good-to-know
Verfahren der thermischen Oberflächenbeschichtung
Temperaturbeständigkeit, Korrosionsfestigkeit, Härte, Stabilität, Druckfestigkeit, Langlebigkeit – an jedes Bauteil im Triebwerk werden spezifische Anforderungen gestellt. Beschichtungen helfen, diese exakt zu erfüllen. Das Spektrum der Verfahren, die dafür zur Verfügung stehen ist riesig. Wir stellen eine Auswahl vor.
Autorin: Monika Weiner | 6 Min. Lesezeit veröffentlicht am: 06.11.2023
Autorin:
Monika Weiner
arbeitet seit 1985 als Wissenschaftsjournalistin. Die Diplomgeologin interessiert sich vor allem für neue Entwicklungen in Forschung und Technik sowie deren gesellschaftliche Auswirkungen.
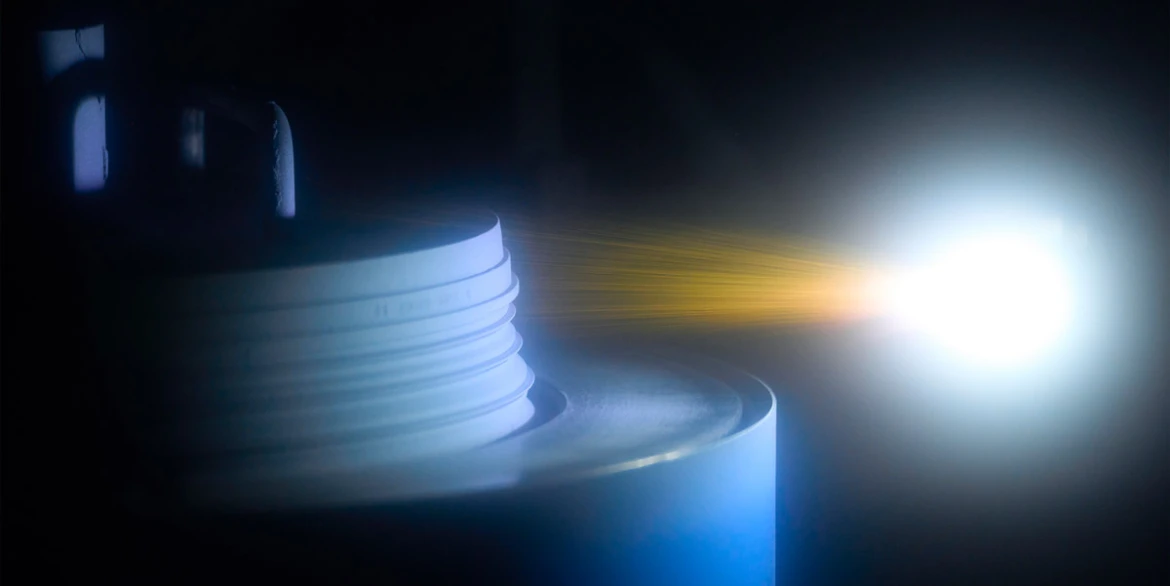
Die Anforderungen an die Bauteile im Triebwerk sind enorm. Mit verschiedenen thermischen Beschichtungsverfahren lassen sich die Oberflächen gezielt veredeln, um den Wirkungsgrad zu verbessern und die Lebensdauer zu verlängern. Bei den thermischen Beschichtungsverfahren wird grundsätzlich zwischen drei Verfahrenstypen unterschieden:
- Thermisches Spritzen: Schichtbildung aus schmelzflüssigen Partikeln
- Physical Vapor Deposition (PVD): Schichtbildung aus der Dampfphase (atomisiertes bzw. ionisiertes Beschichtungsmaterial)
- Chemical Vapor Deposition (CVD): Schichtbildung aus einer chemisch reagierenden Dampfphase
Der AEROREPORT stellt eine Auswahl an Verfahrensvarianten, Schichteigenschaften und Anwendungsbeispielen vor:
1. Thermisches Spritzen:
Hierbei werden die Substanzen, die eine Schicht auf dem Werkstück bilden sollen, in der Regel aufgeschmolzen. Die Energie hierfür liefern Lichtbogen, Flammen oder Gase im Plasmazustand. Die als Pulver oder Draht eingesetzten Werkstoffe (reine Metalle, Metalllegierungen, Keramiken oder organische Polymere) gelangen als feiner Strahl aus flüssigen Partikeln auf die Oberfläche des Werkstücks.
