aviation
On-site service: Mobile teams for urgent engine repairs
MTU has set up shops around the world for urgent repairs. The mobile teams specialize in carrying out repairs on the wing or at the airline to ensure smooth engine operation and can handle even complex challenges: from borescope inspections and top case repairs on high-pressure compressors to the replacement of entire modules.
author: Nicole Geffert | 9 mins reading time published on: 22.05.2024
author:
Nicole Geffert
has been working as a freelance journalist covering topics such as research and science, money and taxes, and education and careers since 1999.
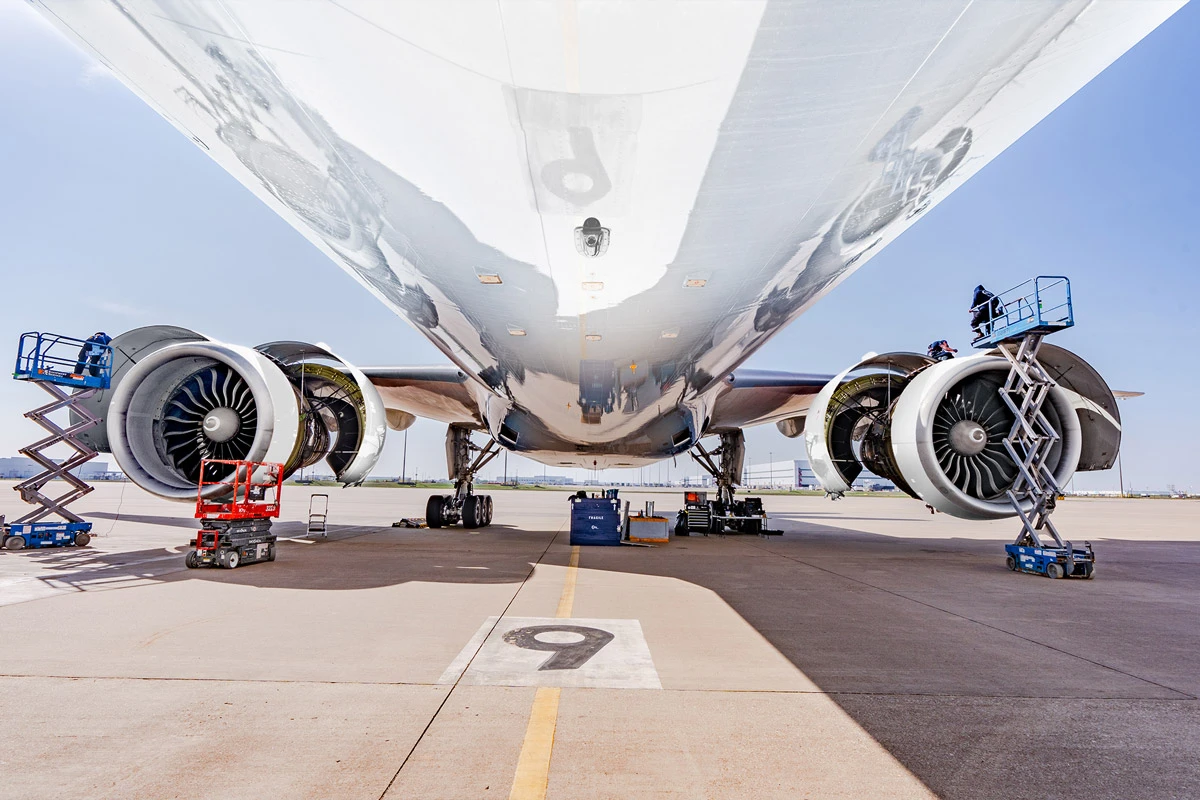
- Michael Schreyögg talks about current trends within the engine maintenance world
- On-site service: Mobile teams for urgent engine repairs
- MTU Maintenance: Training Programs Worldwide
- Technical customer training: trust through transparency and expertise
For two decades, Michael Kautzschmann was at the helm of quality assurance at MTU Maintenance Berlin-Brandenburg in Ludwigsfelde, and he’s still at the forefront of MTU’s Group-wide quality initiatives. “Quality means safety, which is a key consideration in aviation,” he says.
