good-to-know
Kurz erklärt: Das elektrochemische Bearbeiten von Bauteilen
Mit dem (P)ECM-Verfahren können schwer zerspanbare Bauteile und komplexe Geometrien verschleißarm und kostengünstig hergestellt werden. Wir erklären, wie es funktioniert.
09.2024 | Autorin: Isabel Henrich | 4 Min. Lesezeit
Autorin:
Isabel Henrich
ist studierte Politologin und Kommunikationswissenschaftlerin. Bei der MTU steuert sie den redaktionellen Prozess des AEROREPORTs und ist zuständig für die Konzeption und Entwicklung der Inhalte.
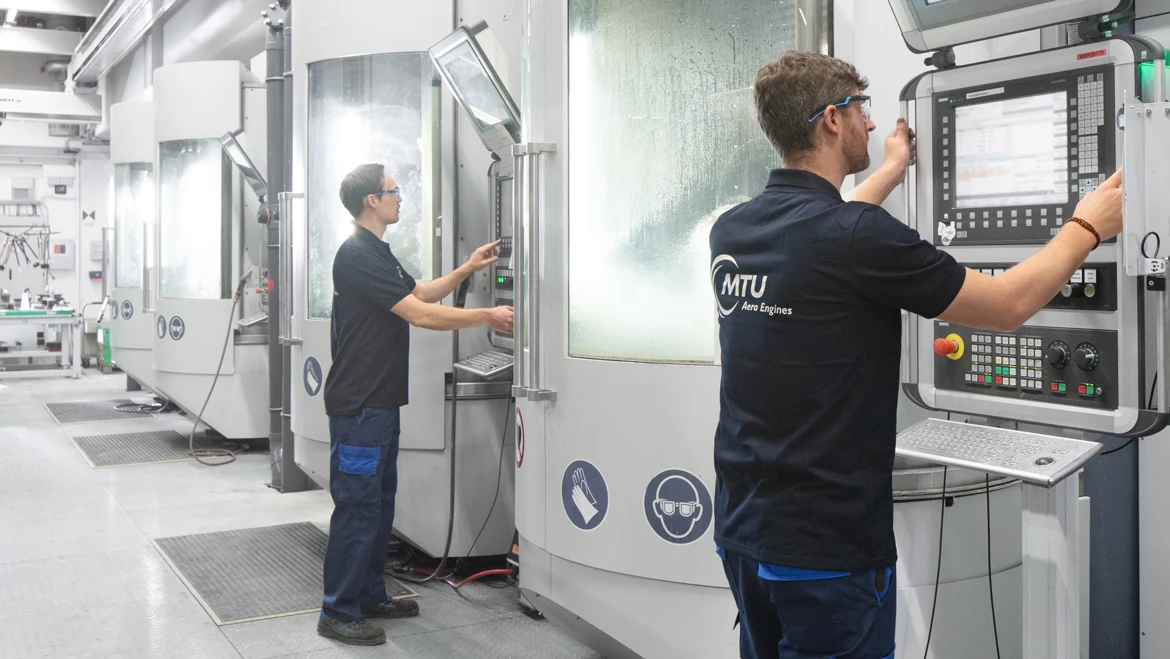
Flugzeugtriebwerke sollen weniger Kraftstoff verbrauchen, weniger Emissionen ausstoßen und zudem auch leiser werden. Dabei spielt auch das Gewicht beim Fliegen eine erhebliche Rolle: Je leichter die Bauteile eines Flugzeuges sind, desto weniger Energie muss beim Flug aufgewendet werden und desto mehr Kerosin kann gespart werden.
Diesen Effekt erbringen auch die sogenannten Blade Integrated Disks, kurz Blisks, bei denen Schaufel und Scheibe aus einem Stück bestehen. Die Hochtechnologie-Bauteile, die in Verdichtern zum Einsatz kommen, haben gegenüber ihren Pendants mit gesteckten Einzelschaufeln einen großen Vorteil: Durch die integrale Bauweise wird die Randlast der Rotorscheiben reduziert und damit Gewicht gespart. Zusätzlich trägt der Wegfall von Leckagen zu einem besseren Wirkungsgrad im Verdichter bei. Die Folge: Triebwerke werden insgesamt kompakter, leichter und verbrauchen weniger Kraftstoff, was wiederum den CO2-Ausstoß senkt.
