innovation
Innovative quality inspection of turbine disks
The new test center at MTU’s Munich site shows how humans and robots can work together efficiently and with precision on quality assurance for turbine disks.
4 mins reading time published on: 16.05.2025
As MTU project planner Martin Gschwendtner walks through the company’s turbine disk production test center in Munich, he notices how quiet it is. There aren’t many employees to be seen; just an e-cart driving around with a component. This transport system, affectionately dubbed “conveyor-belt sushi” by the team, brings the turbine disks to the employees’ workstations for final visual inspection after the measuring process. The 900-square-meter test center, which opened in summer 2024, is unique in the world in its level of automation and digitalization. “The machines here can run fully automatically around the clock,” Gschwendtner says.
Over the next few years, turbine disks for various engine types, such as the PW800 for business jets or the geared turbofan for the Airbus A320neo, will be inspected and tested here.
A range of testing procedures for components
In principle, a component passes through the test center twice: once for the intermediate test and once for the final inspection. After the disks have been turned and milled one floor below, a transport system specially developed for the facility brings them up to the test center via elevator. The RFID chip on the transport crate provides information about which component is involved. Chain conveyors and conveyor belts automatically transport each component to the shelf system, which can store up to 274 turbine disks at the same time.
As soon as the component is stored in the shelf system, the test center’s control system can request the crate with the component for the inspection process, while the robot automatically supplies the appropriate fixture. An employee gets the component set up within a few minutes. By comparison, the next step—the inspection process on the machine—takes up to four hours; this generally requires no human intervention. The robot then automatically removes the component from the measuring machine, which moves on to the next workpiece. A separate cell is used to label the component with a measurement. This measurement aids the detection of deviations later during maintenance. Here, too, the robot guides the component automatically. The turbine disk is then placed on an optical measuring device on which various radii and edges are checked by a collaborative robot arm with a 3D measuring sensor.
You may also be interested in following content
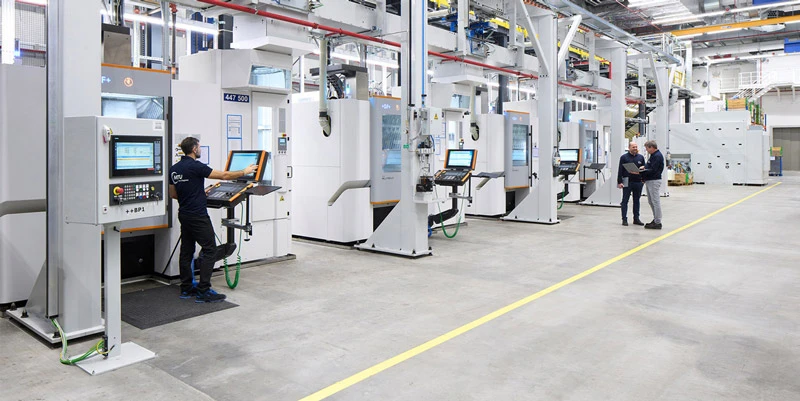
Turbine disk production: MTU is revolutionizing turbine disk production: fully automated processes, shorter turnaround times, and maximum precision.
Putting parts through their paces
After the robot has automatically unloaded the component, it places it on an e-cart, which takes the turbine disk to the inspectors’ workstations. There, a visual inspector takes one last close look at the component; the trained eye is particularly useful in places that are difficult for cameras to see. “Once finished, the inspector gives final approval for installation in the engine,” says Hüseyin Hirlak, team leader at the test center. “This task carries a great deal of responsibility and requires a lot of experience and precision.” At facilities where there’s still a low level of automation, inspectors perform logistical tasks in addition to visual inspections. “In the new test center, by contrast, certain processes have been carefully selected for automation, allowing employees to concentrate even more on their core competence: the meticulous assessment of component quality.”
