innovation
MTU and Fraunhofer: Research partners for Industry 4.0
For the past two decades, Fraunhofer researchers have been working with MTU to develop new technologies for building and maintaining engines and put the results into practice.
author: Monika Weiner | 5 mins reading time published on: 14.11.2022
author:
Monika Weiner
has been working as a science journalist since 1985. A geology graduate, she is especially interested in new developments in research and technology, and in their impact on society.
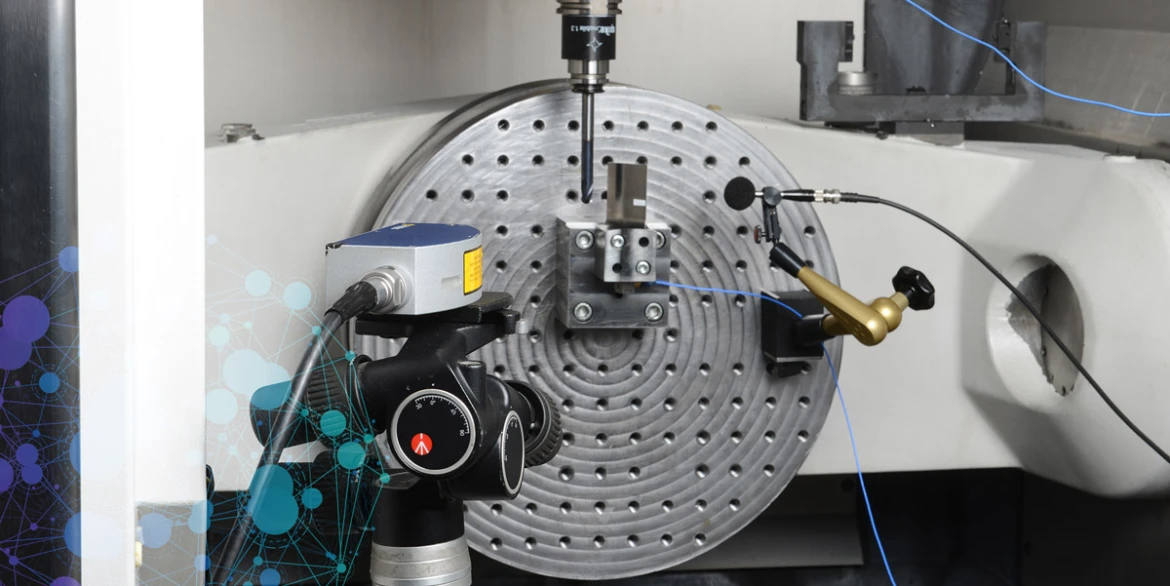
“Simulating the sequences during a five-axis milling process was a real challenge,” recalls Dr. Sascha Gierlings, Head of the Turbomachinery division at the Fraunhofer Institute for Production Technology IPT. “We can’t really look inside machining devices like this. It’s a black box: the input variable is a titanium disk, and about 40 to 60 hours later, the finished machined blisk can be removed.” To investigate what’s going on inside this black box, the team from the High Performance Machining department is operating a five-axis milling machine in the Fraunhofer IPT machine shop in Aachen, Germany—the same model used by MTU Aero Engines in Munich. This will help the engine manufacturer safeguard and evolve its high-tech production processes.
- DLR and MTU: Joint research for zero-emission aviation
- MTU and universities: Cutting-edge research for future technologies
- MTU and Fraunhofer: Research partners for Industry 4.0
MTU is one of the world’s leading blisk manufacturers. Blisks—blade integrated disks—are disks of titanium or nickel with aerodynamic blades integrated around their edges. These compressor rotors, which compress the air from the engine intake, have an extremely complex geometry. At its Munich site, MTU uses a five-axis milling machine to turn blanks into titanium blisks. Since the demands placed on material properties, surfaces and geometric precision are high, so are the risks: should the quality inspection reveal a defect in a blisk, this expensive, high-tech component’s only worth might be as scrap.
“Even small glitches in production can lead to a costly reject and thus to considerable psychological stress. So it’s imperative that the cause of the defect, surface imperfection or crack be found and remedied as quickly as possible,” says Dr. Ulrich Retze, Head of Production Process Simulation at MTU. But in the case of a five-axis milling machine, the interplay of forces between the tool and the workpiece is incredibly complex. This is why Retze and his team use computer programs to visualize cause-and-effect correlations. “Thanks to these simulations, we can now troubleshoot during production. If a problem arises, we can quickly identify what might be causing it,” Retze says. This troubleshooting program was developed as part of the Virtual Milling Processes project, in which MTU has been collaborating with Fraunhofer IPT for the past two years.
