aviation
F117 engine: MTU technology powers Boeing C-17
The Boeing C-17 Globemaster III is a real eye-catcher on the big screen and on little ones—and MTU has a share of more than 20 percent in its propulsion system.
author: Eleonore Fähling | 4 mins reading time published on: 15.04.2025
author:
Eleonore Fähling
has been on the AEROREPORT editorial team since 2014 and in charge of the MTU employee magazine since 1999. As an aerospace journalist, she specializes in aviation history and market topics.
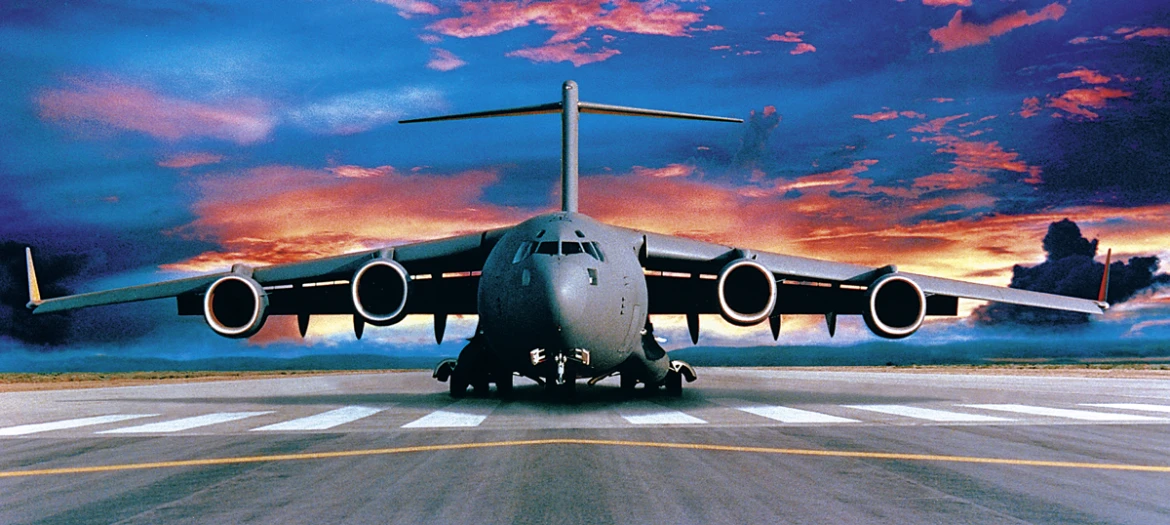
C-17: 30 years of service
The C-17 made its maiden flight in September 1991 at its manufacturer McDonnell Douglas in Long Beach, California; McDonnell Douglas has been part of Boeing since 1997. The first C-17 off the production line was delivered to Charleston Air Force Base in South Carolina in 1993. The U.S. Air Force’s first C-17 unit, the 17th Airlift Squadron, began flying on January 17, 1995. By 2015, 279 C-17s had been built, almost all of which are still in service today with a total of nine operators.
It was an exciting 12 days that the United Arab Emirates Air Force spent in spring 2018 supporting the filming of the action thriller “Mission Impossible: Fallout.” It supplied the film crew with two aircraft: a DHC 6 Twin Otter plus the aircraft that appears later in the film, a Boeing C-17 Globemaster III. This resulted in footage of nothing less than one of the most spectacular stunts in movie history: a HALO jump from a height of more than 7,500 meters. HALO stands for “high altitude – low opening” and refers to a parachute jump from a high altitude in which the parachute is opened only a few hundred meters above the ground so as not to be detected by enemy air defenses.
The film’s lead, Tom Cruise, performed this and other stunts himself. He had to do a total of 94 jumps before the scene was finally in the can. Cruise’s training jumps were from the Twin Otter, but the sequences shown in the film take place in and with the C-17. Theater audiences and critics alike appreciated the effort—and aviation enthusiasts were delighted by the spectacular twilight shots of the scene’s secret star, the iconic C-17 shoulder-wing aircraft with its wingspan of more than 50 meters.
