innovation
Efficient and highly integrated: Automated guided vehicle systems at MTU
These autonomous helpers play an important role in the increasing automation of the material flow in complex logistics and engine production.
author: Nicole Geffert | 6 mins reading time published on: 16.01.2025
author:
Nicole Geffert
has been working as a freelance journalist covering topics such as research and science, money and taxes, and education and careers since 1999.
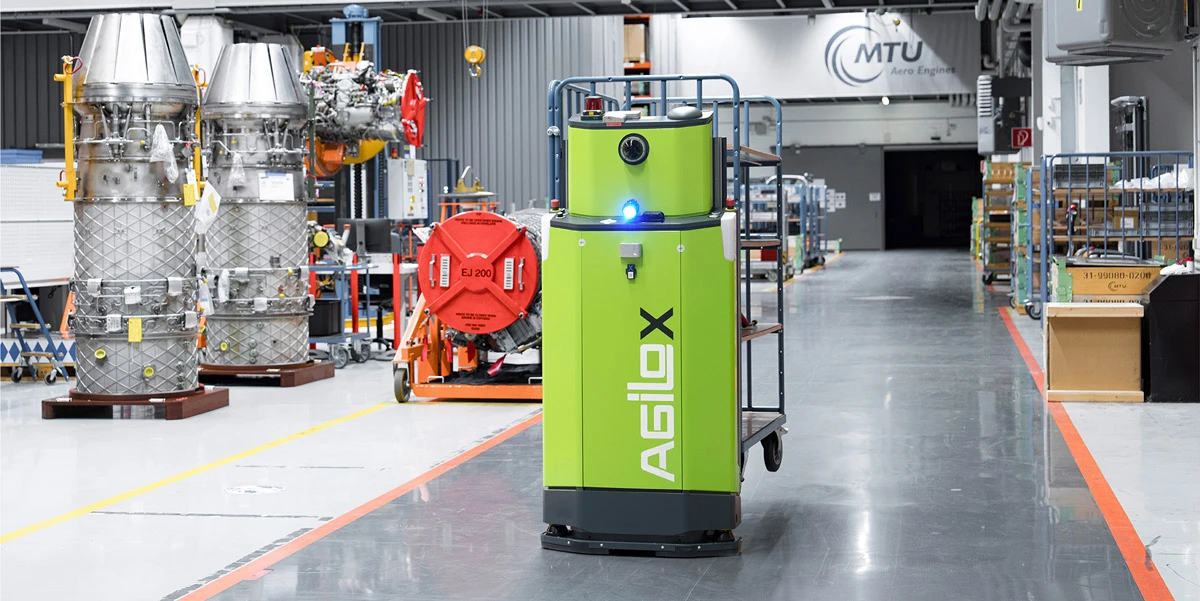
Production is running at full speed in MTU Aero Engines’ spacious manufacturing and logistics facilities. Three autonomous helpers make their way between engine specialists and imposing production equipment, gliding unobtrusively but purposefully across the shop floor in Munich and Erding. Their names are “Lena”, “Denki” and “Yoda”—automated guided vehicles (AGVs) with the job of transporting high-quality engine components from one workstation to another.
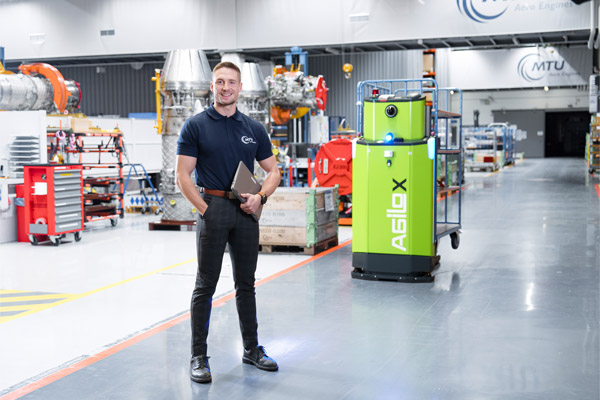
“As we continue to automate the material stream, AGV systems play an important role in optimizing material flow and efficiency. When it comes to AGV system innovation in the aviation industry, MTU is a pioneer.”
Logistics manager and AGV expert at MTU
Each AGV follows a precise route and is programmed to reliably meet the exacting demands of engine production and maintenance. “As we continue to automate the material stream, AGV systems play an important role in optimizing material flow and efficiency,” says Philipp Schmuttermayr, a logistics manager and AGV expert at MTU. “When it comes to AGV system innovation in the aviation industry, MTU is a pioneer.”
While AGV systems have long been standard in the automotive sector, they’re still an exception in the world of aviation. “Our working environment is different to high-volume automotive production, because aircraft engine components are subject to rigorous certification, whereas in the automotive industry processes are more standardized across the board. Such processes make it easier to integrate AGV systems into existing production and logistics systems,” explains Benjamin Hofmann, an AGV system project manager in MTU production. “Manufacturing at MTU, on the other hand, is more like a craftsman’s workshop. It involves many highly specialized processes, which is a challenge for the use of AGV systems.”
