team zusammen.“ Wutz weiß, wovon er spricht. Er stellt sicher, dass alle Kolleg:innen aus seinem Team optimal eingesetzt werden und ihre Qualifikationen bestmöglich einbringen können. Engpässe sollen so gar nicht erst entstehen. Schließlich ist die Stückzahl, die es zu schaffen gilt, hoch: Rund 70.000 Schaufeln fertigt die MTU pro Jahr.
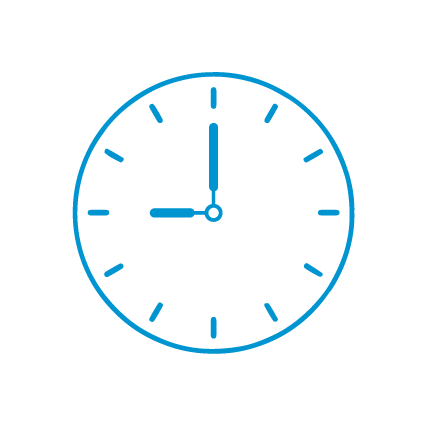
Verfahrensspezialist:innen sind für einen oder mehrere thematisch verknüpfte Spezialprozesse technisch zuständig.
Im Prüfraum dreht sich heute Morgen alles um Verdichterrotoren. Es ist 9 Uhr und Expert:innen aus der Produktion, Arbeitsvorbereitung, Qualitätslenkung sowie Strukturmechanik begutachten ein Bauteil. Mit dabei ist Lea Mainberger, Verfahrensspezialistin für Verfestigungsverfahren. Gemeinsam wird geklärt, wie im Fertigungsprozess eine spezielle Abdeckung für Blisks – das sind Hochtechnologie-Bauteile, bei denen Scheibe und Schaufeln integral gefertigt sind – optimiert werden kann.
„Ich arbeite an einer Schnittstelle zu mehreren Fachabteilungen“, sagt Lea Mainberger. „Wir stimmen uns fachübergreifend ab und entwickeln gemeinsam Lösungen, damit unsere Fertigungsprozesse optimal laufen.“ Die Wirtschaftsingenieurin mit Schwerpunkt Werkstofftechnologien arbeitet seit 2019 bei der MTU in der Abteilung für chemische und nicht-konventionelle Technologien.
Hier hat sie sich zu einer Verfahrensspezialistin für Verfestigungs- sowie Abrasivstrahlen entwickelt. Beim Verfestigungsstrahlen wird die Lebensdauer eines Bauteils mittels Einbringung von Druckeigenspannungen verlängert. „Dafür werden sehr kleine Stahlkugeln entweder gezielt über eine Düse auf das Bauteil gestrahlt oder mit Hilfe von Ultraschall so angeregt, dass die Kugeln eine ähnliche Wirkung erzielen“, erklärt sie. „Alle rotierenden und hochbeanspruchten Bauteile wie Scheiben, Schaufeln und Blisks werden auf diese Weise behandelt.“ Beim Abrasivstrahlen werden Oberflächen etwa von Gehäuseteilen gereinigt oder aufgeraut.
Lea Mainbergers Know-how ist gefragt, wenn es beispielsweise um Prozessänderungen und Erprobungen, um die Bewertung neuer Methoden zum Verfestigen und um die Zulassung der Verfahren bei Zulieferern geht. „Jeder Tag ist anders und spielt sich bei mir zwischen Fertigung und Schreibtisch ab“, sagt sie. Dabei ist sie auch von dem Teamspirit begeistert und dass sie sich zu hundert Prozent auf ihre Kolleg:innen verlassen kann.
