good-to-know
A brief guide: High-pressure compressor
High-pressure compressor design is the supreme discipline in engine construction. AEROREPORT explains what HPCs do and highlights the innovative technologies that lie behind them.
author: Isabel Henrich | 3 mins reading time published on: 11.09.2023
author:
Isabel Henrich
studied political science and communications. At MTU, she coordinates the editorial process of AEROREPORT and is responsible for the conception and development of its content.
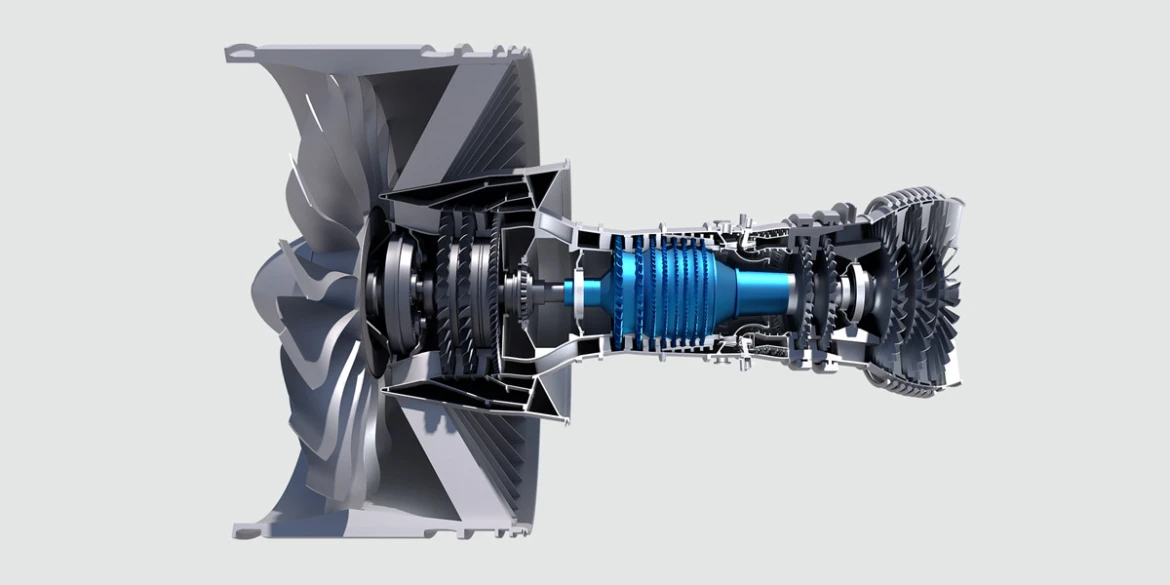
Compressors are the centerpiece of an engine. MTU Aero Engines has been developing, manufacturing and repairing high-pressure compressors (HPCs) for over 50 years. HPC design is the supreme discipline in engine construction. Those who master it are right at the top of the engine league.
What do high-pressure compressors do?
The portion of air ingested by the fan that flows into the core engine is further compressed in the low- and high-pressure compressors. The low-pressure compressor is responsible for precompression, while the high-pressure compressor handles main compression. MTU’s high-pressure compressors feature extremely high efficiencies combined with low weight.
Compressor development at MTU
MTU initially acquired its compressor expertise in the military sector: it supplies the intermediate-pressure and high-pressure compressors for the Tornado’s RB199 engine, the low-pressure and high-pressure compressors for the Eurofighter’s EJ200 engine, and the intermediate-pressure compressor for the TP400-D6 in the Airbus A400M military transporter.
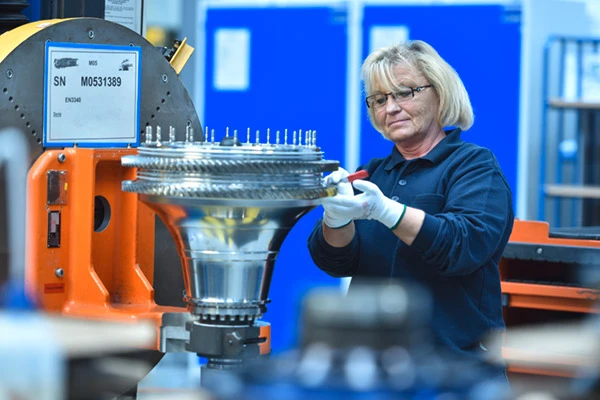
For the EJ200, MTU for the first time designed compressor stages in blisk design which are now also being used very successfully in MTU components for commercial engines.
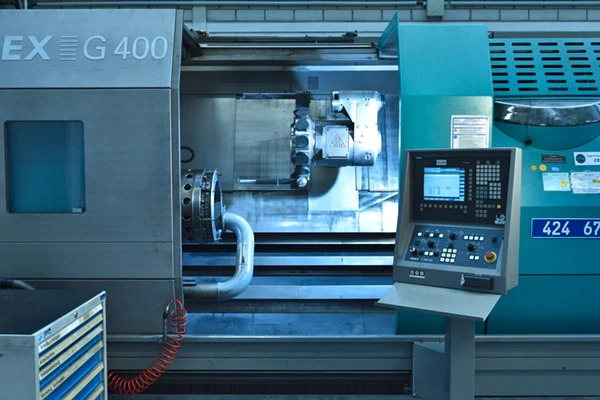
For the first time, MTU contributed components developed and built under its own responsibility to the RB199, such as the intermediate- and high-pressure compressor and the intermediate-pressure turbine.
