aviation
Making old new again: Reinventing the legendary Douglas DC 3
The DC-3 is a legendary aircraft, with some 16,000 built since 1936. Oshkosh-based company Basler turns them into new turboprop-powered aircraft.
author: Andreas Spaeth | 5 mins reading time published on: 08.02.2023
author:
Andreas Spaeth
has been traveling the world as a freelance aviation journalist for over 25 years, visiting and writing about airlines and airports. He is frequently invited to appear on radio and TV programs to discuss current events in the sector.
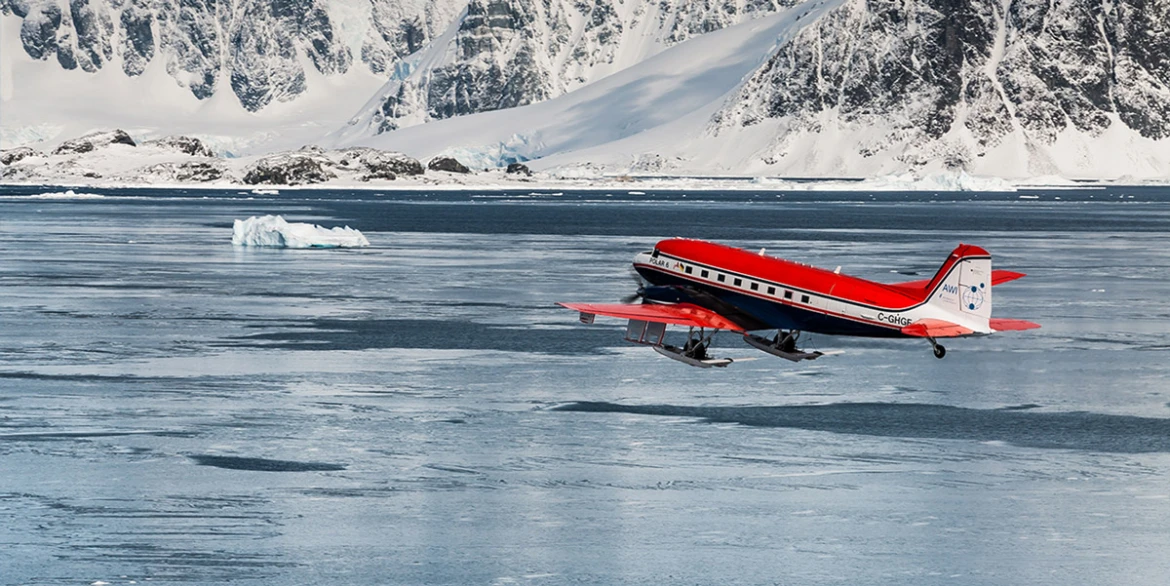
©Michael Fischer
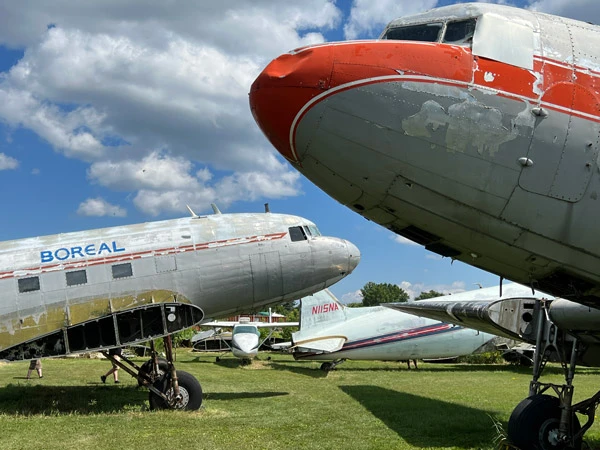
©Andreas Spaeth
No wings, dents in the fuselage: It’s hard to believe that Basler is turning DC-3s that are essentially scrap, some of them 80 years old, back into brand-new aircraft.
