The German Air Force Tornados streak across the landscape just 30 meters above the ground. At speeds of more than 800 km/h, the impressive expanse of the Alaskan wilderness turns to a blur in the cockpit. During their Pacific Skies 2024 exercise, the fighter-bombers approach their target with extreme precision. It’s hard to believe that the first aircraft of this type took off on its maiden flight almost exactly 50 years earlier. On August 14, 1974, test pilots Paul Millett and Nils Meister took off from Manching in Bavaria in the prototype of a fighter aircraft that would usher in a new era in Europe: the multirole combat aircraft (MRCA). As the name suggests, the aircraft, which was later christened the Panavia Tornado, was intended to cover a wide range of tasks. This was the first time that three nations—Germany, Italy, and the UK—had joined forces in a consortium.
©GettyImages
aviation
Fifty years of the Tornado – Success with the RB199 engine
author: Patrick Hoeveler | 8 mins reading time published on: 25.09.2024
author:
Patrick Hoeveler
is a freelance aviation journalist working for FLUG REVUE and other publications.
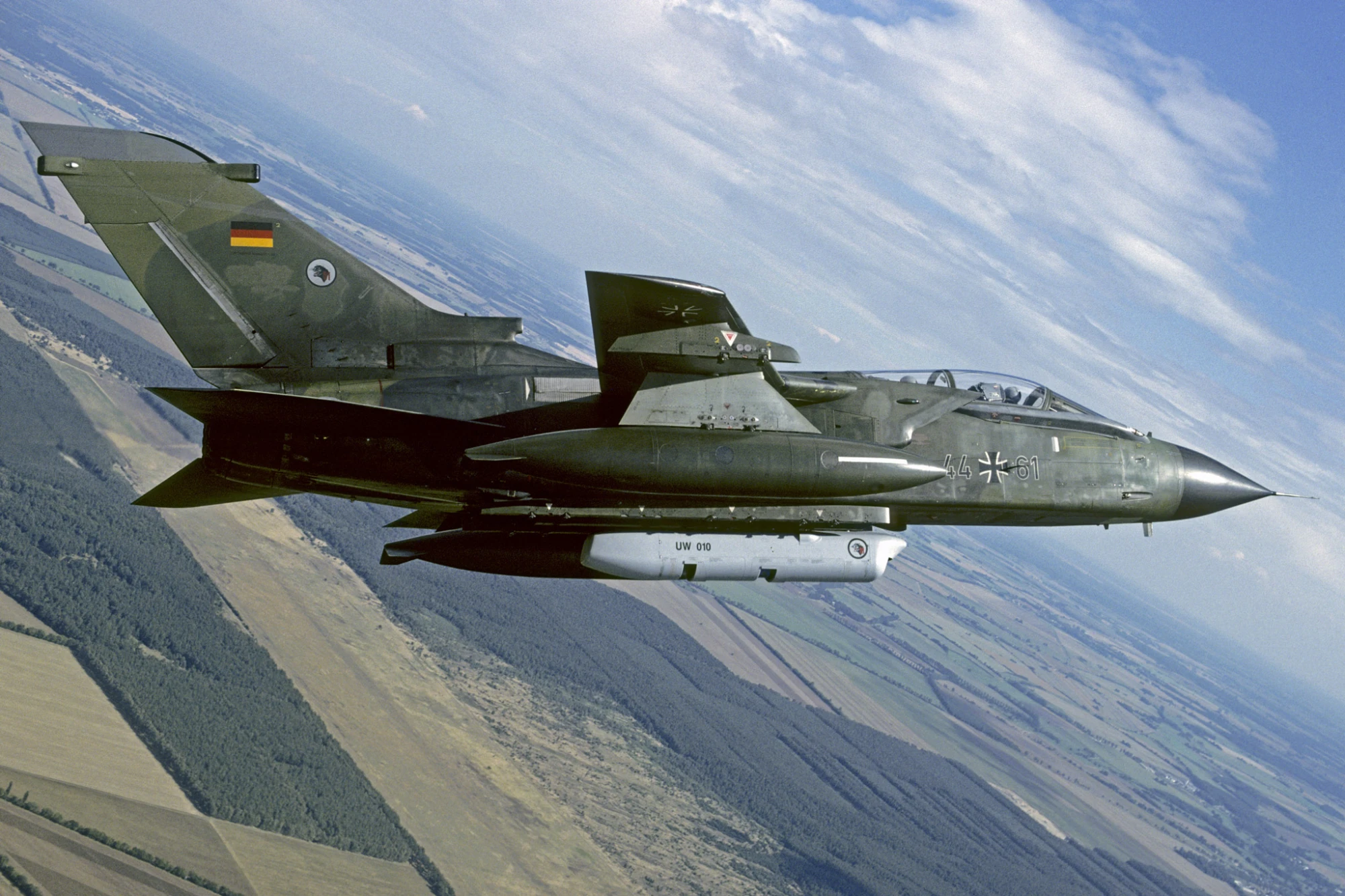
Takeoff weight: | max. 28,5 t |
Length: | 17,23 m |
Thrust force with afterburner: | max. 69,000 N |
Combat and reconnaissance – also at low-level flight
The PA-200 Tornado is a trinationally developed, all-weather, two-seat combat aircraft that was introduced into the armed forces by Germany, the United Kingdom and Italy from 1980 onwards. Delivery of the first PA-200 Tornados to the Bundeswehr began in 1981 and was completed in 1992 with the handover of the last PA-200 Tornado. A total of 357 multi-role combat aircraft was delivered to the German Air Force and the German Navy.Demanding specifications
At that time, the challenges were considerable: the product of the newly created Panavia network was expected to be able to fly at up to Mach 2.2 for supersonic interception missions. For its ground combat role, however, the list of requirements included the ability to cover long distances, fly extremely low, and consume a minimum of fuel. The aircraft also had to be designed for short takeoff and landing distances. This was no easy task at a time when slide rules and drawing tables, not computers, were still the order of the day. When designing the aircraft, one of the features its engineers opted for would later become the jet’s trademark: a variable wing geometry—which also explains the aircraft’s German moniker, “folding kite.”
