good-to-know
A brief guide: Low-pressure turbine
MTU’s low-pressure turbines are world-class. AEROREPORT explains what they do and the innovative technologies they feature.
author: Isabel Henrich | 4 mins reading time published on: 08.08.2023
author:
Isabel Henrich
studied political science and communications. At MTU, she coordinates the editorial process of AEROREPORT and is responsible for the conception and development of its content.
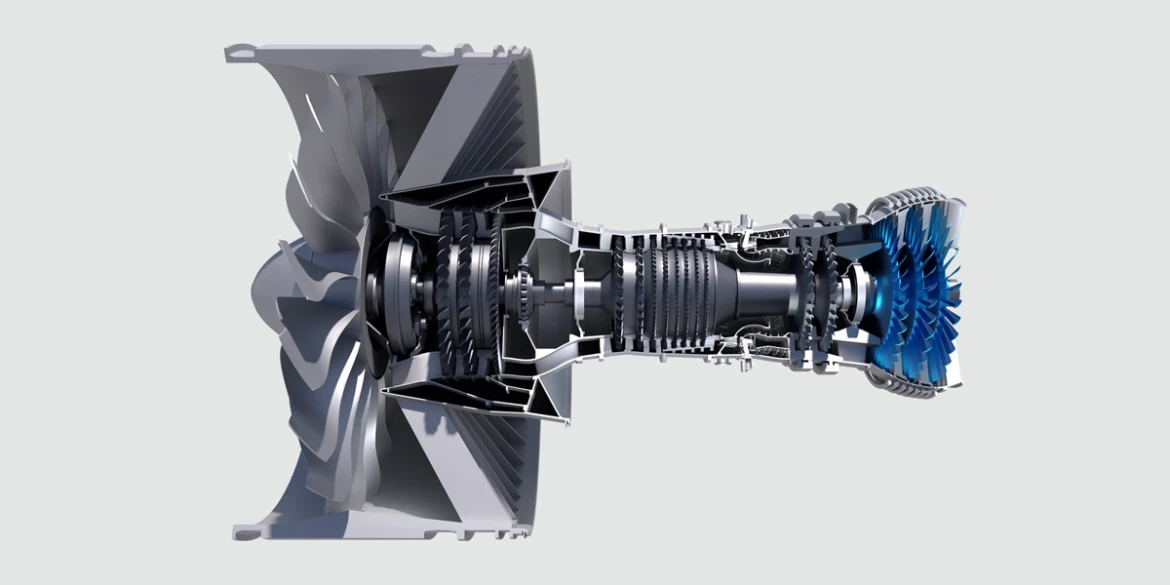
MTU Aero Engines is the world’s technology leader when it comes to low-pressure turbines (LPTs) that operate at maximum efficiency and minimum weight. The breadth of its expertise ranges from conventional models for business jet engines and power turbines for heavy-lift transport helicopter engines all the way to large conventional low-pressure turbines for turbofan engines powering medium- and long-haul airliners. MTU’s masterpiece is the high-speed low-pressure turbine, a key component of the GTF™ engine— technology unparalleled in the world.
What does the low-pressure turbine do?
The air compressed by the compressors flows into the combustor. There, the delivered fuel is burned and the resulting hot combustion gases escape at high energy. These race through the high- and low-pressure turbines, each of which has several turbine stages and numerous blades, which are rotated by the combustion gases. A shaft connecting the LPT to the low-pressure compressor (LPC) and the fan drives the LPC and the fan. The fan generates most of a turbofan’s thrust by way of the sheath flow.
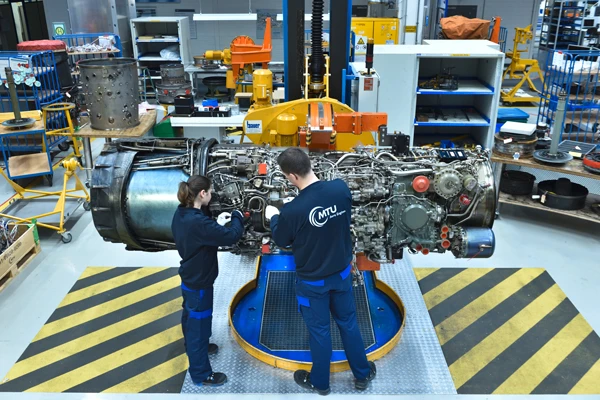
RB199: For the first time, MTU contributed components developed and built under its own responsibility to this engine.
