innovation
How engine certification and validation works
Certifying and validating an engine is a rigorous process that takes years. It concerns flight safety as well as energy consumption and maintenance intervals.
author: Tobias Weidemann | 7 mins reading time published on: 09.01.2024
author:
Tobias Weidemann
has been working as a journalist and content consultant for more than 20 years. He writes about technology and business topics, often with a focus on business IT, digitalization and future technologies.
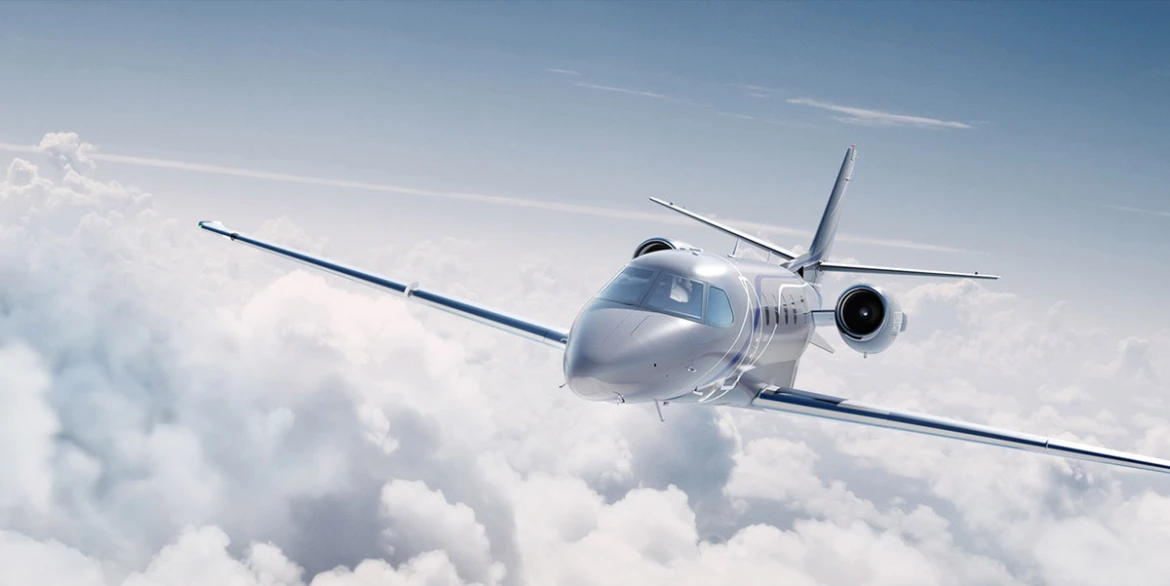
©Textron Aviation
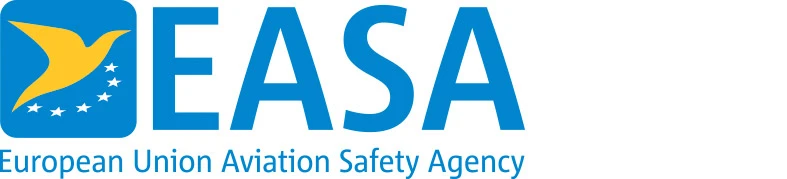
EASA (European Union Aviation Safety Agency): EASA is the European Union's safety authority for civil aviation. Its headquarters are in Cologne, Germany.
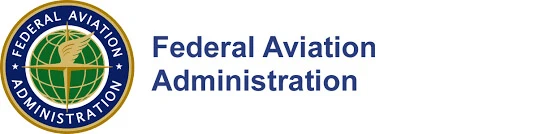
FAA (Federal Aviation Administration): The FAA is the United States Federal Aviation Administration. It is headquartered in Washington, D.C.
It should come as no surprise that the aviation industry has the highest safety standards. The aircraft as well as the engines and their individual components undergo rigorous testing and inspection. Nothing’s left to chance. But what exactly happens before an engine gets the green light?
If you listen to Dr. Stefan Gehring, who is in charge of type approval at MTU Aero Engines, it quickly becomes clear that this is a challenging process involving both certification through an aviation authority and validation of additional requirements. “Here, we differentiate between certification and qualification. Certification through the authority concerns only safety and airworthiness; it’s a flight-safety-related proof of functionality.” It serves to ensure that an engine never jeopardizes flight safety in any situation or environment throughout its lifecycle; for instance, when it comes to taking off safely under snowy or icy conditions. In addition to the independent assessment of the design itself, an extensive test program is carried out that includes demanding endurance runs, the sucking-in of foreign bodies, and operation at high temperatures or when icing occurs. After the first certification, the engine can go into operation. Subsequent enhancements and repair methods are developed based on the experience gained from operation and have to be approved for use as well.
