innovation
DLR and MTU: Joint research for zero-emission aviation
Computer models, test labs and a fleet of research aircraft—at DLR’s Institute of Propulsion Technology, MTU is testing and optimizing components for the next generation of geared turbofan engines.
author: Monika Weiner | 6 mins reading time published on: 05.08.2022
author:
Monika Weiner
has been working as a science journalist since 1985. A geology graduate, she is especially interested in new developments in research and technology, and in their impact on society.
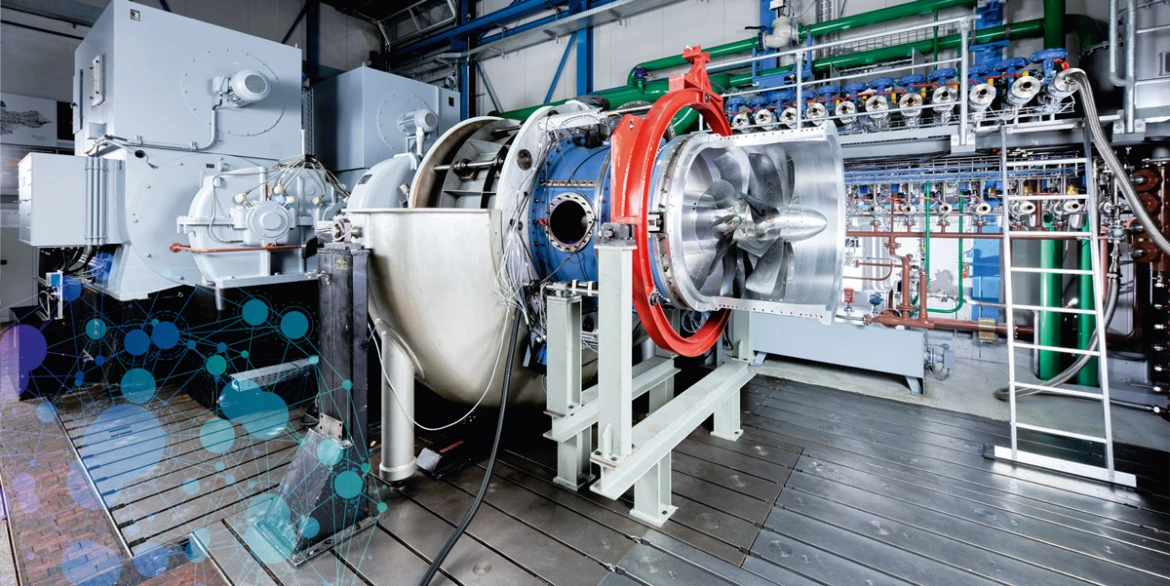
©DLR
German Aerospace Center (DLR) DLR is the Federal Republic of Germany’s research center for aeronautics and space. It conducts research and development activities in the fields of aeronautics, space, energy, transport, security and digitalization. DLR has 55 institutes and facilities and employs 10,000 people, who all share the same mission: to research the Earth and space and to develop technologies for a sustainable future. The Center develops solutions tailored to the aviation industry that enhance the current and next generations of technology. DLR applies its research expertise in aviation as an overall system to pursue the aspiration of developing sound proposals for subsequent technology generations and thus pioneer new perspectives. MTU has been collaborating with DLR since the 1990s.
- DLR and MTU: Joint research for zero-emission aviation
- MTU and universities: Cutting-edge research for future technologies
- MTU and Fraunhofer: Research partners for Industry 4.0
Right next to Cologne Bonn Airport sits the test lab operated by the Institute of Propulsion Technology at the German Aerospace Center (DLR). Inside, two electric motors—each with an output of five megawatts—are purring, oil pumps and measuring devices are hanging on the walls, and strands of cables are hooked up to a ten-meter test station in the center of the room. Everything is in place for real-world testing to begin. What’s special about the “multistage 2-shaft compressor test facility,” or M2VP for short, is that its two shafts can be driven independently from one another by the electric motors. Thanks to a combination gearbox, these motors can generate infinitely adjustable speeds of up to 20,000 revolutions per minute—it’s even possible to have the shafts rotate in opposite directions. “This test set-up is virtually unique. It enables us to examine and test the operating behavior of each test object under very realistic conditions,” says Dr. Christian Tiedemann, Head of the Fan and Compressor department at DLR’s Institute of Propulsion Technology. “Testing under these realistic conditions helps developers of new engines optimize the aerodynamics of their components, increase engine efficiency and reduce emissions.”
Engine modules headed for Cologne
Researchers from MTU Aero Engines and its long-standing partner GKN Aerospace have already reserved a slot in Cologne: in spring 2023, three modules—stages of the high- and low-pressure compressors together with the duct that connects them—are scheduled to arrive at the test stand. It is hoped that the tests in Cologne, which will take place as part of Clean Sky 2, will verify the sought-after aerodynamic improvements. The components for the modules are currently being produced and packaged for their journey, which will begin in winter.
