innovation
Die Zukunft der Turbinenscheibenfertigung
Die MTU revolutioniert die Turbinenscheibenfertigung: Vollautomatische Prozesse, kürzere Durchlaufzeiten und höchste Präzision.
Autor: Tobias Weidemann | 5 Min. Lesezeit veröffentlicht am: 07.05.2025
Autor:
Tobias Weidemann
ist seit mehr als 20 Jahren als Journalist und Content-Berater tätig. Er berichtet über Technik- und Wirtschaftsthemen, oft mit Schwerpunkt auf Business-IT, Digitalisierung und Zukunftstechnologien.
Ein leises Surren, dann packt der Roboter zu. Millimetergenau greift er nach einem Rohling für eine Turbinenscheibe, positioniert ihn und verschraubt das Bauteil sicher in der Vorrichtung. Auf der anderen Seite der Maschine setzt ein zweiter Roboter die passenden Drehwerkzeuge in den Werkzeughalter ein. Die Rüstzelle ist in der Lage, das verbrauchte Drehwerkzeug etwa alle 37 Sekunden mit einem neuen zu ersetzen. Ist das Werkzeug gerüstet, transportiert ein Greifer das Bauteil und bestückt damit die Drehmaschine. Parallel werden die einsatzfähigen Werkzeuge vollautomatisiert beladen. Dann fährt die Drehmaschine das Werkstück mit den entsprechenden Zerspanungswerkzeugen immer wieder ab und gibt dem Rohling so Schritt für Schritt seine Konturen.
Das Besondere an diesem System: Der gesamte Ablauf ist so optimiert, dass die Maschine komplett ohne Unterbrechung arbeitet. Werkzeuge und Werkstücke werden getrennt voneinander geführt – während ein Bauteil im Bearbeitungsraum entspannt wird, bereitet die Rüstzelle bereits das nächste für den Drehvorgang vor.
Vollständig automatisierter Prozess – bis auf wenige Ausnahmen
Die Art und Weise, wie hier produziert wird, das wird schon auf den ersten Blick klar, unterscheidet sich deutlich von vergleichbaren Anlagen zur Herstellung von Turbinenscheiben. „Es ist die modernste Fertigungshalle für Turbinenscheiben weltweit, weil wir das Rüsten der Bauteile, aber vor allem auch das Rüsten der Werkzeuge vollautomatisiert mit Hilfe von Industrierobotern erledigen können“, berichtet MTU-Projektleiterin Christina Braun. Auch die Unabhängigkeit der einzelnen Bereiche ist ein Alleinstellungsmerkmal der Anlage. „Wir wollten bewusst ein Handlingssystem, das entkoppelt ist vom Maschinenarbeitsraum. Das war in bestehenden Anlagen immer ein begrenzender Faktor, weil der Rüstvorgang für Werkstück und Werkzeuge stets die Maschine blockiert hat.“
Vier Dreh- und vier Fräsmaschinen stehen für die Bearbeitung der Turbinenscheiben bereit. Die Rohlinge, die vom polnischen MTU-Standort in Rzeszów kommen, werden zunächst gedreht und dann zum Räumen in die benachbarte Produktionshalle gebracht. Die anschließende Fräsbearbeitung erfolgt wiederum in der neuen Fertigungshalle. Die Beladung der Werkstücke erfolgt auch hier automatisiert über eine Schleuse, die Werkzeuge werden im Werkzeugspeicher hinter den Maschinen gelagert.
Am Ende des Fräsprozesses wird die Turbinenscheibe entgratet - eine feine Handarbeit, bei der ein kollaborierender Roboter den Menschen unterstützt. Abschließend werden die Turbinenscheiben an anderer Stelle im Werk mit entsprechenden Spezialverfahren behandelt und so zum Beispiel beschichtet, kugelgestrahlt und wärmebehandelt. Danach kehren sie zur Endkontrolle in die Prüfstelle zurück, die sich ein Stockwerk über der Fertigungslinie befindet.
