innovation
Innovative Qualitätsprüfung für Turbinenscheiben
Die neue Prüfstelle am MTU-Standort München zeigt, wie Mensch und Roboter in der Qualitätssicherung für Turbinenscheiben effizient und präzise zusammenarbeiten.
Autor: Tobias Weidemann | 4 Min. Lesezeit veröffentlicht am: 16.05.2025
Autor:
Tobias Weidemann
ist seit mehr als 20 Jahren als Journalist und Content-Berater tätig. Er berichtet über Technik- und Wirtschaftsthemen, oft mit Schwerpunkt auf Business-IT, Digitalisierung und Zukunftstechnologien.
Geht man mit MTU-Projektplaner Martin Gschwendtner durch die Prüfstelle der Turbinenscheibenfertigung der MTU in München, ist man überrascht über die Ruhe. Viele Mitarbeiter:innen sind nicht zu sehen, lediglich ein eCart fährt mit einem Bauteil herum. „Running Sushi“ nennt das Team liebevoll das Transportsystem, das die Turbinenscheiben zur finalen Sichtprüfung an die Arbeitsplätze der Mitarbeiter:innen bringt. Die 900 Quadratmeter große Prüfstelle, die im Sommer 2024 eröffnet wurde, ist in ihrem Automatisierungs- und Digitalisierungsgrad weltweit einmalig. „Die Maschinen können rund um die Uhr vollautomatisch laufen“, berichtet Gschwendtner.
Hier werden in den nächsten Jahren Turbinenscheiben für verschiedene Typen wie den Businessjet-Antrieb PW800 oder den Getriebefan für den Airbus A320neo begutachtet und geprüft.
Unterschiedliche Prüfverfahren für die Bauteile
Grundsätzlich durchläuft ein Bauteil die Prüfstelle zweimal – einmal zur Zwischen- und einmal zur Schlussprüfung. Nachdem die Scheiben eine Etage tiefer gedreht und gefräst wurden, bringt ein eigens dafür entwickeltes Transportsystem sie über einen Aufzug nach oben in die Prüfstelle. Der RFID-Chip an der Transportkiste zeigt an, um welches Bauteil es sich handelt. Über Kettenförderer und Förderbänder kommt jedes Bauteil automatisch in das Regalsystem. Bis zu 274 Turbinenscheiben können dort gleichzeitig gelagert werden.
Sobald das Bauteil im Regalsystem eingelagert ist, kann das Leitsystem der Prüfstelle die Kiste mit dem Bauteil für den Prüfvorgang anfordern, währenddessen bringt der Roboter automatisch die passende Vorrichtung. Innerhalb weniger Minuten rüstet ein Mitarbeiter das Bauteil auf. Bis zu vier Stunden dauert dagegen der Prüfvorgang an der Maschine, der in der Regel ohne menschliches Zutun auskommt. Danach entnimmt der Roboter das Bauteil wieder automatisch aus der Messmaschine, die sich dem nächsten Werkstück widmet. In einer separaten Zelle erfolgt die Kennzeichnung. Dort wird das Bauteil mit einem Maß versehen. Dieses hilft später in der Instandhaltung, Abweichungen zu erkennen. Auch hier führt der Roboter das Bauteil automatisch zu. Anschließend wird die Turbinenscheibe auf ein optisches Messgerät gebracht. Dort prüft ein kollaborativer Roboterarm mit einem 3D-Messsensor diverse Radien und Kanten.
Dieser Inhalt könnte Sie auch interessieren
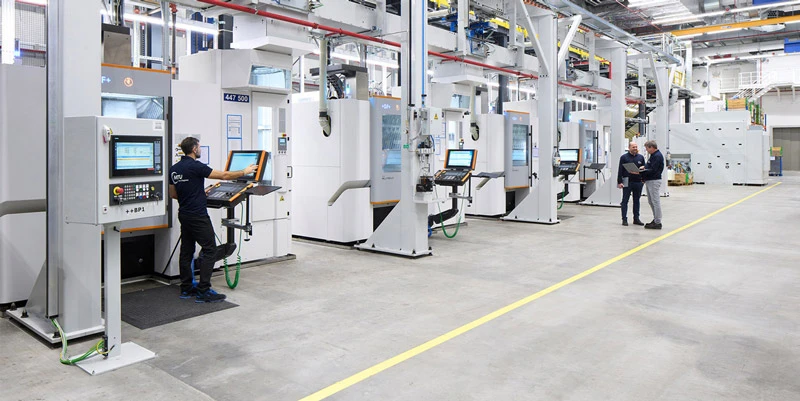
Turbinenscheibenfertigung: Am MTU-Standort in München wurde eine hochmoderne Fertigung in Betrieb genommen, die dank Automatisierung Kosten senkt und Prozesse beschleunigt.