“For us as the manufacturer and for our customers, the safety of MTU products is a top priority. But we also look at efficiency, energy consumption, maintenance intervals, and numerous technical measurements,” Gehring says. Naturally, MTU strives to use less fuel and energy and therefore produce fewer emissions to make flight operations as efficient as possible. That’s why the validation program encompasses a wide range of engine tests in coordination with technical departments and collaboration partners so as to learn as much as possible.
PW500
MTU has held a 25 percent stake in the PW500 since 1993. The PW545D engines use new materials and technologies to improve fuel efficiency, increase thrust and extend time on wing.
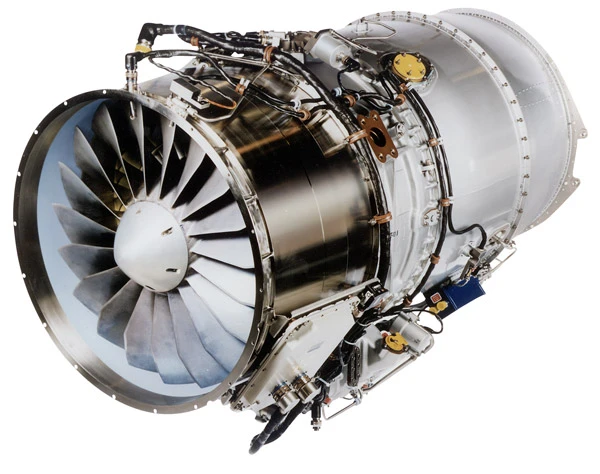
Max. thrust (Start): 4,500 lb
Bypass ratio: 4.1:1
Pressure ratio: 15.5:1
Length: 67 in
Fan diameter: 27 in
Weight: 824 lbs
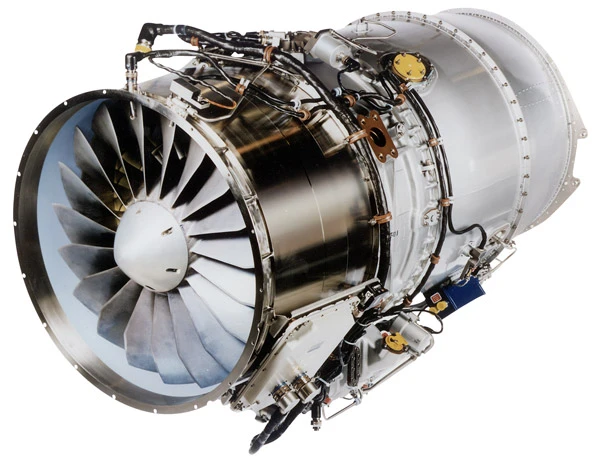
A modified engine with a number of tried-and-true components
All of this sounds theoretical at first, which is why MTU validation engineer Philipp Kreppenhofer explains the process using the PW545D as an example. This is an engine MTU is collaborating on with Pratt & Whitney Canada for the Cessna Citation Ascend. In this particular case, Pratt & Whitney Canada is in charge as Textron Aviation’s engine manufacturer and contractor. Since Pratt & Whitney Canada is located near Montreal, the certification for approval is done by Transport Canada (TCCA), the department within the Government of Canada responsible for aviation safety, among other things. Usually, this certification is then adopted by the U.S. Federal Aviation Administration (FAA) and the European Union Aviation Safety Agency (EASA) due to bilateral agreements. MTU in turn supports Pratt & Whitney in advance through comprehensive documentation of parts coming from the company.
In contrast to an initial certification, such a type extension requires only a selected engine test program. This gives MTU the opportunity to focus attention specifically on new components and to carry out particularly comprehensive and careful tests for components that have changed significantly. “The parts of the engine that have been used unchanged for years on previous models have already been certified. This applies to a large proportion of the PW545D’s components,” Kreppenhofer says. Because, as the name indicates, this is the D series, the fourth and, to date, most powerful variant of the PW500 series. It consumes less fuel and is more efficient than its predecessors. But although few components have changed completely from the C to the D series, the latter represents much more than just a facelift. “Changes include the turbine case and the mixer,” Kreppenhofer says. “But the low-pressure turbine and the turbine exit case are identical to the C version.”
