innovation
Die Kunst der besten Bürstendichtung
Gegenüber konventionellen Dichtungen verringern MTU-Bürstendichtungen Leckagen im Triebwerk um 50 bis 80 Prozent. Das spart im Betrieb bis zu einem Prozent Kraftstoff.
Autor: Thorsten Rienth | 5 Min. Lesezeit veröffentlicht am: 16.10.2024
Autor:
Thorsten Rienth
schreibt als freier Journalist für den AEROREPORT. Seine technikjournalistischen Schwerpunkte liegen neben der Luft- und Raumfahrtbranche im Bahnverkehr und dem Transportwesen.
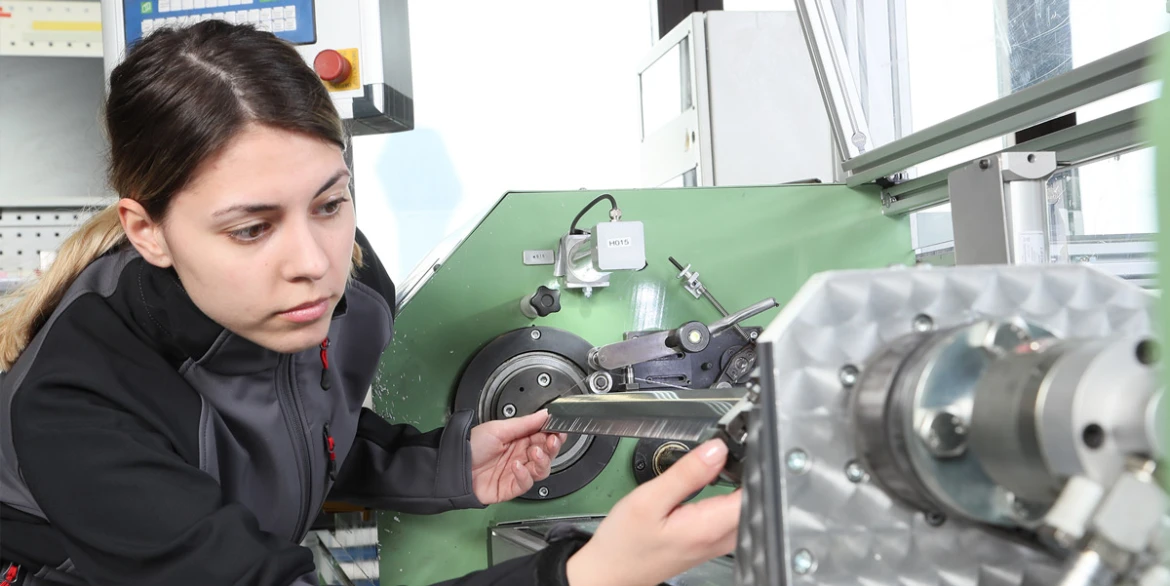
Ein kleiner Luftzug nur und der Draht würde sofort wegfliegen. Filigrane 0,07 Millimeter misst sein Durchmesser. Selbst Pergamentpapier ist oft dicker. Deshalb zieht ihn die Maschine unter einem schützenden Sicherheitsglaskasten auf ein Wickelschwert, mehrere dieser Stränge auf einmal. Viele Arbeitsschritte später wird der Draht trotzdem abheben. Aber in Form einer Bürstendichtung, zum Beispiel in einem PW1100G-JM-Triebwerk an einem Airbus A320neo.
Labyrinthdichtungen bezeichnen eine Dichtart, die das Austreten von Flüssigkeiten oder Gasen berührunglos verhindert. Anstatt eine physische Barriere zu bilden, nutzen Labyrinthdichtungen mehrere integriert angeordnete Kammern, die den Fluss der Medien verlangsamen und dadurch Leckagen minimieren.