Auf Herz und Niere prüfen
Nachdem der Roboter das Bauteil automatisch entladen und auf ein eCart gelegt hat, bringt dieses die Turbinenscheibe zu den Arbeitsplätzen der Prüfer. Dort nimmt ein Sichtprüfer das Bauteil ein letztes Mal genau unter die Lupe – besonders an Stellen, die für Kameras schwer einsehbar sind, kommt der geschulte Blick besser zum Einsatz. „Am Ende gibt der Prüfer seine finale Zustimmung für die Montage in das Triebwerk. Eine sehr verantwortungsvolle Aufgabe, die viel Erfahrung und Präzision erfordert“, sagt Hüseyin Hirlak, Teamleiter der Prüfstelle. Wo bislang an vielen Stellen noch ein geringerer Automatisierungsgrad herrscht, übernehmen Prüfer neben der Sichtprüfung auch logistische Aufgaben. „In der neuen Prüfstelle hingegen werden diese Prozesse gezielt automatisiert – so können sich die Mitarbeiter:innen noch stärker auf ihre Kernkompetenz konzentrieren: die sorgfältige Beurteilung der Bauteilqualität.“
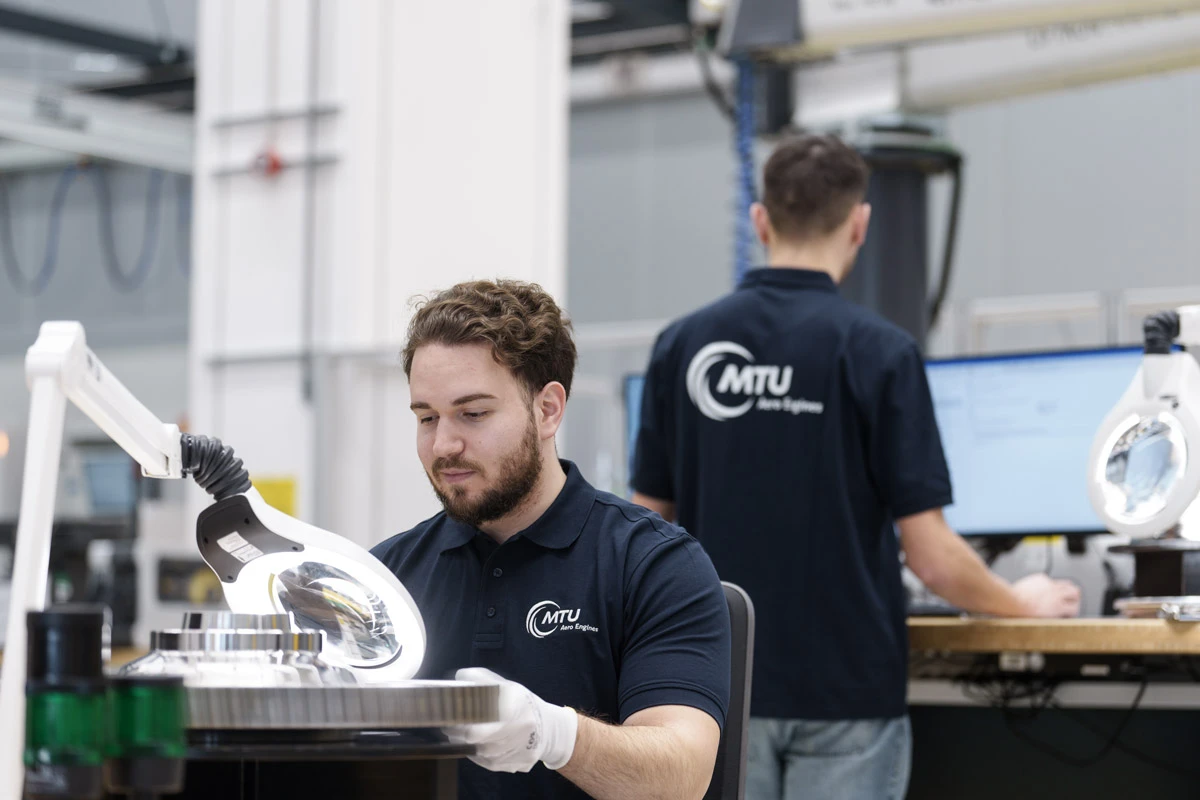
Die Mitarbeiter:innen begutachten mit geschultem Auge nochmals alles im Detail.
