innovation
Wie der Roboter beim Verschrauben von Verdichterrotoren unterstützt
Einen über Jahre gewachsenen Prozess bei der Instandhaltung und Reparatur von Verdichterrotoren zu digitalisieren, bringt ein Mehr an Prozesssicherheit und reduziert die Ausfallrate.
Autor: Tobias Weidemann | 5 Min. Lesezeit veröffentlicht am: 10.01.2023
Autor:
Tobias Weidemann
ist seit mehr als 20 Jahren als Journalist und Content-Berater tätig. Er berichtet über Technik- und Wirtschaftsthemen, oft mit Schwerpunkt auf Business-IT, Digitalisierung und Zukunftstechnologien.
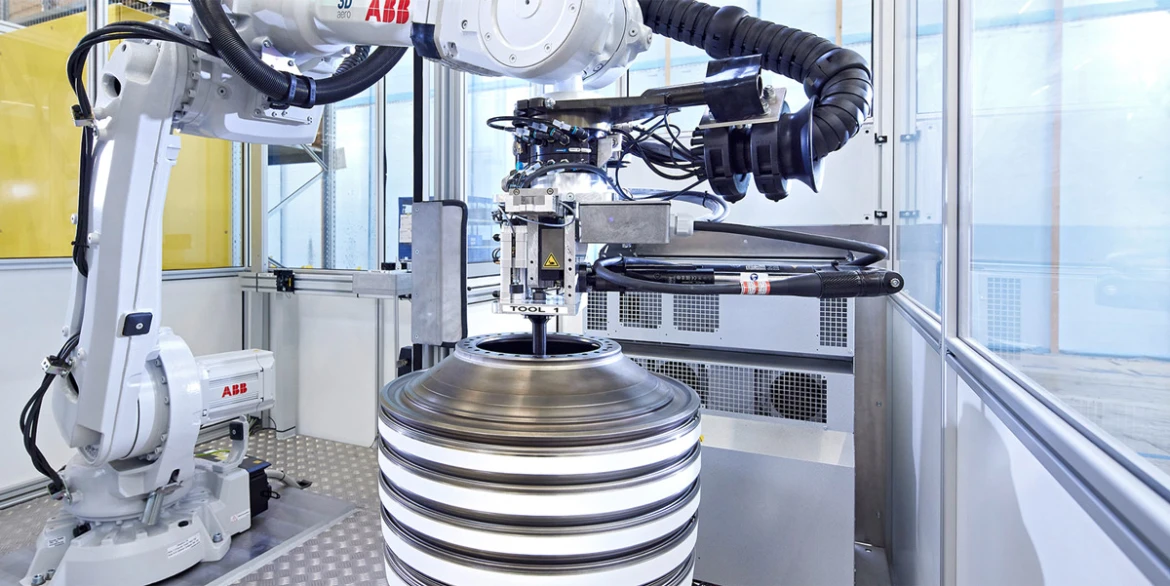
Das Verschrauben eines Verdichterrotors ist eine Arbeit, die viel Geduld erfordert. Eine Aufgabe, bei der nichts überstürzt werden darf und bei der es auf eine ruhige Hand ankommt. Es werden zunächst die beiden Drums positioniert, 34 Muttern und die dazugehörigen Unterlegscheiben nach und nach an die richtige Stelle gebracht. Dann erst leicht eingeschraubt und kontinuierlich mit dem korrekten Drehmoment in mehreren Runden festgezogen. Immer nacheinander über Kreuz, um nichts zu verziehen. Vor und nach dem Verschraubungsprozess wird das Drehmoment durch die Kalibriereinheit gegengemessen. Beim finalen Festziehen wird zudem die Selbsthemmung der ovalen Muttern überprüft – diese dürfen weder zu fest noch zu locker angezogen sein.
„Ziel war es dabei, ein bestehendes manuelles Verfahren, das aufgrund des komplexen Anzugsvorgehens bei der Verschraubung zunehmend fehleranfällig war, zu ersetzen.“
Initiator und Ideengeber des Projekts
Ein Job, bei dem es auf das Fingerspitzengefühl der Mechaniker:innen ankommt – und den in Zukunft zumindest bei der MTU Maintenance in Hannover ein Roboter übernimmt. Mit dem neuen Verfahren lässt sich nicht nur die Verschraubung der Rotoren automatisieren, sondern auch gleich alles digital dokumentieren. Zum Einsatz kommt der Roboter zunächst beim Hochdruckverdichter des V2500-Triebwerks, einem Rotor für ein Zweiwellen-Zweistromtriebwerk, das unter anderem in den Airbus Modellen der A320-Serie zum Einsatz kommt.
„Ziel war es dabei, ein bestehendes manuelles Verfahren, das aufgrund des komplexen Anzugsvorgehens bei der Verschraubung zunehmend fehleranfällig war, zu ersetzen“, erklärt Nico Vohse, der Initiator und Ideengeber des Projekts. Das Projektteam suchte dabei nach einer optimalen, zukunftsweisenden Lösung.