6.000 Niederdruckturbinenscheiben pro Jahr
Bis zu 6.000 Niederdruckturbinenscheiben, zum Beispiel für Getriebefan-Triebwerke des Airbus A320neo, werden hier derzeit pro Jahr gefertigt. „In einer zweiten Ausbaustufe in etwa zehn Jahren könnten es bis zu 12.000 Bauteile pro Jahr sein“, sagt Markus Full, Leiter NC-Programmierung bei der MTU, wobei das Unternehmen in Zukunft auch weitere Varianten für andere Triebwerke fertigen will.
Das Team hat viel Aufwand in die Prozessentwicklung und -optimierung gesteckt, etwa in eine völlig neue Messlösung für die Kalibrierung und Justierung der Maschinen und Roboter. Darüber hinaus kommt ein für die Halle neu entwickeltes System mit speziellen Transportkisten und eindeutiger Identifikation über RFID-Chips zum Einsatz. „Auch die Anpassung des Leitsystems, das die MTU-Anforderungen berücksichtigt, war aufwändig, haben sich aber bezahlt gemacht. Durch den hohen Automatisierungsgrad, aber auch viel Know-how in der Entwicklung von NC-Programmen sowie neuartigen Bearbeitungsstrategien erreichen wir kürzere Maschinenlaufzeiten und Einsparungen bei den Werkzeugkosten“, so Full.
Diese Zeitersparnis ist vor allem auf verbesserte Prozesse zurückzuführen, wie Christina Braun an einem Beispiel verdeutlicht: „Früher hat ein Werker beim Werkstückwechsel die Maschine manuell mit dem Kran beladen, heute ist das eine Sache von Sekunden.“ Unterm Strich, rechnet die Projektleiterin vor, können durch den Grad der Vollautomatisierung somit eine signifikante Reduktion der Bauteilkosten erreicht werden. „Wir arbeiten komplett individuell mit Losgröße 1, richten also die Maschinen im Rahmen des Rüstvorgangs für jedes gefertigte Bauteil neu aus.“
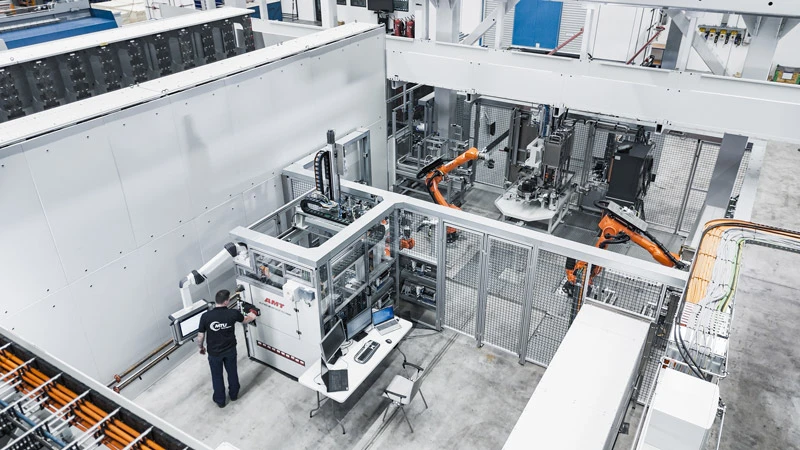
Am MTU-Standort in München wurde eine hochmoderne Fertigung in Betrieb genommen, die dank Automatisierung Kosten senkt und Prozesse beschleunigt.
Anforderungsprofil wird vielfältiger
Allerdings hat sich angesichts des hohen Automatisierungsgrades auch das Aufgabenspektrum der Mitarbeiter:innen, die für die Anlage zuständig sind, gewandelt. Anders als früher ist nicht ein Mitarbeiter für eine bestimmte Anzahl von Maschinen zuständig, sondern kümmert sich agil um verschiedene Aufgaben. „Die Arbeit wird dadurch vielfältiger und abwechslungsreicher. Sie reicht vom Überwachen über das Beheben von Störungen bis hin zum Beurteilen, ob die Prozesse stabil laufen“, erklärt Zeljko Leovac, der als Betreiber der Halle das Fertigungsteam leitet.