While the five-axis milling machine makes a blisk in the service of science, Fraunhofer engineer Pascal Kienast can follow each step in the process from his office in real time. Kienast spent three years developing the algorithms that help create a virtual representation of information from the machine, including the workpiece’s size and position, material abrasion and the precise movements of the part and the tool. With just a couple of clicks, Kienast can visualize what forces are in play, how and where vibrations are intensifying, the consequences of defects in the spindle or bearings, and whether the condition of the blisk meets the prescribed criteria. Back in Munich, Retze and his team are applying the results of this sophisticated research work.
Gierlings emphasizes that this is only the beginning: “In the first stage of the project, we used the simulations to visualize correlations and can thus improve the process stability of our manufacturing. The next will be about enhancing the software tools so that they efficiently support us in process design for new component geometries.”
How simulations save time and money
Reconfiguring production for a new generation of blisks is still a complex and costly business: “Finding the right settings is a matter of trial and error, which makes rejects inevitable,” Retze says. “Being able to optimize machine control in advance would allow us to save a lot of time and money.”
By the time the project concludes in five years’ time, the engineers plan to have taken the simulation program yet another step further: “In the long term, it’ll be possible to use more and more milling machine data to monitor and control large-scale production and thus increase process stability,” Gierlings says.
Prototype development: At Technikum Blisk, MTU and Fraunhofer ITP are developing the blisks of tomorrow.
Almost two decades of joint research
Developing the virtual milling process is just one of many collaboration projects: “MTU and Fraunhofer IPT began working together back in 2003 and jointly operate the ‘Technikum Blisk’ facility for prototype development since 2017,” says Ann-Kathrin Jung, Program Coordinator Technology Partner Management at MTU. “Over the years, we added more and more projects with other Fraunhofer Institutes as well.”
In one such project, researchers at the Fraunhofer Institute for Laser Technology ILT examined how laser powder bed fusion (LPBF) might be used in the manufacture of turbine components: here, the workpiece is built up layer by layer—like in a 3D printer—from metal powder fused together by a powerful laser beam. Another example is the creation of new, particularly heat-resistant titanium-aluminum alloys for engine components at the Fraunhofer Institute for Manufacturing Technology and Advanced Materials IFAM in Dresden. Based on this cooperation, work is currently being carried out on the high-temperature application of IN718 (nickel-based alloy).
In June 2022, the Fraunhofer-Gesellschaft joined MTU’s centers of competence (CoC) network, making the organization a strategic research and development partner. “The special thing about the Fraunhofer Institutes is that they not only contribute important findings from research, but they also put them into practice together with our engineers,” Jung points out. This is why the new CoC has “Industrialization” in its name. “The Industrialization CoC upgrades the collaboration to a strategic research partnership in the field of production and industrialization technologies,” the agreement states. “Specifically, MTU intends for the CoC to support ongoing research and development activities over the long term while also driving forward practical, targeted research for future generations of engines.”
The Fraunhofer-Gesellschaft
Headquartered in Germany, the Fraunhofer-Gesellschaft is the world’s leading organization for applied research. By focusing on developing key technologies of relevance to the future and harnessing the results to the benefit of industry and the economy, the organization plays a vital role in the innovation process.
Established in 1949, it currently operates 76 institutes and research institutions across Germany. Over 30,000 employees, the majority of whom are science and engineering graduates, work with an annual research budget of more than 2.9 billion euros. Of this sum, 2.5 billion euros is generated through contract research.
Dialogue forums for new projects
To identify new fields of collaboration, MTU and Fraunhofer experts now take part in regular dialogue forums. At the first of these meetings, which took place in 2021, the focus was on maintenance, repair and overhaul (MRO). Engine maintenance takes a lot of time and effort—components must be taken apart, inspected and put back together again. In collaboration with the Smart Maintenance Community (SMC)—an affiliation of a dozen Fraunhofer Institutes—MTU now wants to explore how digital technologies could make the process of maintaining engine modules more efficient and economical.
This year’s meetings added the flying fuel cell (FFC) to the agenda. These discussions centered around new manufacturing methods and techniques plus options for process optimization and quality assurance and special assembly technologies to enhance the performance of the FFC.
“The discussions at the dialogue forums have shown that there are numerous opportunities beyond the existing and previous projects for MTU to benefit from this collaboration. The spectrum of joint activities ranges from the development of new materials and propulsion technologies to more efficient engine maintenance,” Jung says.