innovation
The art of the best brush seals
Compared to conventional seals, MTU’s brush seals reduce in-engine leakage by between 50 and 80 percent. This saves up to 1 percent of fuel during operation.
author: Thorsten Rienth | 5 mins reading time published on: 16.10.2024
author:
Thorsten Rienth
writes as a freelance journalist for AEROREPORT. In addition to the aerospace industry, his technical writing focuses on rail traffic and the transportation industry.
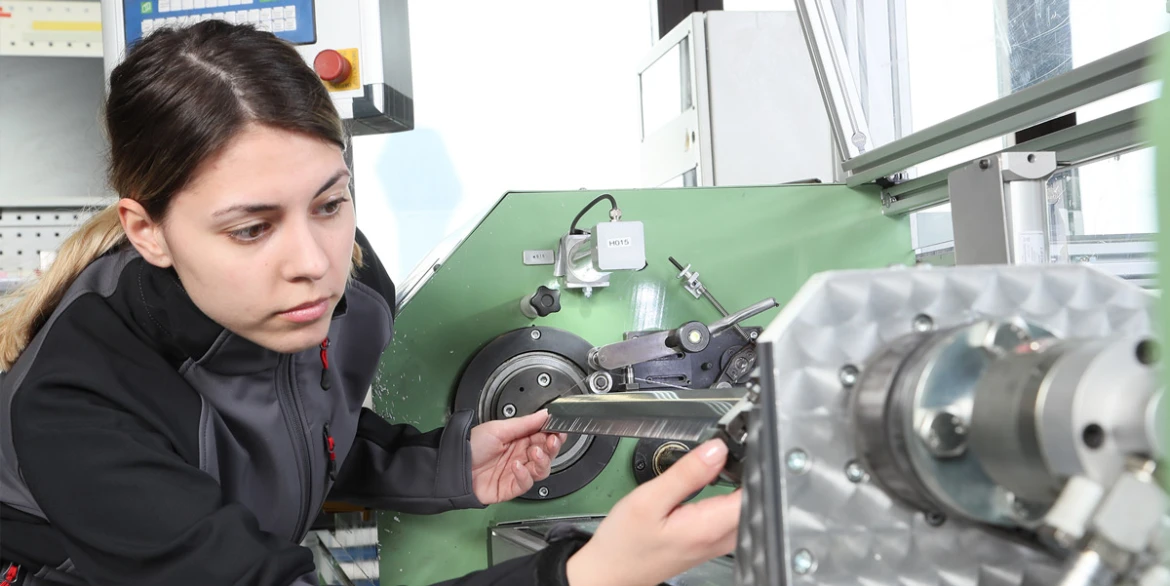
A slight gust of air and this wire would fly away. Its diameter is a mere 0.07 millimeters; even the parchment paper used in baking tends to be thicker. That’s why when the machine draws this wire, multiple strands each time, onto a winding blade, it does so under a protective case made of safety glass. Multiple work steps later and the wire will still fly away—only this time as part of a brush seal installed in, say, a PW1100G-JM engine powering an Airbus A320neo.
Labyrinth seals are a noncontact means of preventing liquids or gases from escaping. Instead of creating a physical barrier, labyrinth seals use an arrangement of integrated chambers to slow the flow of the substance and thus minimize leakage.
“Compared to conventional labyrinth seals, our brush seals can reduce leakage by between 50 and 80 percent, depending on where they’re installed in the engine,” says Dr. Stephan Pröstler, Project Manager for Brush Seals at MTU Aero Engines in Munich. That translates into fuel savings of up to 1 percent.
“Thousands of fine wires are skillfully worked to produce an incredibly flexible seal that adjusts to fit almost perfectly to the rotating surface,” Pröstler explains. “Even at 25,000 revolutions a minute, a rotor can nestle into the ‘brush’ and suffer virtually no wear and tear. The gap between the seal and the component in question is always kept as small as possible.”
Patented MTU manufacturing process
MTU entered into the brush seal business over 40 years ago. At that time, a new cooling air seal was required for the high-pressure turbine in the RB199 engine for the Tornado. This seal would have to withstand pressures greater than 6 bar, temperatures in excess of 500 degrees Celsius, and sliding velocities of up to 170 meters per second.
“Conventional labyrinth seals had no trouble meeting these requirements,” recalls Stefan Beichl, an expert consultant for brush seals at MTU. “However, they frequently caused major unexpected leaks into the rotor, resulting in damage. Then we showed up with a new, soon-to-be patented idea for the manufacture of brush seals.” MTU has been pursuing this principle ever since.
