innovation
The virtual engine
In the future, MTU wants to use digital twins to virtually map an engine’s entire lifecycle—from development to flight operations.
author: Tobias Weidemann | 6 mins reading time updated on: 21.05.2025
author:
Tobias Weidemann
has been working as a journalist and content consultant for more than 20 years. He writes about technology and business topics, often with a focus on business IT, digitalization and future technologies.
Virtual Engine:
A virtual engine is a virtual version of a physical engine. It comprises the “as-designed twin,” the “as-built twin,” the “as-used twin,” and the digital thread that runs through the object’s entire lifecycle. Creating and assessing a virtual engine calls for special skills, tools, processes, and data.
Aircraft engines are high-tech products in a class of their own. Back when passenger air travel was in its infancy, engineers would spend long periods hunched over the drawing board to design these complex machines. The introduction of computers simplified and speeded up the process immensely. Development work is constantly progressing, with collaboration among the various technical disciplines involved in developing an engine working particularly well in the virtual world. That makes it easier to coordinate the various product requirements. The primary focus for MTU Aero Engines here is on developing future engines such as the second generation of the geared turbofan, which MTU is creating together with partner Pratt & Whitney, or the New Generation Fighter Engine in the military sector.
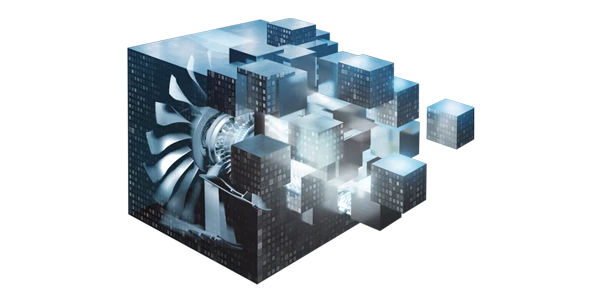
As-designed twin: The as-designed twin describes a product’s geometry and behavior based on target data gathered from analytics and its design.
As-built twin: The as-built twin describes the geometry and behavior of a specific, real product and contains all deviations that occurred during manufacture and assembly.
As-used twin: The as-used twin maps a product’s geometry and behavior during operation. It features deviations resulting from operational wear and damage.
Digital thread: The digital thread maps the data flow over a product’s entire lifecycle.
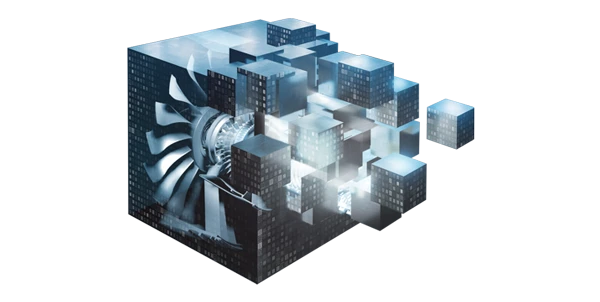
Digital twin for future engine development
For some time, MTU’s propulsion engineers have been working on the virtual engine, which is made up of a series of digital twins. A digital twin is much more than a static model that provides a snapshot of a particular stage in development. Rather, it’s a virtual representation that tracks how a given product has evolved over time. A digital twin allows developers to simulate an unlimited number of scenarios and draw conclusions about product development, manufacture, operation, and maintenance.
First to emerge is the “as-designed twin,” which describes what the ideal product should be like. This is used to plan the manufacture and assembly of the real product. With the data gathered from this physical product, the engineers can create a virtual “as-built twin.” That means the as-built twin isn’t an exact copy of the as-designed twin, but differs from it in several respects, since it reflects all deviations that occurred during manufacture and assembly.
Having both these digital twins available makes it possible to analyze how they differ. As a result, the engineers can determine whether or not the finished product not only fulfills stringent quality and efficiency requirements, but is also cost-effective to manufacture and maintain. The next step is for the as-built twin to go through acceptance testing and internal validation before being used in flight operations. Any wear and damage that occurs during these operations represents further deviations and is documented in what’s called the “as-used twin.”