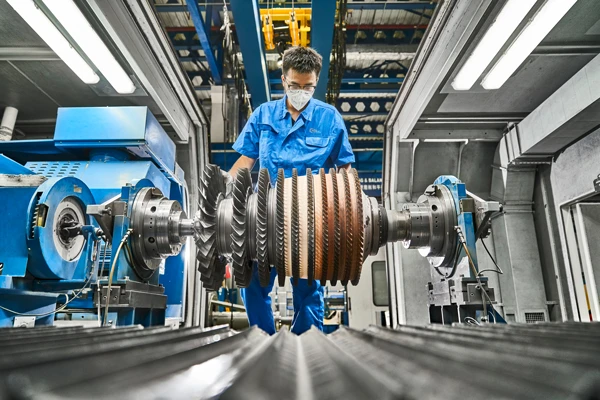
V2500: MTU holds a 16% stake in the IAE V2500 and is responsible for the complete low-pressure turbine and numerous add-on parts.
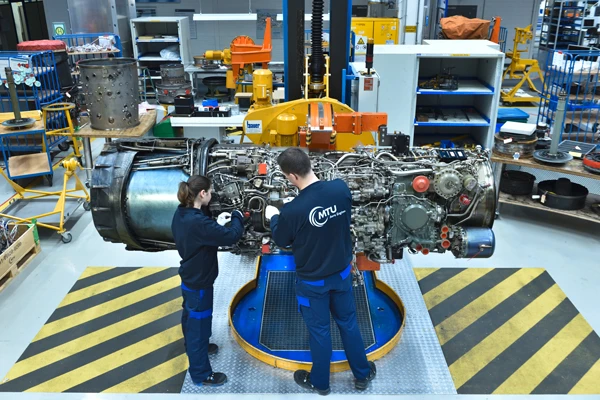
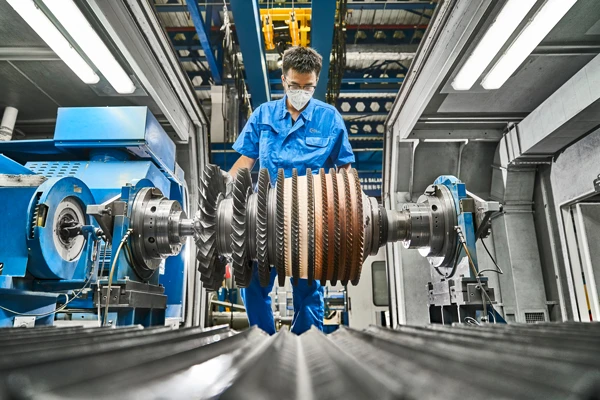
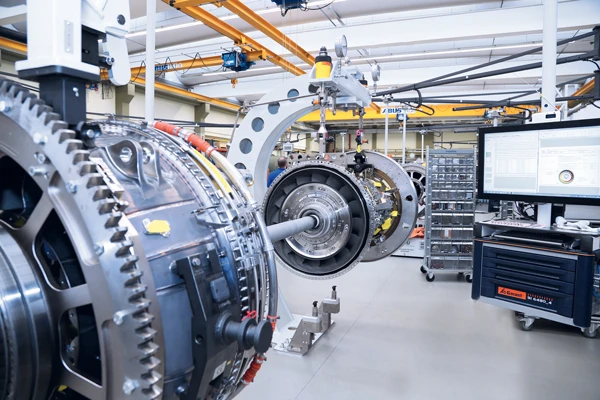
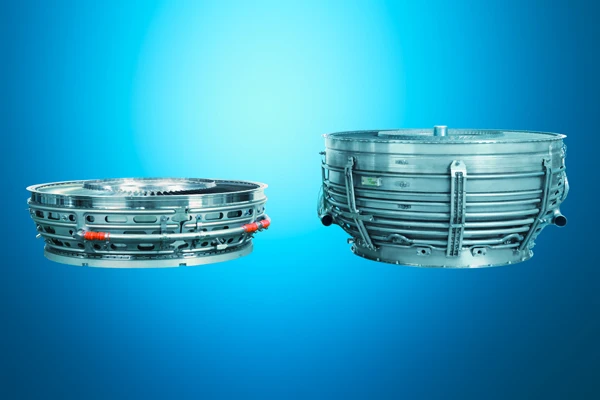
Development of the low-pressure turbine at MTU
MTU has been pursuing turbine technology since the 1960s. The company’s first independent development activities came with the RB199 engine for the Tornado: MTU is responsible for its intermediate-pressure turbine.