Die vorderen Stufen eines Hochdruckverdichters bestehen aus Titan, bei den hinteren Stufen herrschen jedoch deutlich höhere Temperaturen von bis zu 650 Grad Celsius. Diese werden daher aus Nickel-Basis-Werkstoffen hergestellt, denn sie weisen die notwendige Festigkeit für hohe Temperaturen auf. Während die Konturen in Titan-Schaufeln in der Fertigung klassischerweise herausgefräst werden, sind Nickel-Blisks nur schwer schweiß- und zerspanbar. Hinzu kommt die extrem komplexe 3D-Geometrie der Blisk-Schaufelblätter. Die MTU Aero Engines wendet daher das (P)ECM-Verfahren an.
Mit dem (P)ECM-Verfahren nutzt die MTU eine kostengünstige und verschleißarme Alternative zum konventionellen Fräsen für die Bearbeitung von Nickel-Blisks.
Innovative Fertigungstechnik: Electro Chemical Machining (ECM)
Electro Chemical Machining, kurz ECM, lautet der Oberbegriff, unter dem sich unterschiedliche Verfahren des elektrochemischen Abtragens gruppieren. Allen gemein ist, dass mit Hilfe eines Elektrolyten sowie elektrischen Stroms ein metallischer Werkstoff formgebend aufgelöst wird. Dabei dient das zu bearbeitende Werkstück als Anode (positiver Pol) und das dreidimensionale, metallische Abformwerkzeug als Kathode (negativer Pol). Als Elektrolyt kommt eine wässrige Natriumnitratlösung zur Verwendung, die zwischen Anode und Kathode fließt. Diese Flüssigkeit hat drei Funktionen: Sie stellt eine elektrisch leitende Verbindung her, sorgt für den Abtransport des abgetragenen Materials sowie der entstehenden Wärme und Gase.
Beim ECM-Verfahren wird das Bauteil bei ungepulster Gleichspannung durch konstanten Vorschub der Werkzeug-Kathode bearbeitet bis die gewünschte Werkstückkontur (Bauteilkontur) erreicht ist. Das konventionelle ECM-Verfahren erzielt hierbei hohe Abtragsraten bei eher geringer Präzision mit einer Abbildegenauigkeit von 0,1 bis 0,5 mm.
Das auf dem ECM-Verfahren basierende Puls-ECM funktioniert vom Prinzip her gleich: Das Bauteil wird durch konstanten Vorschub der Werkzeug-Kathode bearbeitet, allerdings wird hier eine elektrisch gepulste Gleichspannung angelegt. So erreicht das Verfahren zwar eine geringere Abtragrate, aber auch eine höhere Präzision.
PECM: MTU als Vorreiter in der Implementierung
Die höchste Präzision kann mit dem PECM-Verfahren (Precise Electrochemical Machining) erreicht werden. Das Verfahren arbeitet mit engen Arbeitsspalten und ermöglicht dadurch eine präzise Abbildung von komplexen Geometrien. Da bei kleinen Spalten der Elektrolytaustausch nicht mehr optimal funktioniert, wird der Prozess mit mechanisch gepulster Kathode durchgeführt. Der Arbeitsstrom wird immer dann eingeschaltet, wenn sich die Kathode nahe dem engsten Spalt befindet. Die MTU hat dieses Verfahren entwickelt und weltweit erstmals zur Herstellung von Bauteilmerkmalen von Nickel-Blisks industrialisiert. Auch die heute im Einsatz befindlichen PECM-Anlagen sind made by MTU.