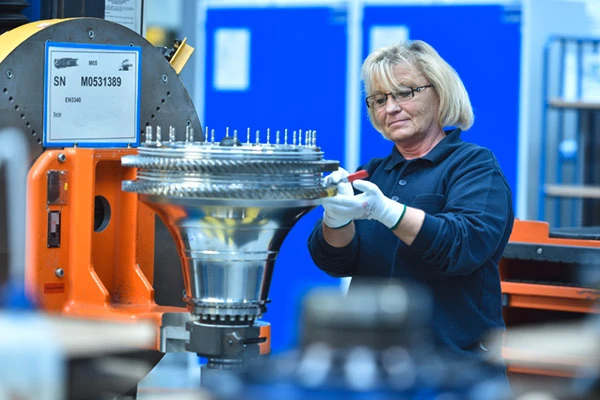
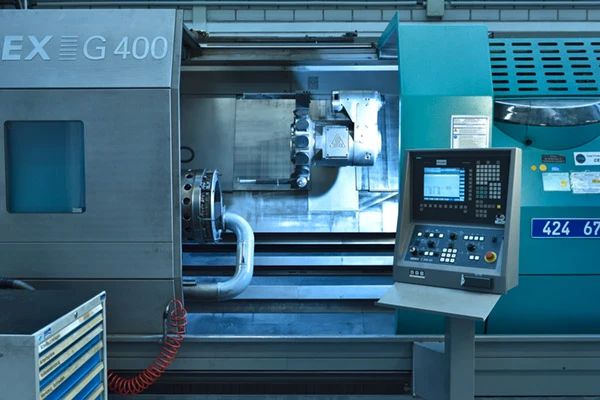
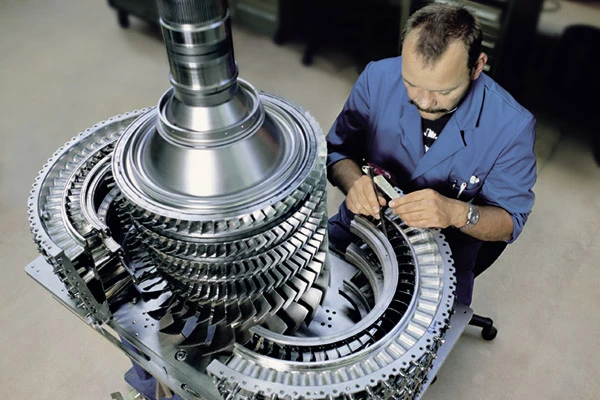
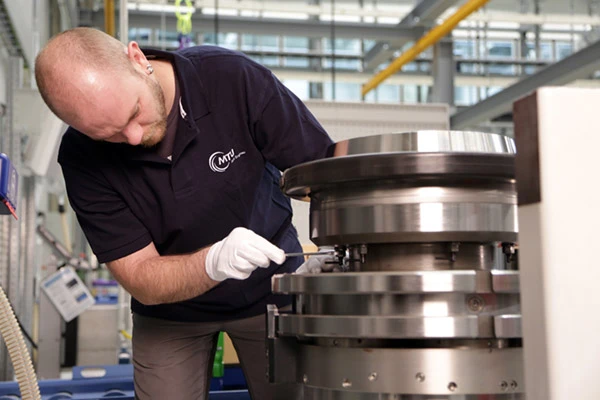
MTU developed its first commercial HPCs for the PW6000, the engine for the A318. The current flagship is the HPC for the eco-efficient GTF™ engine, which MTU developed jointly with Pratt & Whitney. And the success story continues: the latest GTF variant—the GTF Advantage™—will feature an HPC that has been enhanced yet again.
MTU’s involvement in the new European fighter jet, the Next Generation Fighter (NGF), also sees the company continue its tradition of military compressors: for this jet engine, MTU is developing and manufacturing the entire compression system consisting of low-pressure compressor, inter-compressor duct and HPC.
What’s special about the high-pressure compressor in the geared turbofan?
The GTF’s eight-stage transonic HPC has a pressure ratio of 15:1 and has been optimized using state-of-the-art design methods. It is characterized by extremely robust operating behavior with outstanding efficiency. The forward four stages come from MTU and the rear four from Pratt & Whitney.
The GTF HPC is built on the blisk principle—and for the first time this includes the rear stages. To this end, MTU manufactures nickel blisks on behalf of Pratt & Whitney using the precision electrochemical machining (PECM) process. Other HPC highlights include new construction methods, such as casing treatment, a new rotor tie shaft design concept, the axially undivided inner ring, new materials, and the novel ERCoatnt® erosion protection layer, which is an innovative multilayer coating for airfoils. Two brush seals are also installed in the GTF compressor area. These innovative MTU seals replace conventional labyrinth seals and significantly reduce any remaining leakage flow.
What optimizations are planned for the GTF Advantage™?
The latest GTF, the GTF Advantage™, uses an HPC that has been further enhanced—and features even greater efficiency. One focus for the enhancement work was on increased robustness and reliability in operation.
What innovative technologies can be found in next-generation high-pressure compressors?
The next generation of high-pressure compressors is already being prepared—supported by sophisticated and ever more refined simulation, calculation and design methods in all analytical disciplines as well as rig and demonstrator tests.
The goal is to achieve a more compact, more lightweight design without sacrificing efficiency. Additional possibilities result from improved interaction between the HPC and the low-pressure compressor in front of it, and the optimized design of the inter-compressor duct. At the component level, additive manufacturing combined with novel bionic design processes enables the optimization of component geometry.
For the engine for the Next Generation Fighter, MTU is developing the entire compression system consisting of low-pressure compressor, inter-compressor duct and high-pressure compressor. The variable cycle engine (VCE) design poses special challenges for MTU, as the compressors have to be particularly flexible in terms of their scope of operations. New materials and construction methods are being considered to reduce weight, such as fiber-reinforced composites (FRCs) and powder metal (PM).