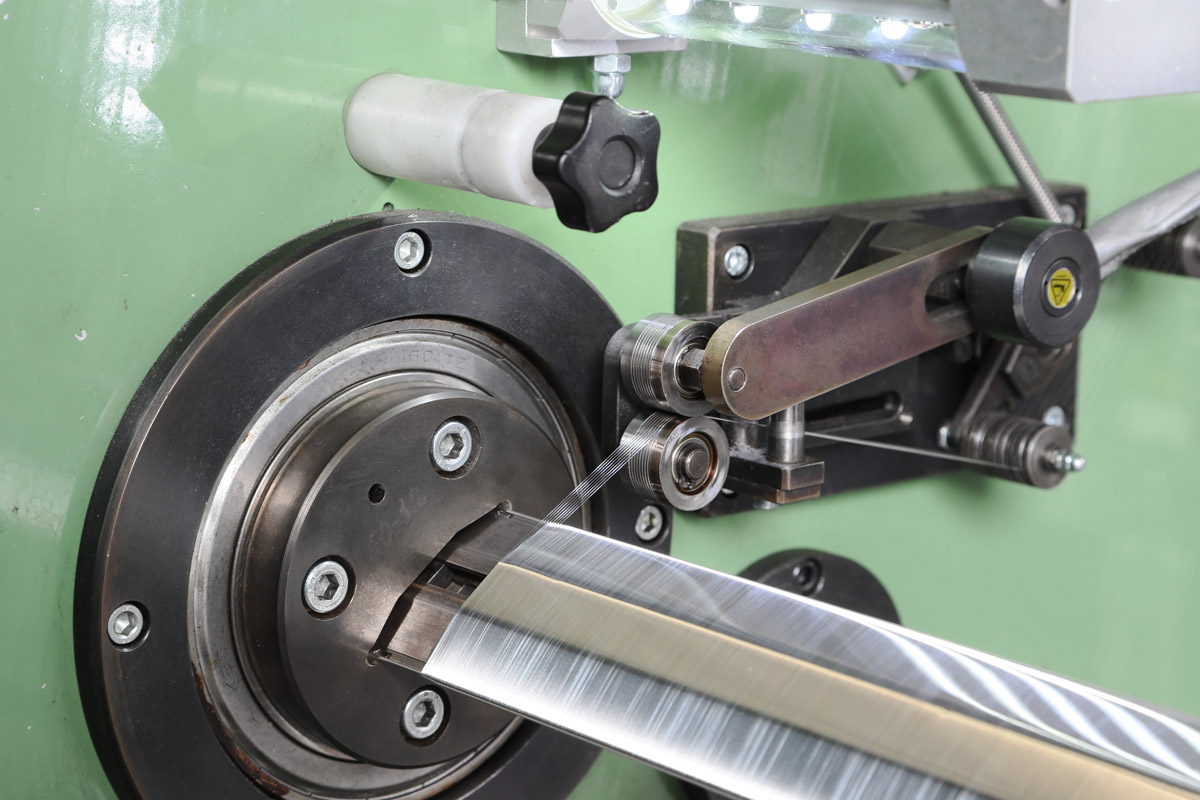
The brush seals are manufactured using a unique wire looping and clamping method.
Haynes25: This cobalt-nickel-chromium-tungsten alloy is characterized by exceptional strength, excellent oxidation properties, and resistance to high temperatures. As this alloy is also relatively workable, it’s an especially common choice for aerospace applications.
Combining multiple wires into a sealing element
“We start by winding wires made of Haynes 25 around two core wires that are held in place by a blade,” explains Alfred Mayr, who has been working in this area from the very start. “We use what’s called a C tube to clamp the wires to the wire core. Then we remove the blade to create a double strip, which we place in a special annealing unit to produce a dense, well-defined wire package. The subsequent low-stress annealing process ensures that the package retains its shape once removed. Next, we cut the double strip in half to produce two brush strips.” The strips are then fashioned into a loop that corresponds to the diameter of the seal type in question. “Now all we have to do is weld the two ends of the strip together, while of course taking extreme care not to damage any of the tiny wires.” That’s precisely what the main challenge has always been in the production of brush seals because it requires such a lot of intricate manual work.
MTU developed its own visual inspection procedure for the final check to ensure that the “brush” has the correct interior diameter.
High wire act
The idea behind the technology of brush seals is as simple as it is brilliant. The construction typically includes thousands of thin bristles forming a very flexible seal which continuously adapts to the moving surface to be sealed. This way, brush seals clearly outperform conventional sealing systems, such as labyrinth seals. Brush seals reduce leakages by up to 90 percent, which boosts the performance of the engine or gas turbine.
MTU’s brush seals have still more advantages to offer: They are suitable for a wide variety of applications, maintain stable operating behavior, and are capable of withstanding extreme service conditions. They are easy to install, have a long life and a compact design which takes up less space than conventional models that have the same sealing effect. On top of that, they are easy to maintain and to replace.
