innovation
MTU and universities: Cutting-edge research for future technologies
Applied research with excellent university partners serve as a key catalyst and source of knowledge for MTU—for example, for technology development in the field of maintenance.
author: Nicole Geffert | 6 mins reading time published on: 10.08.2022
author:
Nicole Geffert
has been working as a freelance journalist covering topics such as research and science, money and taxes, and education and careers since 1999.

- DLR and MTU: Joint research for zero-emission aviation
- MTU and universities: Cutting-edge research for future technologies
- MTU and Fraunhofer: Research partners for Industry 4.0
MTU Maintenance Hannover’s test stands are bustling with activity. Here, overhauled engines undergo the necessary acceptance runs in quick succession. Integrating special tests for research purposes into this tight schedule requires smooth collaboration. Proof that this is possible has now been provided by MTU and teams from two of the company’s research partners: the Institute of Jet Propulsion and Turbomachinery (IFAS) at Technische Universität Braunschweig and the Institute of Turbomachinery and Fluid Dynamics (TFD) at Leibniz University Hannover (LUH).
“Our university partners put in a strong performance,” says Dr. Jörn Städing, Technology Coordinator MRO at MTU Maintenance Hannover. Their program included a complex back-to-back test, which involves comparing the test results of two different high-pressure compressor configurations. The test is part of a joint technology project between MTU and the IFAS. To this end, the IFAS V2500 research engine was set up on the MTU test stand twice within a few months and equipped with special measurement technology. Meanwhile, the TFD research team used the special test for an exhaust gas analysis. The novel method they tested for early detection of damage in the hot gas path involves measuring the exhaust gas stream optically.
Improved repair technologies
This experiment was part of a project in the Collaborative Research Centre (SFB) 871: Regeneration of Complex Capital Goods, located at LUH. Since 2010, an interdisciplinary team of scientists have been using the example of a commercial aircraft engine to investigate how complex capital goods can be repaired in an efficient and resource-saving manner. They developed a novel approach that combines improved repair technologies with a virtual fact-based decision-making process. “This Collaborative Research Centre developed many different technologies relating to engine repair—from novel optical measurement methods to welding repairs and production planning processes,” says Dr. Michael Bartelt, Director Industrial Engineering at MTU Maintenance Hannover. “Working together with our university partners is extremely valuable for MTU as a maintenance specialist, and it shows just how effective an industry setting can be for making the link between fundamental research and practical application,” he continues.
MTU has long maintained communications with SFB871. “Technology development certainly isn’t standing still in maintenance either,” Städing says. “We’re going to further optimize our overall MRO process and make it even more efficient. What’s more, technological progress can also enable entirely new MRO products—for example, in the form of special maintenance services.”
Collaboration with top-performing universities and institutes is a given in research and development at MTU. These partnerships serve as a key catalyst and provide new knowledge. And because MTU’s experts are involved in day-to-day business, they have little time for basic research themselves. That’s why MTU relies on collaboration with universities.
Long-term, strategic partnerships
“MTU has established centers of competence with selected universities,” explains Ann-Kathrin Jung, Program Coordinator Technology Partner Management at MTU Aero Engines. “We maintain long-term, strategic partnerships with these universities and conduct special research projects in the area of our core competencies.” In addition to the centers of competence, MTU collaborates with other top-class university partners on specific issues.
Many years of close collaboration and intensive, personal dialogue are every bit as important as academic expertise. In 2008, MTU joined forces with LUH and the Laser Zentrum Hannover to found the Maintenance, Repair & Overhaul Center of Competence and conduct joint research into future issues in repair development and maintenance strategy. Since 2019, Technische Universität Braunschweig and its IFAS institute have also been part of this center of competence.
“MTU’s technological expertise and the high demands it places on us are what make this open and trusting collaboration so appealing,” says Professor Jörg Seume, Executive Director of the Institute of Turbomachinery and Fluid Dynamics at LUH. The universities conduct research independently, but also in an application-oriented manner as part of the collaboration. For the research activities in SFB871, MTU provided not only its test stand but also components that had been subjected to operational stress so that the research teams can study the effects of wear.
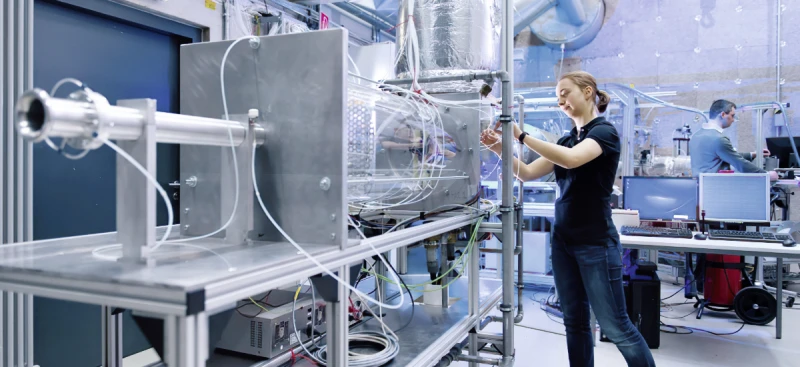
Engine condition monitoring: At the University of Stuttgart’s Institute of Aircraft Propulsion Systems (ILA), entire engines or their modules can be put into operation on test rigs. There, they are examined for their behavior at high altitudes using individual measuring instruments and high-performance computers.