Auch die Reduzierung von Fehlerquellen spielte bei der Konzeption der neuen Fertigungslinie eine wichtige Rolle: „Mit der vollautomatischen Produktion riskieren wir weniger Handling Damages - also jene kleinen Fehler, Mikrokratzer und Produktionsabweichungen, die entweder im Nachhinein entdeckt und behoben werden müssen oder im schlimmsten Fall dazu führen können, dass ein Bauteil aussortiert werden muss und das Werk nicht verlässt“, so Leovac.
Letztlich spiegelt die neue Turbinenscheibenfertigung vor allem den Wandel einer Branche wider, die in den nächsten Jahren schneller und effizienter produzieren muss. Braun: „Die Automatisierung spielt in der Zukunftsstrategie der MTU eine zentrale Rolle: Sie erhöht die Kapazität in unserer Fertigung und ermöglicht den Einsatz neuer Fertigungstechnologien. Denn schon heute ist absehbar, dass durch unsere Beteiligung an neuen Triebwerksprogrammen ein deutliches Wachstum bevorsteht.“
Intelligente Turbinenscheibenfertigung mit Höchstmaß an Automation
In der neuen Halle des MTU-Standorts München findet sich die modernste Produktionsstätte für Turbinenscheiben weltweit. Automatisierte Prozesse ermöglichen eine nachhaltige und ressourcenschonende Produktion.
