innovation
Innovative assembly system for the PW800
MTU breaks new ground in (dis)assembly for maintaining the PW800 engine.
author: Tobias Weidemann | 6 mins reading time published on: 03.07.2024
author:
Tobias Weidemann
has been working as a journalist and content consultant for more than 20 years. He writes about technology and business topics, often with a focus on business IT, digitalization and future technologies.
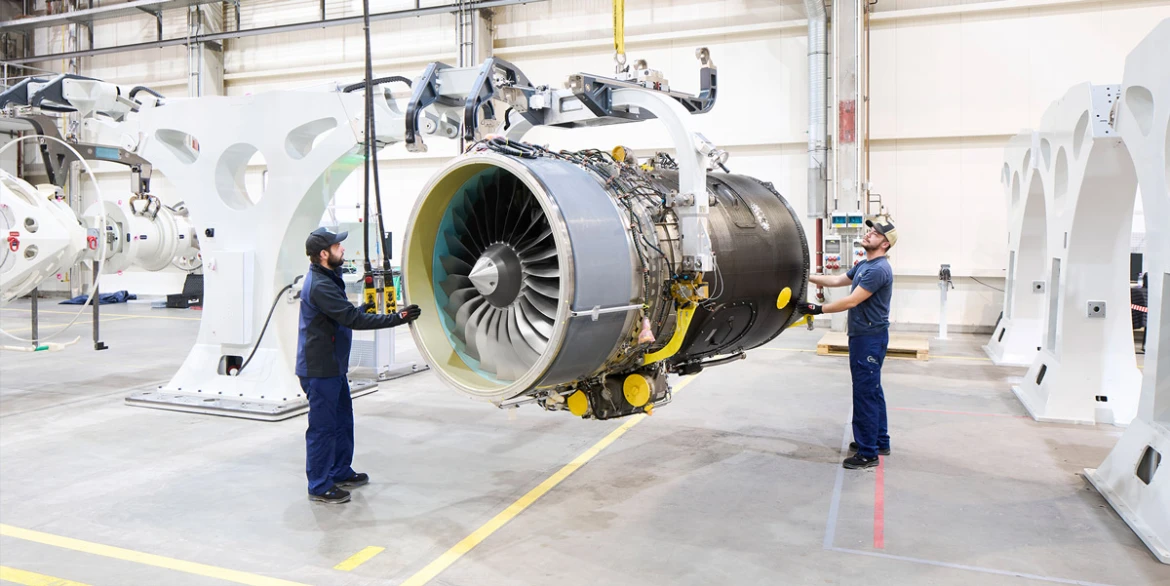
Repairing an aircraft engine is not just a procedure that must be planned right down to the smallest detail. When dismantling, turning, and inspecting the engine to gauge its repair needs, it’s essential not to damage any of its components. This is literally a weighty task: the engine itself weighs several metric tons, while each of its modules weighs several hundred kilograms. To work on these modules, each one must be turned from the horizontal position it occupies in the engine to a vertical position in a way that doesn’t risk any damage.
PW800: Powering long-haul business jets
- The PW800 is part of Pratt & Whitney’s PurePower® family, offering significant improvements in fuel efficiency, emissions, and operating costs.
- It is designed for long-haul business jets, regional aircraft, and narrowbodies.
- MTU contributes to the development and manufacturing of the low-pressure turbine and various stages of the high-pressure compressor.
- Applications include Gulfstream G400, G500, G600, and Dassault Falcon 6X.
There are plenty of shop floor repair concepts, and deciding which one is the right solution depends on the number and extent of potential maintenance steps. Sometimes the engine is positioned on a central dock and worked on there from start to finish; other times it travels from station to station along an assembly line.