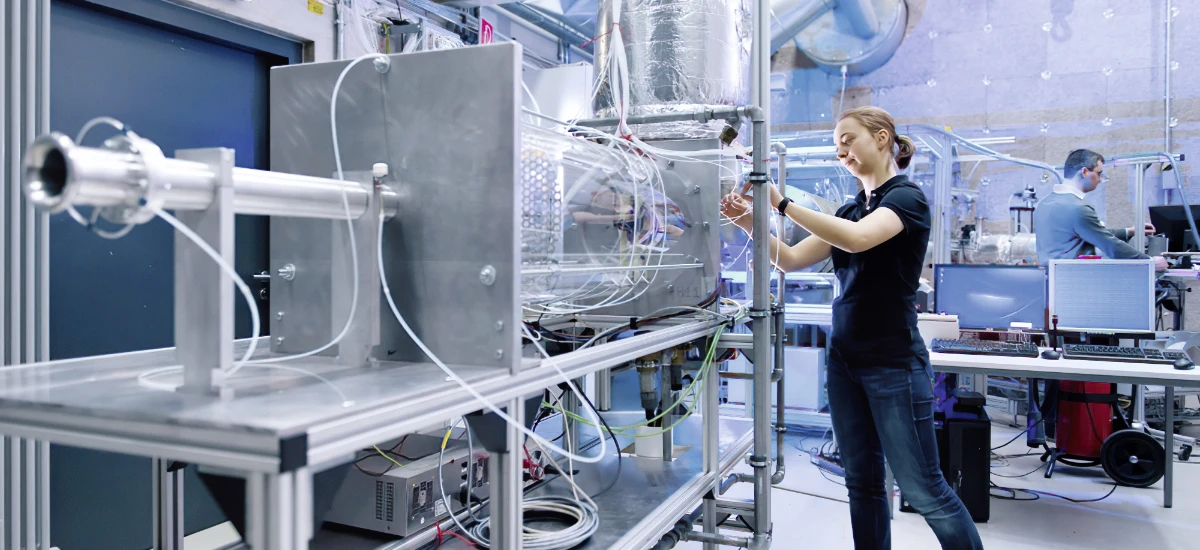
Transfer to industrial application
“By collaborating with MTU, we can test our methods in a real industrial environment,” Seume says. As a result, over more than 12 years of challenging project work, the TFD team has gained a deeper understanding of the cross-component effects in an engine. Seume says: “Many results have reached a maturity that allows us to transfer them to industrial applications.”
MTU is working with another excellent partner in the field of predictive maintenance: in 2006, it founded a joint center of competence for turbine testing and thermodynamics with the University of Stuttgart. MTU’s research partners are the university’s Institutes of Aircraft Propulsion Systems (ILA) and of Aerospace Thermodynamics (ITLR). At ILA, MTU can connect with scientists conducting research in the fields of lifecycle analysis, condition monitoring, structural mechanics and aeronautical propulsion systems of the future.
To monitor the condition of engines, MTU has developed engine trend monitoring (ETM), which monitors and evaluates important engine parameters measured in flight. The knowledge and experience gained from shop visits can be used to identify anomalies at an early stage and prevent engine failures. “The ETM system is being continuously developed, and ILA is an important partner for us in this process,” says Jürgen Mathes, an expert in engine health monitoring at MTU Aero Engines.
Highly motivated university partners
In the future, instead of two to five discrete data points per flight, data will be recorded continuously. Experts use the term “full flight data” to refer to the recording of one data point per second. Making this 1 hertz data useful for ETM requires innovative methods from the fields of advanced data analysis and machine learning. Mathes says: “Developing these pioneering methods calls for a combination of expertise in aerospace propulsion and in data analytics.”
And MTU can access this expertise at ILA, which is headed by Professor Stephan Staudacher. “At this stage of condition monitoring, algorithms and artificial neural networks both play an important role,” he says. “Since we also conduct research in this area, we put MTU in touch with students and graduate students in this field, who develop solutions as part of a master’s or doctoral thesis.”
Mathes can see how motivated MTU’s university partners are: “Together with our university partners such as the ILA, we are continuously developing new, forward-looking projects.” This practical approach also enables MTU to secure young talent from universities at an early stage. For Staudacher, collaborating with MTU is part and parcel of a high-quality scientific education: “It lets young people learn the rules of such partnerships, as well as how to act in a reliable and trustful way.” And he is pleased when graduates from his institute find interesting positions at MTU. “MTU’s corporate culture makes it particularly attractive to young people,” Staudacher says.
Mathes considers personal contact with the universities to be very important. Accordingly, he has agreed to give a lecture at ILA on ETM in practice—and will also taking the opportunity to draw attention to MTU as a technology leader and innovative employer.