aviation
MTU Maintenance: On-site service for particularly urgent repairs
MTU’s on-site services ensure engine operations remain smooth. MTU’s site in Ludwigsfelde now has a new hangar and a specialized team for smaller, extremely urgent jobs.
author: Nicole Geffert | 6 mins reading time published on: 06.04.2022
author:
Nicole Geffert
has been working as a freelance journalist covering topics such as research and science, money and taxes, and education and careers since 1999.
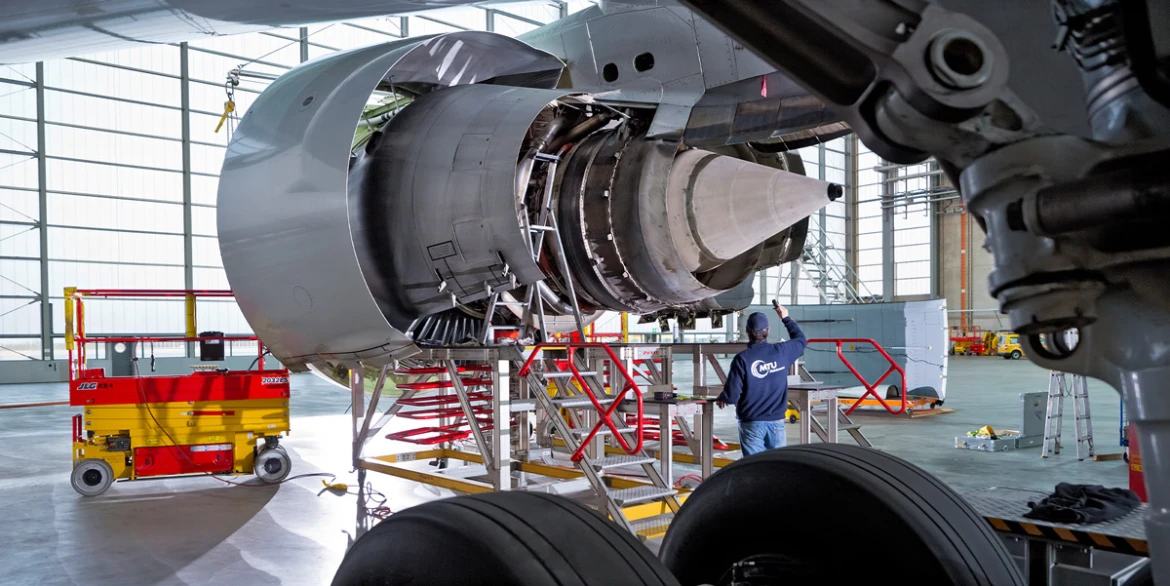
Some jobs never become routine—and nobody knows this better than the mobile teams for MTU Maintenance’s on-site service (OSS). The time pressure alone is enough to turn every assignment into a challenge: there was no time to lose, for example, when one MTU customer’s aircraft had to make an unscheduled stop after an engine bird strike meant it was unable to continue flying. For the operator, such an aircraft on ground (AOG) situation can be critical and expensive.
“After consulting with the customer, we simply went ahead and chartered an aircraft to get our team, along with special tools and spare parts, to the engine as quickly as possible.”
Director 0n-site services at MTU
MTU Maintenance’s OSS team responded quickly and flexibly to keep the aircraft’s time on the ground as short as possible. However, due to the coronavirus pandemic, there was no regular flight to the airport where the plane with the defective engine was stranded. “After consulting with the customer, we simply went ahead and chartered an aircraft to get our team, along with special tools and spare parts, to the engine as quickly as possible,” says Arne Straatmann, Director On-Site Services at MTU.
Once the team had repaired the damage, the aircraft was able to take off again and the customer could breathe a sigh of relief. To ensure that MTU customers around the world can call on this service without delay, MTU has set up highly qualified on-site service teams at locations in Brazil, Canada, the U.S., Germany and China. An around-the-clock on-call service ensures that the teams are ready to roll as soon as a customer reports engine damage that calls for repairs. MTU’s customer service organizes the deployments, including all technical, logistical and customs handling.