Entdecken Sie die Fertigung interaktiv: In der nachfolgenden Grafik haben Sie die Möglichkeit, die einzelnen Stationen unserer hochautomatisierten Turbinenscheibenfertigung interaktiv zu erkunden. Klicken Sie auf die einzelnen Punkte, um mehr über die jeweiligen Fertigungsschritte, Technologien und Innovationen zu erfahren.
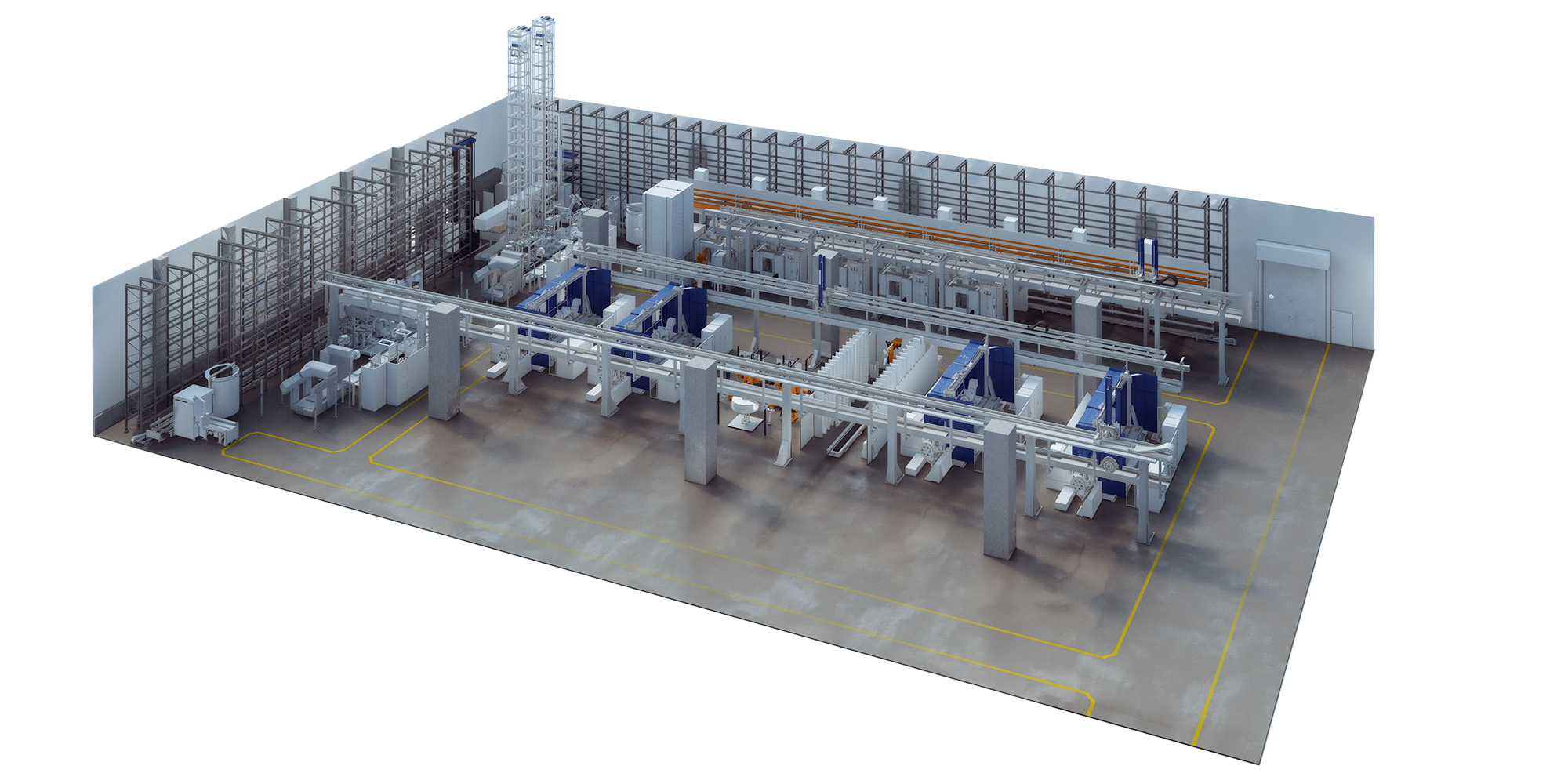
Bauteilspeicher und Vorrichtung fürs Drehen
Automatisches Bauteilrüsten
Maschinenbeladung von Bauteilen
Werkzeugrüstzelle Drehen
Drehwerkzeugspeicher
Drehprozess
Bauteil- und Vorrichtungsspeicher fürs Fräsen
Werkzeugrüstzelle Fräsen
Bearbeitung Fräsen
Bauteilverteilstation
Bauteilspeicher und Vorrichtung fürs Drehen
Die am polnischen MTU-Standort in Rzeszów vorgedrehten Rohlinge werden für den Drehvorgang in einer Kiste im Bauteilspeicher eingelagert. Die Bauteile werden für die Bearbeitung von einem Roboter vollautomatisiert aus der Kiste entnommen.
zurück zur Halle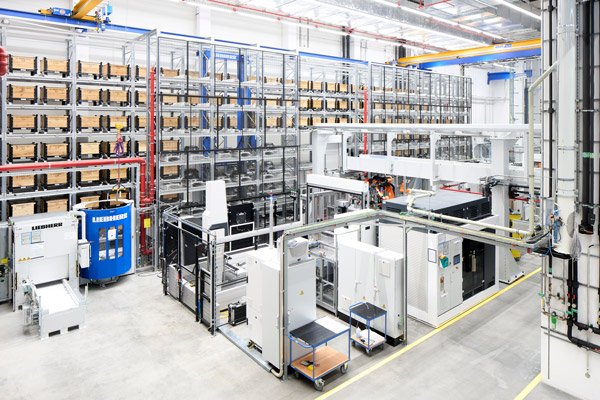
Automatisches Bauteilrüsten
Für den Dreh- und Fräsprozess werden die Rohlinge mit Hilfe eines Roboters mit der jeweils modellspezifischen Vorrichtung verschraubt. Für die verschiedenen Turbinenscheibenvarianten gibt es hier jeweils die passenden Vorrichtungen.
zurück zur HalleHier sehen Sie das automatische Bauteilrüsten beim Drehen.
