innovation
How robots help screw together compressor rotors
Digitalizing a process that evolved over years of maintaining and repairing compressor rotors is a way to increase process reliability while reducing failure rates.
author: Tobias Weidemann | 5 mins reading time published on: 10.01.2023
author:
Tobias Weidemann
has been working as a journalist and content consultant for more than 20 years. He writes about technology and business topics, often with a focus on business IT, digitalization and future technologies.
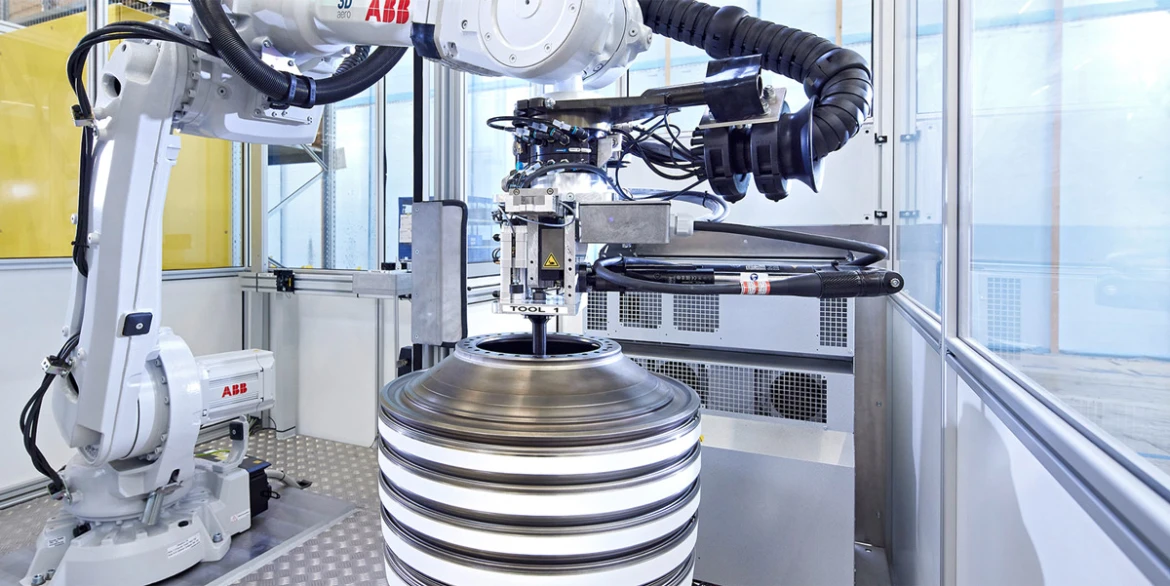
Screwing together a compressor rotor demands considerable patience. This is a job that must not be rushed and that calls for a steady hand. Mechanics begin by aligning the two drums before placing 34 nuts and the corresponding washers, one by one, at the correct position. They fasten the nuts loosely and then tighten each one in turn in several stages and with precisely the right amount of torque. To ensure this doesn’t warp the component, they tighten the nuts in opposite pairs. Before and after the tightening process, they use a calibration unit to measure the torque. At the final tighten, they check the self-retention of the oval nuts—these must not be too loose or too tight.
“Our goal was to replace the established manual job because the sheer complexity of the tightening process meant that it was becoming increasingly prone to error.”
Initiator and idea provider of the project
So this is a job that requires mechanics to have a very delicate touch. But in the future, at least at MTU Maintenance in Hannover, it will be performed by a robot. In addition to automating the process of screwing the rotor components together, this new method also uses the robot to digitally document everything at the same time. The robot’s first assignment will be the high-pressure compressor rotor for the V2500 two-shaft turbofan engine, which powers the Airbus A320 series, among others.
“Our goal was to replace the established manual job because the sheer complexity of the tightening process meant that it was becoming increasingly prone to error,” says Nico Vohse, who had the idea for the project and launched it. The project team set out to find an optimum, forward-thinking solution.
But instead of simply replacing one manual process with another, MTU decided to switch to an automated process based on industrial robots. This promises to be a sound investment in the future: as this new solution offers significantly greater precision and can be adapted to other models of rotor, other MTU sites also stand to benefit in the medium term.
Arduous and unergonomic manual labor eliminated
Together with 3D.aero—an automation solutions provider specializing in solving problems particular to the aviation industry—the Hannover team developed a solution that combines many of the benefits of digitalization and Industry 4.0. It also happens to make life much easier for the employees who have to get the job done.
It was advantageous that among the project team comprised several employees who had performed the task manually many times before, which meant they were very familiar with the hand movements and the obstacles involved. “In the past, mechanics would work in a less than ergonomic position bent over the rotor, ultimately using a mirror and a light to check whether the nuts were in the correct position,” says Ingo Scheele, the member of the project team responsible for first level support.
“So when we switched to the robotic solution, we took the opportunity to eliminate these unergonomic processes while also introducing a camera system to help chart and document the tightening process,” Vohse says. Now, the camera system moves inside the rotor and documents whether everything there is up to scratch and if the nuts have been tightened correctly. The image data collected is then filed for future reference. This system’s added bonus is that the whole process can now be monitored remotely.