Due to rising cost pressure, airlines are increasingly demanding smaller and more targeted repairs instead of extensive maintenance. And the engine architecture is also increasingly changing so that work can be carried out on the wing. Kautzschmann says: “Instead of sending an engine halfway around the world to be repaired in a shop, they wanted us to repair it locally if possible.”
This on-site service is one of MTU Maintenance’s strengths. At their ON-SITEPlus services (OSS) locations across the globe, mobile MTU teams specialize in carrying out repairs on the wing or at the airline to ensure smooth engine operation.
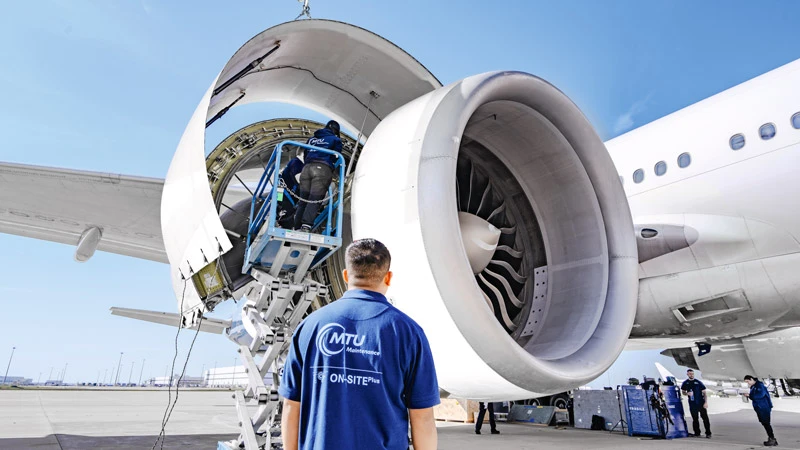
Working on-wing: MTU Maintenance's OSS assignments usually have to be carried out quickly. Like here with the GE90, the world's largest engine, which the experts have made ready for take-off again.
You may also be interested in following content
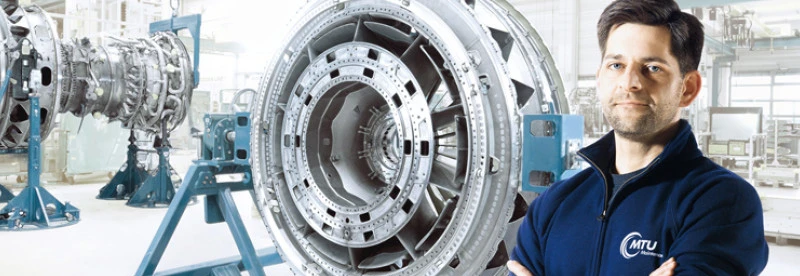
Customized service solutions for aero engines
MTU Maintenance is the global market leader in customized service solutions for aero engines.
As the demand for rapid service increased, MTU expanded its locations in Dallas (U.S.), São Paulo (Brazil), and Perth (Australia) into service centers for aviation, with support from Kautzschmann and teams of MTU experts from Ludwigsfelde. At these new centers, engines such as the CF34, PW800, and CFM56 are now being made ready for use again in hangars with special docks for smaller scopes of work and urgent repairs. For even more customer service, the teams have now extended their capabilities to include complex repair services: from borescope inspections and top case repairs on high-pressure compressors to the replacement of entire modules.
Kautzschmann says: “If an airline calls us, MTU Maintenance is able to send a specialized team anywhere in the world within 24 hours. This happened recently when an OSS team with people from Ludwigsfelde, Hannover, and Dallas got a GE90, the world’s largest engine, ready for takeoff again.”
Quality is a dynamic process. “Customer needs and market trends are changing, and technologies are being further developed. We have to adapt our work to this,” Kautzschmann says. How, exactly? “In our MRO network, we regularly share our expertise, learn from the best in the field, and carefully review our standards—always with the aim of delivering maximum quality and safety worldwide.”
Join us as we travel to four destinations to see MTU’s expert MRO teams demonstrate their engine skills and expertise:
“The fact that we share our knowledge and resources in the MRO network is invaluable. For our customers, this creates confidence in the reliability and safety of MTU products.”
