aviation
EME Aero’s MRO shop sets standards for modern maintenance
EME Aero set up its state-of-the-art MRO shop for Pratt & Whitney GTF™ engines in record time. An efficient flow line with an innovative assembly system is the highlight.
author: Nicole Geffert | 4 mins reading time published on: 09.03.2021
author:
Nicole Geffert
has been working as a freelance journalist covering topics such as research and science, money and taxes, and education and careers since 1999.
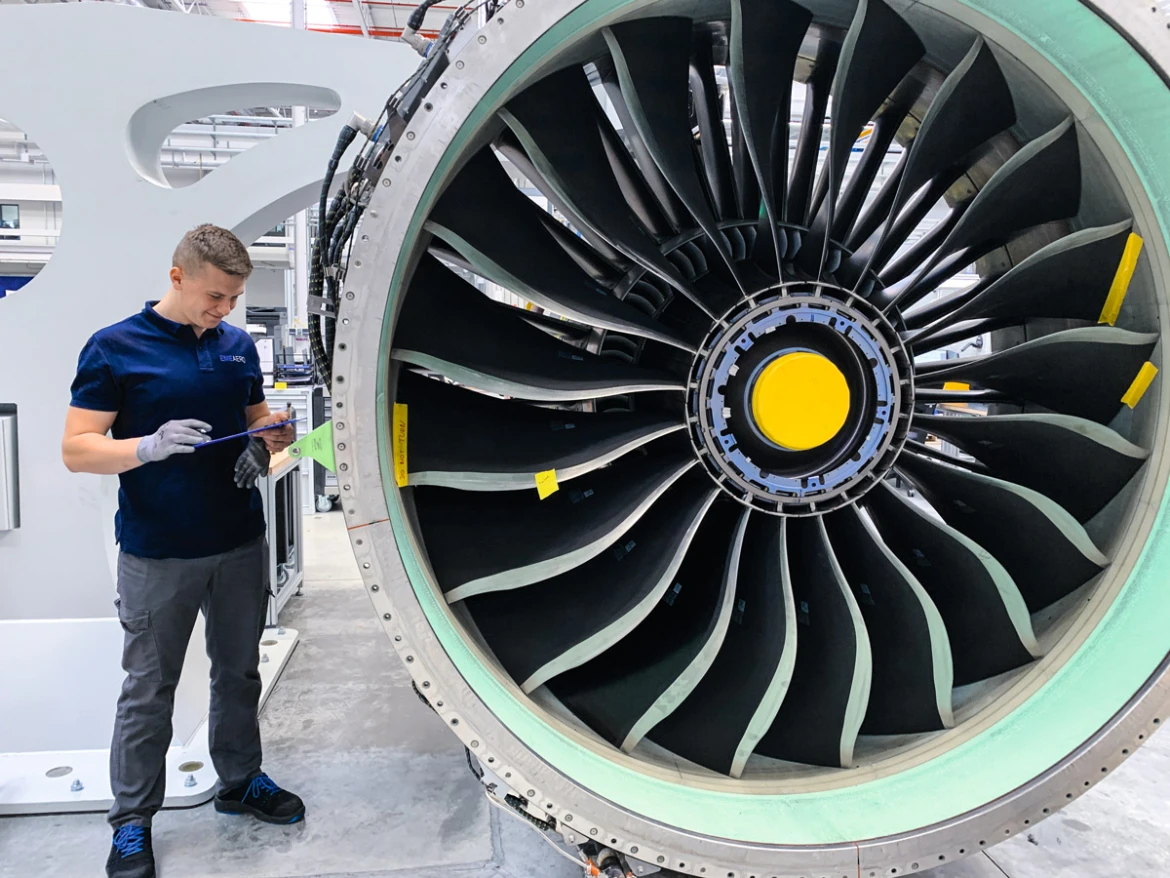
In just 18 months, EME Aero, a joint venture between Lufthansa Technik and MTU Aero Engines, went from a greenfield project to one of the world’s largest and most advanced maintenance shops for Pratt & Whitney (P&W) geared turbofan (GTF™) engines. “Whether we’d manage it was called into question more than once,” says Derrick Siebert, CEO and Managing Director of Business at EME Aero. “It was a tremendous challenge, but we succeeded in our ‘mission impossible’.”
Located in Jasionka, just outside of Rzeszów in Poland, the company started operations in January 2020. “The team got going immediately,” says Robert Maślach, COO and Managing Director of Operations at EME Aero. “At the start, the shop handled engines that were part of P&W’s retrofit program for the low-pressure turbines. Then the first PW1100G-JM production engines began coming in for overhaul.”
Shop highlight: The efficient flow line
To ensure it provides the highest standard of repairs, EME Aero’s shop is state of the art—which is only fitting for the most advanced and efficient engine family on the market today. Setting up a shop from scratch has clear advantages, as it gave the project team a blank canvas to create the ideal layout and ensure the optimum flow of processes. Effective cooperation between MTU and Lufthansa Technik, both aviation specialists, also helped drive things forward. “We incorporated insights and best practices from both joint venture partners so we benefited from the best of both worlds,” Siebert explains.
