innovation
MTU opens new high-tech test center for en gine parts
MTU is known the world over for its unique testing and inspection expertise—and is setting new standards with its state-of-the-art component test center.
author: Nicole Geffert | 4 mins reading time published on: 01.02.2020
author:
Nicole Geffert
has been working as a freelance journalist covering topics such as research and science, money and taxes, and education and careers since 1999.
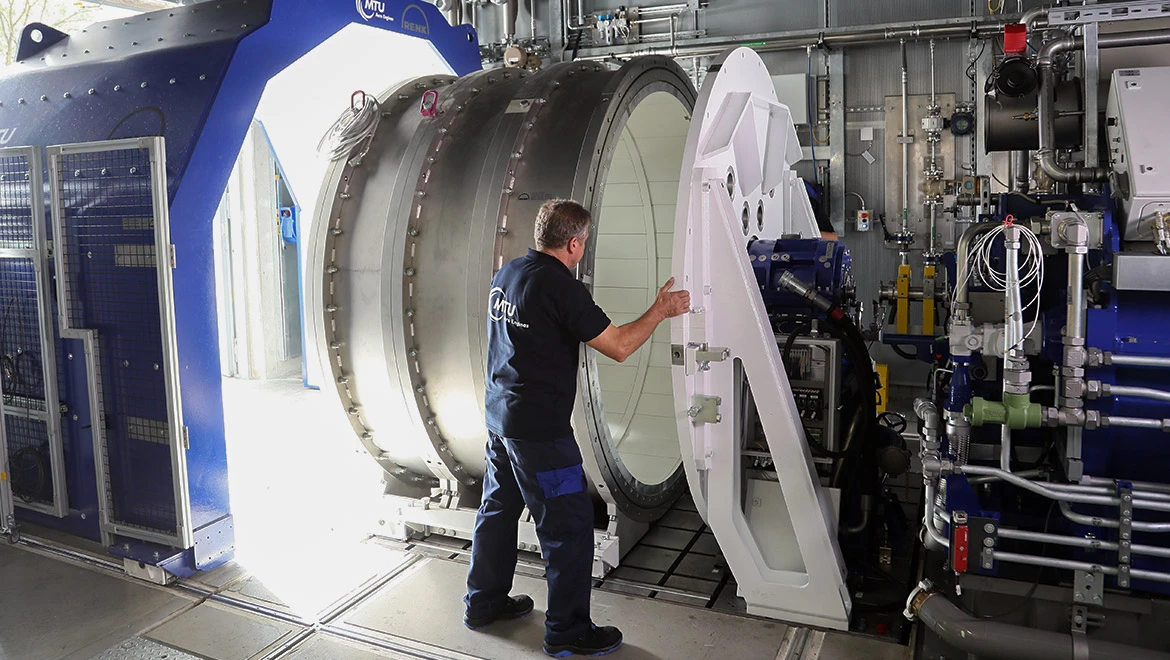
At first glance, the sober architecture of new building G200 at the MTU Aero Engines Munich site doesn’t give much away about what’s inside. In fact, the building’s interior hums with state-of-the-art and highly sophisticated technology. G200 is MTU’s new test center for engine parts. One of the people who works there is Dr. Christian Eichler, Senior Manager Component Testing Rotation, Structures and Devices. “We’re thrilled about our new testing facilities and the extended capabilities they offer,” he says.
The new center is a key component of MTU’s testing expertise, which covers development tests, certification tests and production acceptance tests. “Our scope of testing is diverse, covering everything from material tests on small standard samples to testing modules and complete engines,” Eichler says. “The new component testing center is the perfect addition to our range of activities.”
MTU has invested more than 25 million euros to expand its testing capabilities and offer its internal and external customers the highest degree of reliability and quality. “In aviation, safety is the top priority, which is why we have to furnish proof that our products meet the highest safety standards—right down to the detail part level,” Eichler says.
