innovation
The future of turbine disk production
MTU is revolutionizing turbine disk production: fully automated processes, shorter turnaround times, and maximum precision.
author: Tobias Weidemann | 5 mins reading time published on: 07.05.2025
author:
Tobias Weidemann
has been working as a journalist and content consultant for more than 20 years. He writes about technology and business topics, often with a focus on business IT, digitalization and future technologies.
After a quiet whir, the robot goes into action. With millimeter precision, it grasps a blank for a turbine disk, positions it, and screws it securely into the fixture. On the other side of the machine, a second robot inserts the appropriate turning tools into the tool holder. The setup cell is able to replace the used turning tool with a new one approximately every 37 seconds. Once the tool is in place, a gripper takes the component and loads it onto the turning machine. At the same time, the ready-to-use tools are loaded fully automatically. The turning machine then goes over the workpiece again and again with the appropriate cutting tools, giving the blank its contours step by step.
What makes this system special? The entire process is optimized so that the machine works without any interruptions. It manages tools and workpieces separately: while one component in the machining area is being unclamped, the setup cell is already preparing the next one for the turning process.
A fully automated process – with just a few exceptions
It’s clear from the first glance that the way turbine disks are manufactured here differs widely from the setup at comparable plants. “We have the most cutting-edge manufacturing facility for turbine disks in the world: with the help of industrial robots, we can set up the components and, more importantly, the tools fully automatically,” says MTU project manager Christina Braun. The independence of individual areas is another of the facility’s USPs. “We specifically wanted a handling system that’s separate from the machine workspace. In our existing facilities, this had always proved to be a limiting factor, because the process for setting up the workpiece and tools would constantly tie up the machine.”
Four turning machines and four milling machines are available for machining the turbine disks. The blanks, which come from MTU’s site in Rzeszów, Poland, are first turned and then sent to the neighboring production facility for broaching. Subsequent milling is carried out in the new manufacturing facility. Here too, the workpieces are loaded automatically via an airlock and the tools are kept in a storage unit behind the machines.
At the end of the milling process, the turbine disk is deburred—a delicate manual operation in which a collaborative robot assists the human operator. Finally, the turbine disks are treated elsewhere in the facility using the required specialized technique, such as coating, shot peening, or heat treatment. They then return to the test center, located one floor above the production line, for final inspection.
6,000 low-pressure turbine disks per year
MTU currently manufactures up to 6,000 low-pressure turbine disks here every year—for use in engines such as the geared turbofan for the Airbus A320neo. “In a second expansion stage in around ten years’ time, this could be up to 12,000 components per year,” says Markus Full, Head of NC Programming at MTU, although the company also plans to produce further variants for other engines.
The team has invested a great deal of effort in developing and optimizing processes—for example, a completely new measuring solution for calibrating and adjusting the machines and robots. In addition, the team developed a new system especially for the facility that uses special transport crates and unique identification via RFID chips. “Adapting the control system to meet MTU’s requirements was also time-consuming, but it paid off. Thanks to the high degree of automation, as well as a great deal of expertise in the development of NC programs and innovative machining strategies, we achieve shorter machine operating times and savings in tool costs,” Full says.
The time saving is primarily due to improved processes, as Braun illustrates with an example: “In the past, a worker would load the machine manually with a crane when changing workpieces; today the same process takes only seconds.” This means, she continues, that full automation can ultimately put a big dent in component costs. “We do completely bespoke work with batch sizes of one, realigning the machines for each component we manufacture as part of the setup process.”
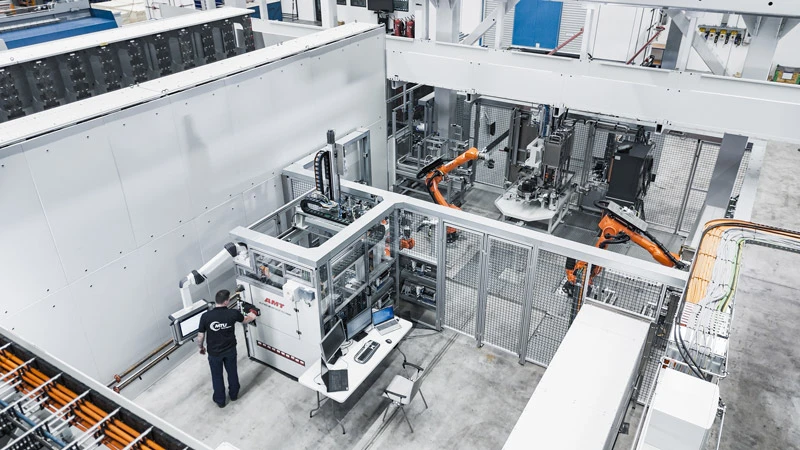
At its site in Munich, MTU has opened a state-of-the-art manufacturing facility that reduces costs and speeds up processes through automation.
Requirements are becoming more diverse
At the same time, the high level of automation has also altered the range of tasks performed by the employees responsible for the facility. Previously, one person would be in charge of a certain number of machines, but employees now take care of a diverse range of tasks. “This makes the work more varied and less monotonous. It ranges from monitoring and troubleshooting to assessing whether the processes are stable and running smoothly,” explains Zeljko Leovac, who heads the facility’s production team.