„Bevor ich meine jetzige Aufgabe bei der MTU übernahm, wurde ich von einem langjährigen Experten eingearbeitet, der kurz darauf in den Ruhestand gegangen ist“, sagt sie. Zudem hat ihr die MTU die Möglichkeit gegeben, externe Kurse zu belegen, um Zusatzqualifikationen zu erwerben. Auch das mache ihren Job so spannend: „Ich kann mir hier immer neues Wissen aneignen, weil es fachlich so in die Tiefe geht.“
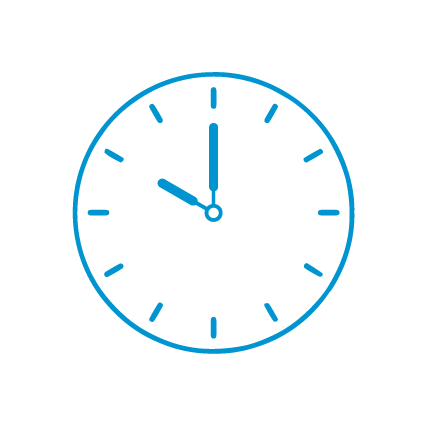
Die Galvanik ist für das Beschichten und Abziehen galvanischer sowie thermischer Beschichtungen zuständig.
„Uns kann man gar nicht übersehen, so viel Platz, wie wir hier einnehmen“, sagt Michael Blümel und zeigt auf zwanzig große Bäder, die sich in der Galvanik aufreihen. Es ist zehn Uhr und Blümel ist in seinem Element. Getestet wird eine neu konstruierte Vorrichtung für die erste Stufe des Mitteldruckverdichters für das TP400-D6, das den Militärtransporter Airbus A400M antreibt.
Die Vorrichtung deckt die Bereiche ab, die nicht beschichtet werden sollen. Routiniert überprüft Blümel, ob das Bauteil perfekt in die neue Vorrichtung passt. Stimmt die Dichtigkeit, wenn es in das galvanische Bad taucht? Wie steht es um die chemische Beständigkeit der Vorrichtung? 85 Zentimeter misst sie im Durchmesser. Für die großen Bauteile gibt es eigene Hebevorrichtungen, damit ein sicherer Umgang mit Bauteil und Vorrichtung gewährleistet wird.
„Wir beschichten bei diesem Bauteil nur eine winzige Nut mit einer Nickelschicht zum Schutz vor Verschleiß. Entsprechend müssen wir den Großteil mit der Vorrichtung abdecken“, sagt Blümel, der sich nach seiner Ausbildung zum Oberflächenbeschichter erst zum Teamkoordinator, dann zum Prozessverbesserer in der Galvanik weiterentwickelt hat.
Die MTU beherrscht eine Vielzahl galvanischer Verfahren für Neu- und Reparaturteile. „Jede rotierende Scheibe muss durch die elektrochemischen Prozesse im galvanischen Bad, um den Grundwerkstoff auf Fehler zu prüfen“, erläutert Blümel. Mit Hilfe der Elektrolyse werden metallische Schichten auf die Bauteile aufgetragen. Mit dieser Veredelung werden sie vor äußeren Einflüssen wie Hitze und Verschleiß geschützt.
„Wir können verschlissene Bereiche immer wieder neu beschichten und schenken so den Bauteilen, ein zweites, drittes oder viertes Leben. Das spart dem Kunden Kosten und schont zudem Ressourcen.“ An der Qualität wird aber nicht gespart. „Wir prüfen akribisch. Das Material muss einwandfrei sein. So sorgen wir dafür, dass jedes Bauteil perfekt beschichtet ist und den hohen Anforderungen der Flugsicherheit entspricht.“

Am Standort in München werden mehr als 5.000 Mitarbeiter:innen täglich mit einer Vielzahl an Gerichten im Betriebsrestaurant versorgt.
Es ist zwölf Uhr und der Koriander neigt sich dem Ende zu. Claude Fini platziert die frisch gehackten Kräuter neben dem Wok. Der Küchenleiter des MTU-Betriebsrestaurants verliert nie den Überblick, selbst wenn tausende hungrige MTU-Mitarbeiter:innen in das neue, sogenannte MTU-Werksviertel strömen. Fini empfängt sie mit einem strahlenden Lachen. „Ich bin für unsere Gäste immer ansprechbar.“ In der Küche gibt derweil sein Team Gas – gekocht, gegart und gedünstet wird allerdings auf Elektro- und Induktionskochfeldern.