Innovations were also called for in the engine so it could manage the balancing act between high thrust and low fuel consumption. In September 1969, three companies from the partner countries—Fiat Avio, MTU Aero Engines, and Rolls-Royce—came together to form the Turbo Union consortium. These two projects—the Tornado in aircraft construction and the RB199 in the propulsion sector—were the first major consortium projects in the history of European military aviation. “This project paved the way for all the ones that followed. The Tiger helicopter, the Eurofighter, or the A400M: they’re all based on the experience gained with the Tornado,” says Markus Becker, the current Managing Director of Turbo-Union. “European aviation benefited immensely, not just from the huge amount of development work that went into it, but also because the companies that worked together on it really hit their stride.”
Three shafts for success
It wasn’t long before the first RB199 was running on the test stand in September 1971. This record speed can be explained by the fact that Rolls-Royce had already done some preliminary work. To guarantee the highly variable thrust requirements, the engineers opted for what was then still an unusual design with three shafts. Some predecessor engines, such as the J79 for the F-4 Phantom, manufactured under license by MTU, had just the one shaft.
The advantage of the three-shaft concept is that it lets each of the components in the high-, medium-, and low-pressure segments operate in its optimum speed range (rpm). “As a result, the respective compressors don’t need as many stages, meaning the entire engine is smaller and lighter,” explains Rasmus Merkler, the current chief engineer for the RB199 at MTU. In addition, the RB199 is a turbofan that already had a bypass ratio of over 1 to reduce consumption—an absolute innovation at the time.