Charting the evolution of every engine over its entire lifecycle means that each one also exists as a virtual engine and the associated digital thread, which maps the data flow over a product’s entire lifecycle. That means each engine has its own traceable life story, which over time steadily moves away from its original as-designed twin. The sum total of all these deviations, and all the associated data, ultimately allow the engine experts to draw conclusions about how a product will perform in the future. In turn, they can predict when the engine will require maintenance and gauge when it would make sense to issue a recommendation to the maintenance support team with a view to optimizing the planning of the scope of work.
A virtual engine is a virtual version of a physical engine. It comprises the “as-designed twin,” the “as-built twin,” the “as-used twin,” and the digital thread that runs through the object’s entire lifecycle. Creating and assessing a virtual engine calls for special skills, tools, processes, and data. In the future, MTU wants to use digital twins to virtually map an engine’s entire lifecycle—from development to flight operations.
Processing massive datasets
Predictions like these are based on vast amounts of data—and evaluating it calls for comprehensive models. Ensuring access to all the relevant data at all times is a challenge, due to the need to harmonize the different data systems used for analytics, design, production, and flight operations. The digital thread plays a key role here as the sum of all the data that links the individual phases and disciplines.
Three factors will be crucial to achieving success here in the years ahead: a high level of automation in gathering, providing, and processing data; a high degree of collaboration and networking; and interdisciplinary processes within the company. In addition, digital twins will play an important role. Whether physics- or data-based, they can help make forecasts and analyses more precise. At present, data-based digital twins are used in the early phase of engine development—in structural mechanics, for instance, when a component’s natural vibrations are assessed. The aim now is to gradually build up the knowledge required to ultimately allow the complete analysis and optimization of a complex engine.
Customizing engines through virtualization
One of MTU’s first lighthouse projects concerns the digital twin for compressor blades. Aerodynamics and structural mechanics have an antagonistic relationship, and there’s always a need to reconcile the two. While the interests of aerodynamics are served by having blades with edges that are particularly thin and sharp, structural mechanics’ pursuit of robustness calls for thicker, more rounded components. This is the tightrope that developers must walk.
That is why aerodynamics and structural mechanics have been designated as key processes in designing blades for compressors. In the medium term, MTU wants this approach to accelerate and enhance product design as well as to reduce costs. In the near future, it will be possible to automate the optimization of any target variable and develop products that are suitable for each use case. That optimization always involves balancing the technical requirements, such as efficiency and weight, with the manufacturing and maintenance costs. And, of course, the product must be sufficiently robust.
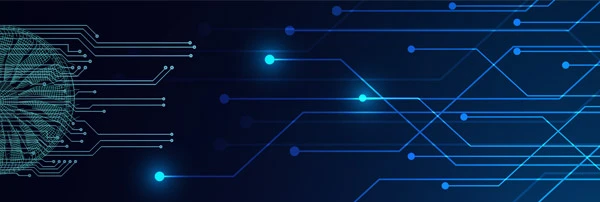
Following the digital thread
MTU’s main focus in this area is currently still on the as-designed twin in other words, on the development processes in engineering and on data transparency between technical departments. In the medium term, the focus will shift more toward production and operations, which will involve the as-built and as-used twins. The aim is to draw a comprehensive picture of the entire digital thread—from development to production and operations to decommissioning. To this end, at the beginning of 2024, MTU set up a dedicated team of experts to coordinate the virtual engine agenda and drive it forward in collaboration with the various technical departments.
MTU is receiving active support from research institutions. One of these is the Institute of Test and Simulation for Gas Turbines run by the German Aerospace Center (DLR), where innovations are first developed and tested on the laboratory scale before they are rolled out to the industry.
End-to-end digitalization in development, manufacturing, and maintenance offers companies a huge opportunity—but it also poses challenges. For MTU’s engine experts across various technical disciplines, this means questioning familiar ways of working. A digital mindset and data-based thought processes are increasingly taking center stage. There’s still a long way to go before the vision of capturing and mapping an entire engine and its functions in the virtual world can be realized. But the MTU experts are already working step by step to make the “virtual engine” a reality.