Projektleiter Christian Ewert fasst zusammen: „Unterm Strich ist hier eine der weltweit modernsten Messlinien in der Fertigung von Turbinenscheiben entstanden.“ Eine technologische Teamleistung: Die NC-Programme (NC = Numerical Control) stammen von der MTU selbst, bei den Maschinen setzte man auf Lösungen einer ganzen Reihe bewährter Partnerfirmen.
Die Anlage zeigt, wohin die Entwicklung in der Fertigung und Endkontrolle geht: Automatisierung wird überall dort eingesetzt, wo sie die Mitarbeiter:innen bei einer Vielzahl von Hilfsaufgaben tatkräftig unterstützen kann.
Die neue Prüfstelle für Turbinenscheiben im Detail: Schritt für Schritt zum optimalen Bauteil
Bei der MTU in München befindet sich eine State-of-the-Art-Prüfstelle für gefertigte Turbinenscheiben. Hier arbeiten Mensch und Maschine effizient zusammen – mit dem Ziel, bei der Begutachtung der Turbinenscheiben nichts dem Zufall zu überlassen.
Entdecken Sie die neue Prüfstelle interaktiv: In der nachfolgenden Grafik haben Sie die Möglichkeit, die einzelnen Stationen unserer innovative Qualitätsprüfung für Turbinenscheiben interaktiv zu erkunden. Klicken Sie auf die einzelnen Punkte, um mehr über die jeweiligen Fertigungsschritte, Technologien und Innovationen zu erfahren.
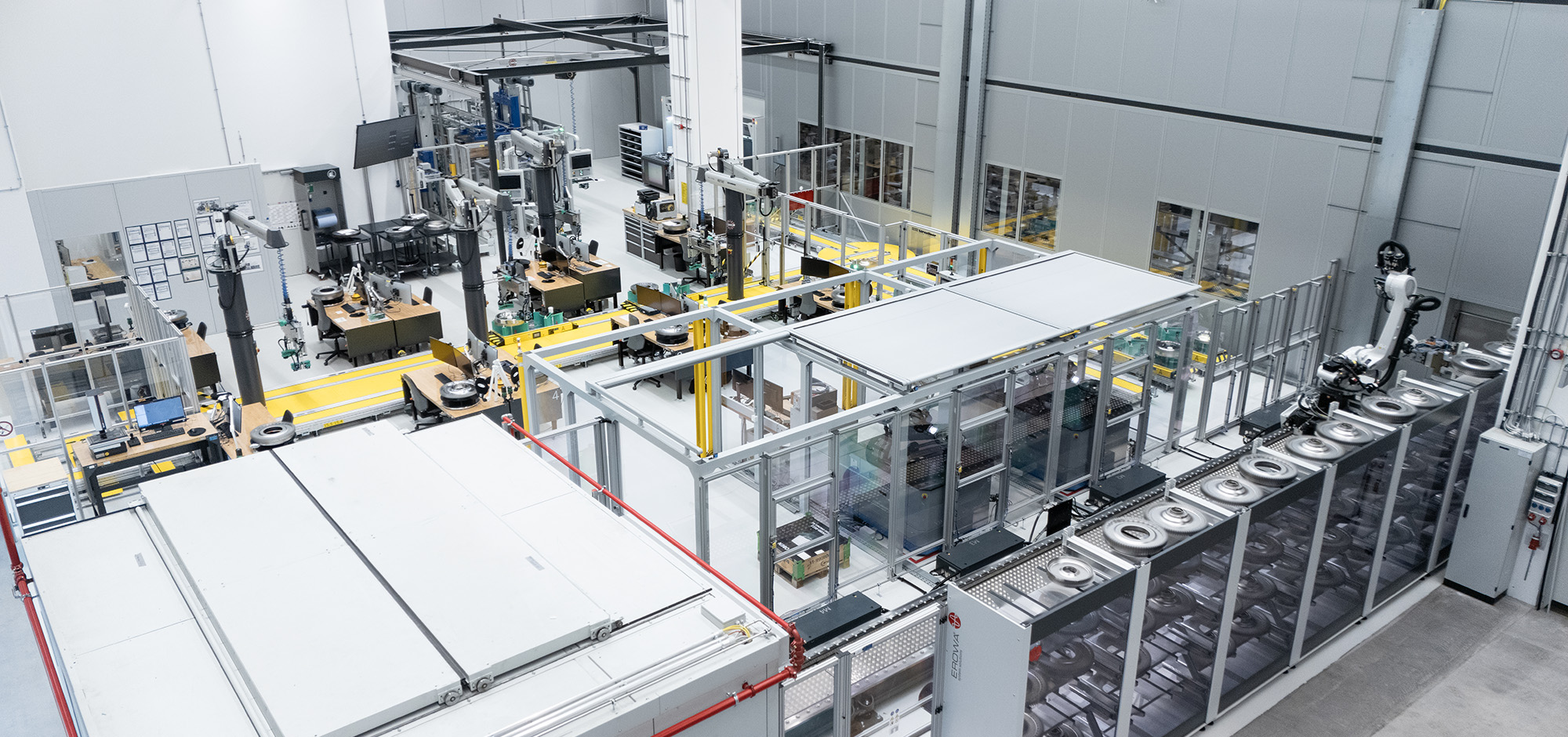
Anlieferung und Einlagerung
Auftragsbearbeitung und Rüsten
Bauteilmessung und -entladung
Kennzeichnung
Optische Analyse
'Running Sushi'
Sichtprüfung
Anlieferung und Einlagerung
Bei der Anlieferung wird das Bauteil mit einem Transporthilfsmittel über einen Aufzug zur Prüfstelle gebracht. Hier wird der RFID-Chip auf den speziell für die Anlage gefertigten Transportkisten ausgelesen und das Bauteil danach über Kettenbeförderer und Förderbänder auf einem der 274 Plätze eingelagert.