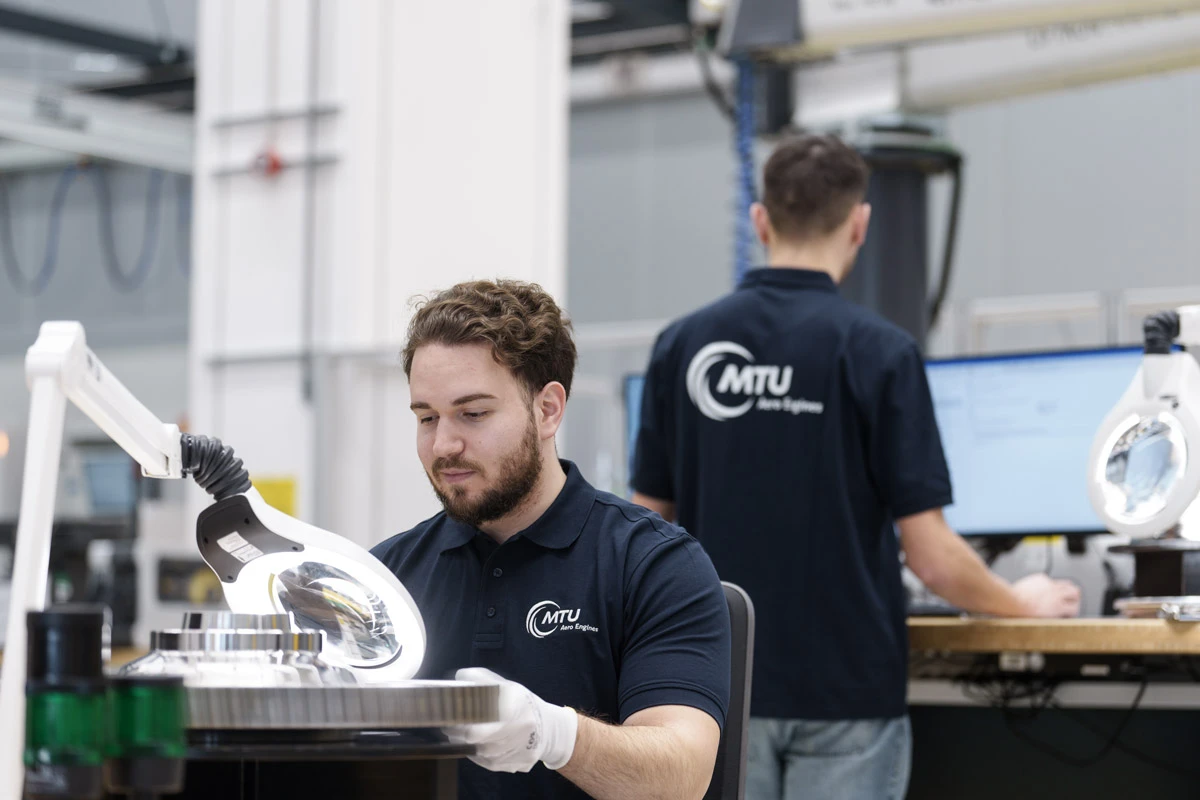
The employee inspects everything again in detail with a trained eye.
Project manager Christian Ewert sums it up when he says: “The bottom line here is, we’ve created one of the world’s most cutting-edge measurement lines in turbine disk production.” Regarding the technology, it was a team effort. The NC programs (NC = Numerical Control) come from MTU itself, while the machines are based on solutions from a whole range of proven partners.
The facility shows where developments in manufacturing and final inspection are heading: automation will be used wherever it can actively support employees in a variety of auxiliary tasks.
Details of the new test center for turbine disks: Getting the optimum component step by step
MTU in Munich is home to a state-of-the-art test center for manufactured turbine disks. Here, humans and machines work together efficiently - with the goal of leaving nothing in turbine disk inspection to chance.