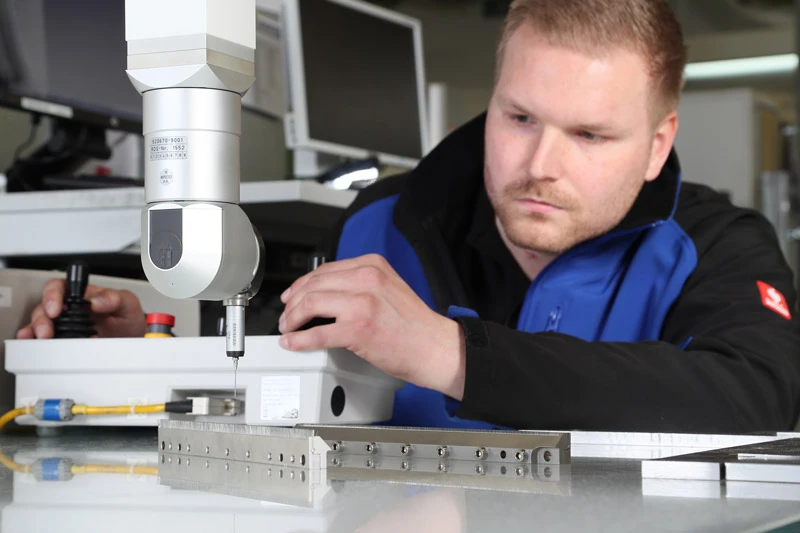
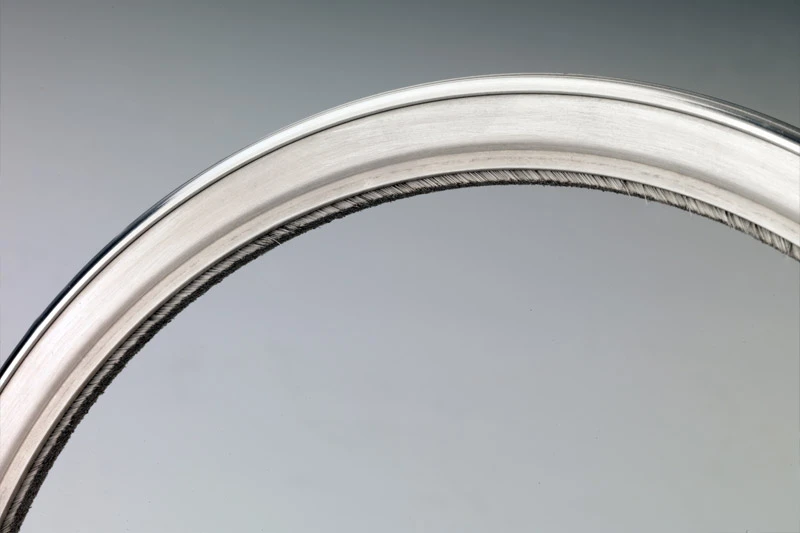
Kevlar: The molecular structure of this heat-resistant, synthetic, para-aramid fiber is composed of numerous bridges and chains. On an equal weight basis, Kevlar has a tensile strength ten times that of steel, which is why it’s become an indispensable component in many safety-critical applications.
Annual kerosene savings of 20,000 metric tons
“We’ve yet to encounter a problem with our RB199 brush seals since they went into production,” Beichl says. Moreover, several of the conventional labyrinth seals in the EJ200, which powers the Eurofighter, have been replaced by the new brush concept. Yet another application is the TP400-D6 for the Airbus A400M military transporter, this time in a variant made using Kevlar. Each millimeter of this brush seal contains more than 6,000 Kevlar fibers.
In the world of commercial aviation, use of these intricate components became popular only gradually. They were first used in test engines such as the IAE V2500 and the Pratt & Whitney PW2037. “Due to the stringent safety requirements of commercial aviation, for a long time companies were reluctant to go through the complex certification process,” Beichl says. “Our first commercial production application was the PW6000 for the Airbus A318.” The “brush” got its big break in commercial aviation with the Pratt & Whitney GTFTM engine family: both the compressor and the turbine contain two brush seals.
New applications on the horizon
MTU systematically developed its brush seals further with a dedicated in-house development team and high-end test stand environment. “The cutting-edge research done for the RB199 application 40 years ago is now the baseline for any brush seal,” Beichl says.
At present, his developer colleagues are in the midst of testing a new wire material. “We’re very optimistic that these efforts will also bump up temperature resistance by a few crucial degrees,” Beichl says. “This would open up new applications for the second generation of geared turbofans, for instance at the inner air seal positions between the rotor and stator in the turbine.” In addition, MTU is hard at work on a potential use case for new military applications.