Plasmaspritzen
Beim Plasmaspritzen spielen ionisierte Gase eine Schlüsselrolle. Diese entstehen, wenn ein Lichtbogen gezündet wird, wenn sich also hohe Spannungen zwischen zwei Elektroden entladen und dabei das Gas, das sich zwischen ihnen befindet, ionisiert. Gesteuert werden die Eigenschaften des Plasmas vor allem durch die Art und Zusammensetzung der verwendeten Gase, die zwischen den Elektroden hindurch geführt werden. Meist kommen hier Gemische aus Edelgasen, wie Argon oder Helium mit Wasserstoff oder Gemische aus Stickstoff und Wasserstoff zum Einsatz, wobei mit zunehmender Wasserstoff-Konzentration die Temperatur ansteigt. In die Plasmaflamme werden pulverförmige, metallische oder keramische Werkstoffe durch eine Düse zumeist radial hineingespitzt, auf bis zu mehrere Tausend Grad erhitzt und im aufgeschmolzenen Zustand auf das zu beschichtende Werkstück gelenkt.
Plasmaspritzen wird im Triebwerksbau vor allem für die Beschichtungen von Materialien genutzt, die einen hohen Schmelzpunkt haben, beispielsweise Hartmetalle oder Keramiken. Schichten aus solchen sehr widerstandsfähigen Materialien werden an den unterschiedlichsten Stellen im Triebwerk benötigt.
Hochgeschwindigkeits-Flammspritzen
Beim Hochgeschwindigkeits-Flammspritzen (englisch: High Velocity Oxygen Fuel, kurz: HVOF) wird unter hohem Druck aus einer Brennkammer in eine etwa 60 Zentimeter lange Flamme das Spritzpulver eindosiert. Die Flamme entsteht durch Verbrennung von Kerosin oder Wasserstoff mit reinem Sauerstoff. Durch die hohe Gasgeschwindigkeit treffen die Spritzpartikel mit Überschallgeschwindigkeit auf die zu beschichtende Bauteiloberfläche. Die hohe Partikelgeschwindigkeit führt zu einer kurzen Verweildauer der Spritzpartikel in der Flamme, sodass die Partikel kaum durch die umgebende Atmosphäre oxidiert werden können. Auch Umwandlungs- oder Zersetzungsreaktionen der Spritzpartikel werden stark reduziert. Am Ende entstehen dichte, besonders gut haftende Schichten mit einer relativ glatten Oberfläche, wodurch die mechanische Nacharbeit bei einigen Applikationen entfallen kann.
Mit dem Hochgeschwindigkeits-Flammspritzen können gut haftende, dichte Beschichtungen erzeugt werden. Das Verfahren wird bevorzugt eingesetzt für harte Verschleißschutz-Schichten auf Lagersitzen von Wellen (Wolframkarbid), auf Statoren in der Turbine (Stellite) sowie als Oxidationsschutz auf Turbinenschaufeln (MCrAlY).
Pulverflammspritzen
Beim Pulverflammspritzen kommt eine Flammspritzpistole zum Einsatz, aus der, ähnlich wie beim autogenen Schweißen, eine Acetylen-/Sauerstoffflamme austritt. Die Flamme erreicht Temperaturen von bis zu 3.000 Grad Cesius. Die Gasgeschwindigkeit ist relativ niedrig. Somit ist dieses Verfahren prädestiniert zur Herstellung von porösen, metallischen Schichten oder porösen Belägen aus Aluminiumoxid. Das Verfahren ist ungeeignet für carbidische Werkstoffe und höchstschmelzende Keramiken wie Zirkonoxid.
Die Methode eignet sich, um poröse Beschichtungen herzustellen, beispielsweise die ausreibbaren Opferschichten (Einlaufbeläge oder Abradables) auf Gehäusen, welche verhindern, dass die Rotorschaufeln beim Anstreifen im Betrieb Schaden nehmen.
Lichtbogen-Drahtspritzen
Beim Lichtbogen-Drahtspritzen liefert ein elektrischer Lichtbogen die Energie. Dieser entsteht, wenn sich starke Spannungen zwischen Elektroden entladen. Bei dieser Verfahrensvariante bestehen die beiden Elektroden aus Drähten des Beschichtungswerkstoffs. Durch den Lichtbogen schmelzen die Drahtenden ab und werden durch ein Zerstäubergas, meist Pressluft, als schmelzflüssiger Partikelstrahl auf die zu beschichtende Oberfläche gerichtet. Die Drähte werden kontinuierlich nachgeführt, sodass der Lichtbogen quasi immer an der gleichen Stelle brennt.
Die Schichten, die so entstehen, können bis zu mehreren Millimetern dick aufgetragen werden, haben eine gute Haftfähigkeit und lassen sich mechanisch gut nachbearbeiten. Das Verfahren wird daher oft in der Instandhaltung genutzt, um verschlissenen Bauteilen ihre ursprüngliche Geometrie wiederzugeben.