MTU was tasked with developing a shop floor repair concept for Pratt & Whitney Canada’s PW814GA and PW815GA engines, which power the Gulfstream G500 and G600 business jets. MTU Maintenance Berlin-Brandenburg has been carrying out repairs on the low-pressure turbine for these propulsion systems for years, but 2024 will see it repairing whole engines for the first time. This work will be performed using a stationary system that is unlike any other in the world—and that’s because there’s something special about this engine series: the PW800 features the same core technology as the Pratt & Whitney GTF™ engine family. Only two locations worldwide repair the PW800, and one is MTU Maintenance Berlin-Brandenburg in Ludwigsfelde.
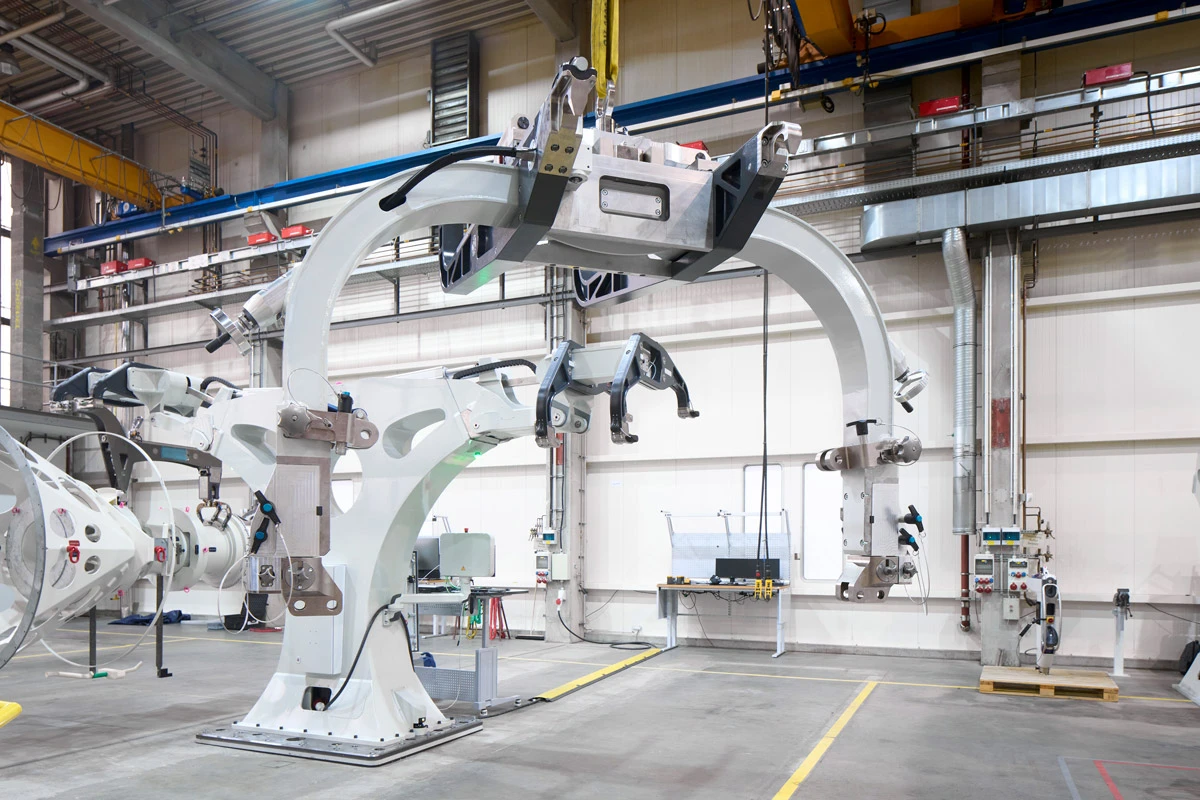
Fixed-Overhaul-System next generation: FOSng features a T-shaped dock that allows two engines to be suspended, one from each arm, and thus worked on simultaneously.