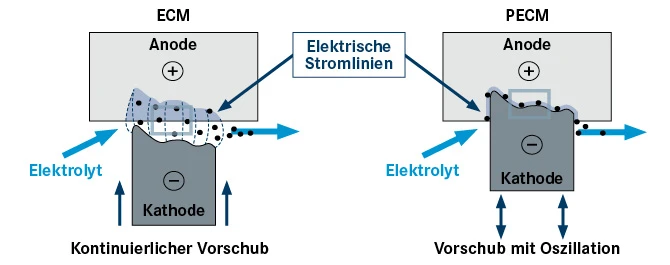
Wirkprinzip: Mit Hilfe eines Elektrolyten sowie elektrischen Stroms wird ein metallischer Werkstoff formgebend aufgelöst. Dabei dient das zu bearbeitende Werkstück als Anode (positiver Pol) und das dreidimensionale, metallische Abformwerkzeug als Kathode (negativer Pol).
Effiziente Bearbeitung durch differenzierte ECM-Techniken
Einer der Vorteile des elektrochemischen Abtragens gegenüber dem herkömmlichen Fräsen: Da das Bauteil nicht berührt wird, verschleißen die Werkzeuge nahezu nicht und Bearbeitungsspuren am Bauteil bleiben aus. Beides spart Kosten ein. Allerdings können mit dem PECM-Verfahren etwa keine scharfen Kanten geformt werden, was mit dem Fräsen möglich ist, da durch die sich an den Kanten verdichtenden Stromlinien ein höherer Abtrag entsteht.
Dieser Inhalt könnte Sie auch interessieren
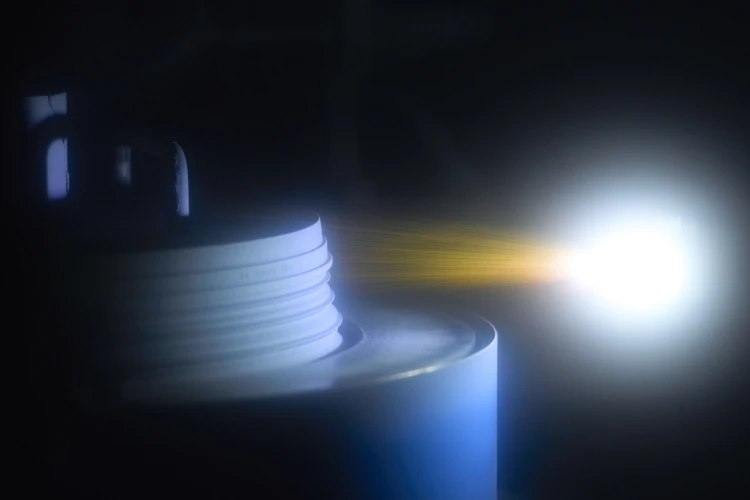
Verfahren der thermischen Oberflächenbeschichtung
Temperaturbeständigkeit, Korrosionsfestigkeit, Härte, Stabilität, Druckfestigkeit, Langlebigkeit – an jedes Bauteil im Triebwerk werden spezifische Anforderungen gestellt. Beschichtungen helfen, diese exakt zu erfüllen. Das Spektrum der Verfahren, die dafür zur Verfügung stehen ist riesig. Wir stellen eine Auswahl vor.
Die durchschnittliche Bearbeitungszeit der Bauteilmerkmale pro Nickel-Blisk liegt bei ca. 24 Stunden. Um den Prozess so effizient wie möglich zu gestalten, werden die drei unterschiedlichen ECM-Verfahren bei verschiedenen Bearbeitungsschritten angewendet. So wird das klassische ECM-Verfahren für Vor-, Zwischen- und Kantenbearbeitung verwendet. Puls-ECM und PECM kommen vorwiegend für den letzten Feinschliff zum Einsatz.
