good-to-know
How aerial refueling works for military aircraft
Even with state-of-the-art technology, refueling a fighter jet during flight remains an adventure that calls for maximum aeronautical skill and experience. This is how it’s done.
author: Tobias Weidemann | 5 mins reading time published on: 08.02.2023
author:
Tobias Weidemann
has been working as a journalist and content consultant for more than 20 years. He writes about technology and business topics, often with a focus on business IT, digitalization and future technologies.
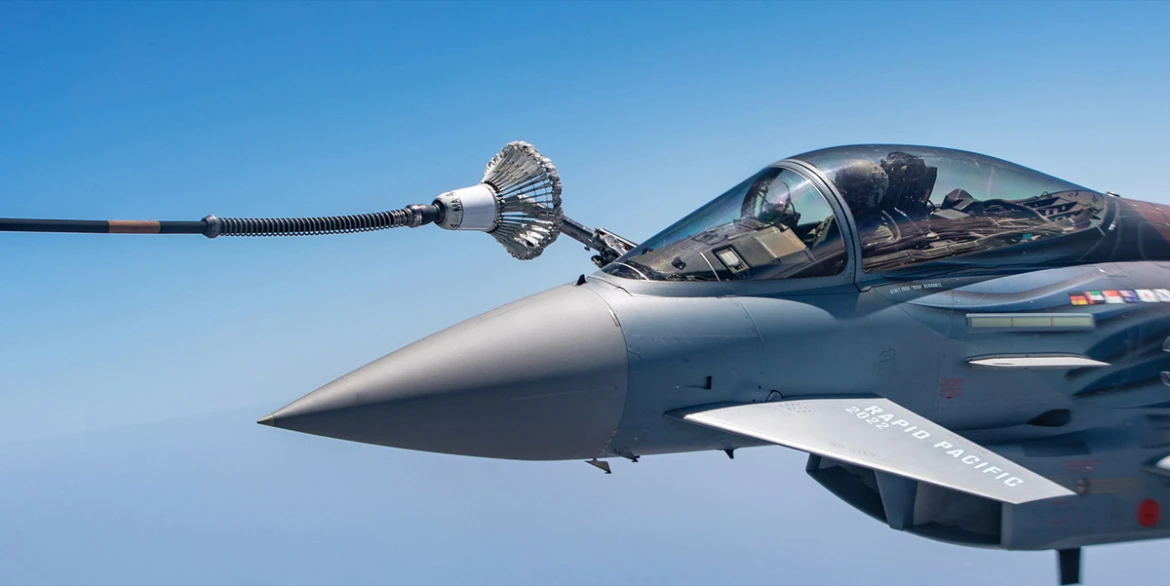
©Bundeswehr
Aerial refueling is still one of the most fascinating maneuvers in aviation: A specially equipped transport aircraft, such as an Airbus A330 MRTT, carrying fuel proceeds to a prescribed position in restricted airspace—in Germany, this risky maneuver is permitted only in a few sparsely populated areas. The fighter approaches from the rear until it is just 20 meters away. As soon as both aircraft are in position and are connected, the refueling process begins and lasts for approximately ten minutes. Depending on the refueling procedure in question, the transporter delivers up to 1,590 kilograms of fuel every minute—at an altitude of between 1,500 and 10,000 meters and while flying at a speed of around 500 kilometers an hour.
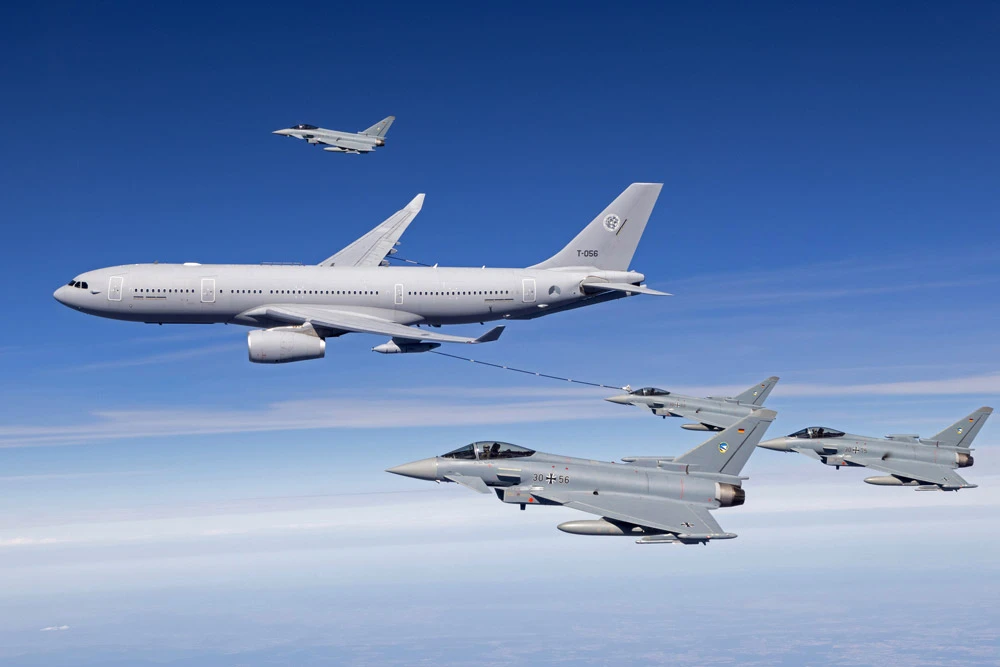
Fascinating maneuvers: Refueling a fighter jet in the air extends its range and pre-vents it from having to waste time making strategically inconvenient stopovers.