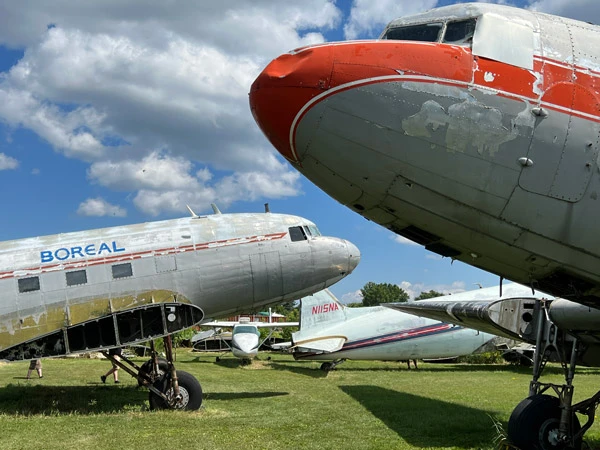
©Andreas Spaeth
In front of the hangar, it looks like an aircraft graveyard: a line of aged Douglas DC-3 Dakotas, their fuselages overgrown with weeds, some without wings, others with broken windows and clouded cockpit windshields. No one would guess that rather than standing at death’s door, these wrecks are about to be given a new lease of life. These veteran aircraft, some of them 80 years old, are waiting to be pushed into the hangar. Around six months and 50,000 work hours later, each will reemerge as a brand-new Basler BT-67. These refurbished aircraft retain some of their original outward characteristics, but are in fact ultramodern and in mint condition. This is the essence of the astonishing business model implemented by Basler Turbo Conversions at Wittman Regional Airport in Oshkosh, Wisconsin.
And business is booming: “Our order books are already full through 2023,” Basler President Joseph Varkoly tells mesmerized visitors as he shows them around the factory hangar, which at 7,000 m2 can accommodate up to four aircraft at a time for their regeneration. Basler is more of a custom contractor than an industrial producer, a specialist provider that used all of its ingenuity and expertise to turn the miraculous “making old new again” metamorphosis into a business model, with customers from all over the world desperate to get their hands on the finished product. Basler currently completes two conversions a year.
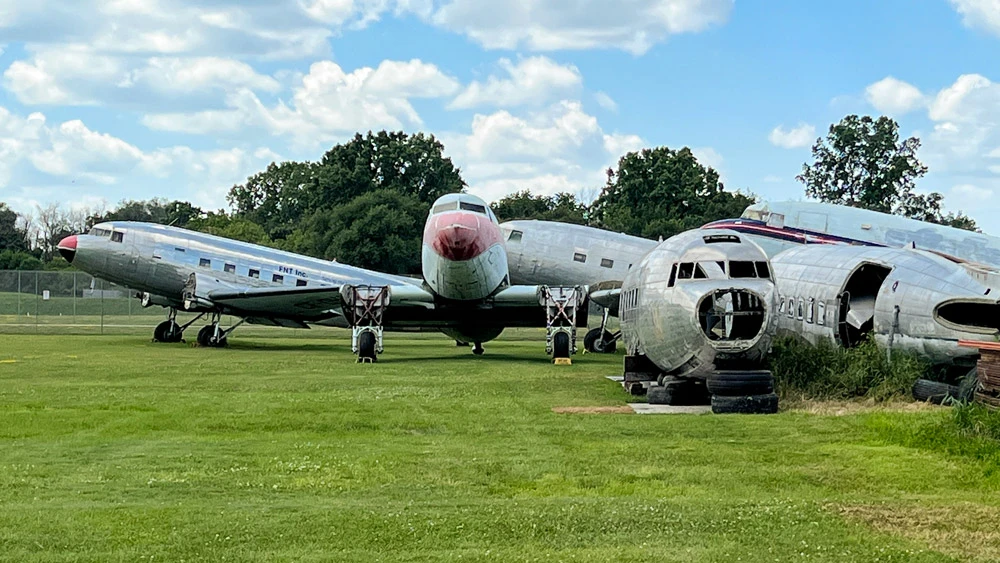
©Andreas Spaeth
Aircraft cemetery in front of Basler’s hangar: In fact, these remnants of old DC-3s are an important basis for production in the years ahead.