Customer Program Manager at MTU in Perth
Perth, Australia
A Christmas party at over 40 degrees Celsius, barbecue instead of cookies: for Sven Zimmermann, an engine mechanic from MTU Maintenance Berlin-Brandenburg, this was the satisfying conclusion to a successful five-week training course in Perth, Western Australia. The CF34-10E engine expert works for the on-site service team in Ludwigsfelde, and his assignments mainly take him all over Europe.
In November 2023, however, the flight to his deployment site took longer than usual—all the way to the MTU Maintenance Service Centre Australia. This time it wasn’t a customer who rolled out the welcome mat, but the Australian MTU team. On the agenda was a special training session on the CF34’s high-pressure compressor (HPC).
The MTU site in Perth specializes in services for industrial gas turbines from GE Power’s LMTM series. At the beginning of 2023, the site received approval from the Australian Civil Aviation Safety Authority (CASA) to carry out maintenance on the GE CF34-10E engine. This makes it the only on-site provider of engine service in the South Pacific.
“Our customer in Australia had requested an HPC top case repair for its CF34-10E engine,” reports Matiu Cox, Customer Program Manager at MTU in Perth. “The training gave us two benefits: one, we were able to show the airline how well MTU’s OSS network works, and two, we had the opportunity to expand our skills for this engine.”
Top case repair is one of the most extensive procedures that an engine can undergo on-site. To gain access to the high-pressure compressor’s nine-stage rotor, the technicians have to dismantle countless pipes, pumps, and valves. “The repairs are complex,” Cox says. “We’re basically doing open-heart surgery,” Zimmermann adds.
“We may be a smaller site than Ludwigsfelde, but we place just as much emphasis on quality,” Cox says. “The fact that we share our knowledge and resources in the MRO network is invaluable. For our customers, this creates confidence in the reliability and safety of MTU products.”
“The mobile teams in Perth and Dallas carry out a lot of on-wing repairs; these account for half their assignments.”
Certifying Staff at MTU Maintenance Berlin-Brandenburg
Dallas, U.S., and Perth, Australia
Michael Eng is not easily rattled. That’s a good thing, because his job requires a steady hand. For 20 years, the most important tool for this MTU engine specialist in Ludwigsfelde has been the borescope. “I use it to inspect the inside of an engine to check the quality or wear of components,” says Eng, who is a member of MTU’s Certifying Staff and is authorized to approve modules for operation after assembly.
“Borescoping is also in demand for on-site services,” Eng says. During these operations, MTU’s mobile teams repair the engine directly on the wing, if possible, without having to dismantle it. This saves the airline time and money. But borescoping is an acquired skill. Only a trained eye can detect the tiniest of faults, and only experience allows the specialist to assess it correctly. Eng and other MTU experts have therefore developed a training concept for borescope inspections to qualify engine professionals at MTU’s MRO sites worldwide. This required Eng to travel to the MTU Maintenance Service Centre Australia for several weeks, then to MTU Maintenance Dallas in the U.S. He brought with him a training concept he had prepared with these two sites in mind.
“The mobile teams in Perth and Dallas carry out a lot of on-wing repairs; these account for half their assignments,” Eng says. That’s why the program included intensive training for borescoping the CF34-8, CF34-10, and CFM56-7 engines. “Carefully borescoping a CFM56-7 takes around ten hours,” the MTU expert says. “It’s crucial for the measurement results and the damage assessment to be reliable.”
In addition to highly trained personnel, it’s also vital to have the right tools. Naturally, MTU’s Perth and Dallas sites have state-of-the-art borescope equipment. “The exciting thing about training sessions like this is that I get to learn from the experiences of others as well,” Eng says. “Everyone benefits from the in-depth exchange.”
“This solution was only possible thanks to the flexibility of the MTU team in working with GOL, and it allowed a reduction in turnaround time and logistics costs compared to the option of sending these engines to a shop outside Brazil.”