Explore our new test center interactively: The interactive graphic below guides you through the key stages of our innovative quality inspection of turbine disks. Click on each element to discover in-depth information on the respective production steps, applied technologies, and our latest innovations.
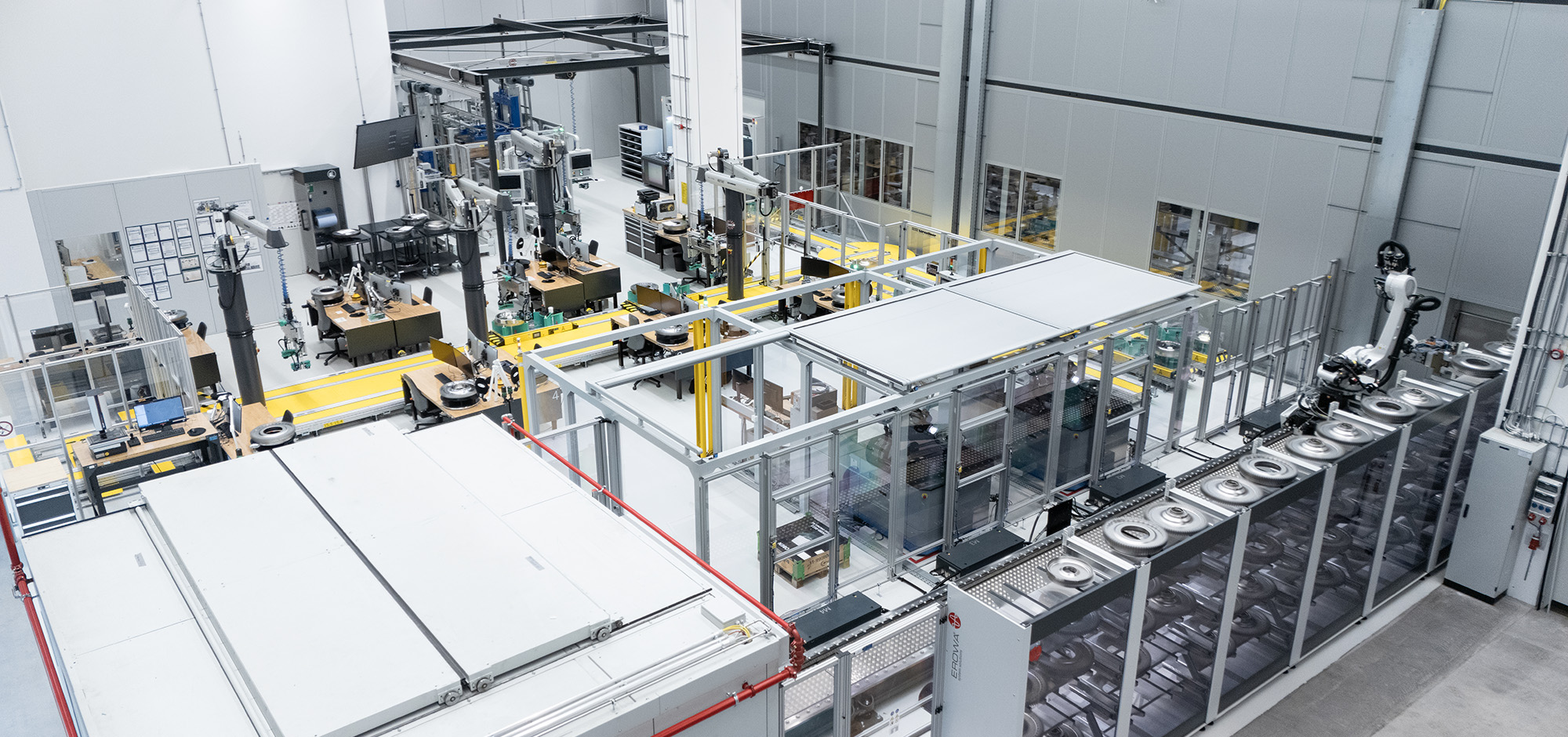
Delivery and storage
Order processing and setup
Component measurement and unloading
Labeling
Optical analysis
Running Sushi
Visual inspection
Delivery and storage
Upon delivery, the component is transported to the test center using an elevator. Here, the RFID chip on the transport crates (which were made especially for the system) is read, and the component is taken via chain conveyors and conveyor belts to be stored in one of the 274 spaces.
back to the hall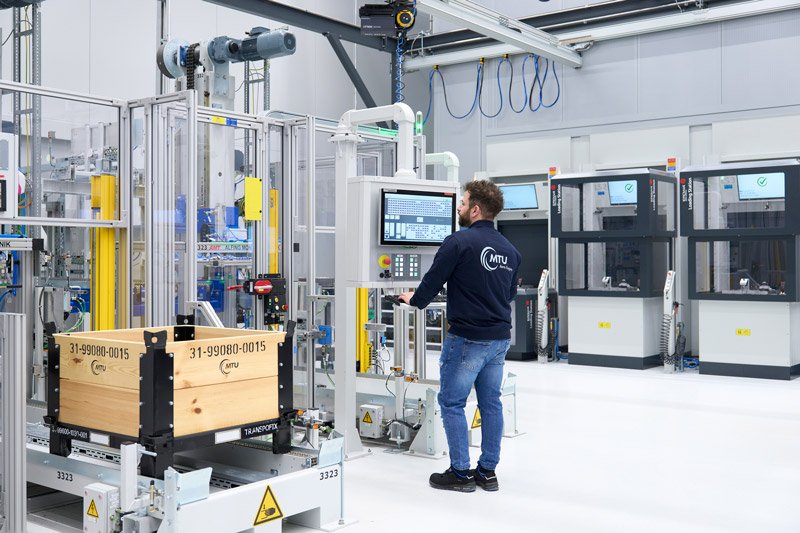
Order processing and setup
The test center’s control system automatically requests the component from the shelf system for processing on the coordinate measuring machine. The robot automatically supplies the correct fixture for this. An employee then sets up the component manually within a few minutes. Human input is essential here, as the employee inspects the component during setup for contamination from the transport process.