„Im Vergleich zu konventionellen Labyrinthdichtungen können wir mit unseren Bürstendichtungen je nach Einbauort im Triebwerk Leckagen um 50 bis 80 Prozent verringern“, sagt Dr. Stephan Pröstler, Projektmanager des Bürstendichtungsgeschäfts bei der MTU Aero Engines in München. Umgerechnet bedeutet das eine Kraftstoffersparnis von bis zu einem Prozent.
„Geschickt verarbeitet bilden die tausenden dünnen Drähte eine sehr flexible Dichtung, die sich nahezu perfekt an rotierende Flächen anpasst“, erklärt Pröstler. „Selbst bei 25.000 Umdrehungen in der Minute kann der Rotor in die ‚Bürste‘ eintauchen, wird von ihr aber fast nicht abgenutzt. Der Spalt zwischen Dichtung und abzudichtendem Bauteil bleibt immer minimal klein.“
Patentiertes MTU-Fertigungsverfahren
Vor über 40 Jahren stieg die MTU ins Bürstendichtungsgeschäft ein. Damals war eine neue Kühlluftabdichtung für die Hochdruckturbine des Tornado-Triebwerks RB199 gefordert. Mehr als 6 bar Druck, über 500° Celsius Temperaturbeständigkeit und eine Gleitgeschwindigkeit von bis zu 170 Meter pro Sekunde sollte sie standhalten.
„Das schafften die konventionellen Labyrinthdichtungen zwar locker“, erinnert sich Stefan Beichl, Fach-Repräsentant der Bürstendichtung bei der MTU. „Aber sie liefen immer wieder ungeplant heftig in den Rotor ein und verursachten Beschädigungen. Dann kamen wir mit einer neuen und bald patentierten Idee für die Fertigung von Bürstendichtungen ums Eck.“ Bis heute setzt die MTU auf dieses Prinzip.
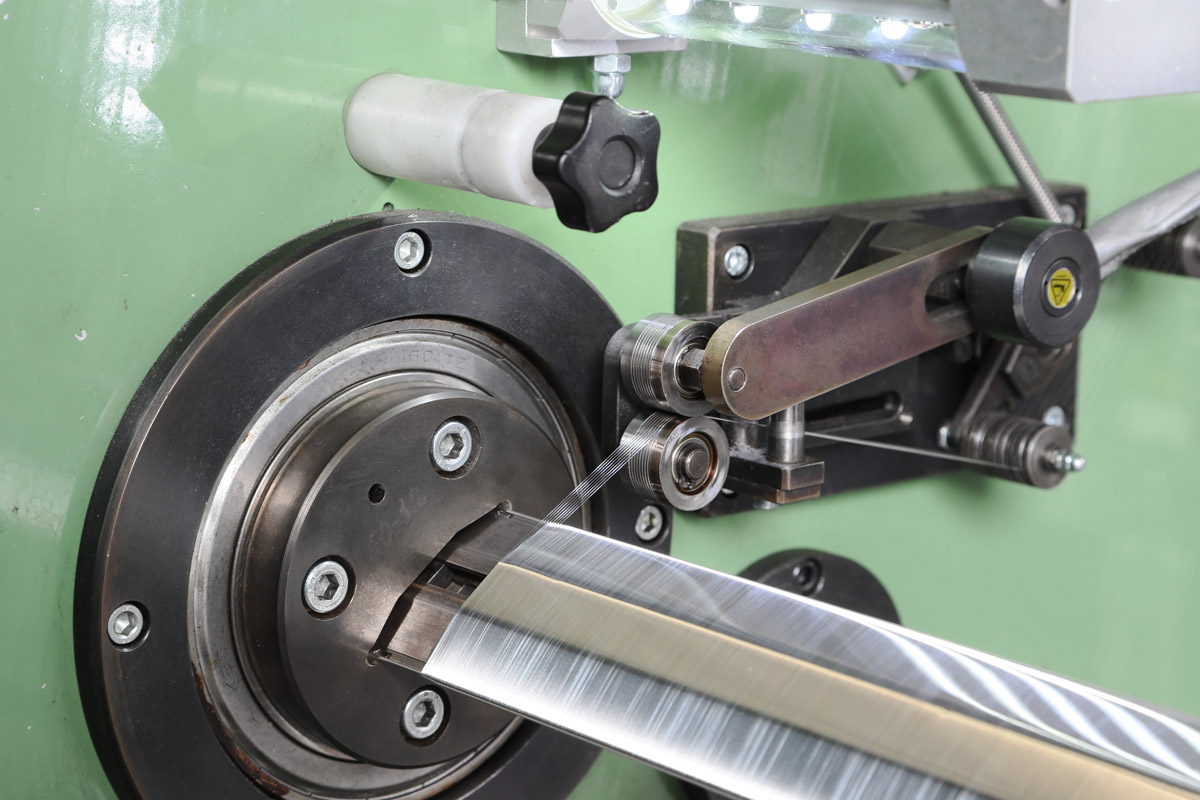
Tausende, dünne Drähte: Die Bürstendichtungen werden in einzigartigen Wickel- und Klemmverfahren hergestellt.