GM Aerotech MRO and Executive Director of Maintenance and SCM
São Paulo, Brazil
Gol Airlines is a long-standing MTU customer. MTU was one of the selected MROs to support a GOL project to perform quick-turn replacement of high-pressure turbine blades on some of its CFM56 engines.
Kay Annemüller, an engine specialist and Certified Engineer from MTU’s on-site service in Ludwigsfelde, was sent out along with two engine mechanics. Their destination was Belo Horizonte in the southeast of Brazil, where Gol’s MRO Aerotech I is based. A team from MTU Maintenance do Brasil was already waiting there to carry out the blade replacement together with the Ludwigsfelde experts.
For the MTU expert team from São Paulo, the job also served as on-the-job training to learn how to carry out these demanding repairs themselves in the future. The MTU site in São Paulo is an on-site service center for aircraft engines and industrial gas turbines. The team is certified for borescope and end-of-lease inspections and for top-case repairs on the high-pressure compressor. It also carries out fan blade and gearbox replacement, and repair and replacement of parts on different engine modules, including high-pressure turbine blades.
“The high-pressure turbine is the most highly stressed module in the engine, subject to extremely high pressures and temperatures,” Annemüller says. The disassembly depth is particularly tricky, and the experience of an expert is essential here. Annemüller has been working at MTU in Ludwigsfelde for 14 years; he is more than happy to share his knowledge with the MRO expert network.
Both the repairs and the training were a success, as the customer also notes: "MTU Maintenance do Brasil's certification to perform HPT blade replacements at GOL Aerotech MRO's engine shop was critical to meeting GOL's needs. This solution was only possible thanks to the flexibility of the MTU team in working with GOL, and it allowed a reduction in turnaround time and logistics costs compared to the option of sending these engines to a shop outside Brazil," says Fernando Miwa, GM Aerotech MRO and Executive Director of Maintenance and SCM.
The team in Brazil is ready for the challenges ahead. Thomas Heinhold, Head of MTU Maintenance do Brasil, says: “Not only do we have the expertise, but we also have the necessary approvals from the aviation authorities in Brazil, Europe, and the U.S. This means we don’t have to send the engines across the Atlantic, but can reliably repair them on-site.”
“We have more than 18 years’ experience maintaining the CFM56-7B, and we share this expertise within the MRO network.”
COO and Director of Technical Operations at MTU Maintenance Zhuhai
Zhuhai, China
In 2023, engine mechanics Liang Yongtong and Wei Li from MTU Maintenance Zhuhai traveled to Berlin. They are both specialists in the maintenance of CFM56-7B engines, and their knowledge is in demand from the expert teams at MTU Maintenance Berlin-Brandenburg. The CFM56-7B is no stranger to Zhuhai, but it’s still a new sight in the Ludwigsfelde shop.
“We have more than 18 years’ experience maintaining the CFM56-7B, and we share this expertise within the MRO network,” says Christian Ludwig, COO and Director of Technical Operations at MTU Maintenance in Zhuhai. In Ludwigsfelde, Liang and Wei demonstrated the workflows and special tools used in assembly and disassembly at the Chinese site. The pair worked side by side with the teams in Ludwigsfelde for two months.
Zhuhai maintains not only the CFM56-5/-7 but also the LEAP-1A and -1B, the PW1100G-JM, and the V2500, with a large in-house repair portfolio. The location has more than 90 customers and its teams can carry out up to 450 shop visits a year. A state-of-the-art training center and a second test cell were opened there just recently to support the growth strategy of MTU Maintenance Zhuhai.
When Zhuhai was still a young MTU location, MTU Maintenance Hannover trained the Chinese teams on-site. “We’ve since built on that to develop our own training system, based on our experience in production and our culture,” says Li Hao, who heads the training center in Zhuhai.
Amsterdam-based MTU Maintenance Lease Services, a specialist in leasing and asset management, recently benefited from this training as well. The leasing teams are very well versed in engine maintenance, which makes them unique in the industry. Training courses, such as the one for the V2500-A5 engine, are key to their success. “Before the training, we got a clear picture of what the leasing experts wanted to know,” Li says. After all, there’s no such thing as off-the-rack training: just like MTU’s MRO services, the training courses in the MRO network are also tailor-made.