innovation
Das virtuelle Triebwerk
Mit Hilfe digitaler Zwillinge will die MTU in Zukunft den gesamten Lebenszyklus eines Triebwerks virtuell abbilden und weiter optimieren – von der Entwicklung bis hin zum Flugbetrieb.
Autor: Tobias Weidemann | 6 Min. Lesezeit aktualisiert am: 21.05.2025
Autor:
Tobias Weidemann
ist seit mehr als 20 Jahren als Journalist und Content-Berater tätig. Er berichtet über Technik- und Wirtschaftsthemen, oft mit Schwerpunkt auf Business-IT, Digitalisierung und Zukunftstechnologien.
Virtual Engine:
Eine Virtual Engine ist das virtuelle Abbild eines physischen Triebwerks bestehend aus dem ‚As Designed Twin‘, ‚As Built Twin‘ und ‚As Used Twin‘ sowie dem digitalen Faden über den Lebenszyklus des Gegenstands hinweg. Für die Erstellung und Bewertung der Virtual Engine werden spezielle Fähigkeiten, Tools, Prozesse und Daten benötigt.
Luftfahrtantriebe sind Hochtechnologie der Extraklasse. Während sich in den Anfängen der Passagierluftfahrt die Ingenieur:innen noch mühsam über Zeichentische beugten, um diese komplexen Maschinen auszulegen, hat die Einführung des Computers diese Prozesse wesentlich vereinfacht und beschleunigt. Die Entwicklung schreitet kontinuierlich voran, wobei das interdisziplinäre Zusammenspiel der verschiedenen Fachdisziplinen, die an einer Triebwerksentwicklung beteiligt sind, in der virtuellen Welt besser erfolgen kann. Dadurch lassen sich die jeweiligen Anforderungen an das Produkt besser in Einklang bringen. Die MTU Aero Engines hat dabei besonders die Entwicklung der zukünftigen Triebwerke im Blick, etwa die zweite Generation des Getriebefans, den die MTU zusammen mit Pratt & Whitney realisiert oder im militärischen Bereich die New Generation Fighter Engine.
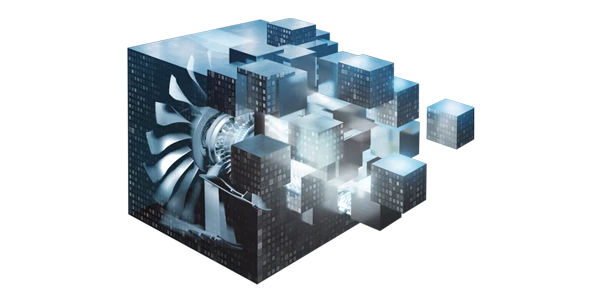
As Designed Twin: Das ist der Soll-Zwilling, der Geometrie und Verhalten eines Produkts auf Basis von Soll-Daten aus Analytik und Design beschreibt.
As Built Twin: Dieser Ist-Zwilling beschreibt Geometrie und Verhalten eines individuellen und realen Produkts und enthält alle Abweichungen aus Fertigung und Montage des Produkts.
As Used Twin: Darunter versteht man einen Ist-Zwilling, der Geometrie und Verhalten eines Produktes im Betrieb darstellt. Er enthält Abweichungen durch Schädigung und Alterung im Betrieb.
Digitaler Faden (Digital Thread): Das ist der Datenfluss über den gesamten Lebenszyklus eines Produkts.
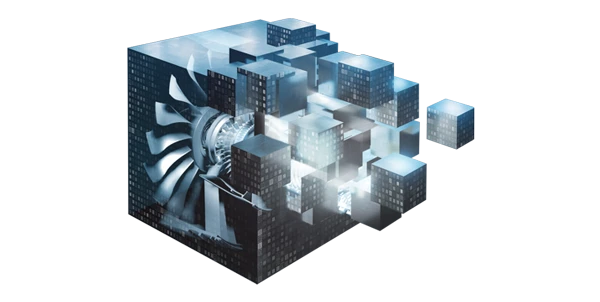
Digitaler Zwilling für die zukünftige Triebwerksentwicklung
Bereits seit einiger Zeit arbeiten bei der MTU Triebwerksingenieur:innen an der „Virtual Engine“, also am virtuellen Abbild eines Triebwerks bestehend aus verschiedenen sogenannten digitalen Zwillingen. Ein digitaler Zwilling ist dabei mehr als ein statisches Modell zu einem bestimmten Zeitpunkt. Vielmehr handelt es sich um die virtuelle Darstellung der Produkte mit ihren Veränderungen über die Zeit. Ein digitaler Zwilling erlaubt den Entwickler:innen, beliebige Szenarien zu simulieren und daraus Rückschlüsse auf Entwicklung, Herstellung, Betrieb und Erhalt des Produkts zu ziehen.