The shop’s highlight is its flow line for the engines to pass through various disassembly and assembly stations. Engines are fitted to freely moving, floor-based carriers that can be pulled in and out of the production line without disturbing the overall flow. “We’ve installed the latest and greatest technologies currently available in this field,” Siebert says. And wherever the team identified a need and opportunity for improvement, they initiated a new technology development process.
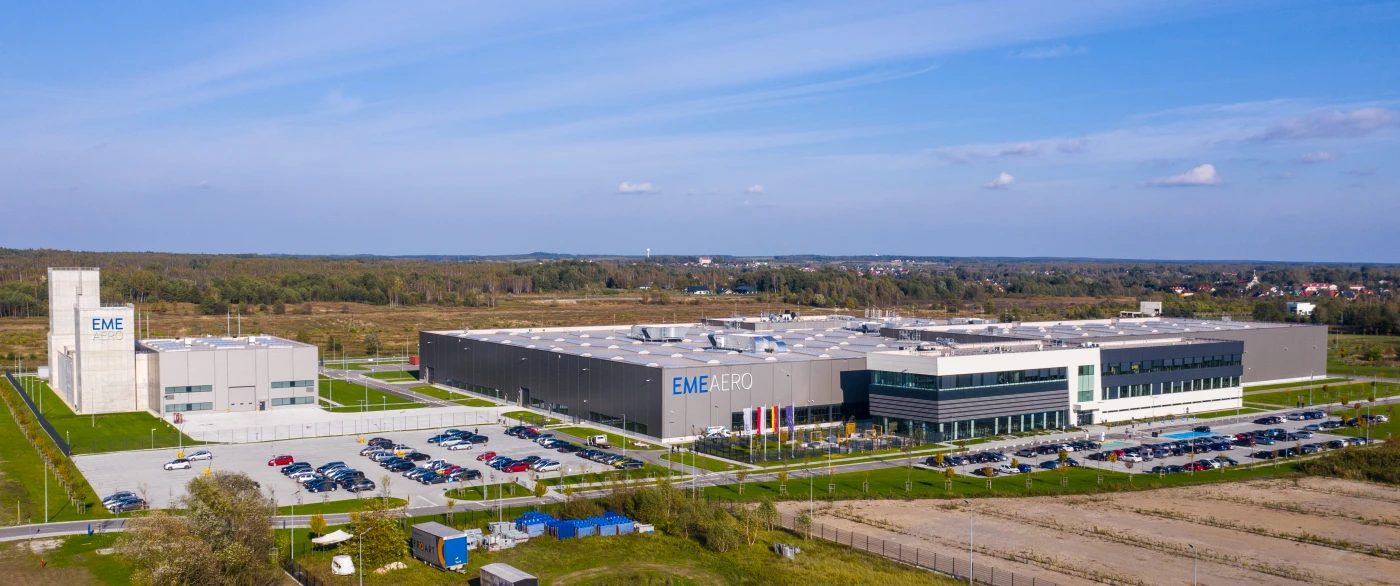
State-of-the-art MRO shop: EME Aero is one of the world’s largest and most advanced maintenance companies for next-generation passenger aircraft engines. The shop is scheduled to reach its full operating capability in 2026, with annual capacity for more than 450 shop visits.
To make the shop as efficient as possible, specialists from MTU’s production and facilities service in Munich worked with the EME Aero team to create a standardized assembly and tooling concept for the various engine types. Its centerpieces are two systems “made by MTU”: the mobile transport and overhaul system (MTOS) is used for complete teardown of engines along the flow line, while partial disassembly is performed in the stationary dock of the fixed overhaul system (FOS). Five FOS have already been installed since the end of 2019, and the MTOS will go into operation in the first half of 2021.
The MTOS is made up of remote-controlled transport facilities that move the engine from one station to the next and hold it in an ergonomic position. What makes the two systems so ingenious is the adapter with which they attach to the engines at a single hoist point. As soon as an engine arrives at the shop, its core is mounted on one of these adapters. Without having to carry out any further setup work, the engine can now be easily disassembled into its individual modules. Since the stationary FOS uses the same adapter as the mobile MTOS, it takes no effort to switch the engines between the two systems.
The world’s quietest test cell
Alongside its high-tech flow line, the shop also boasts a high-tech test cell. “Rather than the usual 50 to 70 hertz, the data transfer system is designed for frequencies of 200 hertz. This allows us to work with a huge volume of data when the overhauled engines undergo acceptance testing,” explains test cell manager Lutz Pfannenstiel. He joined EME Aero from joint venture partner Lufthansa Technik.
In terms of the noise protection it offers, the test cell is also outstanding. “It’s currently the quietest in the world,” says MTU senior consultant Martin Köster, who helped plan and build the test cell. “During an engine test run with take-off (full load) no more than 40 decibels may reach the perimeter of the site where the test cell is located. Noise levels generated by EME Aero’s test stand remain well below this limit, making it the quietest there is.”