Haynes25: Die Cobalt-Nickel-Chrom-Wolfram- Legierung weist eine außergewöhnliche Festigkeit, sehr gute Oxidationseigenschaften sowie Beständigkeit auch gegenüber hohen Temperaturen auf. Weil die Legierung dennoch relativ gut bearbeitbar ist, kommt sie insbesondere bei Luft- und Rahmfahrtanwendungen zum Einsatz.
Aus vielen Drähten wird ein Dichtelement
„Zuerst wickeln wir die Drähte aus Haynes25 um zwei Kerndrähte, die durch ein Schwert gehalten werden“, erklärt mit Alfred Mayr ein Mann der ersten Stunde bei der MTU. „Mit dem sogenannten C-Rohr klemmen wir die Drähte am Kerndraht fest, entfernen das Schwert und erzeugen somit den sogenannten Doppelstreifen. Dieser Doppelstreifen wird in eine spezielle Glühvorrichtung montiert, um ein dichtes und definiertes Drahtpaket zu erzeugen. Durch das anschließende Spannungsarmglühen behält er nach der Demontage aus der Glühvorrichtung seine Form. Dann schneiden wir den Doppelstreifen in der Mitte durch und erhalten dadurch zwei Bürstenstreifen.“ Durch das Abrunden in eine kreisrunde Form wird der spezifische Durchmesser jedes Dichtungstyps hergestellt. „Jetzt müssen wir nur noch die beiden Enden des gerundeten Bürstenstreifen zusammenschweißen, natürlich so vorsichtig, dass keiner der feinen Drähte Schaden nimmt.“ Genau das war bis dato die zentrale Herausforderung bei der Produktion von Bürstendichtungen und hat viel filigrane Handarbeit erfordert.
Mit einem eigens entwickelten optischen Prüfverfahren vermessen die Schlussprüfer:innen am Ende den korrekten Innendurchmesser der „Bürste“.
Fliegende Drähte
Hinter den Bürstendichtungen steht eine ebenso einfache wie geniale Technologie: Bei Bürstendichtungen bilden tausende dünne Drähte eine sehr flexible Dichtung, die sich nahezu perfekt an die abzudichtende Fläche anpasst. Mit dieser Eigenschaft sind sie den üblicherweise verwendeten Labyrinthdichtungen deutlich überlegen. Durch den Einsatz von Bürstendichtungen können Leckagen um bis zu 80 Prozent verringert und dadurch die Leistungsfähigkeit der Maschine gesteigert werden.
MTU-Bürstendichtungen haben noch weitere Vorteile: Sie sind vielfältig einsetzbar, zeigen ein robustes Verhalten im Betrieb und halten extremen Bedingungen stand. Sie sind leicht einzubau-en, benötigen bei gleicher Dichtwirkung weniger Raum als herkömmliche Modelle und erreichen eine lange Lebensdauer. Zudem lassen sie sich einfach instand setzen und nachrüsten.