A reduction in sources of errors was another key consideration while designing the new production line: “With fully automated production, we reduce the risk of handling damage—i.e., those small errors, micro-scratches, and production deviations that either are discovered afterward and have to be rectified or, in the worst case, can lead to a component having to be rejected and not leave the factory,” Leovac says.
Ultimately, the new turbine disk production facility primarily reflects the transformation of an industry that will have to manufacture faster and more efficiently in the coming years. Braun says: “Automation plays a central role in MTU’s strategy for the future. It increases our production capacity and lets us deploy new manufacturing technologies. This will be crucial later on, as we can already see how our involvement in new engine programs will lead to significant growth.”
Intelligent turbine disk production with maximum automation
The new facility at MTU’s Munich site is home to the world’s most cutting-edge production plant for turbine disks. Automated processes enable sustainable manufacturing that conserves resources.
Explore our production interactively: The interactive graphic below guides you through the key stages of our cutting-edge production plant for turbine disks. Click on each element to discover in-depth information on the respective production steps, applied technologies, and our latest innovations.
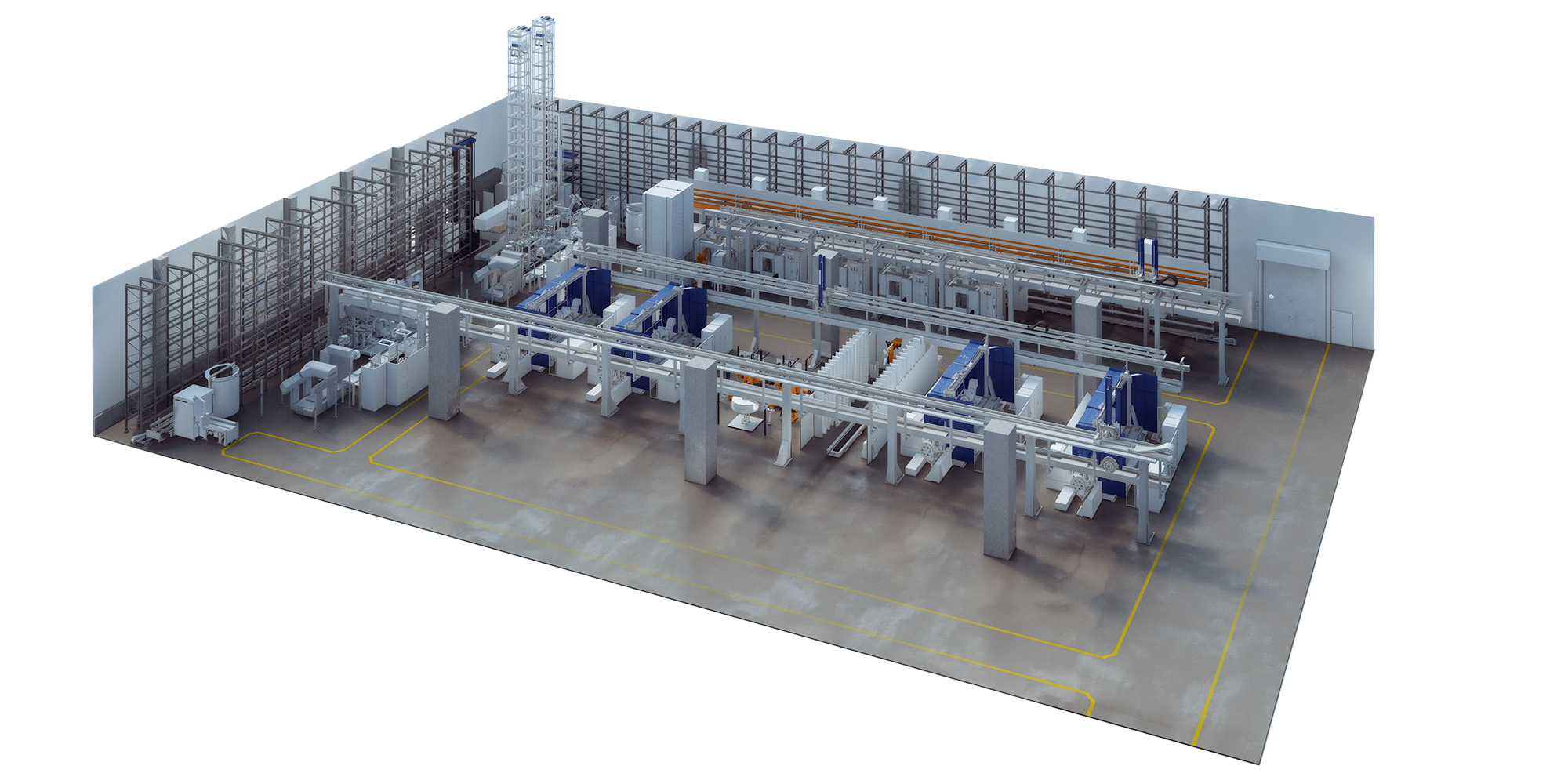
Component storage and fixture for turning
Automatic component setup
Loading components on the machine
Turning tool setup cell
Turning tool storage
Turning process
Component and fixture storage for milling
Milling tool setup
Milling
Component Distribution Station
Component storage and fixture for turning
The blanks, which are pre-turned at MTU’s site in Rzeszów, Poland, are held in a component storage box ready for turning. A fully automated robot removes the component from the box for processing.