Cross-site collaboration for a custom solution
Known as FOSng, which stands for fixed overhaul system next generation, the chosen assembly and disassembly system is the result of two years of intensive cross-site collaboration between the team at MTU Maintenance Berlin-Brandenburg and their design colleagues at MTU Aero Engines in Munich. MTU decided to build on the existing FOS assembly concept, which was developed several years ago for EME Aero, a joint venture between MTU and Lufthansa Technik, in Jasionka, Poland. The concept is an essential part of maintaining the GTF engine family at that location and is applied in the same way at MTU Maintenance Zhuhai.
“The alternative would have been to procure an assembly bay solution from Pratt & Whitney Canada (P&WC),” reports Dr. Nico Koppold, Head of Process Engineering Operations at MTU in Ludwigsfelde. But the system that the MTU experts examined at P&WC’s location in West Virginia would have taken up roughly twice as much space and been incompatible with the crane system available at the MTU facility.
“We then looked at what’s involved in fully disassembling a PW800 engine and realized that it made more sense to develop a new assembly and disassembly concept,” explains Florian Brummer, Process Engineer for assembly systems at MTU in Munich. As it happens, there was a solution that would allow the engine to be suspended in a central location, freely accessed by the overhead crane, and fully repaired.
A universal interface for good adaptability
FOSng features a T-shaped dock that allows two engines to be suspended, one from each arm, and thus worked on simultaneously. It is designed to bear 5.5 metric tons each side—plenty for two PW800 engines. As FOSng is taller and wider than its predecessor, it can be used to work on larger engines. A positive side effect is the increased space between engine and the FOSng supports, which means work can be carried out ergonomically.
FOSng should also offer greater flexibility: “While previous FOS systems were designed for the GTF engine family, we wanted FOSng to be compatible with a variety of narrowbody engine types. That would make it suitable for several of MTU’s MRO sites, where it could be adapted to meet the needs of the local engine portfolio,” says Stefan Hofner, Assembly Systems Designer at MTU in Munich. The only engine-specific element is the shuttle that connects the engine and FOSng.
This is why FOSng features a universal interface that can accommodate different custom adaptor plates, which as Hofner says is “a mechanically very simple yet low-maintenance and highly robust solution.” With the plate in place, the crane can follow the shuttle principle that proved so successful with the first FOS generation. The transport vehicle brings the engine into the maintenance shop and positions it beneath the overhead crane. Then the crane, which has already been equipped with the adapter shuttle that corresponds to the given engine casing, gently lifts the 1.5-meter-tall engine off the vehicle and hangs it on one of the FOSng supports. The engines suspended on each side can be moved up and down independently of one another so that the mechanics can always work on the engines in an ergonomic position. The system lets them maneuver each engine into the desired working height as well as angle.
The FOSng System
- Development: Two years of intensive collaboration between MTU Maintenance Berlin-Brandenburg and MTU Aero Engines.
- Design: T-shaped dock allowing simultaneous handling of two engines.
- Capacity: Designed for weights up to 5.5 tons per side.
- Smartlifter: Intelligent crane hook lifting and rotating loads up to 750 kilograms.
Advantages:
- Reduced setup time to half an hour.
- Adaptable to different engine types and MRO locations.
- Optimal working conditions for mechanics through adjustable heights.
Smart lifter as a fitting addition to the system
Attached to the crane is a core component for intelligent working: a smart lifter. This “intelligent crane hook” docks with individual engine modules and can lift and rotate loads of up to 750 kilograms. “This smart lifter can be specifically adapted to any fixture on any engine variant. It automatically recognizes which tooling equipment is currently attached and thus which module is hanging on the hook,” Hofner explains.
As soon as the smart lifter is connected to the fixture, it adopts the appropriate settings and positions the crane hook based on the given program. In addition, sensors measure the weight and center of gravity of empty as well as loaded fixtures. “Our top priorities are to provide our mechanics with optimum support during the assembly and disassembly process, avoid errors, prevent the engine from being put under undue strain, and ensure that none of the components gets damaged,” Koppold explains. “For us, the smart lifter is a fitting addition to all the other tools that allow us to complete the assembly and disassembly process without error and as quickly and efficiently as possible.”