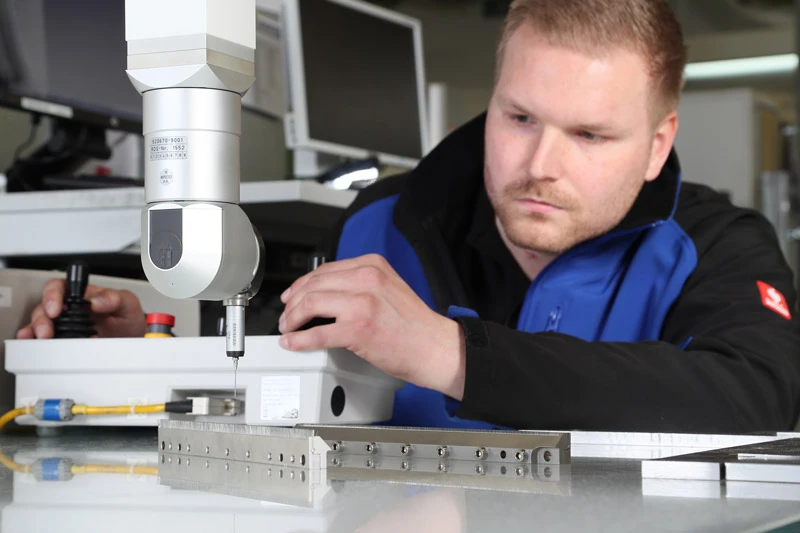
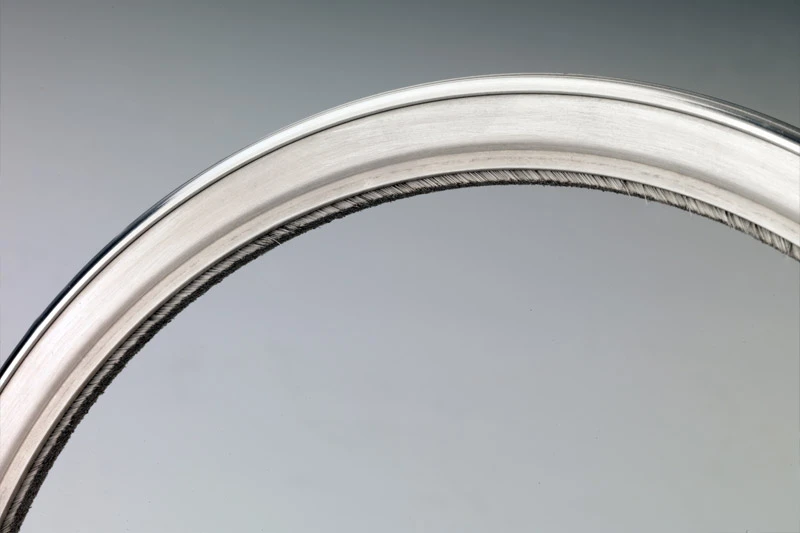
Kevlar: Bei dem syntehischen Material handelt es sich um eine hitzebeständige Para-Aramidfaser mit einer Molekularstruktur aus zahlreichen Brücken und Ketten. Bei gleichem Gewicht erreicht Kevlar eine zehnmal höhere Zugfestigkeit als Stahl – weswegen es heute aus vielen sicherheitskritischen Anwendungen nicht mehr wegzudenken ist.
20.000 Tonnen weniger Kerosin pro Jahr
„Probleme mit den RB199-Bürstendichtungen hat es im Serienbetrieb nie gegeben“, resümiert Beichl. Also wichen auch im Eurofighter-Triebwerk EJ200 einige der konventionellen Labyrinthdichtungen dem neuen Bürstenkonzept. Eine weitere Anwendung kommt mit einer Kevlar-Variante im TP400-D6 für den Airbus-Militärtransporter A400M hinzu. Auf einen Millimeter Bürstendichtung kommen dabei mehr als 6.000 Kevlar-Fasern.