back to the hall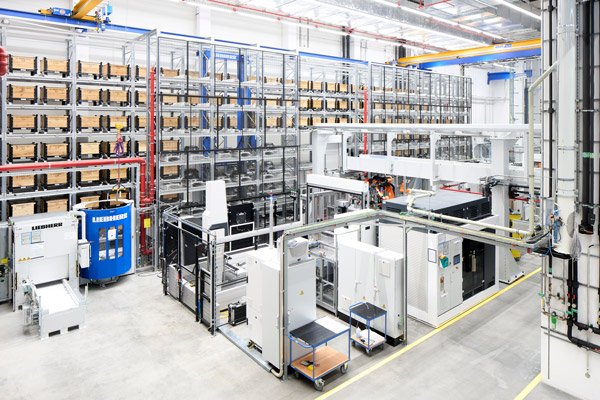
Automatic component setup
For the turning and milling process, a robot helps screw the blanks to the fixture specific to that model. Each turbine disk variant has a matching fixture.
back to the hallHier sehen Sie das automatische Bauteilrüsten beim Drehen.
Loading components on the machine
A gripper transports the component and loads it onto the turning machine. At the same time, the ready-to-use tools are loaded fully automatically. Tools and components are guided separately from each other here—while one component is being released in the machining area, the setup cell is already preparing the next one for the turning process.
back to the hallTurning tool setup cell
For the turning process, the small cutting inserts can be replaced every 37 seconds—the robot takes care of this as well. After use, the inserts are cleaned and prepared for the next time.
back to the hallTurning tool storage
The cutting inserts are stored in the tool storage. For use in the turning process, a robot removes them and places them into a tray, from which they are loaded into the lathe.
back to the hallTurning process
Turning is a closed-door process—no intervention on the part of the operator required.
back to the hallComponent and fixture storage for milling
After being broached in another production facility, the workpiece is returned to the production line by an automated guided vehicle system. There it is also stored by robot in the corresponding component and fixture storage unit.
back to the hall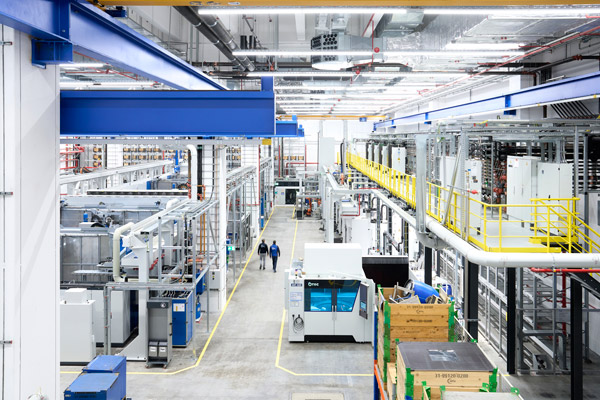
Milling tool setup
For the milling process, too, the workpiece is automatically screwed to the appropriate model-specific fixture with the help of a robot. As in the turning process, each turbine disk variant has a matching fixture.
back to the hall
Milling
The milling process also takes place in the form of a closed-door process without the need for operator intervention. The tools are changed by robots as well.
back to the hallComponent Distribution Station
After turning, the components are transferred to the neighboring hall for broaching before re-turning to the milling process via the distribution station. The component distribution station also functions as an elevator—transporting parts to the inspection area one floor up for intermediate and final inspections.
back to the hall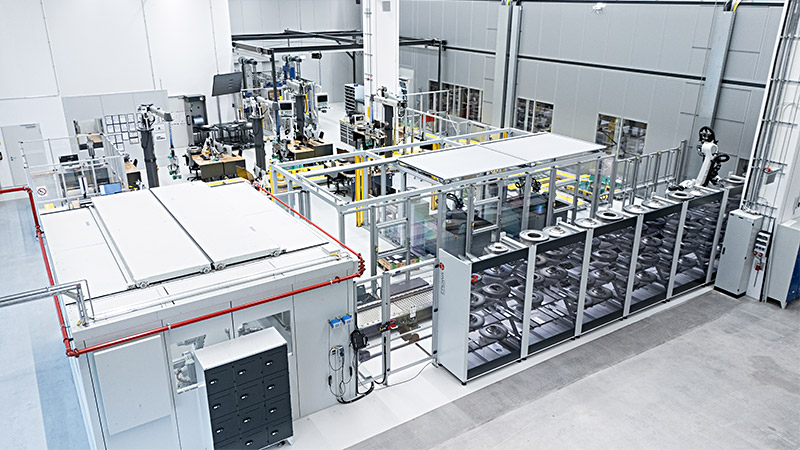