300 of 16,000 DC-3s still in service today
The main reason all this is possible is that the twin-engine DC-3s that began to emerge from the Douglas factory in California in 1936 demonstrated a level of resilience, robustness and durability that remains unparalleled to this day. Both the DC-3 (607 had been built by 1942) and especially the military version C-47 (of which more than 10,000 were made) would soon become pillars of aviation. Counting all license variants and subvariants, around 16,000 of these classics were built—and some 300 of them are still in service today. During the Second World War, as “Candy Bombers” during the Berlin Blockade of 1947–48 and later during the Vietnam War, this aircraft was regarded as basic equipment. After the Second World War, many C-47s were converted into passenger aircraft and were the backbone of the global boom in air travel.
It was back in 1980 that company founder Warren Basler (1926–1997) completed the first modern reincarnation of the DC-3/C-47. Brought to market as the Basler BT-67, it soon found buyers. The US Federal Aviation Administration (FAA) recognizes the reincarnations as brand-new aircraft with zero flight hours. “In a typical BT-67, only around 10 percent of the metal from the original aircraft has been retained,” Varkoly says. While it’s sometimes possible to reuse up to 40 percent of the total material, the vast majority of the airframe is replaced, as is the skin. Since original spares for aircraft of this vintage are no longer available, Basler manufactures all the parts—6,800 different components in all—it needs in-house.
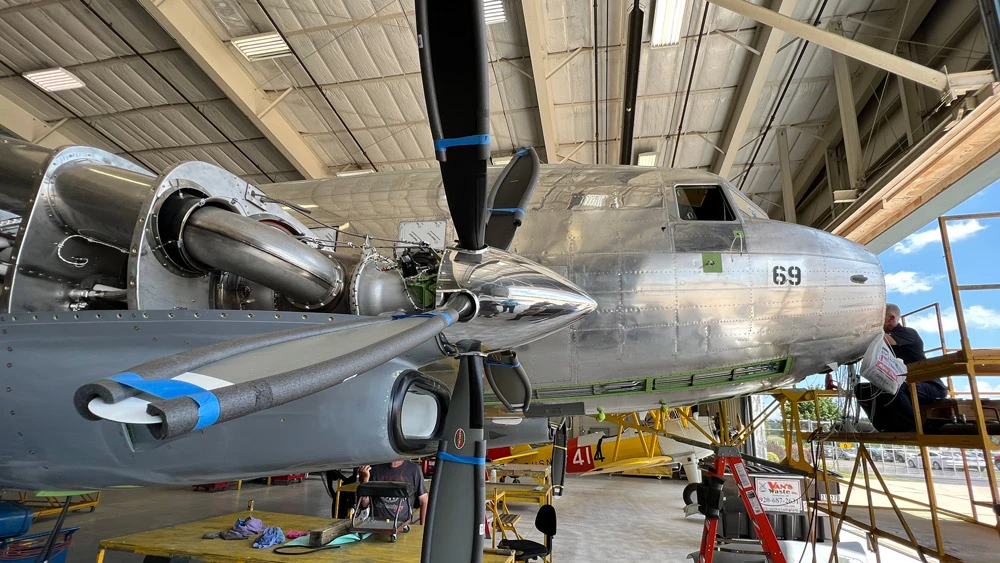
©Andreas Spaeth
Modern turboprop engines, shiny fuselages: Basler turns DC-3 scrap metal into ultramodern special-purpose BT-67 aircraft.