FOSng as a blueprint for other MTU sites
By the end of 2023, the FOSng system had completed its test phase and was installed in Ludwigsfelde, where it was gradually taken into operation using a training engine. At the same time, teams of inspectors, assembly mechanics, and certifiers completed the necessary training at Pratt & Whitney Engine Services in Savannah, Georgia, and Dallas, Texas, before going to work on PW800 engines at the company’s location in Bridgeport, West Virginia. These professionals are familiar with every single component as well as the correct sequences for assembly and disassembly. They also possess in-depth knowledge of the features particular to this engine and the corresponding maintenance processes. “Simplifying the handling and height-adjustment processes means we can shave our preparation time to just half an hour,” Koppold says.
MTU’s Ludwigsfelde site is already planning to add a second FOSng. In total, MTU currently has 18 active FOS systems and more are in the pipeline. Through this new innovative maintenance solution, MTU has also acquired a wealth of expertise that it can apply in other areas and adapt to the given requirements.
So it’s clear that FOSng also serves as a blueprint for other MRO locations and stands as a success story built on in-house knowledge management between MTU’s maintenance and operating resources design teams.
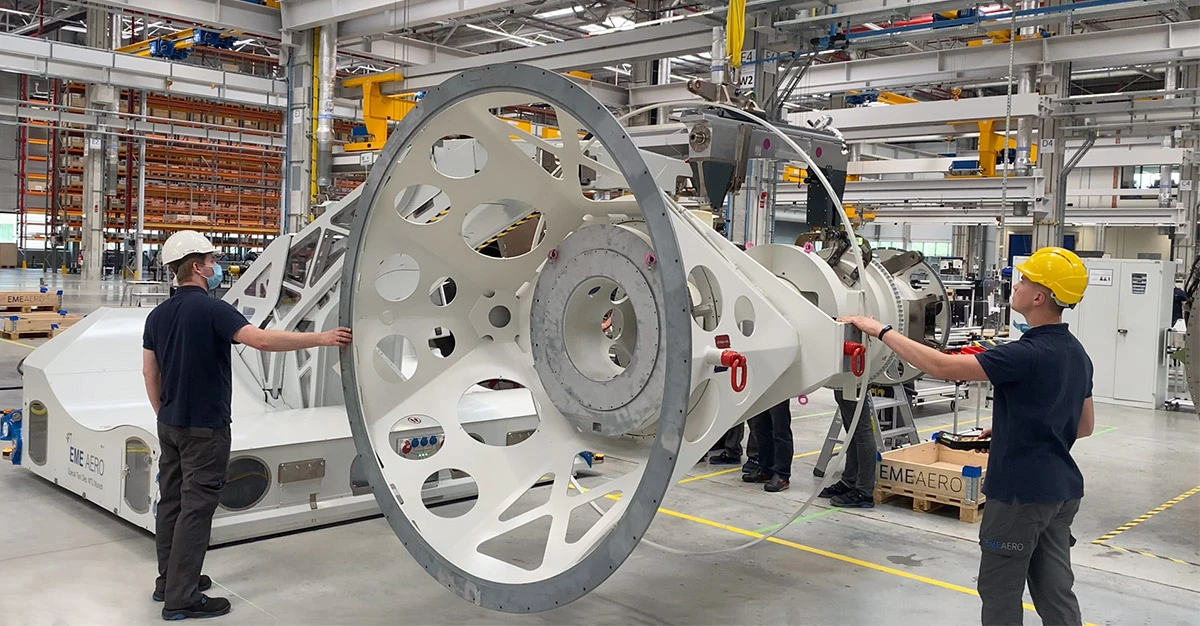
High-tech assembly concept: In record time, MTU specialists developed an assembly concept for maintaining geared turbofan engines in EME Aero’s MRO shop.