The inter-compressor duct: Making the interaction visible
When developing a highly efficient engine, it’s particularly important to ensure that the high- and low-pressure compressors work in harmony. The two are connected by the inter-compressor duct (ICD), which gets progressively narrower from front to back, and it’s essential to optimize the air flow in this duct. To save weight, and thus fuel, the engineers are trying to make the ICD as short as possible. At the same time, the ICD can’t be too short because this would prevent the air from flowing along its inner wall as intended. When the air flow strays from the wall, vortices are produced, which in turn cause friction that reduces the engine’s efficiency.
“A crucial point in engine development is achieving the balance of an ICD that’s as short as possible while also offering optimum aerodynamics,” explains Dr. Deni Nakaten, Module Team Leader for the two-shaft rig at MTU. “This balancing act starts with the initial designs and models and continues right though to the end of development, when we measure the interaction of air flows on the M2VP test stand.”
Collaboration at every stage of development
At all these stages of development, MTU works closely with DLR: together the partners developed the TRACE aerodynamics simulation tool. TRACE can be used to produce 3D simulations of unsteady air flows in compressors and turbine elements, for instance, and help reduce waste and lower noise emissions. MTU engineers also used TRACE software to optimize the ICD for the next-generation geared turbofan currently being tested. Three years ago, the prototypes, which were manufactured in Munich, were assembled at DLR’s Institute of Propulsion Technology in Cologne and put through their paces on a test stand specially designed for ICD rigs. “These tests helped us take a close look at the threshold at which the air flow strays. This model validation will be a key step in all future developments,” Nakaten says. All that’s missing now is an in-depth analysis of how the modules interact: How do air flows from the high- and low-pressure compressors influence what happens in the ICD? Do vortices occur that inhibit performance? Or is the air flow already ideal and increasing efficiency during flight?
The only way to answer these questions is to conduct experiments on the M2VP. At the DLR lab in Cologne, MTU engineers will have to reassemble all the individual parts of the new geared turbofan and connect it to a “two-shaft rig”—the test object comprising the two compressors and the ICD. Once this rig has been integrated into the test stand, and all the modules have been connected to motors and sensor systems, the tests can begin. The first job will be to measure the aerodynamic interactions between the modules. After comparing the results with the computer models, the engineers can further optimize the design as needed.
Test Stand
Multistage 2-shaft axial compressor test stand (M2VP): Stages of the high- and low-pressure compressors together with the inter-compressor duct (ICD) that connects them are assembled on the M2VP to form a “two-shaft rig.” This makes it possible to measure the aerodynamic interactions between the modules: How do air flows from the high- and low-pressure compressors influence what happens in the ICD? This duct must ensure optimum air flow and at the same time be as short as possible to save weight and thus fuel.
Increase efficiency, avoid pollutants
“Ultimately, we’re looking to minimize our climate-relevant emissions. A significant proportion is carbon dioxide, which can be lowered by increasing efficiency and thus reducing fuel consumption,” says Dr. Martin Stadlbauer, Senior Vice President for Advanced Commercial and Military Programs at MTU. “Compared with the already very efficient first-generation models, the next generation of geared turbofans from the Pratt & Whitney GTF™ engine family are expected to emit significantly less carbon dioxide.”
But enhancing geared turbofan technology is just one of many projects in which DLR researchers and MTU engineers are developing new technologies to make flying more environmentally friendly. The flying fuel cell (FFC), for example, is designed to convert hydrogen into electricity, which can then be used to power an aircraft. A prototype electric powertrain will be installed in a Do228 research aircraft operated by DLR. Another pioneering propulsion concept is the WET engine, which utilizes residual heat from its exhaust gas. It uses a steam generator to vaporize water, which is then injected into the combustor. This kind of “wet” combustion increases the engine’s efficiency and slashes nitrogen oxide emissions. “Our collaboration with DLR is fundamental to all these projects,” says Dr. Arne Weckend, Technology Collaboration Representative at MTU. “In addition to having exceptional in-depth knowledge, the experts at DLR also have the requisite experience to assess aviation’s impact on the atmosphere and climate.”
Tiedemann adds that DLR also benefits from the collaboration with MTU: “We want to apply our research to make aviation cleaner. So it’s important that we work with manufacturers to improve the efficiency of individual parts as well as entire engines and aircraft, and to develop practical solutions that will enable climate-neutral flight.”
Collaboration on all levels
The list of collaboration projects is long and getting longer all the time. MTU engineers have been working closely with DLR researchers for many years on everything from researching new materials to developing new engine concepts. To enhance the design of new engines, DLR and MTU together developed the TRACE simulation program. Its uses include optimizing the aerodynamic and aeroelastic properties of engine blades. TRACE helps improve an engine’s efficiency and ensure the stability of the blades, which oscillate during flight due to the movement of the air.
Another area of focus for the collaboration between MTU and DLR is researching the properties of new metallic materials and compounds. Simulations and extensive test programs conducted under realistic conditions help ensure that these new materials are suitable for use in engines. The experts from MTU and DLR also collaborate on developing new kinds of protective coatings for engine parts. These coatings decrease the parts’ thermal load during operation and increase their service life. As part of other research projects, DLR and MTU engineers explore how an engine—or its interaction with the aircraft—affects noise emissions. The findings of this research provide the basis for new designs that help lower noise levels.