Im ersten Schritt entsteht der sogenannte Soll-Zwilling (‚As Designed Twin‘), der beschreibt, wie das ideale Produkt aussehen soll – dementsprechend wird dann die Fertigung und Montage des realen Produkts ausgelegt. Im zweiten Schritt werden die Daten des realen Produkts zum virtuellen Fertigungszwilling (‚As Built Twin‘) zusammengefasst. Dieser Fertigungszwilling entspricht nicht mehr haargenau dem Soll-Zwilling, sondern weicht in einigen Punkten davon ab, da er die Abweichungen aus Fertigung und Montage berücksichtigt.
Hat man beide Zwillinge in virtueller Form vorliegen, können die Abweichungen analysiert werden. So lässt sich ableiten, ob das fertige Produkt sowohl die hohen Anforderungen an Effizienz und Qualität, als auch eine kostengünstige Fertigung und Instandhaltung erlaubt. Im nächsten Schritt geht der ‚As Built Twin‘ in den Abnahmelauf und in die interne Validierung, danach in den „Flugbetrieb“: Die im Flugbetrieb auftretenden Abnutzungen und Beschädigungen stellen weitere Abweichungen dar und werden im sogenannten ‚As Used Twin‘ festgehalten.
Auf diese Weise ergibt sich im Laufe des Lebenszyklus‘ eines jeden Triebwerks eine Virtual Engine mit dem dazugehörigen digitalen Faden (Digital Thread): Das ist der Datenfluss über den gesamten Lebenszyklus eines Produkts. Jedes Triebwerk hat dabei seine eigene, nachvollziehbare Lebensgeschichte, die sich im Laufe der Zeit immer individueller vom ursprünglichen Soll-Zwilling unterscheidet. Die Summe aller Abweichungen und die damit verbundenen Daten erlauben schließlich Rückschlüsse darauf, wie sich ein Produkt in Zukunft verhal-ten wird. Die Triebwerksexpert:innen können dann sehen, wann eine Instandhaltung angebracht ist und wann eine Empfehlung für den Instandhaltungs-Support ratsam wäre, um die Planung des Arbeitsumfang zu optimieren.
Eine Virtual Engine ist das virtuelle Abbild eines physischen Triebwerks bestehend aus dem „As Designed Twin“, „As Built Twin“ und „As Used Twin“ sowie dem digitalen Faden über den Lebenszyklus des Gegenstands hinweg. Für die Erstellung und Bewertung der Virtual Engine werden spezielle Fähigkeiten, Tools, Prozesse und Daten benötigt. Mit Hilfe digitaler Zwillinge will die MTU in Zukunft den gesamten Lebenszyklus eines Triebwerks virtuell abbilden und weiter optimieren – von der Entwicklung bis hin zum Flugbetrieb.
Immense Datenbestände zu verarbeiten
Solche Voraussagen basieren auf einer immensen Fülle an Daten und benötigen umfangreiche Modelle zu deren Auswertung. Die Herausforderung besteht darin, dass die Analytik, Konstruktion und Fertigung sowie der Betrieb jeweils eigene Datensysteme nutzen, die miteinander in Einklang gebracht werden müssen, um jederzeit Zugriff auf alle relevanten Daten zu gewährleisten. Hier spielt der digitale Faden eine wichtige Rolle als Summe aller Daten, der die einzelnen Phasen und Disziplinen miteinander verknüpft.