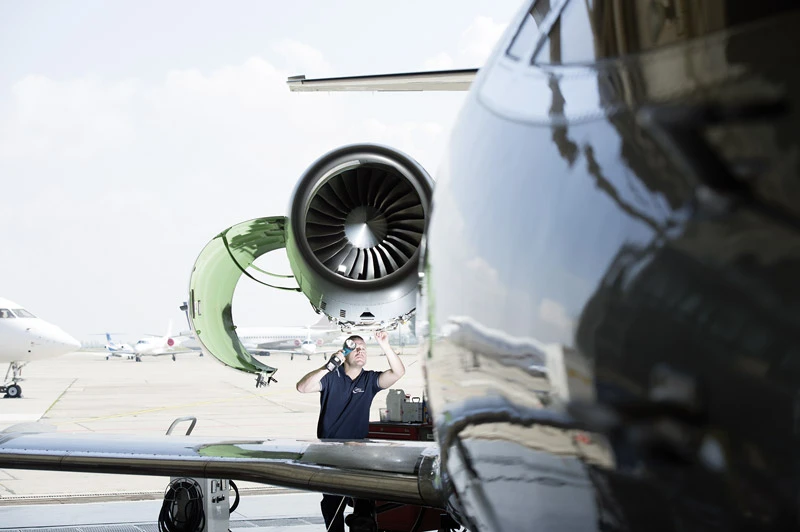
On-wing inspection: Whenever possible, MTU Maintenance’s OSS teams perform repairs on-wing.
“We serve customers on their first inquiry, even if they don’t yet have a contract with MTU Maintenance—and we respond to every call by getting a specialized team to the site quickly and reliably,” Straatmann says. The on-site service portfolio includes borescope inspections, minor repairs such as boroblending on high-pressure compressors, as well as top case repairs or even the replacement of entire modules.
If an upgrade is required, MTU will take care of all additional services within its network of worldwide MRO shops. Engine needs replacing? No problem: MTU Maintenance Lease Services B.V. in Amsterdam can have one ready on short notice, and the same goes for comprehensive materials solutions.
Preventive maintenance
Not every on-site deployment is an AOG. The OSS team also performs planned engine maintenance at airports, customer locations or in the shop. “Our aim with planned repairs is to make shop visits as cost-effective as possible for the customer,” Straatmann says. “For example, whenever our specialists replace a component or carry out important modifications, the customer is benefiting from preventive maintenance since more serious damage, not to mention more extensive shop visits, are avoided as a result.”
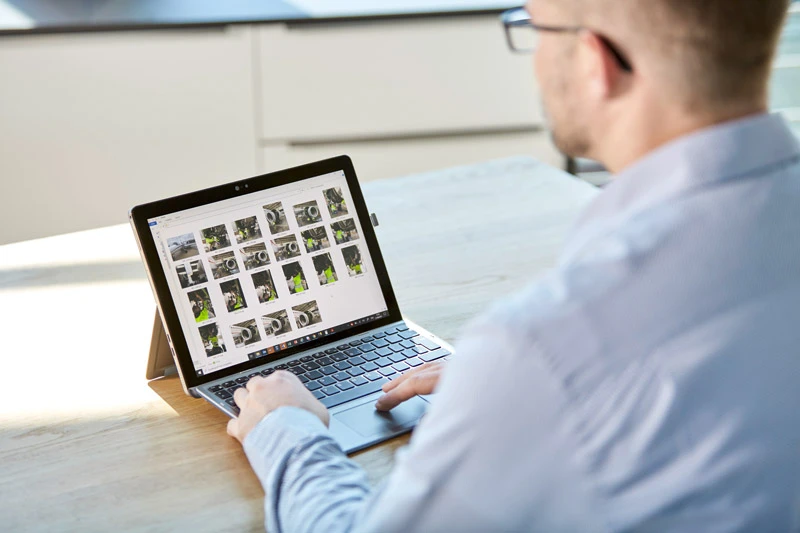
Predictive maintenance: Intelligent tools like engine trend monitoring enable better maintenance planning.
