good-to-know
A brief guide: The New Generation Fighter Engine
The New Generation Fighter Engine (NGFE) powers the next-generation fighter that is the centerpiece of Europe’s FCAS. We offer some insights into the key technologies behind it.
author: Isabel Henrich | 3 mins reading time published on: 10.06.2024
author:
Isabel Henrich
studied political science and communications. At MTU, she coordinates the editorial process of AEROREPORT and is responsible for the conception and development of its content.
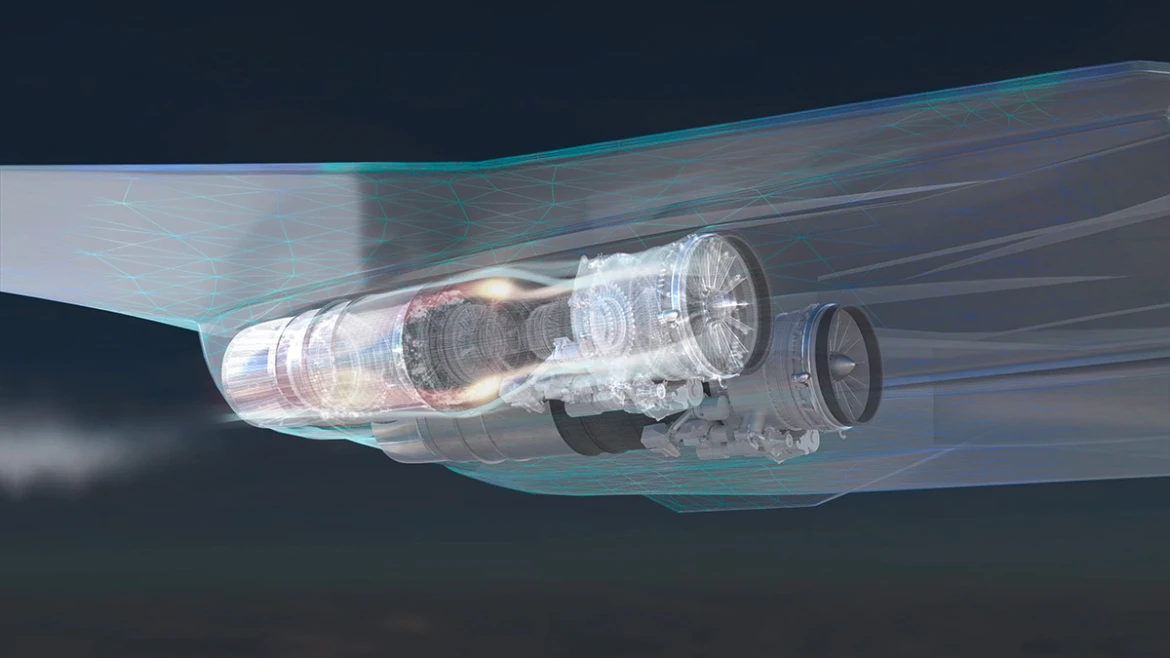
©EUMET
You may also be interested in following content
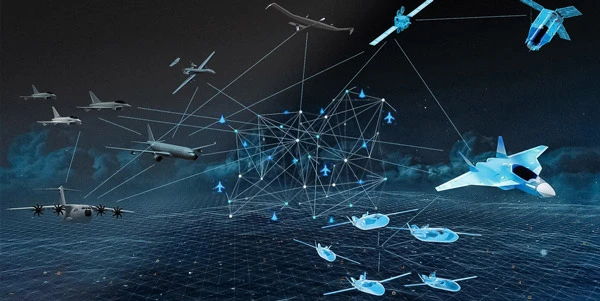
A brief guide: The Future Combat Air System
As a system of systems consisting of various platforms and components, FCAS will be significantly more effective than previous air defense systems.
The Future Combat Air System (FCAS) is the European air defense system that is set to enter into service in 2040. Germany, France, and Spain are working together on this. The centerpiece is the New Generation Fighter, a next-generation jet with a human pilot.
Engine specialists MTU Aero Engines, Safran Aircraft Engines, and ITP Aero are developing the engine for the New Generation Fighter under the leadership of EUMET (European Military Engine Team), an MTU and Safran joint venture. MTU is responsible for its core competencies of high-pressure and low-pressure compressors and the compressor intermediate case as well as for parts of the control systems. It is also the lead company for aspects of engine maintenance. Safran is in charge of engine design and integration, while ITP Aero is responsible for the low-pressure turbine and the thrust nozzle.
What are the core elements in developing an entirely new engine for a fighter jet?
Fighter aircraft like the New Generation Fighter are generally designed to perform a wide range of missions, which calls for reliability, versatility, and cost effectiveness in equal measure. This puts the focus on key operating parameters such as extensive range, high speed (mostly in the supersonic range), good maneuverability, and reduced visibility. Based on the interaction between an aircraft and its engines, these factors can easily lead to snowball effects in system design: a larger aircraft—carrying multiple or larger weapons or more fuel—requires a larger, heavier engine, which in turn calls for a larger aircraft. At the engine level, this creates some particular challenges: the goal is to achieve the greatest possible thrust within a compact and lightweight casing as well as optimized fuel consumption and thermal and power management.