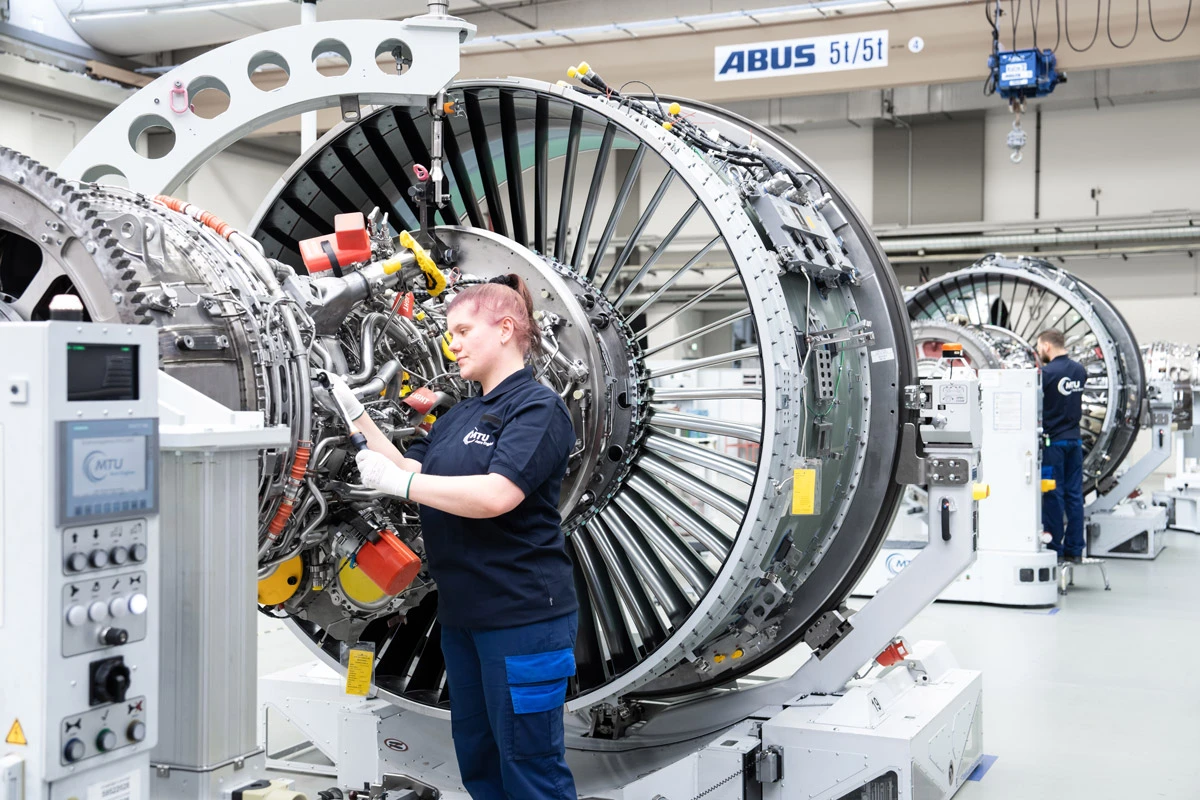
GTF engine family: both the compressor and the turbine contain two brush seals.
Lower losses, higher efficiency
Beichl is convinced that this in no way marks the end of the brush seal story: “Actually, we’re about to see a massive upswing in demand.” Modern turbofan engines are now so advanced, he says, that it will take a lot of effort to improve them further, especially with regard to design. “But when it comes to brush seals, we’re talking about the technological equivalent of a virtually untilled field,” Beichl says. In other words, there is much potential as yet untapped.
Beichl provides some context for how these seals are becoming an increasingly important economic and ecological factor in such engines: “Better seals result in lower losses for the engine. Lower losses mean higher efficiency, and higher efficiency translates into lower fuel consumption.”
MTU brush seals for industrial applications
Approximately 60 percent of the brush seals MTU Aero Engines manufactures are earmarked for the company’s engine business. The remaining 40 percent are allotted to third-party business: customers whose products have problematic spots that require excellent sealing technology. “Many of these external applications are found in pumps and turbomachinery, tools and specialist machines, or vacuum applications,” says MTU expert Stefan Beichl. “We even supply special brush seals to three Formula 1 racing teams.”
MTU brush seals are also found in many industrial turbines—such as those used to generate electricity—that are derived from aircraft engines. For these non-flying applications, weight is less of a factor, but the need for robustness is greater. “Shutting down a power plant for a while because a defective seal needs replacing is simply not an option,” Beichl says.
A particularly novel application is the production of coaters for industrial 3D printers. “We tapped into our sealing expertise for general mechanical engineering and took a strip originally intended as a brush seal and turned it into a long, thin coater for 3D printers,” says Stephan Pröstler. Since then, the European aerospace company ArianeGroup has been successfully using this coating system to 3D print extremely thin-walled components.