In addition, the safety-critical engine components are very expensive. “The cost of goods on a load being transported through the facility can quickly add up to one million euros,” Schmuttermayr says. If an engine disk were to fall off the vehicle, that would immediately make it unusable and, in the worst case, it would have to be destroyed.
All this had to be taken into account when Schmuttermayr and his team launched the first AGV system project in intralogistics at MTU in Munich in 2020. “Intralogistics” covers all logistical material and goods flows on the factory premises. The team’s aim was to optimize internal transport so that material flow and production would become even more efficient. Their project began with extensive tests of AGV systems from various manufacturers. In the end, they opted for the AGV system from Austrian start-up Agilox.
Automated guided vehicle (AGV) systems are indispensable in digitally controlled manufacturing. MTU uses them in its highly specialized engine production, making the company a pioneer in the aviation industry.
“Lena” optimizes the transport route
The AGV system, with the Lena vehicle, was successfully tested and introduced in 2021 at the MTU site in Erding, east of Munich. Erding handles assembly and repair for, among others, the EJ200 for the Eurofighter Typhoon of the German Armed Forces, the RB199 for the Tornado, the T408 for the Sikorsky CH-53K transport helicopter, and the MTR390 for the Tiger helicopter. The site hosts two facilities for maintenance and logistics, which cover more than 10,000 square meters.
Lucas Leifheit works as a team coordinator in Erding and was involved in introducing and testing the AGV system. “Previously, a logistics employee drove the factory train—a forklift truck with wagons—through the facility four to five times a day on a fixed route, stopping at individual workstations to unload or load components,” he says. “Lena makes us faster because she can respond more flexibly.”
In other words, Lena heads directly to the areas that need a component or want to dispatch one, which saves time and money. The employees request the AGV at the click of a mouse. Lena optimizes the transport route herself and processes orders in the most efficient sequence.
Logistics specialists supervise AGV systems
“People quickly recognized the advantages,” Schmuttermayr says. “The AGV system is in use around the clock. Waiting times are shorter and work processes are getting more efficient.” The AGVs are also able to communicate with each other. If, for example, something is blocking one of the routes, an AGV can pass this information on to the other vehicles. Lena also generates alternative routes to avoid a blockage and get to her destination.
“The system relieves the burden on our employees, which is important to us,” Leifheit says. “That’s why we integrated them into the project right from the start, so we could test and build it together.” The logistics specialists who previously drove the factory train can now concentrate on new, more specialized tasks.
They’ve had further training and are now taking on the role of AGV system supervisor. For example, they ensure that the AGV systems are always ready for use. “Compared to the bulky factory train, the AGVs take up less space and increase safety at work,” Leifheit says. By scanning the entire environment with sensors, Lena ensures there are no collisions with objects or people.
Wireless infrastructure in manufacturing
Implementing AGV systems, such as Lena in Erding or Denki and Yoda in Munich, in highly specialized engine production is a challenge—including for MTU’s IT specialists. “To be able to operate an AGV system, we had to set up an extended wireless infrastructure throughout the facility,” says Michael Leicht, an industrial IT planner at MTU. “Such infrastructure in logistics and production areas is more complex and implementation is more challenging than in a purely office environment.” This is especially true when it also involves integration into military aviation operations such as those in Erding, which are subject to special security requirements. Individual MTU-specific solutions were required here.
MTU aims to fully integrate the AGVs into its IT systems. Ultimately, the goal is to map a fully connected goods flow and link it to a complete digital system—part of the pursuit of Industry 4.0. “AGV systems are a key linking step on the path toward digitally controlled manufacturing, as they increase connectivity and efficiency in production,” Schmuttermayr says.
Trackers for more transparency
Each wagon that the AGV system transports through the facilities is equipped with a tracker. Since the track and trace system can locate all produced components in real time, it ensures greater transparency and efficiency in the production network. “As a result, employees always know where the component that they’re expecting or have dispatched is located,” Leifheit says.
AGV systems are now in use at MTU locations worldwide; one of these is the world’s most modern turbine disk production facility, which MTU recently opened in Munich. AGV systems have also been implemented at the MTU Maintenance sites in Hannover and Zhuhai. There are plans to deploy further systems at MTU Maintenance Berlin-Brandenburg and at the MTU sites in Poland and Serbia. A cross-location MTU team specializing in AGV system innovation ensures the exchange of know-how.
Incidentally, the unusual names "Lena", "Yoda" and "Denki" come from the manufacturer Agilox and the MTU colleagues. Instead of “I’ll put in a request for the AGV,” workers simply say: “I’ll call Denki.”