Nächster Entwicklungs-Meilenstein
Seit einigen Jahren forschen die Ingenieur:innen der MTU daran, wie die beim elektrochemischen Abtragen entstehenden gesundheitsschädlichen Chrom-VI-Verbindungen reduziert werden können. Im Rahmen eines Technologieprojektes zeigten sie, dass mit einer alternativen Salzlösung - Eisen-II-Nitrat - die Cr(VI)-Verbindungen zu Cr(III)-Verbindungen reduziert werden können und mit dem ECM-Schlamm aus dem System abgetrennt werden. Das Projektteam der MTU entwickelte daraufhin ein Ionentauscher-Verfahren, welches automatisch Eisen-II-Nitrat produziert und den Stoff, gesteuert über die Leitwarte, kontinuierlich ins (P)ECM-Elektrolytmanagementsystem als Reduktionsmittel dosiert. Der im ersten Halbjahr 2023 in Serie gegangene Aufbau bei der MTU ist weltweit einmalig.
Ab 2026 plant die MTU mit neu entwickelten ECM-Anlagen auch die Profilnuten von Niederdruckturbinen-Scheiben zu bearbeiten, als Alternative zum konventionellen Räumprozess.
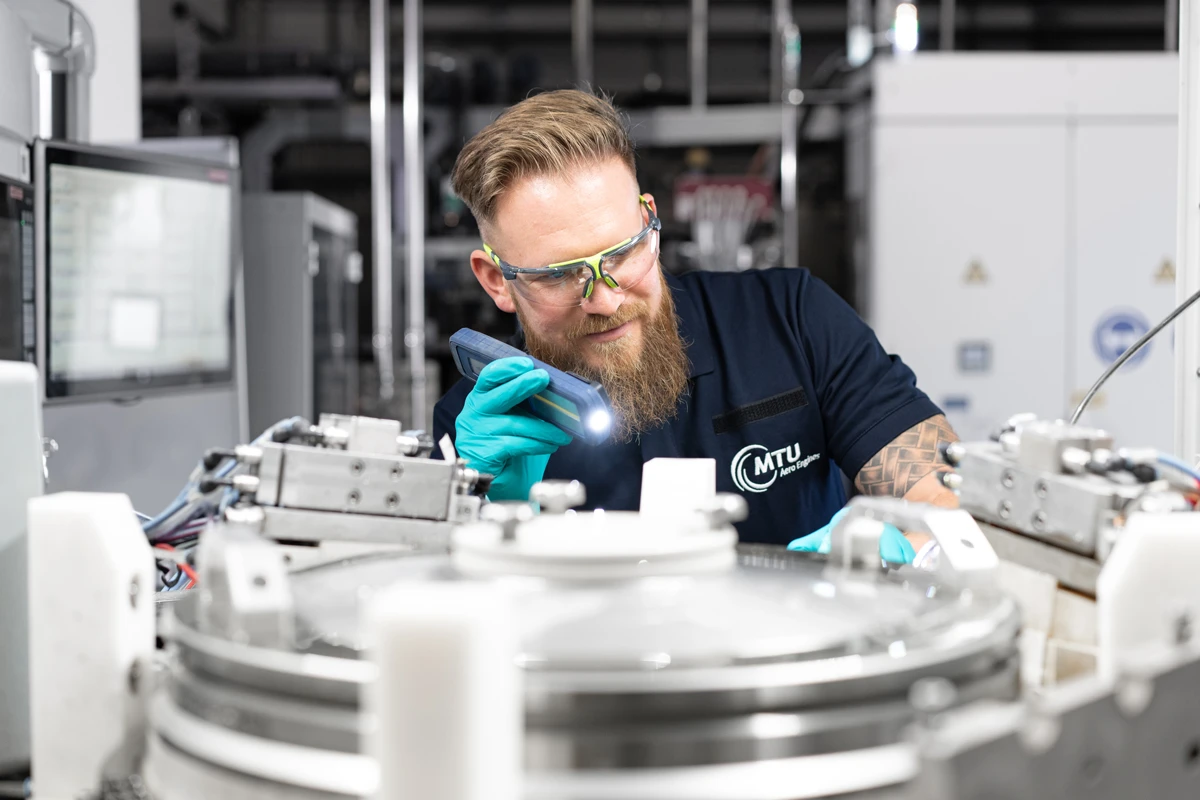
Effiziente Bearbeitung: Da das Bauteil nicht berührt wird, verschleißen die Werkzeuge nahezu nicht und Bearbeitungsspuren am Bauteil bleiben aus.