The Citation Ascend
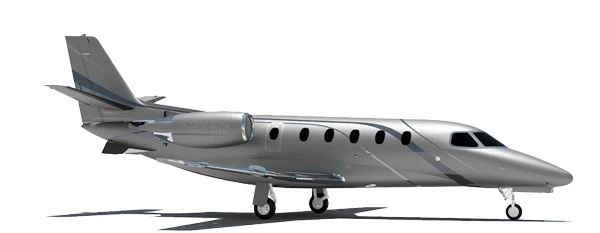
©Textron Aviation
4 Passenger Range: 1,900 nm / 3,519 km
Maximum Cruise Speed: 441 ktas / 817 km/h
Maximum Passengers: 12
Full Fuel Payload: 850 lb / 386 kg
Takeoff Field Length: 3,660 ft / 1,116 m
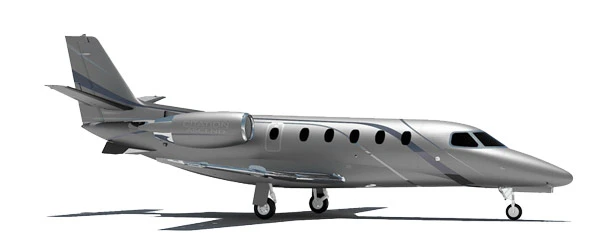
©Textron Aviation
An extensive process even for modifications
Although the new Cessna business jet is set to go into regular operation no earlier than 2025, the development and the certification process began much earlier. At the time of publication, the verification and validation phase has been completed with the first development tests and performance runs. The team, the OEM, and the certification authority have decided which areas to validate and how, as well as what test scenarios can be used to reliably gather the desired data. “For the tests that ran this year, we’d already adapted, instrumented, and delivered the hardware over the course of last year to ensure that everything’s there on time,” Kreppenhofer says.
The actual certification test—the certification endurance test, or “block test”—took place at the beginning of this year. “The block test, which is always mandatory, is an endurance run that provides a lot of relevant data on the engine’s service life, in particular regarding its hot section, as well as on its behavior in typical operating situations, including under extreme conditions,” Kreppenhofer explains. This test simulates numerous takeoffs and landings and alternately starts the engine up and shuts it down to simulate, as best as possible and in a very short time, the engine’s consumption throughout its entire service life, especially in the hot section. The goal here is to gain the quickest possible overview of the engine’s mechanical state up to its first scheduled overhaul and to demonstrate its flight safety. The test thus allows for inferences about part behavior across a wide range of loads, such as vibration excitations due to different rotor speeds, as well as about its mechanical integrity up to the first scheduled repair.
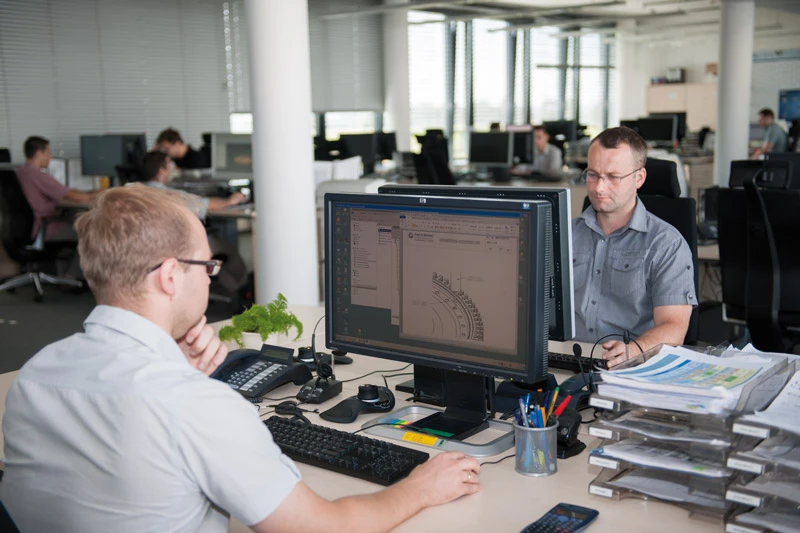
Simulations: In the future, MTU plans to use a full computer simulation known as a digital twin to test certain issues across the engine’s entire lifecycle.