Die Küchenausstattung im neu gebauten MTU-Werksviertel ist hochmodern. Die Speisen werden an vier Countern ausgegeben: „Heimat & Tradition“, „Salat & Grill“, „Pizza & Pasta“ und „Wok im Werk“. „Wir planen mit 1.500 bis 1.700 Essen pro Tag“, sagt Fini und organisiert den Nachschub am Heimatcounter. Heute hat sein Team 900 Schnitzel gewürzt, paniert und gebraten.
„Wir sind hier in Bayern. Schnitzel und Schweinsbraten kommen gut an, aber auch vegetarische und gesunde Gerichte genießen einen hohen Stellenwert auf unserer Speisenkarte“, sagt Fini. Im MTU-Betriebsrestaurant wird Fleisch vom „Strohschwein“ verarbeitet. Die Tiere werden artgerecht auf Stroh gehalten. Auch das Hühnerfleisch ist zu großen Teilen aus einem Freilandhof vor den Toren Münchens. Regionale Lebensmittel haben Vorrang. Erst kürzlich war Fini auf einem Bauernhof, der das Betriebsrestaurant mit Kartoffeln und Gemüse beliefert, um sich vor Ort von der Qualität zu überzeugen und die langfristige Lieferantenbeziehung zu pflegen.
„Wir machen fast alles frisch, Convenience-Essen kommt bei der MTU nicht auf den Tisch“, sagt der Küchenleiter. „Wir sorgen dafür, dass die Mitarbeiter:innen motiviert und fit ihre Arbeit verrichten können.“ Gemeinsames Essen, davon ist Fini überzeugt, fördert die Kommunikation und stärkt das „Wir-Gefühl“. Dieser Zusammenhalt ist ihm auch in seinem Team wichtig. „In Restaurantküchen geht es stressig zu“, sagt er. Umso wertvoller ist eine gute Organisation und Planung. „Und Spaß an der Arbeit, die möchte ich auch vermitteln.“
Um 13:45 Uhr schließt das Betriebsrestaurant. Pause. Für den Küchenleiter geht es später noch an den Schreibtisch. Die Bestellungen für die nächsten zwei Tage müssen raus. Kaiserschmarrn und Apfelstrudel sollen mit auf den Speiseplan. Süßes geht immer!
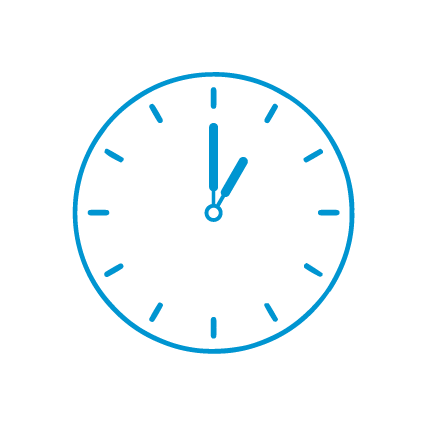
SAP Inhouse Consultant sind für die Konfiguration und Betreuung des SAP-Systems innerhalb der komplexen IT-Systemlandschaft der MTU verantwortlich.
Es ist 13 Uhr und Lisa Schneider ist in ein IT-Konzept für die Arbeitsplanung vertieft. „Während meines ersten Jobs habe ich schnell gemerkt, dass ich eine Affinität zur IT und zur SAP-Software habe“, berichtet die SAP Inhouse-Consultant, die bei der MTU hauptsächlich das SAP-Modul Arbeitsplanung betreut. „Das SAP-System erstreckt sich über die gesamte MTU. In meinem Bereich passen wir es auf die speziellen Anforderungen der Fertigung an.“
Anfang 2022 kam Lisa Schneider zur MTU. „Ursprünglich komme ich aus dem Prozessmanagement im Einkauf, ich bin also Quer-Einsteigerin in der IT“, sagt sie. Als IT-Expertin gehört sie auch zu einem Kompetenzteam, das sich regelmäßig trifft. Hier steht sie im direkten Austausch mit den Kolleg:innen aus den Fachbereichen der Fertigung. „SAP Inhouse-Consulting ist keine Aufgabe, in der man ausschließlich allein vor dem Rechner sitzt“, sagt sie. „Im Gegenteil: Kommunikation und Teamfähigkeit sind gefragt, weil wir eng mit den Fachbereichen zusammen arbeiten.“