In der zivilen Luftfahrtwelt haben die filigranen Bauteile erst nach und nach Einzug gehalten. Zuerst in Versuchstriebwerken der IAE V2500 und Pratt & Whitney’s PW2037. „Wegen der hohen Sicherheitsanforderungen scheute man einfach lange Zeit den Zulassungsaufwand“, schildert Beichl. „Beim PW6000 für den Airbus A318 waren wir dann zum ersten Mal mit einer zivilen Serienanwendung an Bord.“ Mit der Pratt & Whitney GTFTM Triebwerksfamilie gelang der „Bürste“ dann der zivile Durchbruch: Je zwei Dichtungen sind im Verdichter und in der Turbine verbaut.
Neue Anwendungen in Sicht
Mit einem eigenen Entwickler:innen-Team und hochwertiger Prüfstandumgebung hat die MTU ihre Bürstendichtungen sukzessive weiterentwickelt. „Die damaligen Spitzenanforderungen aus dem RB199 gehören heute zum Komfortbereich jeder Bürstendichtung“, ordnet Beichl ein.
Seine Kolleg:innen aus der Entwicklung befinden sich derzeit mitten in der Erprobung eines neuen Drahtmaterials. „Wir sind sehr optimistisch, dass wir damit bei der Temperaturbeständigkeit einige entscheidende Grad zusätzlich ermöglichen“, erzählt Beichl. „Das eröffnet uns neue Anwendungen in der zweiten Getriebefan-Generation, zum Beispiel an den Inner-Air-Seal-Positionen zwischen Rotor und Stator in der Turbine.“ Darüber hinaus wird mit Hochdruck an einem Einsatz in neuen militärischen Anwendungen gearbeitet.
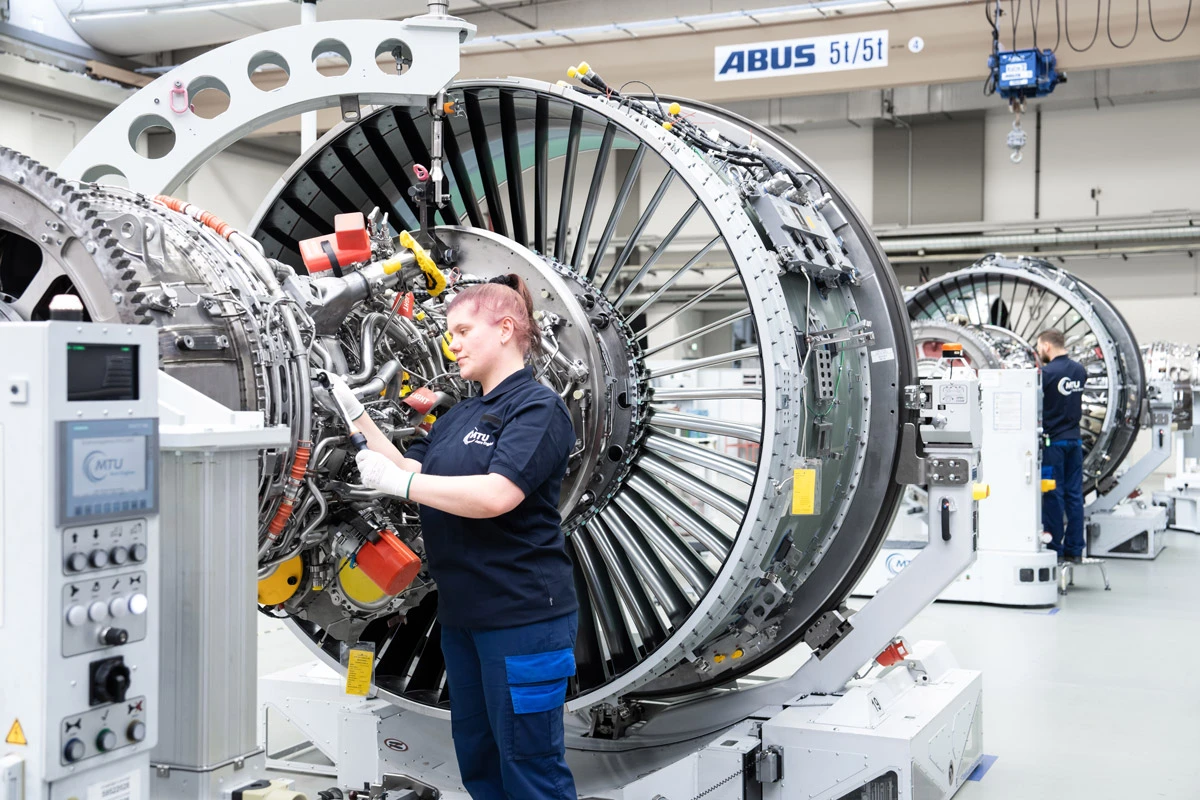
GTF Triebwerksfamilie: Je zwei Bürstendichtungen sind im Verdichter und in der Turbine verbaut.