zurück zur Messhalle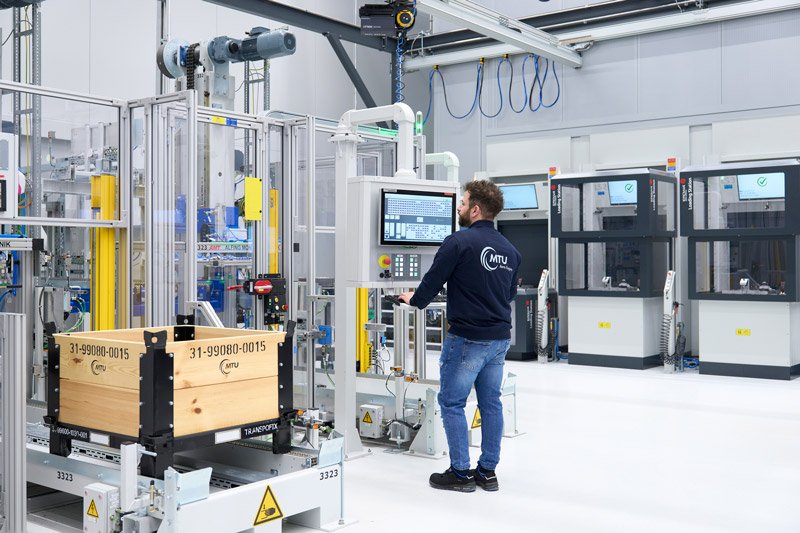
Auftragsbearbeitung und Rüsten
Für die Bearbeitung auf dem Koordinatenmessgerät fordert das Prüfstellenleitsystem das Bauteil automatisch im Regalsystem an. Der Roboter stellt hierfür automatisch die richtige Vorrichtung bereit. Innerhalb weniger Minuten wird das Bauteil dann durch einen Mitarbeiter manuell aufgerüstet. Die menschliche Zuarbeit ist hier essentiell, da der Mitarbeiter beim Aufrüsten das Bauteil auf Verschmutzungen durch den Transport untersucht.
zurück zur Messhalle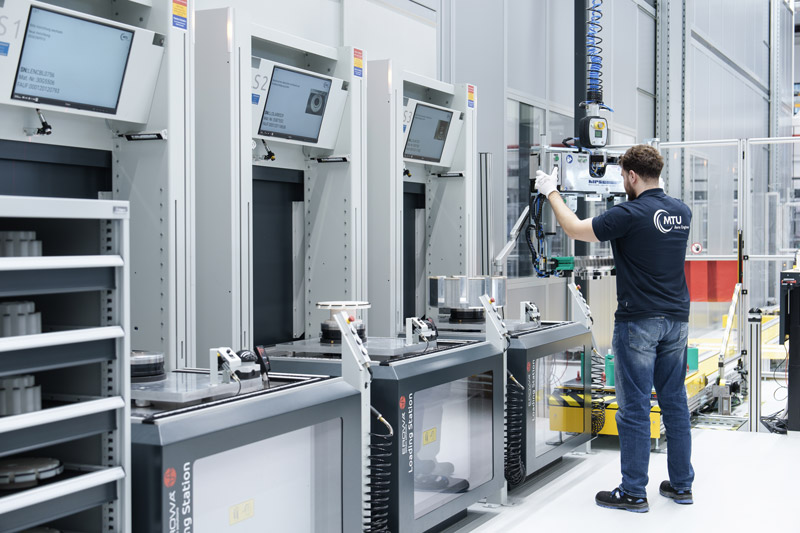
Bauteilmessung und -entladung
Per Roboter gelangt die Turbinenscheibe in das Koordinatenmessgerät. Dort wird sie bis zu vier Stunden lang von allen Seiten vermessen und anschließend wieder automatisch vom Roboter entladen. Je nach Qualität des Bauteils können die Prüfabläufe variieren.
