innovation
With GelSight, MTU can measure even the tiniest of flaws
MTU uses the GelSight device to detect and document even small defects, ultimately accelerating engine assembly.
author: Tobias Weidemann | 5 mins reading time published on: 21.03.2023
author:
Tobias Weidemann
has been working as a journalist and content consultant for more than 20 years. He writes about technology and business topics, often with a focus on business IT, digitalization and future technologies.
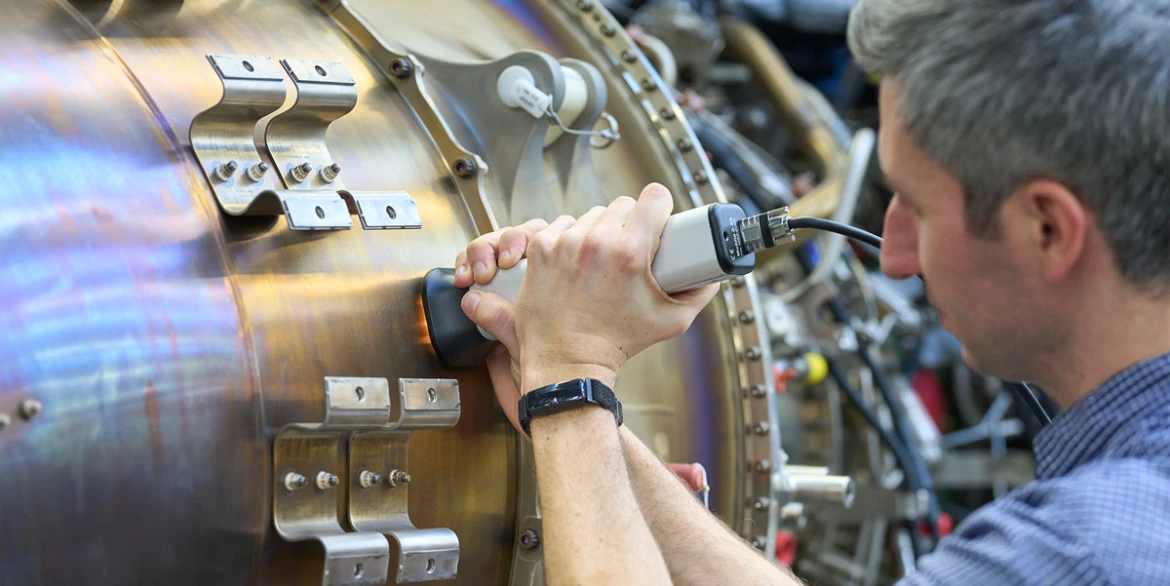
The head of the surface-measuring device glides over a component during final engine assembly. There’s a small scratch; it’s visible to the naked eye but hard to describe—and especially difficult to evaluate. The experience and gut feeling of MTU’s seasoned engine experts are a good indication, but these alone are not enough for a reliable assessment. Is it just a minor flaw, a tool mark on a component? Or could it impair functionality or cause damage later on? Going further, does the part need to be replaced? And if so, will this delay the assembly of the engine, which consists of several thousand components?
To answer these questions, in the past an MTU Aero Engines assembly mechanic would have had to make an impression of the component and then send it to the lab for analysis. There, the lab technicians would measure the anomaly and issue a damage report, which the technical department would use as a basis for making a decision. This report would also be kept for documentation. Alternatively, the component would be replaced as a precautionary measure, which was not in the best interests of costs nor sustainability.