Doch anstatt die manuelle Lösung einfach zu ersetzen, entschied sich die MTU für ein Robotik-Verfahren auf Basis eines Industrieroboters. Eine gute Zukunftsinvestition, denn weil die neue Lösung deutlich mehr Präzision verspricht und anpassbar an andere Rotormodelle ist, könnten davon mittelfristig auch andere MTU-Standorte profitieren.
Anstrengende und unergonomische Handarbeit eliminiert
Zusammen mit 3D.aero, einem auf Problemstellungen der Luftfahrtindustrie spezialisierten Anbieter von industriellen Automatisierungslösungen, hat das Team aus Hannover eine Lösung entwickelt, die zahlreiche Vorteile im Hinblick auf Digitalisierung und Industrie 4.0 in sich vereinigt und ganz nebenbei auch für die betreuenden Mitarbeiter:innen weniger anstrengend in der Handhabung ist.
Als Vorteil erwies es sich dabei auch, dass an dem Projekt mehrere Mitarbeiter beteiligt waren, die die manuelle Rotorverschraubung in der Vergangenheit häufiger durchzuführen hatten und somit die Handgriffe und damit verbundenen Hürden genau kannten. „Der Mechaniker hat früher gebückt und wenig ergonomisch über dem Rotor gestanden und darin gearbeitet, am Schluss mit einem Spiegel und einer Lichtquelle den Sitz der Muttern kontrolliert“, berichtet etwa Ingo Scheele, der als Mitglied des Projektteams für den First Level Support zuständig ist.
„Die Umstellung auf die Robotik-Lösung haben wir daher gleich dazu genutzt, diese wenig ergonomischen Prozesse zu eliminieren und die Möglichkeit für eine vernünftige Dokumentation und Protokollierung der Verschraubung mit Hilfe eines Kamerasystems eingeplant“, erklärt Vohse. Die Anlage fährt jetzt mit einer Kamera in den Rotor und dokumentiert, ob in der Innensicht des Rotors alles in Ordnung ist und alles korrekt verschraubt wurde. Die entsprechenden Bilddaten werden zudem zur Dokumentation archiviert. Quasi als „Beifang“ kann der Prozess damit auch von Remote überwacht werden.
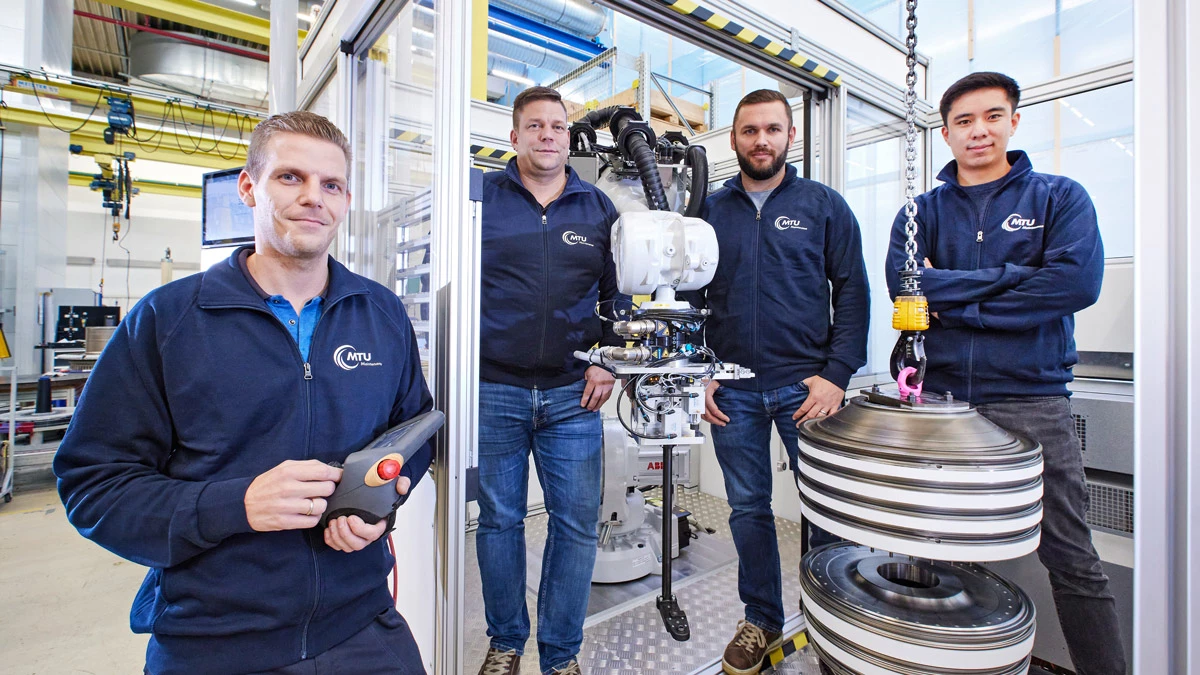
Das Team: Sebastian Lorenz, Oliver Persuhn, Nico Vohse, William Xu (von links nach rechts).