Drei entscheidende Faktoren tragen in den kommenden Jahren zum Erfolg bei: ein hoher Grad an Automatisierung bei der Aufnahme, Bereitstellung und Verarbeitung von Daten, ein hoher Grad an Vernetzung sowie interdisziplinäre Prozesse im Unternehmen. Darüber hinaus spielen digitale Zwillinge eine wichtige Rolle. Ob physik- oder datenbasiert, sie können dazu beitragen, dass die Prognosen und Analysen präziser werden. Datenbasierte Digitale Zwillinge befinden sich in der Triebwerksentwicklung derzeit noch in der Anfangsphase, etwa bei der Strukturmechanik, wenn Eigenschwingungen von Bauteilen bewertet werden. Nun sollen schrittweise mehr Erkenntnisse gewonnen werden, damit am Ende auch ein komplexes Triebwerk komplett analysiert und optimiert werden kann.
Maßgeschneidertes Triebwerk dank Virtualisierung
Ein erstes MTU-Leuchtturmprojekt ist der digitale Zwilling für die Beschaufelung eines Verdichters. Aerodynamik und Strukturmechanik stehen in einem antagonistischen Verhältnis und müssen ständig in Einklang gebracht werden. Während etwa die Schaufeln im Interesse der Aerodynamik besonders scharfe, dünne Kanten aufweisen sollten, erfordert die Strukturmechanik aus Gründen der Robustheit eher runde und dicke Bauelemente. Ein Spagat, den die Entwickler:innen leisten müssen.
Deshalb habe man sich in der Verdichterbeschaufelung die Aerodynamik und Strukturmechanik als Schlüsselprozesse vorgenommen. Mittelfristig will die MTU damit die Produktauslegung beschleunigen und verbessern sowie Kosten sparen. In naher Zukunft wird es dann möglich sein, automatisiert auf beliebige Zielgrößen hin zu optimieren und Produkte zu entwickeln, die für jeden Einsatzbereich geeignet sind. Das Spannungsfeld der Optimierung besteht dabei immer wieder aus den technischen Anforderungen, wie zum Beispiel Wirkungsgrad und Gewicht, sowie den Herstell- und Instandhaltungskosten. Und natürlich muss das Produkt ausreichend robust sein.
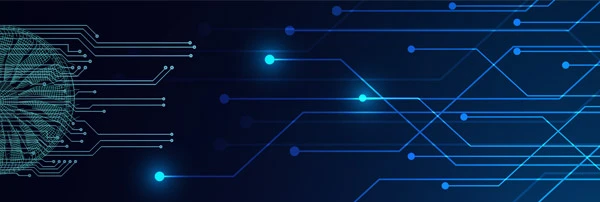
Digitalen Faden nachvollziehen
Noch konzentriert man sich bei der MTU vor allem auf den Soll-Zwilling, also die Entwicklungsprozesse im Engineering und die Datentransparenz zwischen den Fach-Abteilungen. Mittelfristig soll der Schwerpunkt eher auf den Bereichen Fertigung und Betrieb liegen, also den Ist-Zwillingen. Ziel ist es, ein umfassendes Bild des gesamten digitalen Fadens zu erhalten – von der Entwicklung über die Fertigung und den Betrieb bis hin zur Außerbetriebnahme. Dafür wurde Anfang 2024 ein eigenes Expertenteam bei der MTU gegründet, das in Zusammenarbeit mit den Fachabteilungen die Belange der Virtual Engine koordiniert und vorantreibt.
Tatkräftige Unterstützung erhält die MTU von Forschungseinrichtungen, wie dem Institut ‚Test und Simulation in der Gasturbine‘ des Deutschen Luft- und Raumfahrtzentrum (DLR). Hier werden Neuerungen zunächst im Labormaßstab entwickelt und getestet, bevor sie in der Industrie zur Anwendung kommen.
End-to-End-Digitalisierung in Entwicklung, Fertigung und Instandhaltung bietet für Unternehmen große Chancen – bringt aber auch Herausforderungen mit sich. Für die Triebwerksexpert:innen der MTU aus verschiedenen Fachrichtungen bedeutet dies, gewohnte Arbeitsweisen zu hinterfragen. Ein digitales Mindset und datenbasiertes Denken rücken dabei zunehmend in den Mittelpunkt. Bis zur Vision, das komplette Triebwerk und seine Funktionalitäten im Ganzen zu erfassen und in der virtuellen Welt abzubilden, ist es noch ein weiter Weg. Doch die MTU-Expert:innen arbeiten bereits Schritt für Schritt daran, die „Virtual Engine“ Realität werden zu lassen.