Powerhouse gets big things done
Even 30 years after its entry into service, the C-17 still causes a stir wherever it flies or lands—and its characteristic shape always attracts attention. It can transport up to 102 paratroopers and their equipment, but its gigantic cargo hold can also accommodate entire fleets of trucks or, in an emergency, more than 800 passengers, as was the case during the evacuation of Kabul in August 2021.
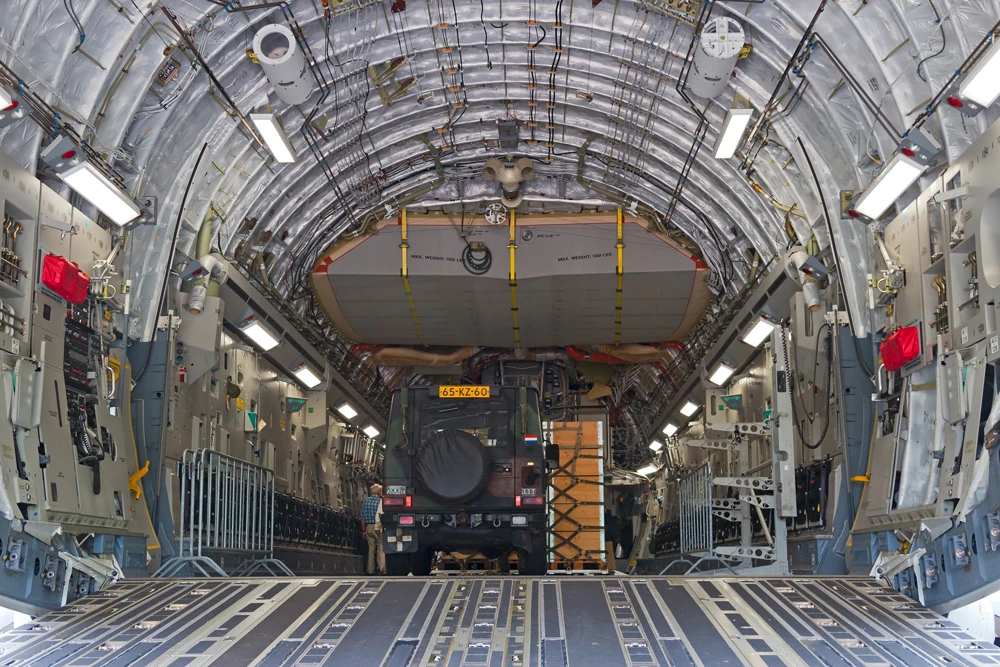
The C-17 can carry a cargo of wheeled U.S. Army vehicles in two side-by-side rows, including the U.S. Army's main battle tank, the M-1.
Four F117-PW-100 engines, each generating 40,000 pounds of thrust, carry the aircraft and its cargo into the air. With a payload of almost 75 metric tons, it can take off from a runway just 2,360 meters long, fly 4,445 kilometers, and land on an airfield just 900 meters long. Empty, it can even fly distances of up to 6,230 nautical miles, or around 11,500 kilometers. The F117-PW-100 is the military version of the PW2000, which powers the Boeing 757 medium-haul aircraft. When the F117 was selected as the exclusive engine for the C-17 in 1991, the commercial variant had already been in production for ten years. The military version completed its first run on December 4, 1981. And MTU has been on board since the beginning, with a program share of 21.2 percent.
Cooling ensures greater engine efficiency
This program share essentially comprises the low-pressure turbine, and that’s no coincidence: back in the early 1970s, MTU was already actively looking for commercial applications for its engine expertise, which it had demonstrated with its RB199 engine for fighter jets. The then world market leader, Pratt & Whitney, was looking to equip its successful JT8D engine with a new exhaust casing, and MTU seized the opportunity. It won over the customer and shortly afterward was awarded the contract to develop the low-pressure turbine for the thrust-enhanced JT10D successor program, later renamed PW2000. This move into producing components for commercial aircraft engines also marked MTU’s entry into development and thus into partnership and program responsibility.
The low-pressure turbine’s standout technical feature was active gap control, featured for the first time here: the turbine case is cooled, which compensates for the differences in thermal expansion of the components and thus increases the efficiency of the module. This approach is now standard in engine construction. While the idea came from Pratt & Whitney, MTU was responsible for its implementation.
