innovation
ScanExpress: So werden Defekte an Triebwerksteilen in 3D gescannt
Ein neues 3D-Messsystem kann Schäden an Triebwerksbauteilen ab einer Tiefe von 20 μm dreidimensional erfassen. Die Technik könnte bald MTU-weit zum Einsatz kommen.
Autor: Tobias Weidemann | 4 Min. Lesezeit veröffentlicht am: 06.12.2024
Autor:
Tobias Weidemann
ist seit mehr als 20 Jahren als Journalist und Content-Berater tätig. Er berichtet über Technik- und Wirtschaftsthemen, oft mit Schwerpunkt auf Business-IT, Digitalisierung und Zukunftstechnologien.
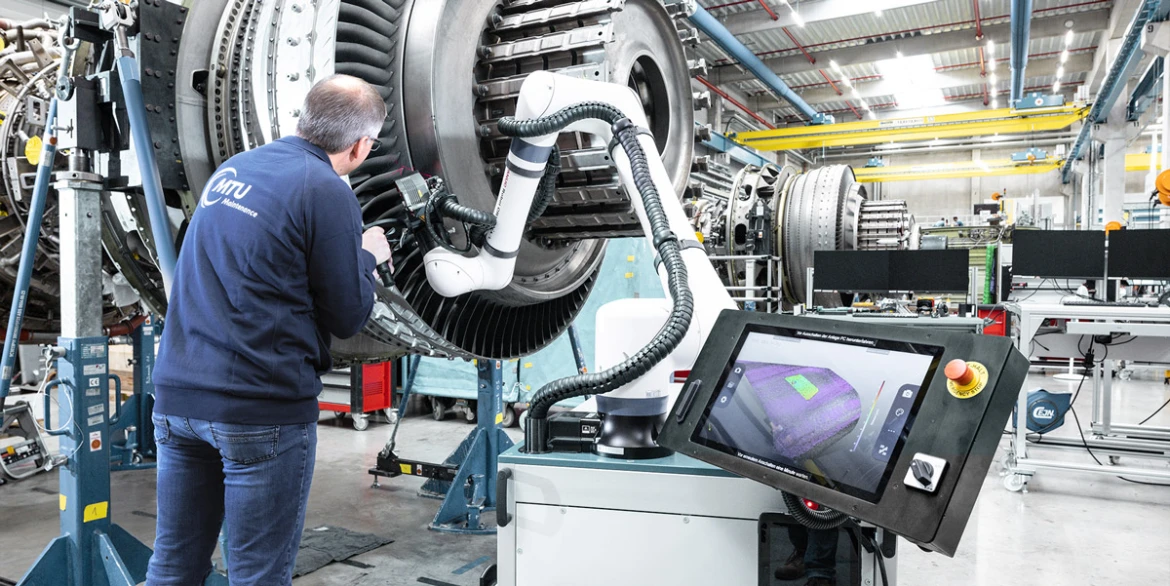
Der Roboterarm bewegt sich über das Triebwerksbauteil – dorthin, wo Benjamin Walter, Projektleiter 3D ScanExpress der MTU Maintenance Hannover, eine minimale, mit bloßem Auge kaum zu erkennende Anomalie ausgemacht hat. An der Spitze hängt ein Weißlicht-Interferometer, das mit Hilfe von Lichtwellen 3D-Messungen durchführen kann. Die Fläche, die mit einem Messvorgang aus wenigen Zentimeter Entfernung begutachtet wird, ist zwar nur drei auf drei Millimeter groß – dafür läuft eine Messung aber in Sekundenbruchteilen ab. So lassen sich auch größere Bereiche eines Triebwerksteils aufnehmen und in einer Punktwolke visualisieren. „Es geht vor allem deutlich schneller und einfacher als dies früher der Fall war und kann komplett auf dem Shopfloor ablaufen“, berichtet Walter.
Hier haben es die Mechaniker:innen täglich mit sehr unterschiedliche Unregelmäßigkeiten auf der Bauteiloberfläche zu tun. Wurde in der Vergangenheit beim Zerlegen und Begutachten des Triebwerks eine vermeintliche Beschädigung an einem Bauteil entdeckt, musste zur Bewertung und Dokumentation mit einer Masse ein Abdruck davon gemacht werden. Dieser ging dann ins Labor zur Auswertung unter dem Mikroskop – Folge: „Das dauerte oft drei bis fünf Tage und hat den Instandhaltungsprozess um mehrere Tage verzögert“.