Dass sie selbständig und eigenverantwortlich Lösungen umsetzen kann, beflügelt sie zusätzlich. „Mich begeistert vor allem, Aufträge vom Konzept bis zum fertigen Produkt betreuen zu können.“ Zum Teil sind die Projekte so komplex, dass die Umsetzung Monate in Anspruch nimmt. Manche Anpassungen an bestehenden Funktionen kann sie dagegen nach zwei Wochen erfolgreich abschließen. „Nicht immer lässt sich jedes Fachkonzept aus der Fertigung eins zu eins in ein IT-Konzept umsetzen. Dann ist Kreativität gefragt, um entsprechende Alternativen zu erarbeiten.“
Der IT-Bereich ist schnelllebig – gerade auch mit Blick auf die zunehmende intelligente digitale Vernetzung von Maschinen und Prozessen innerhalb des Unternehmens, auch Industrie 4.0 genannt. „Ich eigne mir ständig neues Wissen an, auch das macht meinen Job so spannend“, sagt Lisa Schneider. „Und ich trage dazu bei, dass die MTU qualitativ erstklassige Triebwerke herstellt, indem ich dafür sorge, dass die jetzigen und künftigen Anforderungen der Fertigung im System bestmöglich umgesetzt sind.“
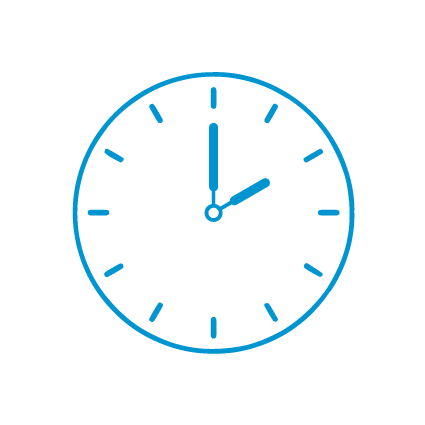
Qualitätslenker:innen gewährleisten in allen möglichen Bereichen die Einhaltung des zu Grunde liegenden Regelwerks im Sinne der Qualität und Sicherheit.
Die winzige Abweichung in der Schaufel einer Turbine ist mit bloßem Auge kaum zu erkennen. Dennoch wurde sie in der Sichtprüfung entdeckt. Es ist 14 Uhr und Marc Rehermann, Qualitätslenker in der Montage, wird umgehend informiert. Er eilt herbei: „Mein Büro liegt nur einen Flur von der Montagelinie entfernt. Das sind kurze Wege für schnelle Entscheidungen.“
Die Expert:innen für das Bauteil arbeiten vor Ort. „Das ist ein klarer Vorteil. Wir können uns mit den Spezialist:innen aus der Konstruktion und Fertigung direkt in Verbindung setzen, um die weiteren Maßnahmen abzustimmen. Produktabweichungen bewerten wir stets im Team“, sagt Rehermann.
Das Abweichungsmanagement zählt ebenso wie die Prozessverbesserung zu den wichtigsten Aufgaben des Qualitätslenkers. „Wir bewerten jede noch so kleine Auffälligkeit“, sagt er. „Ich bin an der Entscheidung beteiligt, ob ein Bauteil eingebaut, nachgearbeitet oder aussortiert wird. Das ist eine hohe Verantwortung.“
Der 26-Jährige hat Luft- und Raumfahrttechnik an der FH Aachen studiert. Seit 2022 arbeitet er bei der MTU. „Während meines Studiums habe ich bei der MTU Maintenance Hannover ein Praktikum absolviert“, berichtet er. „Das hat mich so fasziniert, dass mir klar wurde, dass ich als Ingenieur auf jeden Fall direkt am Triebwerk arbeiten möchte.“
Hier ist sein theoretisches Know-how ebenso gefragt wie die Erfahrungen und Expertise der Fachkräfte aus der Fertigung und Montage. „Wir schauen aus vielen unterschiedlichen Blickwinkeln auf das Bauteil, um ein Höchstmaß an Qualität sicherzustellen“, so Rehermann. „Wir sorgen dafür, dass überall da, wo MTU drauf steht, auch MTU-Qualität drin ist.“
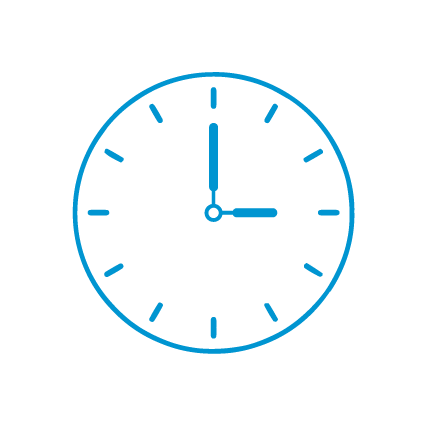
Die Ausgangslogistik ist verantwortlich für die Versand- und Transportabwicklung sowie die Versandkontrolle und Qualitätssicherung.