A secondary air system (SAS) test was also carried out to check the engine’s air system. “This can sometimes reveal the extent to which the real pressures and temperatures measured in the test match MTU’s analytical models. Verifying the computational models is an important step in product development,” Kreppenhofer says. Such tests lend themselves particularly well to collecting and evaluating large amounts of thermal data. These nondestructive test scenarios allow engineers to assess very accurately if individual components could get damaged or cause problems and are thus unfit for standard operations.
“After the validation and certification runs, we take a detailed look at the hardware to find out if it shows the expected wear and tear or anomalies or whether it needs optimizing,” Kreppenhofer explains. MTU then thoroughly assesses the data and analyzes the lab results. The technical departments issue certification reports for Pratt & Whitney based on the data and results gathered. Pratt & Whitney Canada collates all relevant data to undergo certification by the TCCA certification authority, followed by the FAA and EASA.
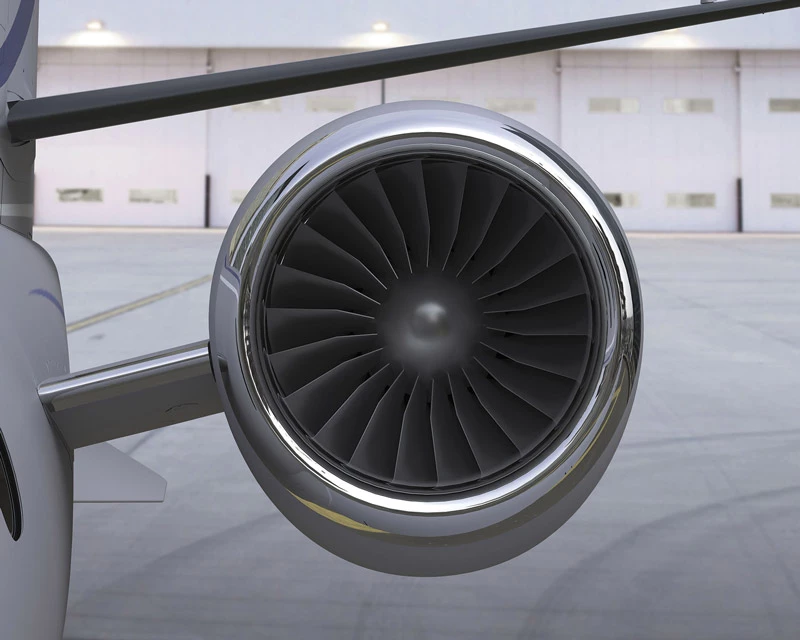
©Textron Aviation
New business jet: The Citation Ascend is designed to bring an all-new cockpit, improved performance and a more luxurious cabin to the midsize business jet market. It will be powered by Pratt & Whitney Canada PW545D engines.
Full engine test on-site yields important findings
The components are developed at the Munich site and at MTU Aero Engines Polska in Rzeszów. Many engineers are located in Rzeszów, where they are driving forward the further development of the PW545D, for example in project management and analytics. Conversely, many of the departments responsible for providing the development hardware are located in Munich, where the procurement, manufacturing, and instrumentation of the development-specific hardware (casings and mixers) took place. The engine was assembled and fully tested by Pratt & Whitney in Canada. As was the case with the PW545C, the rotor and stator parts supplied by MTU Aero Engines Polska are assembled later in production, while accessories such as the exit cases and mixers are provided in individual parts. The components that hadn’t changed from the PW545C standard and were used for the development tests came from MTU Aero Engines Polska’s existing standard production.
While this may sound like a lot of effort, there is no alternative when it comes to ensuring safety: “A full engine test yields important findings for the technical departments involved and will therefore remain important for us in its entirety. Certifying only the individual parts in Germany wouldn’t provide all the relevant data; it would not satisfy the requirements for the overall engine,” Gehring explains.
Yet, simulations are already being used as far as possible. In the future, MTU plans to use a full computer simulation known as a digital twin to test certain issues across the engine’s entire lifecycle. With the help of increasing computing power, it will be possible to map more and more test scenarios and thus accelerate and simplify development immensely. Simulations will also be able to calculate a large number of variants much faster, enabling MTU to further optimize engines specifically for different application scenarios.