Powerhouses from Pratt & Whitney Canada provide new propulsion
A crucial modification is the incorporation of two new, highly efficient Pratt & Whitney Canada PT6A-67R turboprop engines in place of the old radial engines. Featuring five-blade metal propellors, each of the new engines delivers 1,062 kW (1,424 PS), whereas each engine on a DC-3/C-47 delivered just 895 kW (1,200 PS). As the new composite engine nacelles are much wider than the old housings, the fuselage has been extended behind the cockpit by 1.06 meters to ensure the crew sit further forward than the propellors. This also increases the volume of the cabin by 35 percent. And pilots now have a state-of-the-art glass cockpit featuring the latest avionics, digital instrument displays and even blind landing and all-weather capabilities.
Veteran-based new builds are cheaper
At first it might seem an odd decision to laboriously convert old veteran fuselages instead of just building a new BT-67 from scratch. But there is a simple reason for this: cost. “Testing an entirely new aircraft and getting it certified is more expensive than our conversions that tend to use only the fully renovated original airframe,” Varkoly says. New parts are generally manufactured according to the original specifications of the DC-3, which has an outstanding safety record.
“They can fly for up to 11 hours, and with long-haul auxiliary tanks even up to 13 hours. A Twin Otter turboprop can manage just three to four hours.”
Basler President
A small company like Basler could never afford a new certification. The price of a new BT-67 starts at around 12 million U.S. dollars, with many custom builds likely to be much more expensive. Each BT-67 is customized to cater for the huge variety of requirements depending on the given use case, the range of which is virtually limitless. The 69th BT-67 will be completed by the end of 2022 and the 70th is already in the works.
Germany, Australia and China use these aircraft for research purposes and for supplying Artic and Antarctic bases with the help of the wheel/ski modification option. Varkoly is aware that it’s really the stamina of his BT-67s that is more sought-after than ever before: “They can fly for up to 11 hours, and with long-haul auxiliary tanks even up to 13 hours. A Twin Otter turboprop can manage just three to four hours.”
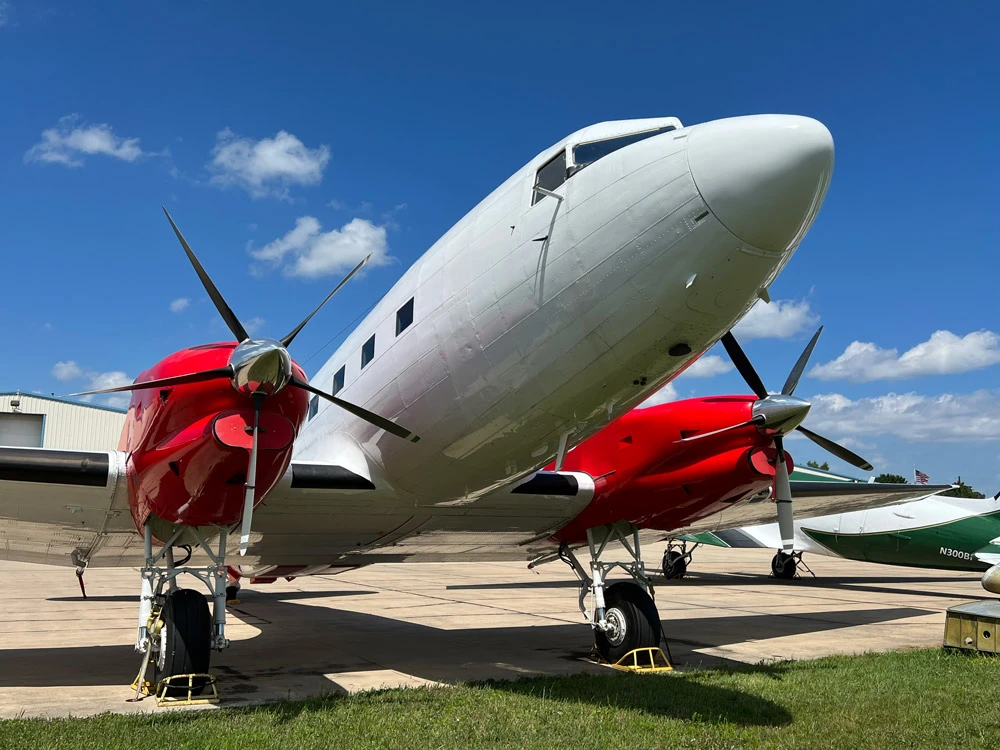
©Andreas Spaeth
The result of all the efforts: A BT-67 straight off the assembly line, in demand worldwide for a variety of special missions.