Es ist 15 Uhr und in der Ausgangslogistik wissen alle, was zu tun ist. Jeder Handgriff sitzt. Der Lkw, der von hier jeden Tag mit MTU-Bauteilen zum Flughafen München startet, steht bereit. 15.45 Uhr ist Deadline, dann muss auch das letzte Paket verladen sein. „Nachmittags verdichtet sich die Arbeit“, sagt Benedikt Buchner, Leiter Ausgangslogistik und Qualitätskontrolle, als er in die Halle kommt. Alles läuft nach Plan. Buchner kann sich auf sein Team verlassen. „Selbständiges Arbeiten ist mir, aber auch meinem Team wichtig.“
Die Zollabwicklung ist komplex. Buchner hat die erforderlichen Dokumente, Zertifikate und Papiere geprüft. Alles muss stimmen. Zum Beispiel für die Blisks, die heute auf die Reise geschickt werden. „Die Verpackung für die Blisks haben wir extra entwickeln lassen“, berichtet er. „Mit der neuen Verpackung sparen wir Arbeitszeit und Kosten, zudem ist sie nachhaltig und kommt ohne Folie aus.“
Buchner spricht von Verpackungs-Know-how und übertreibt nicht. „Wir versenden Millionenwerte, die mit größter Sorgfalt zu verpacken sind. Flugsicherheit ist unser oberstes Gebot, wir haben eine Null-Fehler-Toleranz. Unsere Partner möchten ihre Ware unbeschädigt entgegennehmen – und pünktlich!“ Das gelingt ihm und seinem Team jeden Tag aufs Neue, Kundenreklamationen sind gleich null. „Wir sind mit Blick auf die Qualität das letzte Bindeglied in der Triebwerksfertigung. Wir stellen sicher, dass jedes Bauteil perfekt verpackt und zuverlässig seinen Empfänger erreicht.“
Auch deshalb ist Buchner stets im direkten Austausch mit Lieferanten, Speditionen und Kunden - weltweit. Er weiß, welche Anforderungen jeder Einzelne an die Transporte stellt. Wenn am nächsten Morgen eine Mail von einem Kunden aus den USA in seinem Postfach landet, dass die Bauteile in der vorgegeben Zeit geliefert worden sind, weiß Buchner, dass die Abläufe in seinem Bereich stimmen.
2001 ist er bei der MTU durchgestartet. Die Begeisterung für seinen Job beflügelt ihn seit nunmehr über 20 Jahren. „Logistik bewegt“ heißt es. Buchner geht noch einen Schritt weiter: „Wir haben hier im Team eine richtige Leidenschaft für Logistik. Wir führen den hohen Qualitätsanspruch in der Triebwerksfertigung bis zur Auslieferung fort“, sagt er und wirft einen Blick in die Halle. Daumen hoch. Der Lkw verlässt den Verladebereich und fährt Richtung Flughafen.
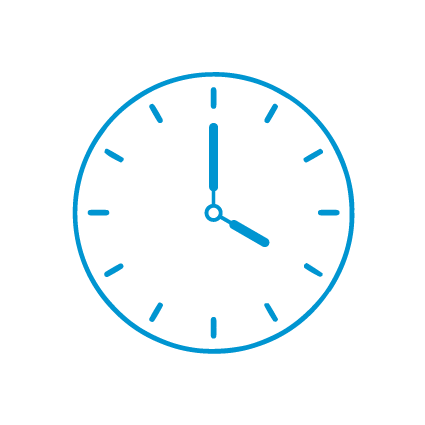
In der Entwicklung für Strukturmechanik wird die strukturelle Integrität der Bauteile sichergestellt.