When Pratt & Whitney launched an engine for a new generation of medium-sized passenger aircraft with about 200 seats in the early 1970s—under the project name JT10-D—MTU developed and manufactured a commercial low-pressure turbine for the first time in its history. The JT10-D, later renamed the PW2037, went on to power the Boeing 757 and the Boeing C-17 Globemaster military transporter.
Right from the start, the JT10-D’s five-stage low-pressure turbine set standards: its efficiency was high enough to really catch the attention of experts in the field. As a result, it was effectively a foregone conclusion that MTU would again be responsible for this module in a follow-up program: the V2500, which powers the Airbus A320ceo family, among others, and has become MTU’s foremost commercial engine program. This was followed by a number of other low-pressure turbine development programs, such as for the PW300 and PW500 engines that power business jets, and for the PW4000 and GP7000.
Today, MTU has a reputation as one of the world’s most experienced and technologically advanced manufacturers of low-pressure turbines. The most recent development is that MTU’s high-speed low-pressure turbine is a key component of the innovative geared turbofan; MTU is the only company to have mastered it for this application. The GTF Advantage™ is set to receive a further enhanced LPT made by MTU.
What’s special about the high-speed LPT in the geared turbofan?
The GTF LPT achieves significantly higher circumferential speeds, which reduces the aerodynamic load and means the stages can work both harder and with higher stage efficiencies. This allows the stage count to be reduced by almost half.
The high-speed LPT features a new type of aerodynamically optimized 3D airfoil. Opting to have the high-pressure and low-pressure shafts rotate in opposite directions made it possible to integrate the previously standard first guide-vane stage of the LPT into the turbine center frame. Other highlights include a new housing concept for better shielding from hot gas as well as lighter materials for the rotor disks. MTU brush seals reduce cooling and leakage air, and borescope bosses are the first components to be produced on an industrial scale using the additive manufacturing technique of laser powder bed fusion.
What optimizations are planned for the GTF Advantage?
For the GTF Advantage™, MTU experts are further enhancing the high-speed LPT, including its gap management system. Active cooling of the housing is used to minimize the clearance between the blades and the housing for each individual flight state to further increase efficiency and performance. In addition, components are optimized geometrically and aerodynamically.
What innovative technologies can be found in new low-pressure turbines?
For all new LPT concepts, the goal is to have the design strike a balance among efficiency, weight, noise, costs, robustness and service life. To this end, MTU is developing new construction methods for many parts of the LPT.
Advanced computer simulations enable the three-dimensional design of the blade channel, including the side walls and fillet radii. In a bid to further reduce aerodynamic losses, optimized solutions are also being investigated that would prevent air from leaking out through seals on the inner and outer blade edges. Improved blade profiles and measures for targeted boundary layer manipulation are being researched for use at high altitudes and with low Reynolds numbers.
Another focus is on new materials, such as sixth-generation single crystals, and rotor materials that are even more temperature-resistant, and steps are being taken to reduce noise. The integration of the LPT into its adjacent partner components, the turbine center frame and exit case, is being optimized across modules.
MTU is venturing into territory as yet untested anywhere in the world with the production of profile grooves in turbine disks by means of electrochemical machining (ECM). The use of data makes the production of low-pressure turbines more efficient, sustainable and competitive.