Engine trend monitoring also comes into play here, enabling predictive maintenance planning and condition-based engine maintenance. Moreover, MTU Maintenance has developed CORTEX, a tool for reducing its customers’ operating and maintenance costs. Unlike any other tool on the market, CORTEX can automatically generate the optimum maintenance strategies for customers’ fleets in real time. “It’s a way for us to help keep our customers competitive,” Straatmann says.
Whenever possible, MTU Maintenance’s OSS teams perform repairs on-wing—a form of on-site service in which the engine is repaired without first having to be removed from the aircraft wing. Since this saves time, it is particularly attractive for customers. However, some repairs can’t be done this way—for example a top case repair, where the top half of the high-pressure compressor housing is removed to allow the compressor’s blades or vanes to be replaced. For these kinds of repairs, the engine is removed from the wing, repaired, and then reattached.
New hangar, independent team
“Our primary aim,” Straatmann says, “is to ensure smooth engine operation for our customers by implementing the best solution either on-site or in one of MTU’s worldwide shops.” For example, at MTU Maintenance Berlin-Brandenburg, where a new 1,200 square meters hangar went into operation at the end of 2021. Five special engine docks for smaller or particularly urgent jobs, known as quick-turn docks, and a highly qualified team are on hand to get CF34-8/-10, PW800, CFM56-7 and soon also CFM56-5 engines back in working order as quickly as possible. The spectrum of jobs ranges from minor repairs to work on the hot section of an engine.
“What we do here doesn’t take the place of major shop visits; our on-site service team specializes in minor repairs between the more extensive shop visits,” says Jan Bierkamp, who heads OSS Europe at MTU. “Here in our shop, we also follow the maxim that says we want to reduce downtime as well as overall costs for our customers and extend the service life of their engines.” MTU Maintenance Berlin-Brandenburg is being expanded to become the central point from which MTU provides on-site services for Europe.
The MTU location already has many years of on-site service experience and expertise: each year, its experts perform hundreds of jobs in the shop and on-site for the CF34, the PW200, PW300, PW500 and PT6 as well as the LM series industrial gas turbines. These services are now being expanded further, as is the portfolio. “We’ve strengthened the already independent team and expanded it with additional competencies. It will focus exclusively on on-site service in the future,” Bierkamp says. In addition, there are Customer Support and Engineering teams, who also work in the new hangar to ensure that the customer receive the best possible support around the clock. This ensures the availability of the customer’s fleet.
This expansion comes at just the right time: demand for on-site service is on the rise. “Customers, airlines and lessors are all feeling increasing cost pressure, which has only intensified during the pandemic,” Bierkamp says. As a result, demand is growing for smaller, more specific work scopes that can keep fleet operations cost-efficient.
It’s good to know that not only the engine but also the aircraft is in the hands of experienced maintenance specialists. That’s why MTU relies on collaborations with selected, competent partners. Starting this year, for instance, MTU Maintenance has been working more closely together with the Nayak Group, which specializes in line and base maintenance.
“MTU Maintenance can now offer its customers not only comprehensive MRO solutions for engines but also line and base maintenance services on aircraft. In return, the Nayak Group will be able to expand the range of services it offers its customers in collaboration with MTU Maintenance to include engine MRO.”
Director on-site services at MTU
For Straatmann, the advantages of this partnership are obvious: “MTU Maintenance can now offer its customers not only comprehensive MRO solutions for engines but also line and base maintenance services on aircraft. In return, the Nayak Group will be able to expand the range of services it offers its customers in collaboration with MTU Maintenance to include engine MRO.” Customers benefit from these partnerships, since it means their engines are up and running again more quickly and the aircraft is back in the air. Mission accomplished!