Dr. Saskia Lessig schaut kurz auf. Es ist 16 Uhr und damit noch Zeit, ihre Notizen durchzugehen, die sie aus dem vorangegangenen Meeting mitgenommen hat. Einmal pro Woche trifft sich das Bauteilteam, das für die Schaufel der Mitteldruckturbine des TP400-D6 Triebwerks zuständig ist. „Wir arbeiten interdisziplinär, das heißt fachübergreifend“, sagt die Entwicklungsingenieurin für Strukturmechanik. In dem Meeting besprechen sich Expert:innen beispielsweise aus dem Engineering, der Fertigung, Qualitätssicherung und aus dem Programmmanagement entsprechend der integrierten Produktentwicklung. „Wenn es um die strukturelle Integrität der Schaufel geht, schauen alle gespannt auf mich“, erzählt sie und lacht. „Die Hausaufgaben aus dem Meeting schaue ich mir dann in Ruhe an meinem Schreibtisch an.“
Die Fragen, die an sie und ihre Fachkolleg:innen aus der Strukturmechanik herangetragen werden, sind komplex und technisch hochanspruchsvoll. „Solche Fragen durchdringen wir immer im Team“, berichtet sie. „Gemeinsam stellen wir sicher, dass unsere Ersatzmodelle fehlerfrei sind und höchste Qualitätsstandards erfüllen. Flugsicherheit ist unser oberstes Ziel.“ Deshalb erfolgen auch sämtliche Freigaben für die Berechnungen stets im Team und mindestens mit dem 4-Augen-Prinzip. „Wir sind Spezialist:innen, aber keine Einzelkämpfer:innen, dafür ist das Fachgebiet zu groß. Jede und jeder von uns besetzt ein Nische, aber zusammen finden wir die Lösung.“
Saskia Lessigs Know-how ist besonders gefragt, wenn es um Numerik oder um stochastische Fragestellungen geht. Die Mathematikerin hat auf dem Gebiet der Kontaktmechanik promoviert. „Damit habe ich die Brücke von der theoretischen Mathematik zum Maschinenbau geschlagen.“ Sie nennt es eine „glückliche Fügung“, dass sie von ihrer damaligen Professorin auf die MTU aufmerksam gemacht worden ist. Durch ihre Promotion ist sie zur MTU gekommen – und geblieben. Hier kann sie auch ihr Wissen aus ihrem Nebenfach Informatik einbringen, beispielsweise wenn es um die Prozess- und Methodenintegration geht.
Die Herausforderungen, die ihr Job immer wieder mit sich bringt, begeistern sie. „Die Anforderungen an unsere Triebwerksprogramme werden immer anspruchsvoller – gerade auch mit Blick auf die innovativen Antriebstechnologien, die wir entwickeln, damit Flugzeuge künftig emissionsfrei abheben können.“
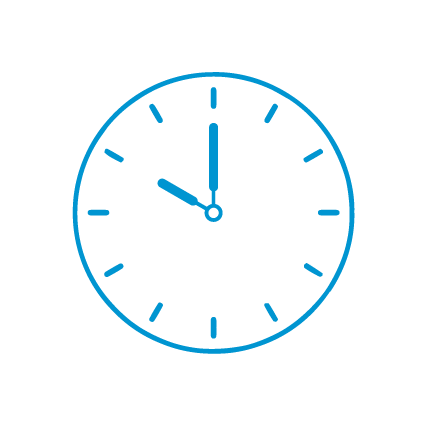
In der Thermischen Spritzerei werden komplexe Triebwerksbauteile mit Hitzeschutz und Verschleißschutzschichten beschichtet.