Maschinenbeladung von Bauteilen
Ein Greifer transportiert das Bauteil und bestückt damit die Drehmaschine. Parallel werden die einsatzfähigen Werkzeuge vollautomatisiert beladen. Werkzeuge und Werkstücke werden hier getrennt voneinander geführt – während ein Bauteil im Bearbeitungsraum entspannt wird, bereitet die Rüstzelle bereits das nächste für den Drehvorgang vor.
zurück zur HalleWerkzeugrüstzelle Drehen
Beim Drehen können die kleinen Schneidplatten alle 37 Sekunden getauscht werden – auch das übernimmt der Roboter. Nach der Verwendung werden die Schneidplatten gereinigt und für den nächsten Einsatz vorbereitet.
zurück zur HalleDrehwerkzeugspeicher
Im Werkzeugspeicher werden die Schneidplatten eingelagert. Für ihren Einsatz beim Drehen entnimmt ein Roboter sie und führt sie in eine Ablage, von wo aus sie in die Drehmaschine beladen werden können.
zurück zur HalleDrehprozess
Der Drehvorgang findet als Closed-Door-Vorgang statt, ohne dass ein Bediener in den Prozess eingreifen muss.
zurück zur HalleBauteil- und Vorrichtungsspeicher fürs Fräsen
Das Werkstück gelangt nach dem Räumen in einer anderen Produktionshalle per fahrerlosen Transportsystems zurück in die Fertigungslinie. Dort wird es ebenfalls per Roboter in den entsprechenden Bauteil- und Vorrichtungsspeicher abgelegt.
zurück zur Halle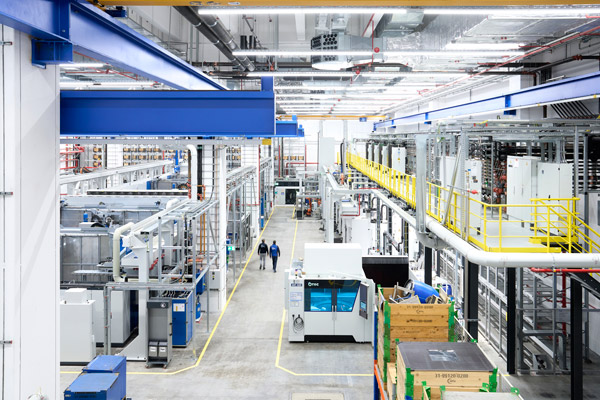
Werkzeugrüstzelle Fräsen
Beim Fräsen müssen die Werkzeuge regelmäßig getauscht und gereinigt werden. Das übernimmt wiederum ein Roboter, der Werkzeugspeicher befindet sich hinter der Maschine.
zurück zur Halle
Bearbeitung Fräsen
Auch der Fräsvorgang findet in Form eines Closed-Door-Prozesses statt, ohne dass ein Eingreifen von Mitarbeiter:innen erforderlich ist. Der Werkzeugwechsel erfolgt ebenso durch Roboter.
zurück zur HalleBauteilverteilstation
Nach dem Drehen werden die Bauteile in die benachbarte Halle zum Räumen gebracht, bevor sie über die Station wieder für den Fräsvorgang zurückkehren. Die Bauteilverteilstation fungiert allerdings auch als Aufzug: Dann, wenn die Bauteile zur Zwischen- und Schlusskontrolle ein Stockwerk höher in die Prüfstelle müssen.
zurück zur Halle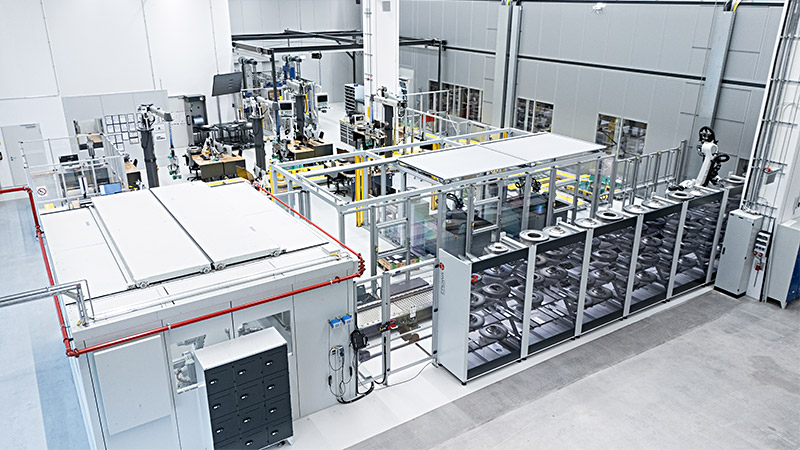