Schnelleres und effizienteres Messverfahren gesucht
Benjamin Walter entwickelte daher die Idee zu einem optischen Messverfahren, das die Mitarbeiter:innen auf dem Shopfloor entlasten und besagte Wartezeiten verkürzen sollte. Die Idee reichte er beim MTU Inno Lab ein. Die Abteilung hilft zusammen mit einem internationalen Partnernetzwerk dabei, Anwendungen innerhalb kürzester Zeit von der Idee zum Proof of Concept zu führen. Über das Inno Lab fand sich ein standortübergreifendes Team aus München und Hannover mit sehr unterschiedlichem Blickwinkel auf das Thema zusammen: Expert:innen aus den Bereichen Messtechnik, Messsystemzulassung, Maschinenbedienung, Arbeitsvorbereitung und Befund, die das Thema in der täglichen Arbeit erleben – dazu eine Innovationsmanagerin, die die Leitplanken zum Projektverlauf und Reporting vorgab.
„Wir erkannten, dass die Weißlicht-Interferometrie das genaueste, vielseitigste und in verschiedene Richtungen ausbaufähigste System darstellt – und dass eine Lösung des Kooperationspartners 3D.aero aus Hamburg für die Problemstellung und die Anforderungen passen könnte“
MTU-Fachreferent für zerstörungsfreie Prüfverfahren
Weißlicht-Interferometrie
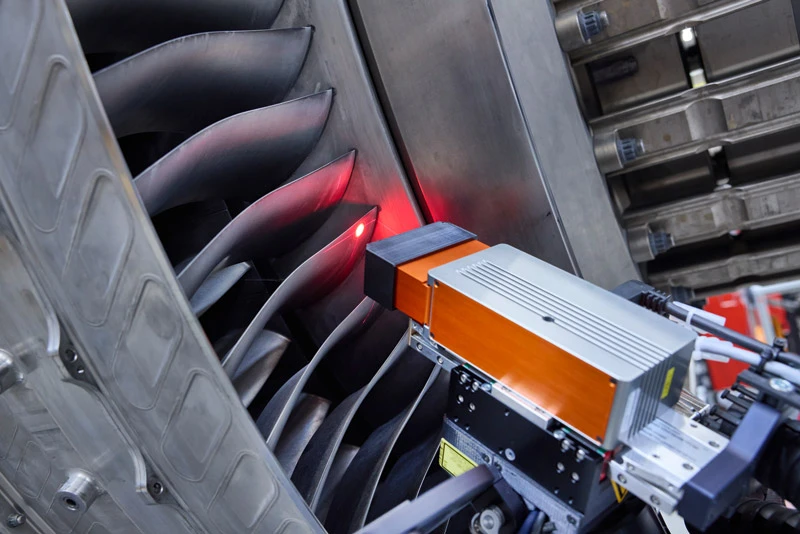
Weißlicht-Interferometrie ist eine optische Messtechnik zur dreidimensionalen Oberflächenvermessung. Sie nutzt Interferenzeffekte, die durch die Überlagerung von reflektiertem Licht und Licht eines Referenzspiegels entstehen, um eine digitale Punktwolke der Bauteiloberfläche zu erzeugen. Weißlicht-Interferometrie ist präzise und unempfindlich gegenüber reflektierenden Oberflächen – ideal für die Triebwerksinstandhaltung.