Weniger Verluste, besserer Wirkungsgrad
Dass die Geschichte der Bürstendichtungen damit zu Ende erzählt wäre, glaubt Beichl keinesfalls. „Eher stehen wir vor einem gewaltigen Hochlauf.“ Moderne Turbofan-Triebwerke seien mittlerweile derart ausgereift, dass weitere Verbesserungen vor allem am Design nur noch mit viel Aufwand umzusetzen sind. Seine Einschätzung: „Bei den Bürstendichtungen handelt es ich um ein technologisch noch vergleichsweise wenig beackertes Feld.“ Entsprechend viel ist dort noch zu holen.
Den Kontext, der die Dichtungen zu einem immer wichtigeren ökonomischen wie ökologischen Faktor im Triebwerk macht, beschreibt Beichl so: „Mit einer verbesserten Dichtung lassen sich im Triebwerk Verluste sparen. Wo Verluste wegfallen, steigt der Wirkungsgrad. Und ein höherer Wirkungsgrad bedeutet wiederum einen geringeren Kraftstoffverbrauch.“
MTU-Bürstendichtungen für Industrieanwendungen
Etwa 60 Prozent der bei der MTU Aero Engines produzierten Bürstendichtungen sind fürs Triebwerksgeschäft des Unternehmens bestimmt. Die restlichen rund 40 Prozent entfallen auf das sogenannte Drittgeschäft: auf Kunden, die an neuralgischen Stellen ihrer Produkte auf höchste Dichtleistung angewiesen sind. „Viele externe Anwendungen kommen aus dem Pumpen- und Turbomaschinensegment, den Bereichen Werkzeug- und Sondermaschinen oder Vakuum-Anwendungen“, berichtet MTU-Experte Stefan Beichl. „Auch drei Formel-1-Rennställe rüsten wir mit speziellen Bürstendichtungen aus.“
In vielen von Flugtriebwerken abgeleiteten Industriegasturbinen, die etwa zur Stromerzeugung eingesetzt werden, sind ebenfalls MTU-Bürstendichtungen verbaut. Bei diesen nicht fliegenden Anwendungen ist der Gewichtsfaktor weniger wichtig. Dafür sind die Anforderungen an die Robustheit höher. Beichl: „Ein Kraftwerk wegen einer defekten und auszuwechselnden Dichtung vorrübergehend abzuschalten? Absolut undenkbar.“
Eine sehr besondere Anwendung stellt die Produktion industrieller 3D-Druck-Beschichterklingen dar. „Wir haben unsere Dichtungsexpertise in den allgemeinen Maschinenbau übernommen und aus einem ursprünglich als Bürstendichtung gedachten Streifen eine längliche Beschichterklinge für 3D-Druckmaschinen entwickelt“, berichtet Pröstler. Seither nutzt etwa das europäische Raumfahrtunternehmen ArianeGroup die „Abzieher“ erfolgreich für den 3D-Druck extrem dünnwandiger Raumfahrtbauteile.