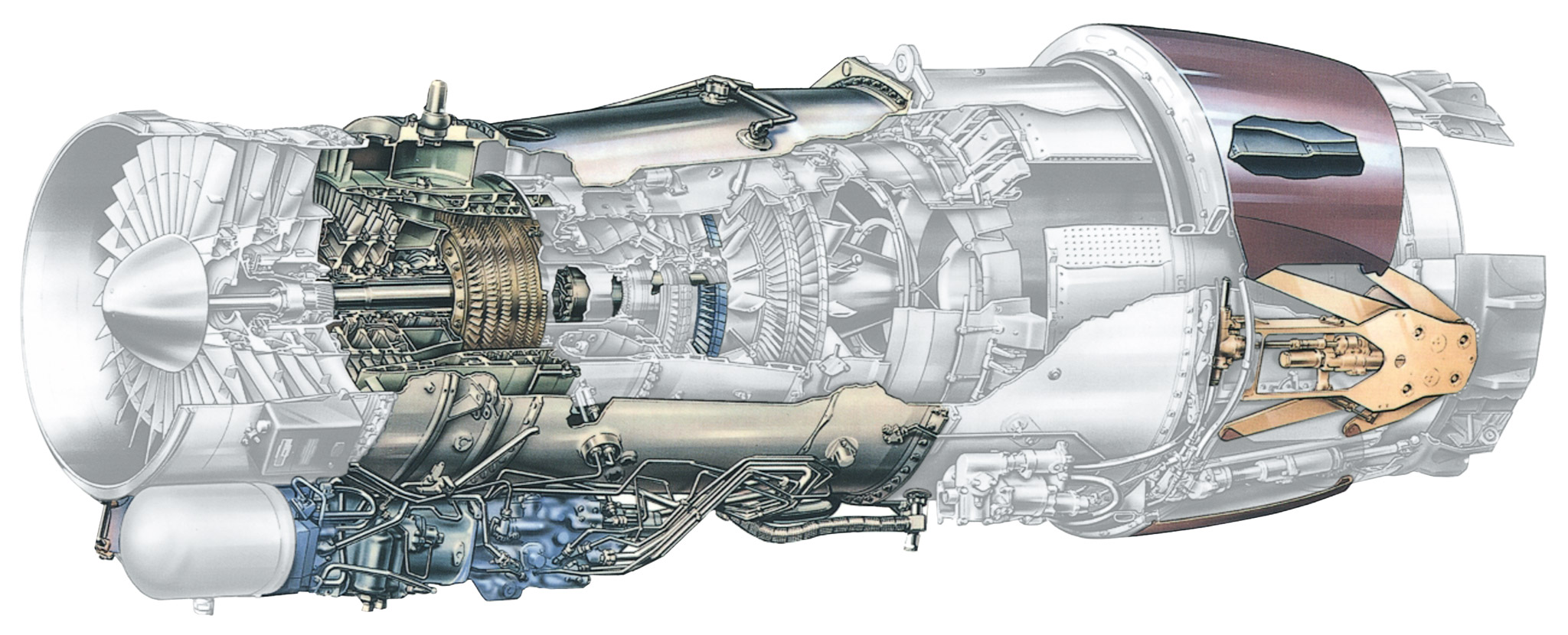
Development and manufacture: MTU’s part in this successful engine was to deliver its first independently developed and manufactured components such as the intermediate-pressure compressor, high-pressure compressor, and intermediate-pressure turbine.
Another requirement was for engine maintenance to be simple and cost-effective. To this end, the planners came up with a modular concept: the engine consisted of 16 modules that are easy to switch out. As part of its 40 percent program share, MTU was given responsibility for the intermediate- and high-pressure compressors as well as the intermediate-pressure turbine, the gearbox, the oil system, and the thrust reverser. Up to this point, the then young MTU—which had just been formed in 1969 from the merger of the engine divisions of Daimler-Benz and MAN—had manufactured only under license. “The RB199 marked our entry into military engine development,” says MTU Program Manager Martin Majewski. “This is where we learned how to construct, so to speak. If we’d continued to manufacture only under license, we would never have gotten to where we are today.” For the RB199, the company learned new processes and technologies that later found their way into other military programs or into the world of commercial aviation. For example, the technicians were able to take the brush seal invented for the Tornado’s engine and incorporate this valuable knowledge into other programs. The most prominent example at present is the geared turbofan from Pratt & Whitney and MTU.