zurück zur MesshalleKennzeichnung
Obwohl das Bauteil bereits seine eingravierte Seriennummer hat, erhält es im nächsten Schritt in einer separaten Zelle noch ein zuvor auf dem Koordinatenmessgerät erfasstes Maß. Dieses Maß hilft später bei der Instandhaltung, Abweichungen zu erkennen - auch hier agiert der Roboter autonom und führt das Bauteil ohne menschliches Zutun.
zurück zur Messhalle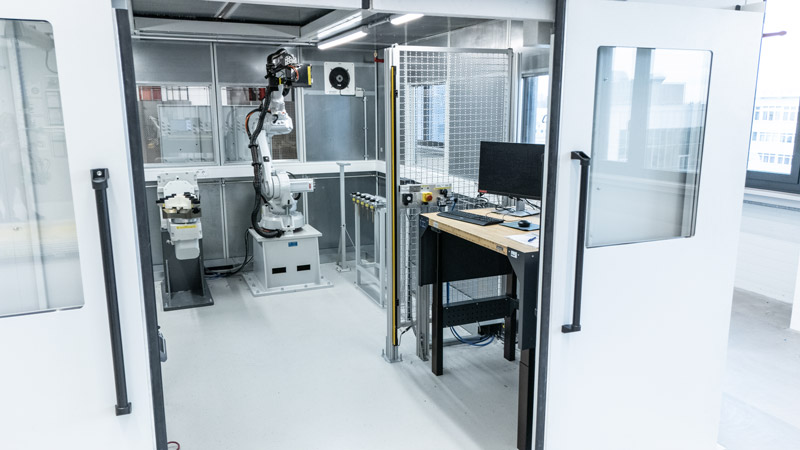
Optische Analyse
Anschließend wird die Turbinenscheibe auf ein optisches Messgerät gebracht, auf dem ein kollaborativer Roboterarm mit einem 3D-Messsensor diverse Radien und Kanten prüft.
zurück zur Messhalle'Running Sushi'
Über am Boden fahrende eCarts wird das Bauteil nach den Prüfvorgängen an die Arbeitsplätze der Mitarbeiter gebracht. Dort findet die finale Sichtprüfung und Abnahme der Bauteile statt.
zurück zur MesshalleSichtprüfung
Schließlich bringt der Roboter das Bauteil über ein automatisches Transportsystem zum Prüfplatz des Mitarbeiters. Dieser begutachtet mit geschultem Auge nochmals alles im Detail. Stellt er Auffälligkeiten fest, prüft er, ob diese noch im Rahmen der Norm liegen oder ob weitere Maßnahmen zur Korrektur ergriffen werden müssen.
zurück zur Messhalle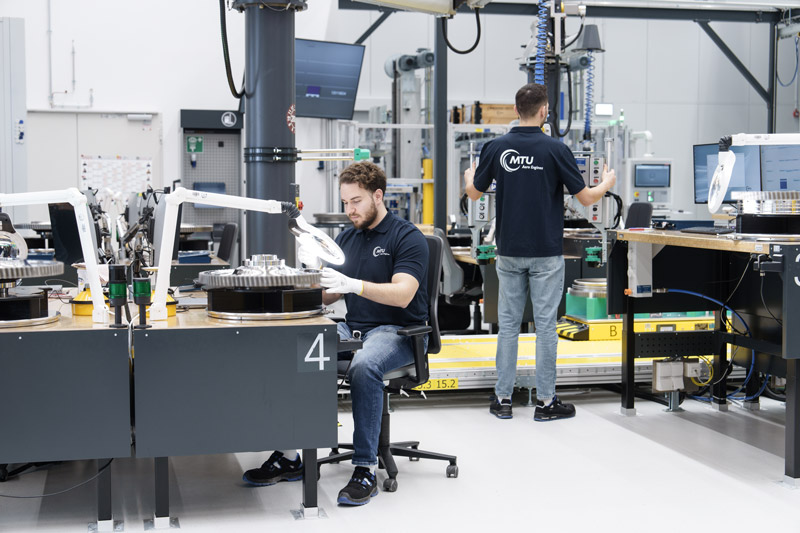