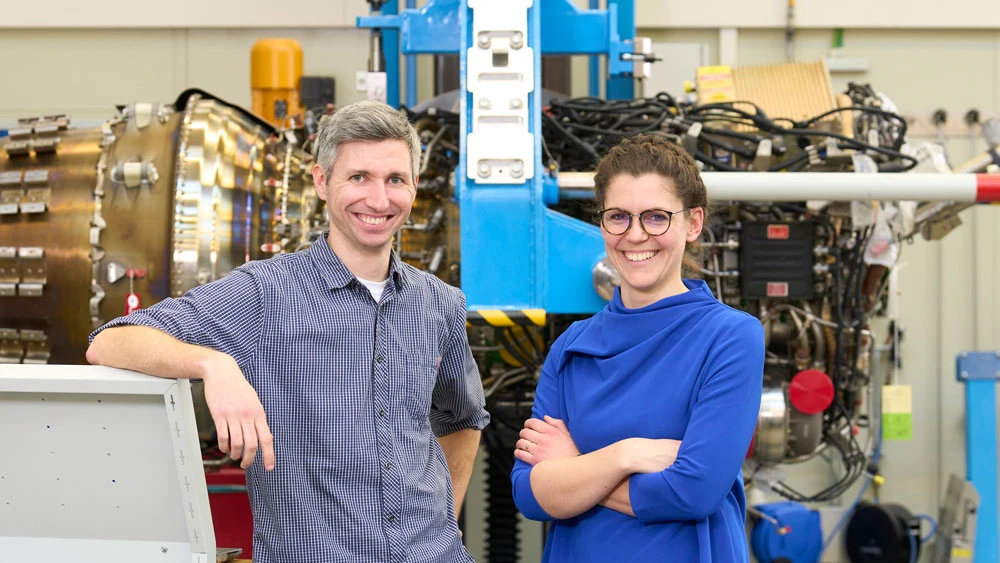
No assembly delays: With GelSight, Julian Mandel and Carmen Pomp found a measurement method that makes engine assembly considerably more efficient.
Either way, this resulted in a significant assembly delay and required that a spare part be available for replacement in the first place. In addition, the engine may have already been on the test stand, so a swap would mean retesting. “All that often took a good deal of time. And if we were unlucky, the assembly of a complete engine would have to wait until the measurement results were available and we had clarity on whether the part could remain installed or not,” explains Carmen Pomp from MTU in Munich. “Even just keeping the engine on ‘hold’ or making it possible to replace a component was a challenge for our assembly teams.”

Measurement of surfaces: The mobile, handy measuring device is pressed against the spot to be examined on the engine. It can also be used to analyze places that are more difficult to reach.
New device accurately measures surface structures
This is precisely where the 3D surface analysis device GelSight Mobile™, which Pomp together with colleagues from different departments helped introduce as an innovation in PW1100G-JM final assembly, comes to the rescue: the high-resolution device can measure the topology of structures in combination with a standard notebook or tablet and the appropriate software. It’s easy to transport to modules consisting of larger parts and can even be operated outside the company network in the interests of data protection. In addition, the device makes it possible to document the degree of deviation from the standard with just a few clicks. This significantly accelerates decision-making processes and shortens timeframes.
The device has a wand like the kind used in medical ultrasounds. At the tip is a round elastomeric gel pad with a diameter of just under two centimeters. When pressed lightly to the component under inspection, this pad conforms to its surface topology and thus creates a precise impression of the area being measured. This works with a variety of materials ranging from reflective to matte, metal to plastic, and can capture and examine even detailed structures and textures. Compared to other optical measuring systems, GelSight allows MTU technicians to cover an area measuring several square centimeters very quickly.
Six LEDs mounted in the wand light up one after the other, producing six individual images at different exposures and from different perspectives within just a few seconds. An algorithm factors out all colors and transparencies as well as reflections and glare, creating a 3D image of the structure. Distilled down to its pure form, this view offers significantly better insights than a conventional microscope. The image can also be rotated, tilted and examined from all perspectives with a manageable amount of graphic processing power. Data obtained this way can be standardized for further processing in other software programs.