The whole process is monitored by an Air Refueling Officer (ARO), who has the controls to adjust the volume of fuel to be delivered and—based on the weather and other local conditions—the speed of the refueling process. To help manage the process, the ARO has access to video and infrared camera systems mounted to the side of the fuselage, which also facilitate reliable docking during hours of darkness. The job of maintaining the short distance between the aircraft and gently making any course corrections falls to the autopilot. Ideally, however, aerial refueling is performed in fair weather with clear skies, good visibility and steady wind conditions. And despite today’s technical possibilities, it still calls for maximum aeronautical precision and experience.
Such operations often involve refueling multiple aircraft, one after another in an intricately planned schedule, before the flying fuel pump returns to the military base. It is also not uncommon to refuel two aircraft simultaneously, provided the weather and airspace conditions permit.
The MRTT—which stands for multi-role tanker transport—version of the Airbus A330 is a versatile transporter. In addition to its uses as a freighter or passenger aircraft, it can also be converted into a flying intensive care unit or, indeed, serve as a flying fuel pump capable of carrying up to 111 metric tons of fuel. To date, this military version of the A330-200 commercial model is in service with four air forces (including the Bundeswehr) and on order for seven countries and NATO. Incidentally, the practice of aerial refueling is exclusive to the military; in commercial aviation, the need to comply with safety requirements means it would be effectively uneconomical and impracticable.
Copyright Airbus 2022
Boom systems vs. probe-and-drogue solutions
There are essentially two established methods of aerial refueling. If a boom system is used, the refueler positions itself in front of the receiving aircraft. The rear of the refueler is equipped with a boom that has limited maneuverability, which allows it to dock with the receiving aircraft’s fuel tank. Locking the boom and nozzles in place completes an electrical circuit that starts the pressurized pumping of the fuel. During refueling, the receiving aircraft flies in formation either behind or below the tanker aircraft. At the end of the refueling process, the valves are sealed and the telescopic boom is retracted.
An alternative method is to use a probe and a drogue, which resembles an oversized shuttlecock. This is attached to a flexible hose that trails behind the refueler. To refuel, the refueler flies in front of the fighter, whose pilot guides the probe into the drogue. The force of the air flow on the drogue establishes a connection between the fuel probe tip and the valve. Once locked, the pressurized refueling process begins.
This method requires the pilot of the receiver aircraft to fly with greater precision; with the boom solution, it is more a question of how well the ARO can maneuver the rigid boom within its limited scope of movement. While the boom’s larger diameter makes it the faster refueling method, the probe-and-drogue method’s 22-meter hose allows the two aircraft to be farther away from one another and thus reduces the risk of collision.
All popular refuelers, including the Airbus A330 MRTT, are suitable for either of these methods. Which one is used depends on the refueling certification given to the aircraft type in question. In addition to these two main concepts, there are also combination solutions that feature both a boom and one or several drogue systems.