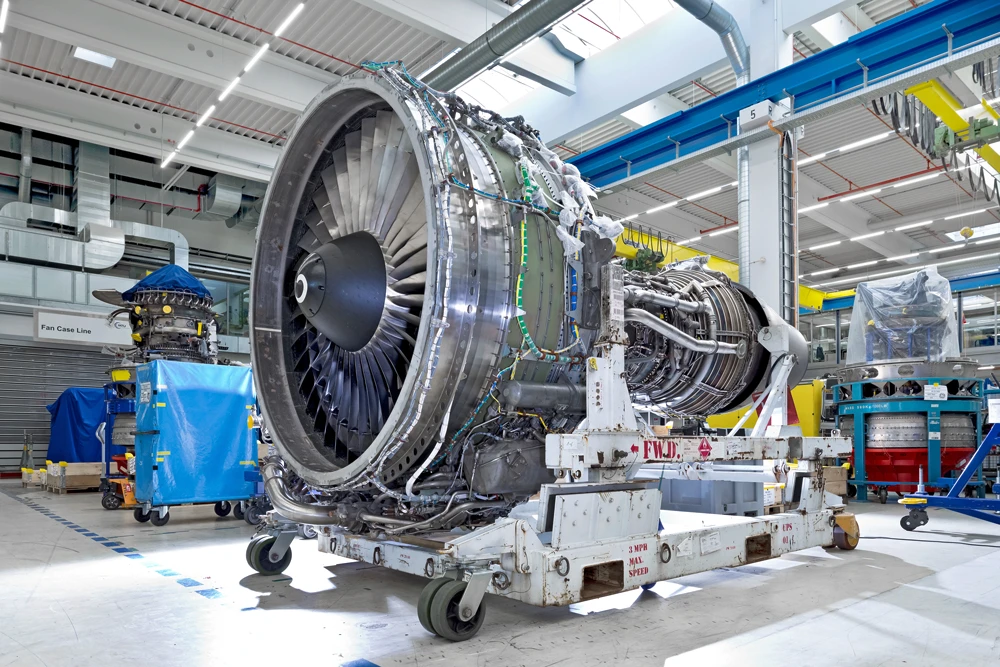
MTU has been working in cooperation with Pratt & Whitney on developing and manufacturing the PW2000 engine family since 1979. MTU’s program share of 21.2 percent in the construction of this successful engine comprises the development of the low-pressure turbine and the turbine exit case as well as the production of the most important parts of the low-pressure turbine and other high-quality components.
A career with no end in sight
The Boeing 757 was built from 1981 to 2004, and the McDonnell Douglas/Boeing C-17 Globemaster III was produced from 1991 to 2015. One prominent Boeing 757 passenger is the Vice President of the United States; “Air Force Two” is usually a Boeing C-32, which is a 757 variant. At the end of 2024, more than 500 757s were still in active service. There’s no end in sight for the C-17 Globemaster III either—especially not for its “second career.” The aircraft’s most recent screen successes have come on social media. It seems it’s never too late to set out on a successful career as an influencer.
Boeing 757 and PW2000: Duo for the medium haul
In the late 1970s, Boeing began developing a new twin-engine long-haul aircraft with an intercontinental range. The 757 was designed to serve medium transcontinental routes more economically. It made its maiden flight in 1982, and was also offered with PW2000 engines as of 1984. By 2004, 1,050 757s had been built. Their successors are the larger versions of the Boeing 737 and Airbus A320 narrowbody families. The aviation authorities in the U.S. and Europe recently granted certification to the Airbus A321XLR, which has a range of 8,700 kilometers, similar to that of the Boeing 757. This aircraft is powered by the PW1100G-JM, an enhancement of the PW2000.
PW2000 in a new guise
Instead of a tube with wings, aircraft could soon have a blended wing body that functions as an airfoil. Read more
Start-up JetZero is the company that is currently furthest along in the design phase for such a project; it is aiming to cut fuel consumption by 50 percent. Test flights are scheduled to begin in 2027 powered by a PW2000 variant, the PW2040.