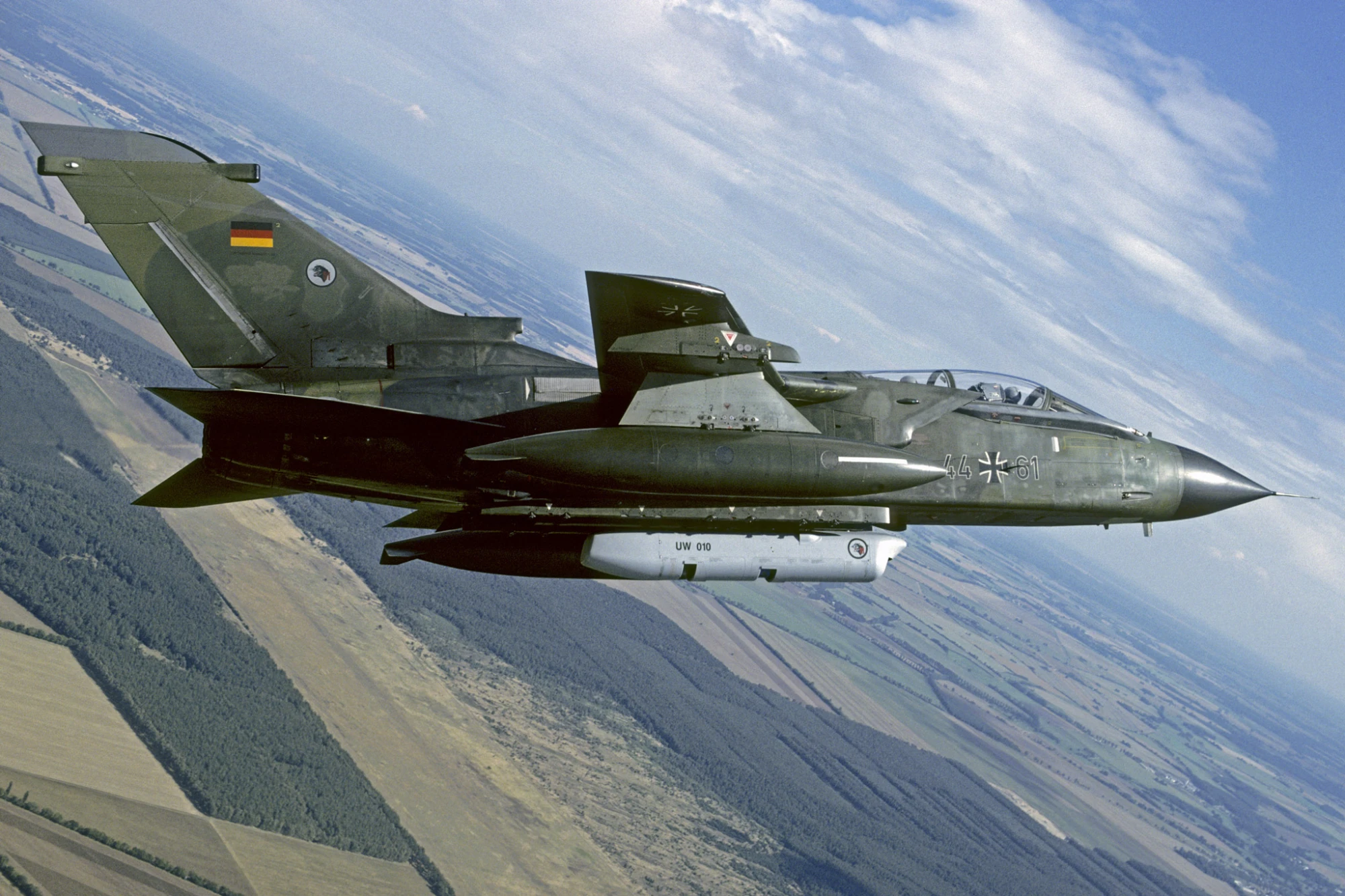
RB199: Powering the Tornado
In collaboration with Rolls-Royce and Avio Aero, MTU began developing and producing the RB199 in 1969 to power the Panavia Tornado multirole fighter jet. As of December 2023, the 2,504 delivered RB199 engines had completed more than 7.18 million flight hours. The RB199 is the world’s only military engine with an integrated thrust reverser.Afterburner thrust (ground level): | 16,000–17,000 lbf |
Max. thrust without afterburner: | 9,217 lbf |
Pressure ratio: | 23:1 |
Bypass ratio: | 1:1.3 |
Length: | 10.5 ft |
Weight including thrust reverser: | 2,390 lbs |
The first step is always the hardest
However, the innovations and the high pace of development also took their toll: the technicians had to overcome a few teething troubles before the engines were ready to enter service. For instance, the three intermeshing shafts required a complex bearing structure with many seals and subsequent changes to the oil system; the intermediate-pressure compressor also initially had a negative impact on aerodynamic stability. The modifications these problems called for contributed greatly to today’s stock of know-how thanks to the necessary performance calculations and design capabilities.