In the new shop, which is built from 1,000 metric tons of reinforced concrete, MTU’s experts will test, for example, the individual parts that make up compressors and turbines, including engine airfoils and shafts, compressor blisks, disks, casings, rings and tubing, plus small assemblies such as bladed turbine disks.
Eichler and his team are particularly proud of one new machine in the test center: a multifunctional rotation test stand that offers an unparalleled application range and performance. It has been set up in a separate, twin-wall reinforced concrete enclosure on a sprung foundation weighing 90 metric tons.
“Test specifications increasingly call for aeroelastic tests in addition to standard mechanical tests,” explains Dr. Jörg Henne, Senior Vice President, Engineering and Technology at MTU. “Previously, it took a huge amount of time and effort to test, say, the interaction between air flow and rotating components. But our new multifunction rotation test stand provides a bespoke environment for this task.”
The team can use the machine to test components at ambient conditions but also in a vacuum chamber. And the test stand’s sophisticated automation system is perfect for overnight or endurance testing. “Our new rotation test stand enables us to conduct a whole range of different tests for our current engine programs, but also offers the resources and capacities that will be required for future applications,” explains Dr. Jörg Eßlinger, who heads Materials Engineering at MTU.
A Tyne rotor is rigged up to the vertical test stand. MTU’s specialists conduct a total of 65 different types of tests in the new test center for engine parts.
A number of other test systems can also be found hard at work in building G200, including vertical-axis spin test benches that were relocated from another part of the site and various smaller testing machines. MTU’s experts conduct 65 different types of tests in the new shop, such as spin tests, air flow measurements, structural tests and tests for vibration, wear, ballistics and fatigue.
Anyone who has ever moved house knows how much effort was involved. For MTU, this effort has paid off. After all, pooling all its component testing systems in shop G200 saves time and increases efficiency. “We’ve also installed innovative rigging technology that allows us to rig up another area for testing the next part while we’re running a test on the multifunctional rotation test stand,” Eichler says. Depending on the complexity of the setup, this can save weeks, he explains.
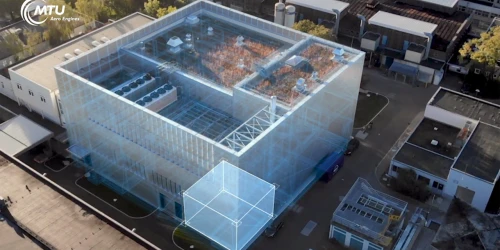
MTU test center opens its doors
MTU opens its doors and provides insights into the high-tech test center for engine components. A total of 25 million euros were invested in the hall, which is now located in Munich. To the video
MTU has a wide range of tasks to manage on its test stands as it ramps up numerous new engine programs and performs contract work for industrial customers. Against this backdrop, shorter turnaround times are an import success factor when it comes to ensuring that internal and external orders, many of which present complex problems, are delivered on time and in the highest quality.
And it goes without saying that all the equipment in the new test center must also run without a glitch when workloads are this high. To this end, highly advanced and sophisticated systems supply water, electricity, technical gases, cooling air and hot air to the systems and dissipate the heat generated by the test stands. All the equipment meets the strictest environmental protection standards.
The test center was built with the future in mind. Besides catering to the testing requirements for all of MTU’s current engine programs, shop G200 has also been designed for the engines of tomorrow. It can be expanded to accommodate them—not only in terms of space, but also in terms of new technologies for the time when innovative materials, construction methods and larger structures, such as parts for future engines onboard long-haul aircraft, need to be put to the test.
According to Henne, future engines such as the ones to power second-generation geared turbofans will have to satisfy even tougher requirements than those of today. “Our ultimate goal is emissions-free flight, and MTU is already systematically driving the development of innovative green propulsion technologies and enhancing them,” he says. Thanks to its powerful test facilities, MTU is ideally equipped to do this—for both its development and its maintenance business.