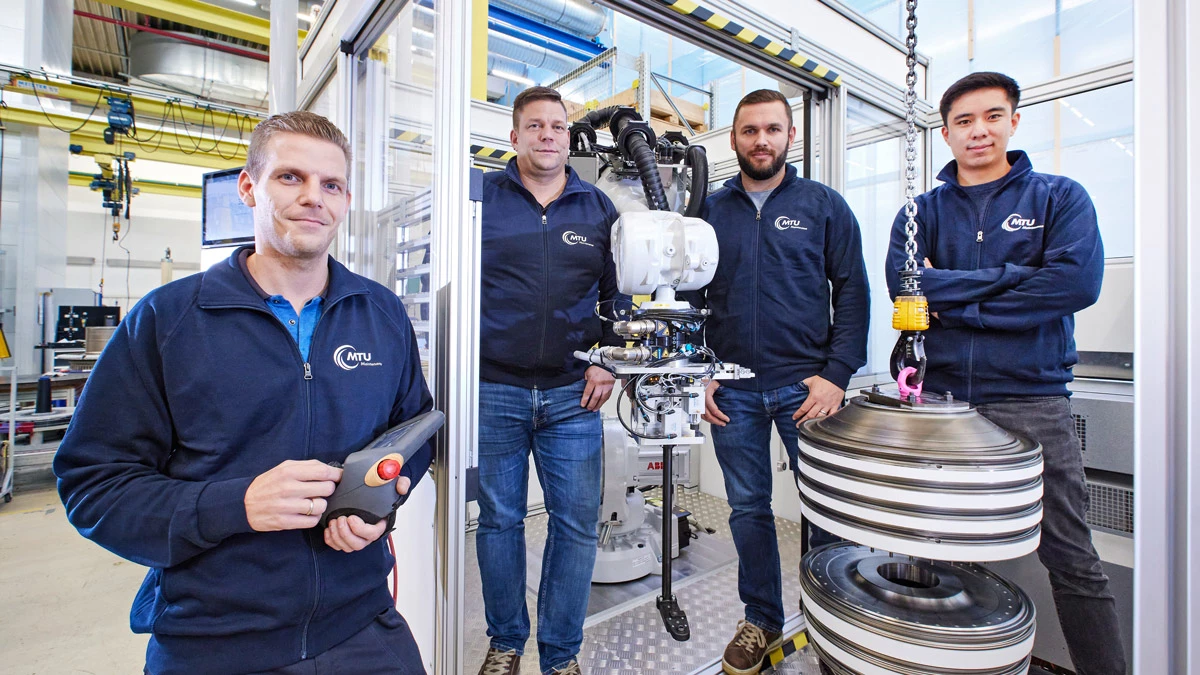
The team: Sebastian Lorenz, Oliver Persuhn, Nico Vohse and William Xu (left to right).
“Instead, what we’ve achieved with the tightening robot is a stable, qualitatively better process and a workflow that enables us to reduce both the likelihood of errors and the failure rate. After all, it’s in a robot’s nature to perform the task more precisely and with less effort than a human.”
Initiator and idea provider of the project
Precise engine assembly with a low error tolerance
The process steps and sequence have, however, remained largely the same compared to the previous version: the first seating of the nuts and washers, tightening in opposite pairs, the second seating followed by self-retention check, and then the final torque. Now, though, the selection of the nuts and washers and their placement in the workpiece are fully automated, performed by a pneumatic grab arm via a grip-change station. Before and after the completed tightening process, a calibration unit is used to check that the torque on the mechanical components complies with the engine manufacturer’s stringent specifications. A twin magazine system reduces unutilized assembly times: while the tightening process is taking place in one chamber, the setup for the next order is being prepared in the other.
Even with the new solution, it still takes around two hours to screw together a compressor rotor. But Vohse notes that a few minutes here or there would be of little consequence given how long it takes to assemble an entire engine. What’s more important, he says, is to have a low error tolerance and a reliable, plannable process—which is why shaving a couple of minutes off the process time was never a high priority. “Instead, what we’ve achieved with the tightening robot is a stable, qualitatively better process and a workflow that enables us to reduce both the likelihood of errors and the failure rate. After all, it’s in a robot’s nature to perform the task more precisely and with less effort than a human.”
Flexibly adaptable to other compressor rotors
The solution achieved in collaboration with 3D.aero is highly customized—there was no real blueprint to follow or any similar process. “This is MTU’s first automated tightening robot in the field of assembly and disassembly to support such a specific maintenance area. But it won’t remain the only application we could imagine for this technology,” says Oliver Persuhn, who, together with Vohse, has been a part of developing the system from day one and is transferring it to standard operations.
“At the end of the day our greatest achievement with the tightening robot is that we’ve brought industrial systems and IT closer together and torn down some big barriers in everything from incorporating IT to helping realize MTU’s Industry 4.0 strategy.”
Project team member
Persuhn explains that MTU is striving to replicate the system’s more precise tightening and the improved time planning in maintenance processes for larger rotor series. “The current system variant can accommodate rotors with a diameter of up to 1.10 meters. And since the robot is equipped with quick-lock couplings, we can change out the tightening tool relatively easily and inexpensively.” What’s more, the technology provides an ideal basis for an automated measuring and assembly system for larger rotors and other automation projects.
“At the end of the day,” says project team member William Xu, “our greatest achievement with the tightening robot is that we’ve brought industrial systems and IT closer together and torn down some big barriers in everything from incorporating IT to helping realize MTU’s Industry 4.0 strategy.” He adds that it’s now easier to integrate process data into the MTU ecosystem and to gather additional empirical data with a view to rolling out this lighthouse project at other sites further down the line.