Following this problematic initial phase, the RB199 has developed into a highly reliable engine, according to Bernd Kramer, Head of Customer Support at MTU. “The technologies in the RB199 gave the aircraft performance capabilities that other models didn’t have.” The engine also had to support the automatic low-level flight and withstand short periods at maximum output. “Today that’s no longer anything special, but back then the RB199 met all its specifications in an exemplary manner.” Over time, the MTU specialists also improved the performance of the high-pressure compressor by a total of 12 percent, and they replaced the mechanical engine control system with a digital version in the mid-1980s—both areas that are now among the company’s core competencies.
MRO mainstay
With a total of more than 2,500 units built, the RB199 also proved to be an economic mainstay for many years. And not only in production, but above all in the MRO business. MTU still tops the list for the German Air Force in this area. Each of the three partners was responsible for final assembly of the engines for their home country—for Germany, MTU has built around 700—and provides comprehensive support for their engines. “This model offered by far the largest volume to date in our military maintenance, in terms of both unit numbers and capacity utilization,” explains Stefan Burger, Head of Program Management EJ200 and RB199 MRO. To date, MTU has performed 1,660 overhaul operations on Tornado engines for the Bundeswehr. As with the other programs, MTU is now carrying out this work jointly with the German Armed Forces as part of their engine maintenance cooperation (IKT).
For MTU, one priority was to develop repair processes: “We built up the lion’s share of our parts repair capability with the RB199. We’ve made a name for ourselves within the Turbo-Union in this respect, and that has continued with the EJ200 for the Eurofighter,” Burger says. That includes things like laser powder cladding on airfoil tips and making dimensional corrections with the help of spray coatings.
“We first industrialized these processes as part of our work on the RB199,” says Gerhard Hackl, a maintenance planner for the engine. “Many of the repairs we developed here have gone on to be very valuable in the commercial sector.”
Instandsetzungsplaner beim RB199
Flight operations up to 2030
In the Tornado’s heyday, around 60 engines came in for a shop visit each year. The number is much lower now, as the European fighter-bomber gradually reaches the end of its career. The British Royal Air Force had already bid the aircraft farewell in 2019. That leaves three operators as of today: Italy, which plans to retire the jet for good in 2027, plus Germany and Saudi Arabia, which are expected to continue flying it until 2030. To date, the entire RB199 fleet has completed around 7.18 million flight hours.
Planning for the procurement of spare parts is now a major task, and one that is becoming increasingly difficult due to the steadily decreasing batch sizes. In some cases, work is already underway on what is known as final stockpiling, in which one last bulk order is placed based on estimated demand. In addition, the Bundeswehr has a large stock of components that MTU specialists have removed from obsolete engines, inspected, and repaired as part of the company’s high-value parts recovery program.
You may also be interested in following content
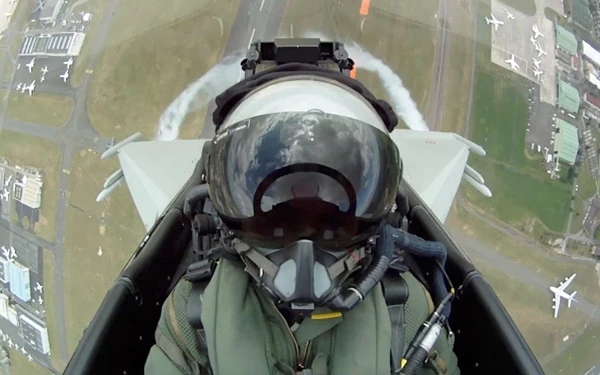
New momentum for the Eurofighter’s EJ200 engine
Thanks to new orders, production of the Eurofighter Typhoon engine is gaining renewed momentum.
The EJ200 takes over
As the RB199 business wanes, the EJ200 business for the Eurofighter is growing. Ultimately, the German Air Force’s Tornados will give way to the F-35 Lightning II from the United States—and to additional Eurofighters. A number of export campaigns for the European product are currently still being pursued. Germany, Italy, and Spain have either ordered further tranches or are planning to procure more, as program manager Majewski explains: “Even if the EJ200 hasn’t yet reached the same level as the RB199 in terms of unit sales, it’s currently experiencing a significant upswing.” The Eurofighter still has three decades—or perhaps even longer— to catch up with its illustrious predecessor.