New Generation Fighter Engine: Under the leadership of their EUMET (European Military Engine Team) joint venture, and in collaboration with ITP Aero, engine specialists MTU and Safran are developing outstanding technologies and engine demonstrators that meet FCAS requirements.
To overcome these challenges, the future engine is to feature numerous innovative technologies:
-
A high-load, distortion-tolerant compressor ensures stable and optimal performance even in tough operating conditions. Located at the “heart” of the aircraft, this technology ensures that the combustor has a continuous supply of compressed air.
-
Using state-of-the-art materials, such as advanced alloys and composites, enhances engine performance even in completely new temperature ranges while simultaneously extending the service life under demanding operating conditions.
-
A high thrust-to-mass ratio is crucial for fighter jets, as this facilitates high performance at minimal weight. The result is a more compact, less visible aircraft with superior combat capabilities, including short response times and fast high-speed maneuvers.
-
The engine will feature state-of-the-art thermal and power management with hybrid technologies for core components. It will also be optimized to cope with the limits of aircraft operation.
Future technologies for the military: One promising future concept is the variable cycle engine (VCE), which can facilitate optimum performance over the entire flight envelope. This concept can significantly improve a combat aircraft’s mission flexibility.
-
The variable cycle engine (VCE) architecture supports flexibility in adjusting to operating requirements, which leads to high specific thrust and low fuel consumption. What really sets the VCE architecture apart from conventional propulsion systems is its adjustment mechanism and additional flow channel. The adjustment mechanism helps the engine control system manage how much ingested air flows through each channel and the core engine. Thanks to this variable adjustment, the engine’s thermodynamic cycle can be optimally adjusted to the most likely operating requirements, which in turn ensures high specific thrust and low fuel consumption.
-
A thrust vectoring nozzle gives the fighter jet exceptional maneuverability and control—particularly useful in aerial combat. The engine nozzle can direct the thrust in different directions, allowing the aircraft to change direction with speed and precision.
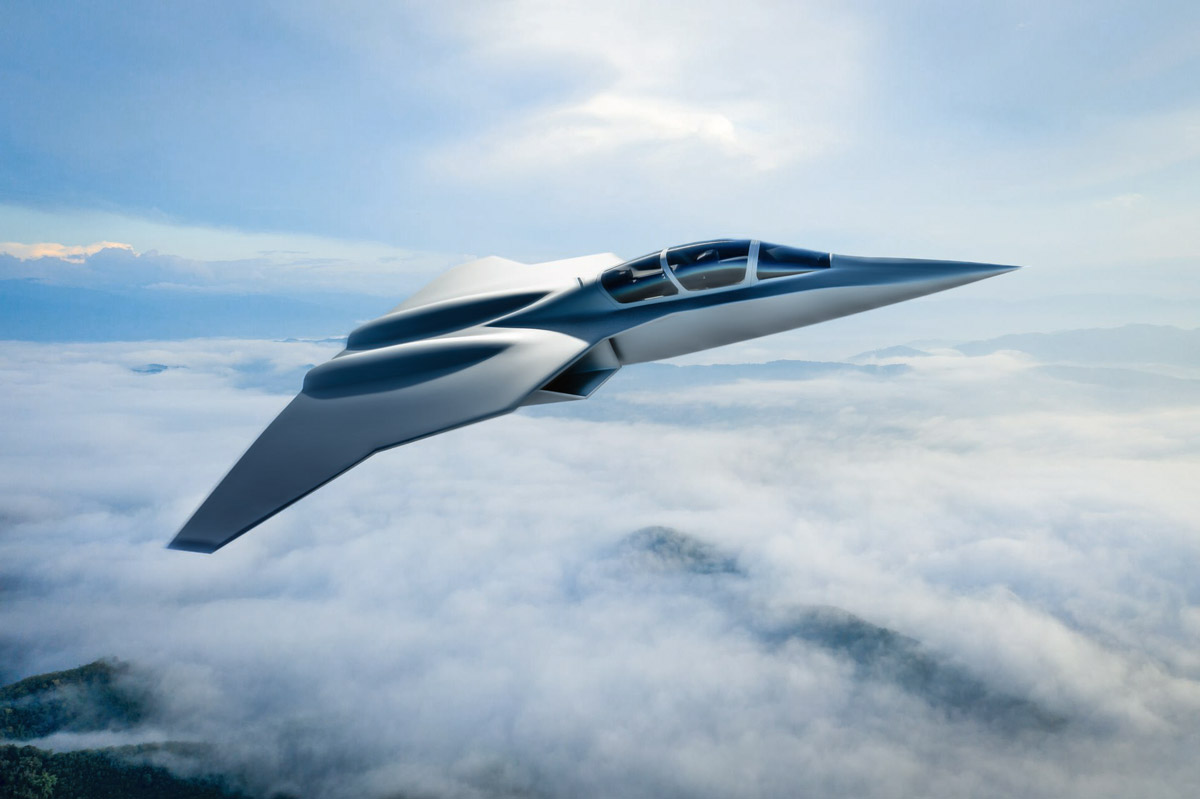
©EUMET
New Generation Fighter: A sixth-generation fighter jet that enables connectivity between the fighter and unmanned components. It uses more advanced key technologies—particularly in the field of electronics and sensors.