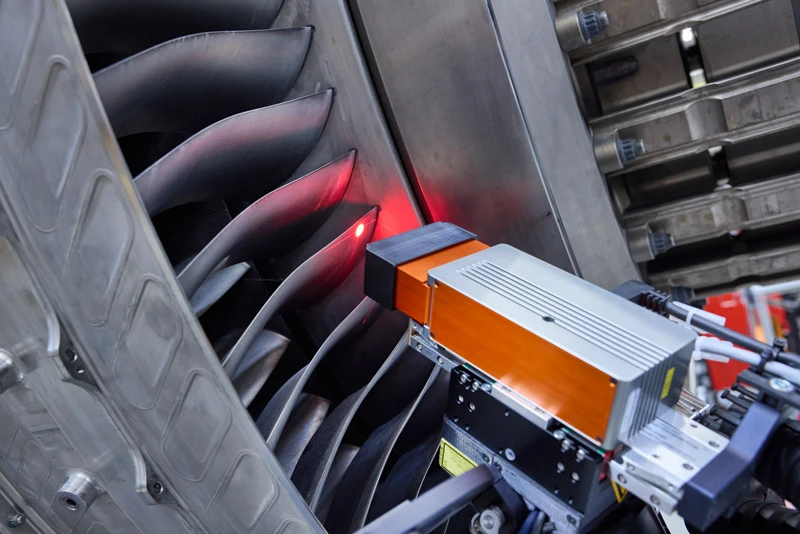
3D.aero liefert passendes Know-how
Das Unternehmen mit Luftfahrtbackground, mit dem die MTU bereits Automatisierungslösungen, wie einen Verschraubungsroboter in Hannover, realisiert hatte, stellte ein Messsystem bereit, das mit Weißlicht-Interferometrie arbeitet, einer leistungsstarken optischen Messtechnik, mit deren Hilfe sich Oberflächen vermessen und in 3D-Datensätze umwandeln lassen. „Dabei überlagert sich das von der Bauteiloberfläche reflektierte Licht mit dem von einem Referenzspiegel zurückgestrahlten Licht. Durch diese Interferenzeffekte entsteht eine digitale Punktewolke, welche die reale Bauteiloberfläche abbildet“, erklärt Stefan Necker, MTU-Experte für geometrische Messtechnik. Durch diese Technologie sind Oberflächenmessungen auf einer breiten Palette von Materialien möglich. Anders als viele andere Technologien ist die Weißlicht-Interferometrie unempfindlich gegenüber reflektierenden Oberflächen – ein entscheidender Vorteil in der Triebwerksinstandhaltung.
Der sechsachsige Rotoberarm lässt sich entweder als kollaborativer Roboter („Cobot“) von Hand bewegen oder führt automatisch das zu untersuchende Bauteil und das Interferometer zusammen. Dadurch können auch größere Bauteile neben dem Messtisch vermessen werden. Über das abnehmbare Tablet lassen sich die Messaufnahmen sofort begutachten oder präsentieren.
In acht Monaten von der Idee zum einsatzfähigen System
Innerhalb von acht Monaten wurde das System für die MTU von der Idee über den Prototyp bis hin zur industriellen Einsetzbarkeit gebracht. „Wir haben es geschafft, die Messung mit Interferometrie sehr agil für die angepassten MTU-Anforderungen zu erschließen, also uns Schritt für Schritt angenähert. Diese Agilität, die in der technischen Entwicklung nicht selbstverständlich ist, hat uns schnell zu einem guten Ergebnis geführt, das nun die Grundlage für weitere Innovationen sein kann“, berichtet Tomas Domaschke, Gründer und Forschungsleiter von 3D.aero.
Wichtig war vor allem, dass die Zuverlässigkeit des Verfahrens für den Anwendungsfall gegeben ist, die Handhabung intuitiv erfolgen und man mit dem Cobot die Messstelle schnell wechseln kann. Inzwischen ermittelt die Software die Messreferenzflächen selbst, führt die Messung aus und entlastet damit den Befunder. Generiert werden 3D-Daten, mit denen man auch gegenüber dem Kunden einen Sachverhalt deutlich besser dokumentieren kann als mit einem Tabellenbericht. Piorun: „Das Team gewinnt täglich neue Erkenntnisse, die in die Weiterentwicklung der Software einfließen.“
„Für die interne messtechnische Zulassung musste zunächst eine Kalibrierroutine des Herstellers so weiterentwickelt werden, dass sie den strengen Vorgaben der MTU genügte“, erzählt Necker. Im Rahmen der anschließenden Messsystemanalyse wurde validiert, unter welchen Bedingungen das System fähige Ergebnisse zuverlässig liefern kann: „So wird sichergestellt, dass das System für unseren Anwendungsfall wirklich geeignet und einsetzbar ist.“ Inzwischen ist das System für die Messung von Oberflächendefekten ab einer Tiefe von 20 Mikrometer (μm) zugelassen – die ungefähre Größe eines weißen Blutkörperchens. „Die nachgewiesen fähige Messung von Defekten in dieser Größenordnung auf dem Shopfloor ist ein echter Meilenstein gewesen“, betont Necker.