„Realisiert haben wir mit dem Schraubroboter eher einen stabileren und qualitativ hochwertigeren Prozess und einen Workflow, der einhergeht mit einer Reduzierung der Ausfallrate und der Fehleranfälligkeit. Denn all das kann ein Roboter naturgemäß präziser und mit weniger Anstrengung leisten als der Mensch.“
Initiator und Ideengeber des Projekts
Präzise Triebwerksmontage mit niedriger Fehlertoleranz
Am Prozess selbst und den Arbeitsschritten, die nacheinander zu erfolgen haben, hat sich dagegen verglichen mit der früheren Variante gar nicht viel verändert – Ansetzen der Muttern mit Scheiben und erster Überkreuzanzug, zweiter Anzug und anschließend das Überprüfen der Hemmung der Mutter – schließlich der finale Anzug. Doch jetzt erfolgt das Greifen und Einlegen von Mutter und Unterlegscheibe in die Abtriebseinheiten vollautomatisch per pneumatischem Greifer und über eine Umgreifstation. Vor und nach dem kompletten Verschraubungsprozess wird das Drehmoment über die mechanischen Bauteile mit Hilfe einer Kalibriereinheit überprüft – streng gemäß der Vorgabe des Triebwerkherstellers. Zur Reduzierung von unproduktiven Rüstzeiten sorgt ein aus zwei Magazinen bestehendes System dafür, dass in der einen Kammer der Verschraubungsprozess ablaufen kann, während in der zweiten bereits für den nächsten Auftrag neu gerüstet wird.
Selbst mit der neuen Lösung dauert die Verschraubung eines Verdichterrotors rund zwei Stunden, wobei aber, so betont Vohse, einige Minuten mehr oder weniger angesichts der Dauer einer Triebwerksmontage nur wenig ins Gewicht fallen würden. Wichtiger sei die niedrige Fehlertoleranz und der zuverlässig planbare Ablauf, weshalb es gar nicht in erster Linie darum gegangen sei, den Verschraubungsprozess ein paar Minuten schneller zu gestalten. „Realisiert haben wir mit dem Schraubroboter eher einen stabileren und qualitativ hochwertigeren Prozess und einen Workflow, der einhergeht mit einer Reduzierung der Ausfallrate und der Fehleranfälligkeit. Denn all das kann ein Roboter naturgemäß präziser und mit weniger Anstrengung leisten als der Mensch.“
Flexibel anpassbar für andere Verdichterrotoren
Zusammen mit 3D.aero wurde hier eine sehr individuelle Lösung geschaffen, für die es auch noch keine Blaupause oder keinen vergleichbaren Prozess gab. „Im Montage- und Demontagebereich ist das der erste automatische Verschraubungsroboter im MTU-Umfeld, der speziell ein solches Instandhaltungsthema unterstützt. Umgekehrt wird das aber auch bei uns nicht die einzige Anwendung bleiben, für die wir uns das vorstellen können“, ist sich Oliver Persuhn sicher, der die Anlage von Beginn an mit Nico Vohse entwickelte und in den Regulärbetrieb überführt.
„Unterm Strich haben wir mit dem Verschraubungsroboter auch Industrieanlage und IT näher zusammen gebracht und einige wichtige Hürden im Rahmen der IT-Einbindung hin zur von der MTU angestrebten Industrie-4.0-Strategie genommen.“
Projektmitarbeiter
Er erklärt, dass die so mögliche präzisere Verschraubung und die verbesserte zeitliche Planbarkeit auch für die Wartungsprozesse größerer Rotorserien angestrebt wird. „In der aktuellen Anlagenvariante lassen sich Rotoren bis 1,10 Meter Durchmesser einbringen – und da die Robotik mit Schnellkupplungen versehen ist, können wir die Verschraubungswerkzeuge relativ einfach und preiswert wechseln.“ Darüber hinaus stelle die Technik eine ideale Basis für eine automatische Mess- und Montageanlage für größere Rotoren und für weitere Automatisierungsprojekte dar.
„Unterm Strich“, betont Projektmitarbeiter William Xu, „haben wir mit dem Verschraubungsroboter aber vor allem auch Industrieanlage und IT näher zusammen gebracht und einige wichtige Hürden im Rahmen der IT-Einbindung hin zur von der MTU angestrebten Industrie-4.0-Strategie genommen.“ Man könne jetzt Prozessdaten besser innerhalb des MTU-Ökosystems einbinden und sammele weitere Erfahrungswerte, um das Leuchtturmprojekt später auch an anderen Standorten auszurollen.