The test cell is also characterized by its energy efficiency. Pfannenstiel gives an example: “Shop air from two compressors is used to start the engines on the test stand. We recycle the heat produced in the process for the underfloor heating in the rigging shop.”
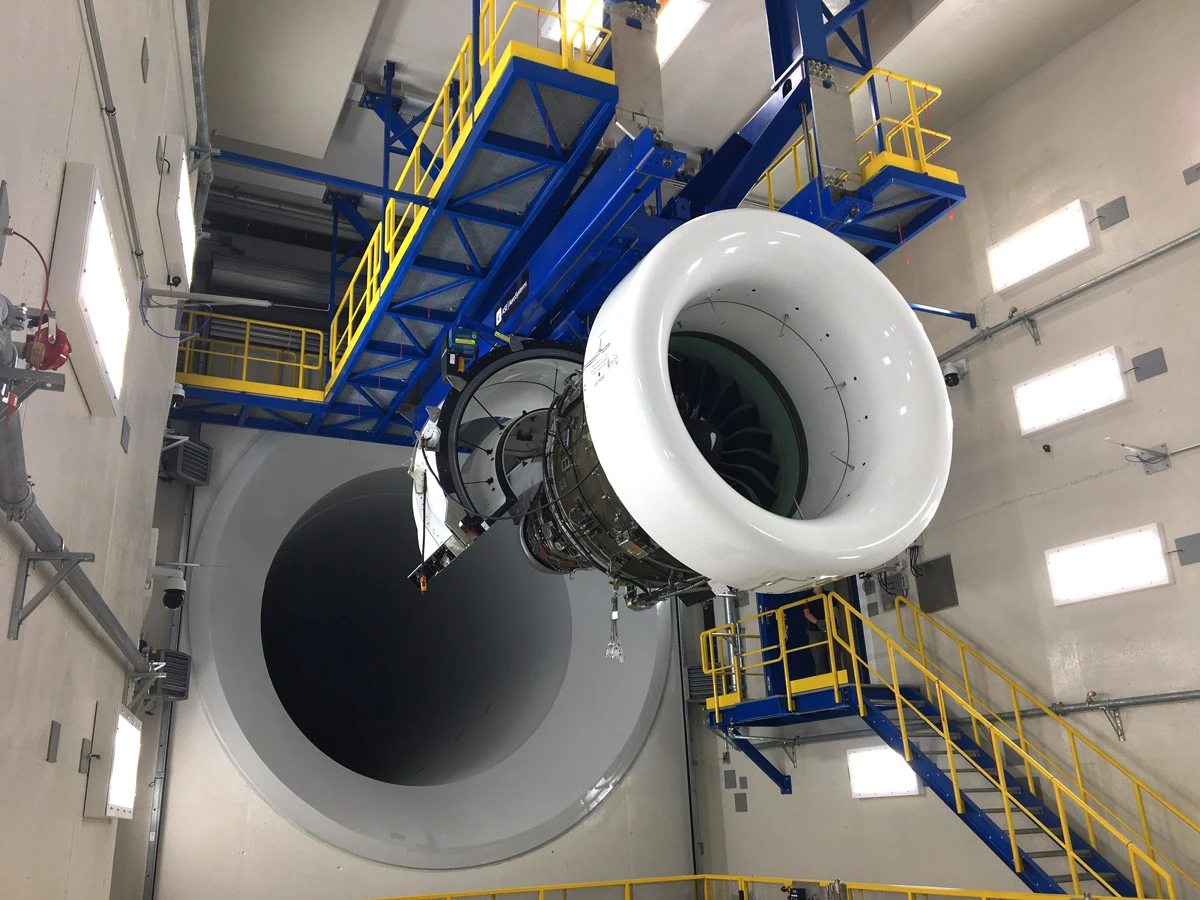
Outstanding test cell: The test cell is currently the quietest in the world and is also remarkably energy efficient.
MRO services for customers worldwide
“We now have around 400 employees maintaining PW1100G-JM engines,” Maślach says. “EME Aero is a partner in P&W’s GTF maintenance network, which provides first-class MRO services to customers all over the world.”
“In 2021, we will continue this growth path until we reach our full capacity of 450 shop visits a year.”
CEO and Managing Director of Business at EME Aero
Within a year of the official start of operations, the team chalked up a huge achievement: “After concluding the project for creating EME Aero, we started—with the help of the MTU shop in Hannover and the Lufthansa Technik shop in Hamburg—one of the steepest ramp-up curves in the history of both joint venture partners. Today, we serve customers around the world,” Siebert explains. “In 2021, we will continue this growth path until we reach our full capacity of 450 shop visits a year.”
The shop is scheduled to reach its full operating capability in 2026, when EME Aero is set to have a workforce of more than 1,000 qualified employees.
“By mid-2021, we’ll have everything in place to maintain, repair and overhaul PW1500G engines,” Maślach says. “We’re optimistic about our future. The strong sense of team spirit we developed from the project and the ramp-up will stay with us. In these challenging times, this will play a key role in helping us prepare for the next ramp-up.”