Es ist 22 Uhr. Vor einer halben Stunde hat Maximilian Bayer seine Nachtschicht in der Thermischen Spritzerei begonnen. Von Müdigkeit keine Spur. Er nimmt eine Scheibe für das GTF-Triebwerk PW1100G-JM unter die Lupe. Wo fliegende – und extrem sicherheitskritische – Teile bearbeitet werden, ist der prüfende Blick erste Pflicht. Die Sichtprüfung zeigt keine Auffälligkeiten und Abweichungen. Das neue Bauteil ist perfekt. Bayer deckt es mit hitzebeständigen Silikonringen ab. „So werden nur die Bereiche beschichtet, die auch beschichtet werden sollen.“
2010 hat er mit einer Ausbildung zum Industriemechaniker seine Karriere bei der MTU gestartet. Jetzt ist er Experte in der thermischen Beschichtung von Triebwerksbauteilen. Bayer befördert die Scheibe in eine Strahlanlage. „Dort wird die Oberfläche aufgeraut, damit die Haftschicht besser haftet.“ Dann schiebt er das Bauteil in die Beschichtungsanlage. Dort wird unter Einsatz eines Roboters und eines Plasmabrenners die Hitze- und Verschleißschutzschicht auf die Scheibe aufgetragen. Die dabei entstehenden Kanten entgratet er mit Bürste und Feile. „Auch wenn wir hier in der Fertigung mit hochmodernen Maschinen arbeiten, ist handwerkliches Können in meinem Job erforderlich.“
„Ich bearbeite ungefähr 25 verschiedene Bauteile. Jeder Arbeitstag ist anders, das gefällt mir.“ Selbständiges Arbeiten ist gefragt, aber ohne Teamarbeit geht es nicht. „Ohnehin gilt bei uns das Vier-Augen-Prinzip, beispielsweise wenn es um das Vermessen des beschichteten Bauteils geht. Die Maße müssen stimmen, wir liefern nur erstklassige Qualität.“
Für Bayer passt an seinem Arbeitsplatz alles: Das Team, zu dem auch viele junge Leute gehören, aber auch die Entwicklungschancen bei der MTU. Und noch etwas begeistert den 27-Jährigen: das Produkt. „Kürzlich bin ich mit einer A320neo mit dem PW1100G-JM geflogen. Als ich kurze Zeit später an meinem Arbeitsplatz ein Bauteil dieses Triebwerkstyps in den Händen hielt, dachte ich: Cool, mit so einem Triebwerk bin ich gerade geflogen. Nicht auszuschließen, dass ich dafür sogar ein Bauteil beschichtet habe.“
Wir sind über 11.000. Wen wir noch brauchen? Sie!
Helfen Sie uns als IT-Expert:in dabei, das Unternehmen bei der Digitalisierung auf neue Ebenen zu heben. Steuern und Überwachen Sie als Controller:in unsere Finanzen und unterstützen Sie bei strategischen Unternehmensentscheidungen. Stellen Sie als Qualitätsprüfer:in sicher, dass unsere Produkte und Prozesse höchsten Standards entsprechen. Unterstützen Sie uns als Fluggerätmechaniker:in bei der Montage oder Instandhaltung unseres breiten Triebwerksportfolio.
Und das ist längst nicht alles: Ob in der Konstruktion, im Einkauf, im Personalwesen, in der Galvanik, auf den Prüfständen; ob Azubis, dual Studierende, Absolvent:innen, Berufserfahrene oder Führungskräfte – bei der MTU ist für jeden etwas dabei.
Unser starkes Team sorgt weltweit dafür, dass sich unsere Partner und Kunden immer auf die Qualität der MTU verlassen können. Wir sind als Luftfahrtunternehmen Teil einer riesigen Transformation. Emissionsfreies Fliegen ist unsere Vision. Und um diese Vision Wirklichkeit werden zu lassen, müssen neue, revolutionäre Triebwerkskonzepte entwickelt werden. Dafür brauchen wir wissensdurstige und mutige Ingenieur:innen, die Teil dieser Transformation sein wollen.
Und schon gewusst? Wir sind nicht nur Triebwerkshersteller sondern bilden in unserer Betriebsgastronomie am Standort in München auch Köche aus. Es lohnt sich also, einmal in unserer Jobbörse vorbeizuschauen.
Werden Sie Teil der großen MTU-Familie und bewerben Sie sich jetzt!