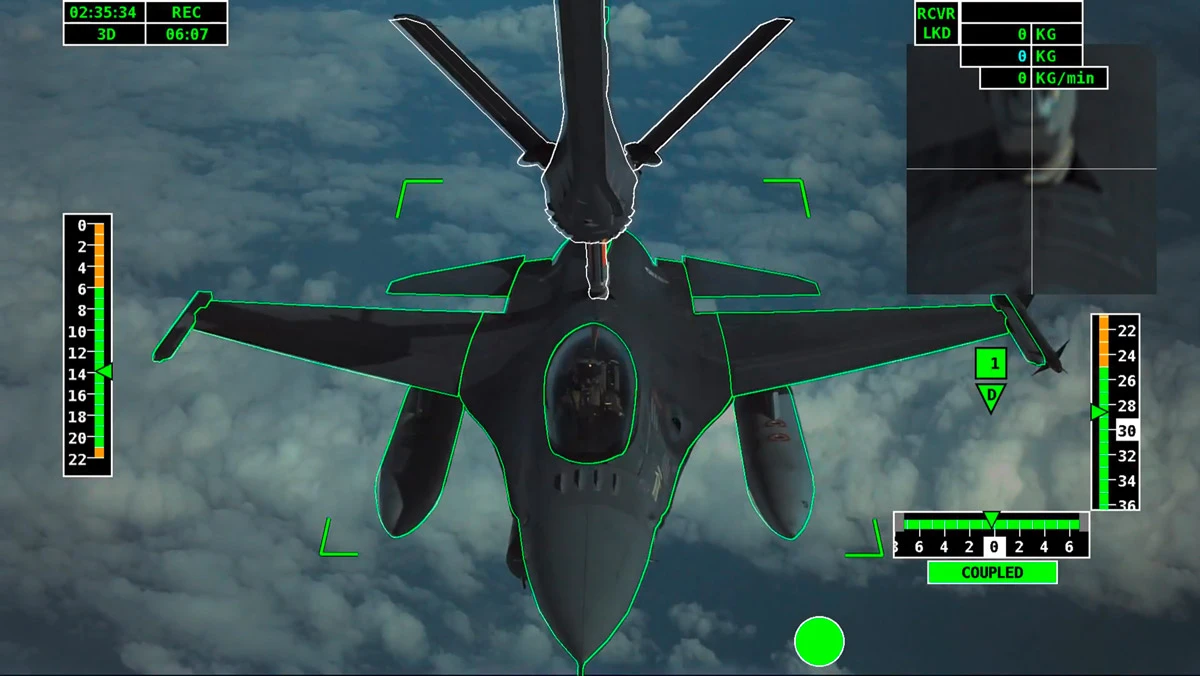
A3R: The air-to-air refueling system reduces the ARO’s workload with the help of automation.
Refueling aircraft will soon be largely autonomous
Although the first forays into aerial refueling were made back in the 1920s, and the various concepts have been refined over the decades, the next few years will also see technical innovations that will trigger further enhancements. For instance, the Airbus A330 MRTT is the first tanker to be certified for automated aerial refueling during daylight.
To gain certification, Airbus developed its automatic air-to-air refueling (A3R) system, which uses automation to potentially reduce the ARO’s workload to simply monitoring the process. Using automated and IT-driven image recognition and processing, the video and infrared camera systems make it easier to align the boom tip with the receiving aircraft’s intake to within a few centimeters. The correct alignment and the stability of the receiving aircraft can be verified in real time.
The system requires no conversion of the receiver aircraft and can make performing refueling operations safer in weather conditions that are less than ideal. In the medium term, this type of refueling process will run largely autonomously and prove reliable even under adverse visibility and atmospheric conditions. One of the goals of the follow-up project, A4R, will be to automate the tasks carried out by the receiving aircraft.
Even if this technology were to relieve some of the burden on the crew, planning these operations will still call for extensive experience and aeronautical skill. But it should make it possible to perform aerial refueling under more difficult conditions than the ones pilots are able to tackle today.
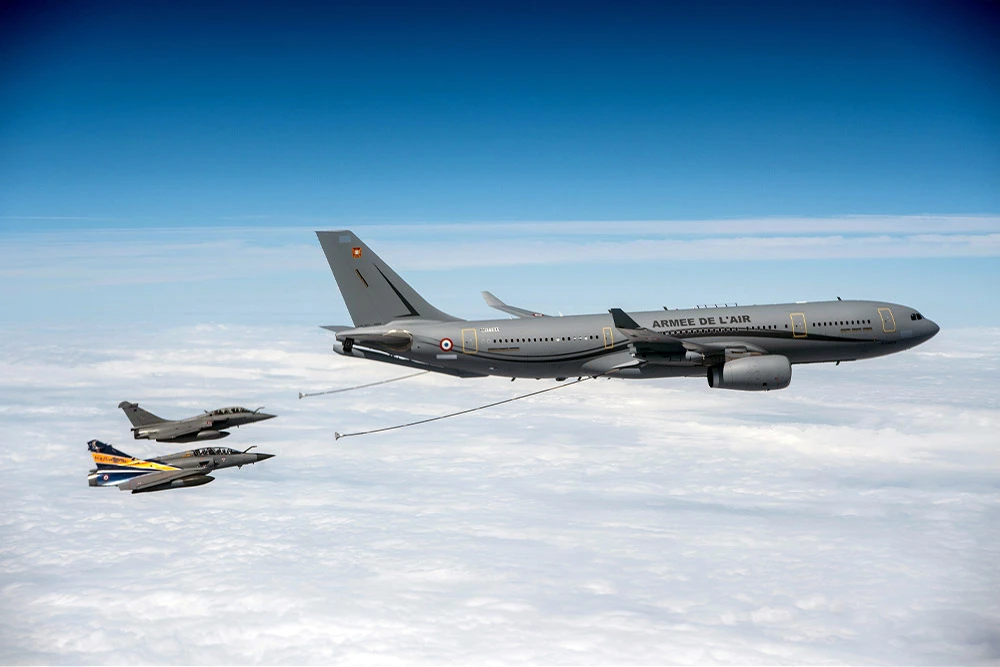
©Airbus - Master Films - Hervé Goussé