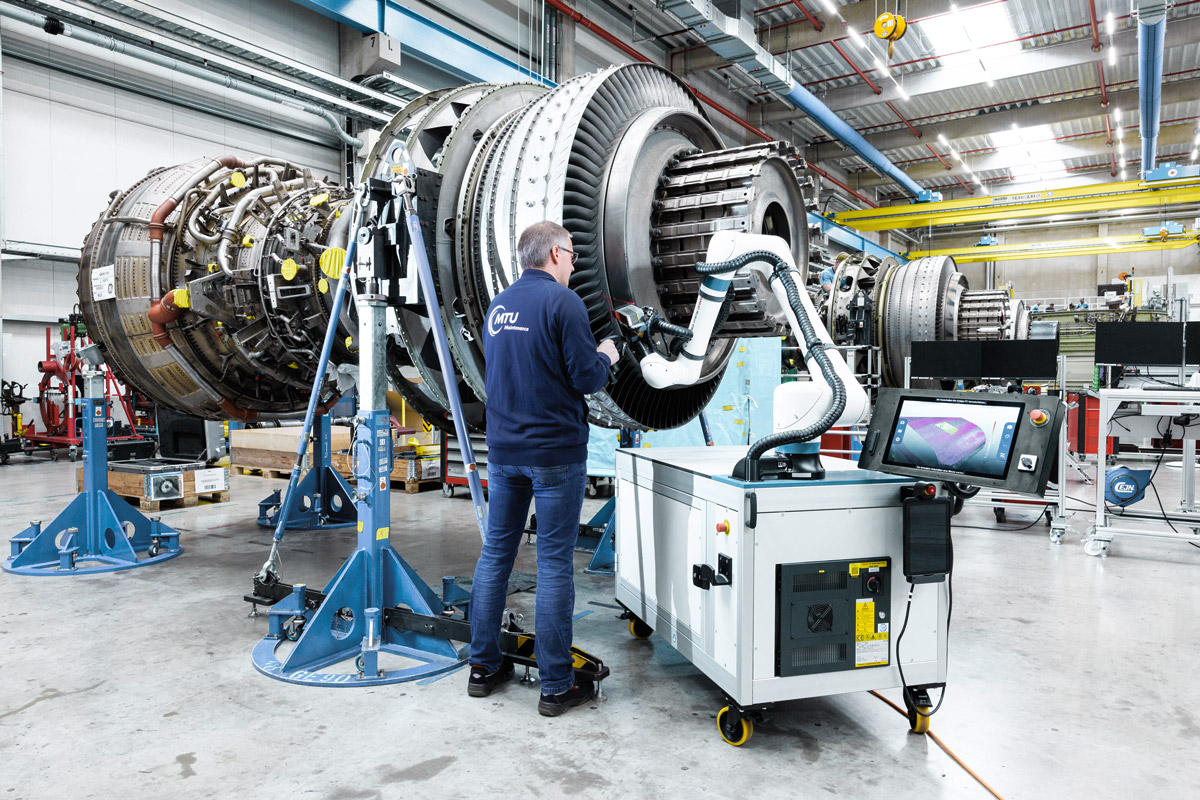
MTU Award für die beste neue Technologie im Unternehmen
Derzeit ist ein System bei der MTU Maintenance Hannover in der Demontage im Einsatz, ein weiteres wird aktuell im Befundbereich industrialisiert und man ist im Austausch mit den anderen MRO-Standorten auf der ganzen Welt um potenzielle Anwendungsfälle zu bewerten. „Im Schnitt gewinnt das Unternehmen einen Tag Durchlaufzeit“, so Walter.
Bereits jetzt hat das neue Messsystem Maßstäbe bei der dreidimensionalen Messung von Oberflächen gesetzt: Für die gemeinsame Einführung mit 3D.aero erhielt das Entwicklerteam den MTU-Award in der Kategorie „Technology and Future“, einen Innovationspreis des Unternehmens, der herausragende Leistungen von Mitarbeiter:innen würdigt.