If desired, it’s also possible to define a specific target surface level in order to accurately measure a deviation or dent. “In the case of a scratch, for instance, the system measures the highest and lowest points in a defined area,” says Julian Mandel, who was also involved in launching the GelSight system at MTU. Measurement resolution is in the single-digit micrometer range and varies between just four (axial) and eight micrometers (lateral). In describing the order of magnitude, Mandel explains: “This is approximately the thickness of a human hair, which is perfectly sufficient for our requirements.”
Extra calibration procedure put in place
One major hurdle to using GelSight was obtaining metrological approval for it from MTU. To meet the stringent requirements of engine production, the device had to undergo an extensive certification process in accordance with exacting international specifications laid down by the production partners. “The deciding factor was that GelSight reliably produces the same measurement results every time,” Stefan Necker, expert for geometric measurement technology, says. “In cooperation with MTU's calibration department, the MTU’s measurement team has found an adequate solution. A particular challenge for the device manufacturer was the integration of a calibration procedure—a basic requirement for measurement systems in the engine world”.
“Through our collaboration with MTU, we have demonstrated that our tactile sensor technology can be used for aerospace quality assurance and quality control, helping to automate and standardize and significantly speed up these processes.”
CEO at GelSight
The young company from Boston was founded within the Massachusetts Institute of Technology (MIT) environment and is involved in tactile imaging as well as tactile sensor technology. The latter involves, for example, determining the optimal force for a robot to use when gripping or holding a component for processing.
“To meet the high safety standards in aviation, engine experts have traditionally had to perform inspections and complex laboratory measurements that slow down processes and decision making. Using the portable GelSight Mobile system, the MTU team now has the ability to significantly simplify and speed up inspection procedures while arriving at the same sound results about the quality of engine parts,” explains Youssef Benmokhtar, CEO at GelSight. “Through our collaboration with MTU, we have demonstrated that our tactile sensor technology can be used for aerospace quality assurance and quality control, helping to automate and standardize and significantly speed up these processes.”
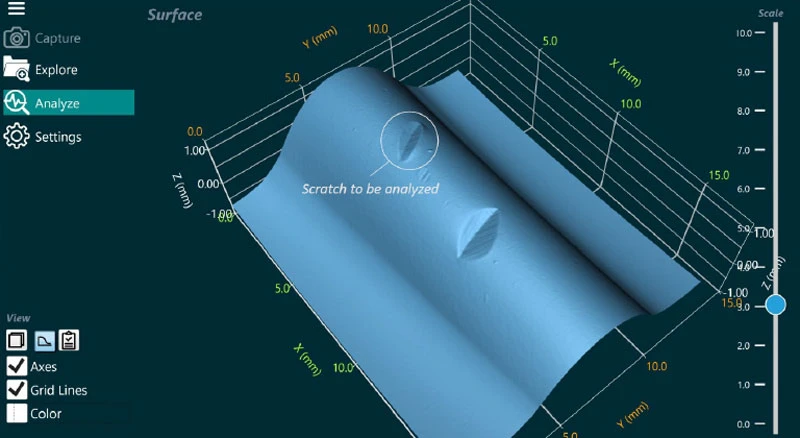
Step 1: The image of the structure of an unevenness can be easily measured with the help of the GelSight measuring device. First, the GelPad is pressed onto the area to be examined. After pressing the trigger, a 3D model is created from the six perspective photos. The location of the damage to be analyzed can now be defined on this model.
Step 2: For the correct assessment of the elevation or indentation, a target surface level is defined against which the area to be assessed is analyzed.
Wide range of applications
Since 2019, the GelSight device has been used at the final assembly lines for the PW1100G-JM engine for the A320neo and the TP400-D6 engine for the A400M. These will not be the only areas where the engine manufacturer relies on GelSight technology. As Mandel says, “We’re already getting visits from colleagues in other departments who want to inspect something quickly.” In addition, the device is already in use in the MTU Maintenance network: at MTU Maintenance Berlin-Brandenburg and at MTU’s Canadian site in Vancouver, GelSight provides support in repair and damage assessment.