back to the hall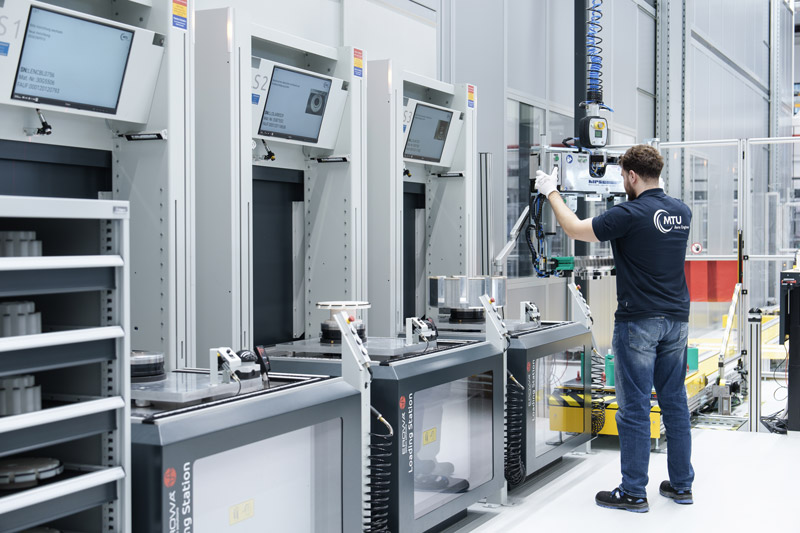
Component measurement and unloading
A robot then transfers the turbine disk to the coordinate measuring machine, which measures the disk from all sides in a process lasting up to four hours. The disk is then automatically unloaded again by the robot. Test sequences can vary depending on the quality of the component.
back to the hallLabeling
Although the component is already engraved with a serial number, in the next step it’s placed in a separate cell to be labeled with a measurement that was previously recorded on the coordinate measuring machine. This measurement aids the detection of deviations later during maintenance. Here, too, the robot acts autonomously and guides the component without human intervention.
back to the hall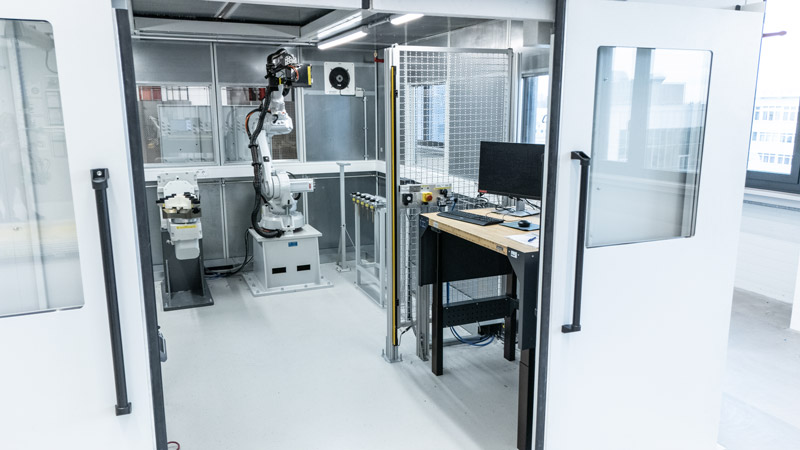
Optical analysis
The turbine disk is then placed on an optical measuring device on which various radii and edges are checked by a collaborative robot arm with a 3D measuring sensor.
back to the hallRunning Sushi
The component is transported via floor-moving eCarts to the employees' workstations after the inspection processes. There, the final visual inspection and approval of the components take place.
back to the hallVisual inspection
Finally, the robot delivers the component to the employee’s inspection station via an automatic transport system. The employee inspects everything again in detail with a trained eye. If any anomalies are detected, the employee checks whether these are still within the norm or if further corrective action needs to be taken.
back to the hall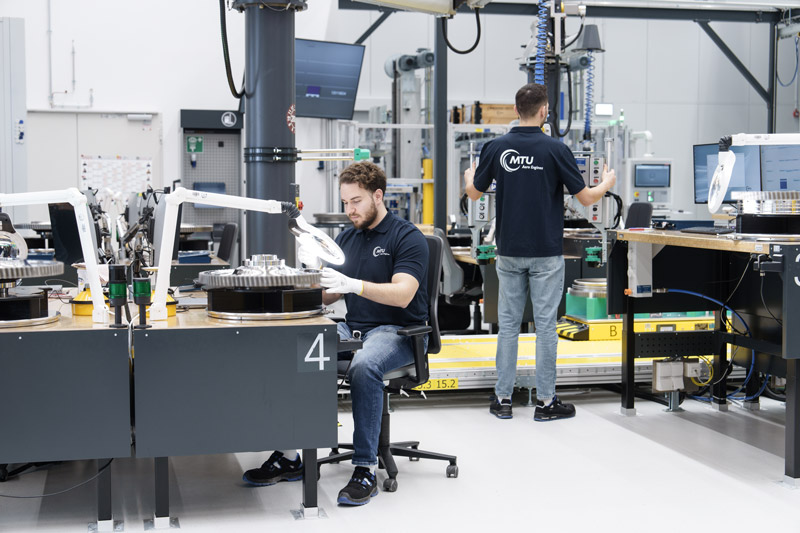