Kaltgas-Beschichtungen
Bei Kaltgasbeschichtungen (englisch: Cold Spray) wird das Pulver, mit dem beschichtet werden soll, nicht aufgeschmolzen, sondern nur erwärmt. Hierfür reichen relativ moderate Temperaturen bis maximal 1.000 Grad Celsius. Erzeugt werden diese elektrisch in einem Vorheizer und zusätzlich in einer Spritzpistole, aus der Stickstoff bei ca. 50 bar Druck expandiert. Mit dem Gas tritt auch das erwärmte Pulver aus der Pistole aus und schießt mit hoher Geschwindigkeit auf das zu beschichtende Bauteil. Beim Aufprall setzen die Partikel ihre kinetische Energie als Verformungswärme frei und verschweißen. Auf diese Weise lassen sich hochfeste und porenfreie Schichten von mehreren Zentimetern Dicke herstellen.
Das Verfahren wird beispielsweise genutzt, um verschlissene Triebwerksteile wiederherzustellen. Durch die Auswahl geeigneten Pulvers und geeigneter Parameter kann man Schichten gewinnen, die annähernd gleiche Festigkeiten haben wie das Grundmaterial.
2. Physical Vapor Deposition (PVD)
Bei der Dampfabscheidung (englisch: Physical Vapor Deposition, kurz: PVD) wird das Material, mit dem beschichtet werden soll, verdampft. Man unterscheidet folgende Verfahrensvarianten:
Arc-Technologie
Die Energie für den Verdampfungsprozess liefert in diesem Fall ein Lichtbogen. Dieser entsteht, wenn sich hohe Spannungen zwischen zwei Elektroden entladen. Verbindet man die Anode mit einer Metallplatte, so lässt der Lichtbogen die Atome an der Oberfläche der Platte verdampfen. Der metallische Dampf kondensiert auf den zu beschichtenden Werkstücken und bildet dort dünne kristalline Schichten. PVD-Anlagen arbeiten unter Ausschluss von Luft. Da diese den Prozess stören würde. Die Beschichtung erfolgt im Vakuum beziehungsweise in einer Schutzgas-Atmosphäre. Wechselwirkungen mit dem Schutzgas können erwünscht sein: So entsteht beispielsweise durch die Verbindung von verdampften Metallionen mit dem Stickstoff in der Kammer Metallnitrid, das sich als harte Keramikschicht auf den Bauteilen niederschlägt.
Sputter-Technologie
Beim Sputter-Verfahren wird das Material durch Ionenbeschuss in die Dampfphase gebracht. Die Ionen dafür stammen dabei aus einem Plasma, das über der Oberfläche des zu verdampfenden Materials erzeugt wird. Durch Stoßprozesse werden durch die Ionen Atome aus der Oberfläche herausgeschlagen, und so das gewünschte Beschichtungsmaterial quasi atomar zerstäubt. Die herausgeschlagenen Atome kondensieren dann wiederum an den Werkstücken und bilden dort eine dünne Schicht. Wie bei der Arc-Technologie findet der Prozess im Vakuum statt, einzig zum Erzeugen des Plasmas werden geringe Mengen an Gas (z.B. Argon) eingeleitet. Im Gegensatz zum Arc-Verfahren ist die Beschichtungsgeschwindigkeit bei der Sputter-Technologie geringer, der Vorteil liegt in glatteren Schichten.
EB-PVD
Bei der Electron Beam Physical Vapor Deposition (EB-PVD) wird das Beschichtungsmaterial, eine hochschmelzende Zirkonoxid-Keramik, mit einem Elektronenstrahl im Vakuum bei bis zu 3.000 Grad Celsius verdampft. Bei der anschließenden Kondensation auf den Bauteilen entstehen bis zu 300 Mikrometer dicke Schichten. Da Zirkonoxid eine vergleichsweise niedrige Wärmeleitfähigkeit besitzt, wird es als Wärmedämmschicht auf den besonders heißen Hochdruckturbinenschaufeln eingesetzt. Die Besonderheit der EB-PVD-Schichten liegt in ihrer säulenartigen Struktur, welche besonders thermowechselbeständig ist. Dieses Beschichtungsverfahren wird im Ceramic Coating Center in Frankreich durchgeführt. welches ein Joint Venture für Hightech-Beschichtungen zwischen der MTU Aero Engines und der französischen Safran Aero Engines ist.
3. Chemical Vapor Deposition (CVD)
Beim Chemical Vapor Deposition (CVD) wird das Beschichtungsmaterial als Metallhalogenid (Metall = Aluminium oder Chrom) in einer bis zu 1.100 °C heißen Retorte, gasförmig an die Oberflächen der Bauteile (vorwiegend Turbinenschaufeln) herangeführt. Hier zerfällt ein Teil des Beschichtungsgases in seine Ausgangsstoffe und es findet eine Diffusion der Metallatome in die Grundmaterialien statt. Über die Beschichtungsdauer und -temperatur lassen sich die Schichtdicke und deren Zusammensetzung gezielt einstellen. Die Anreicherung der Oberflächen mit Aluminium bzw. Chrom erhöht die Oxidations- bzw. Korrosionsbeständigkeit der Bauteile und damit deren Lebensdauer deutlich.