PT6 – the all-around talent
An aviation classic, the Pratt & Whitney Canada PT6 turboprop engine first flew in 1961. It is available in different sizes for applications ranging from single-engine sports aircraft to helicopters. The largest variant of the PT6A is for heavier twin-engine aircraft like the BT-67 or the Short 360 regional commuter airliner. Approximately 12,000 of these large PT6A engines are around today, and it is estimated that, counting all variants, some 55,000 PT6 engines have been built to date.
MTU Maintenance Berlin-Brandenburg in Ludwigsfelde offers maintenance services as part of the P&WC Customer Service Centre joint venture with Pratt & Whitney Canada (P&WC). “We work on between 60 and 80 PT6A engines a year,” says Jens Arend, Director of Pratt & Whitney Canada programs at MTU Maintenance Berlin-Brandenburg. “Up to 50 percent of these are the large variant.” Ludwigsfelde has also serviced a pair of PT6A-67R engines, which power the Basler BT-67, but these particular examples were on the wings of a Short 360.
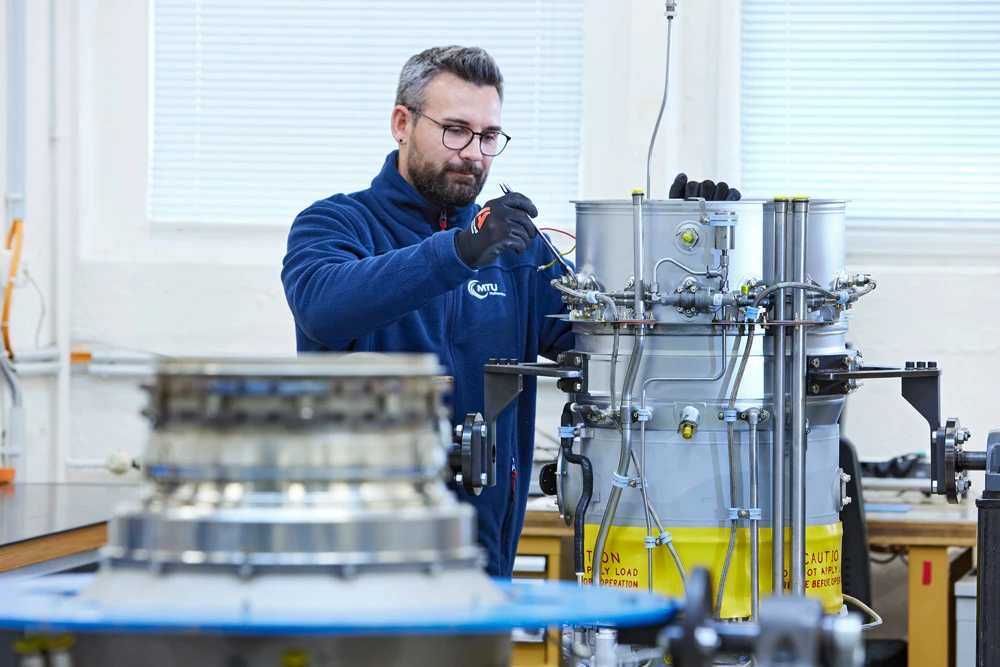
Maintenance professionals: Maintenance of the PT6A is performed at MTU Maintenance Berlin-Brandenburg as part of the worldwide Pratt & Whitney Canada Customer Service Centre.