innovation
Natur als Vorbild: Bionik für leisere und effizientere Triebwerke
Ingenieure entwickeln bionische Komponenten für künftige Luftfahrtantriebe.
Autorin: Monika Weiner | 9 Min. Lesezeit veröffentlicht am: 01.02.2019
Autorin:
Monika Weiner
arbeitet seit 1985 als Wissenschaftsjournalistin. Die Diplomgeologin interessiert sich vor allem für neue Entwicklungen in Forschung und Technik sowie deren gesellschaftliche Auswirkungen.
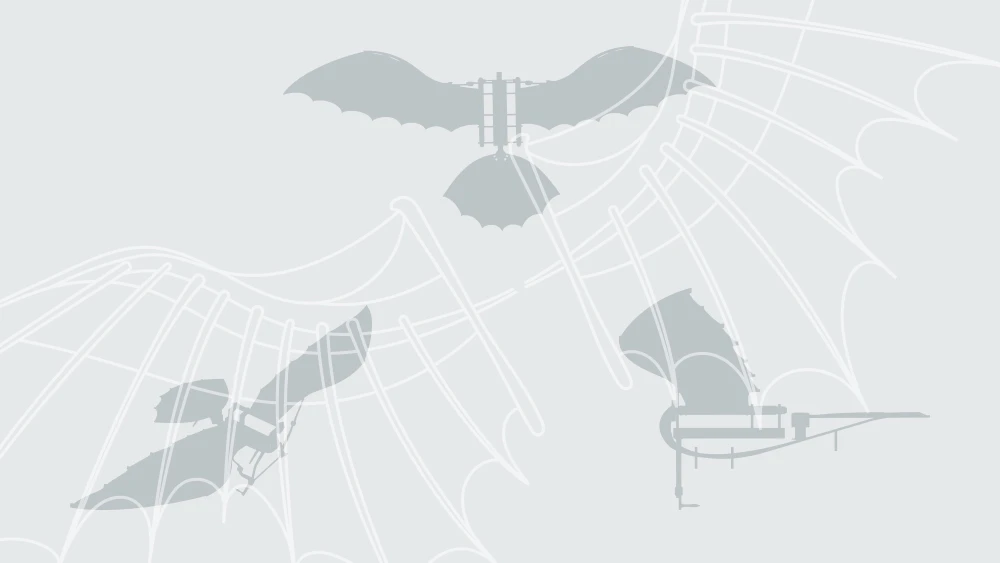
Die Natur hatte mehrere Milliarden Jahre Zeit, um optimale Lösungen zu entwickeln: Holz, das durch die Zellwände eine hohe Stabilität bekommt. Knochen, die durch ihren Aufbau leicht und doch belastbar sind. Schilfrohr, dem verschiedene Zellschichten Härte und Flexibilität verleihen. Die Blätter der Lotusblume, die, dank einer strukturierten Oberfläche, Wasser und Schmutz abweisen. Die gerillten Schuppen der Haifische, die den Strömungswiderstand reduzieren.
Die natürlichen Vorbilder inspirieren seit langem den menschlichen Erfindungsgeist. Schon Leonardo da Vinci studierte die Bewegung der Vögel, bevor er seine Flugapparate baute. Die ersten Flugversuche scheiterten übrigens, weil die menschliche Muskelkraft nicht ausreicht, um den nötigen Auftrieb zu erzeugen. Doch das Prinzip Auftrieb durch Vortrieb steckt bis heute in jedem Flugzeug. Mittlerweile nutzen die Ingenieure Inspirationen aus der Natur auch für die Material- und Bauteilentwicklung.
Von der Entwicklung bis zur Fertigung
Additive Fertigung Mit Hilfe von numerischer Simulation werden die bionischen Formen eines Bauteils entwickelt und dann mittels additiver Fertigung in Metall umgesetzt.
Enormes Innovationspotenzial
Die „Bionik“ – eine Wortkombination aus Biologie und Technik – ist ein eigenes Forschungsfeld geworden. Und in dem steckt ein enormes Innovationspotenzial, davon ist Markus Hollermann, Gründer und Geschäftsführer von „die Bioniker GbR“ und Berater bei Altran Deutschland, überzeugt: „Es geht hier nicht darum, von der Natur abzukupfern. Ziel ist vielmehr, von der Natur zu lernen – Prinzipien zu abstrahieren, auf technische Produkte und Prozesse zu übertragen und neue Funktionalitäten zu entwickeln. So kann man zum Beispiel für die Luftfahrt leichte, extrem belastbare und auch schalldämpfende Bauteile entwickeln.“
Mit bionischen Strukturen lassen sich auch Triebwerke leichter, leiser und effizienter designen – zumindest theoretisch. Praktisch schien dies lange unmöglich, weil die Bauteile traditionell geschmiedet oder gegossen werden – da ist es schwierig, Hohlräume oder Muster nach natürlichem Vorbild zu integrieren. Additive Fertigungsverfahren eröffnen den Konstrukteuren jedoch neue Möglichkeiten. Bei der MTU Aero Engines wurde vor einem Jahr ein eigenes Team „Bionische Auslegung“ als Bestandteil des Centers of Excellence für additive Verfahren gegründet.
Teamleiter Dr. Mark Welling und seine Kollegen haben mittlerweile ein bionisches Bauteil entwickelt, das auch sicherheitsrelevant für den Betrieb des Triebwerks ist mit entsprechend hohen Anforderungen an die Zulassung: eine Halterung für Ölleitungen. Anders als die bisher eingesetzten gefrästen Brackets, die gerade Kanten hatten, ist die neue Halterung geschwungen – die Form erinnert an einen Knochen. „Durch das Design konnten wir die Hälfte des Gewichts einsparen, ohne dass sich dies negativ auf Festigkeit und Dämpfungseigenschaften auswirkt“, berichtet Welling. Die Ähnlichkeit mit dem Knochen sei dabei kein Zufall: „Die Natur ist äußerst sparsam. Sie investiert nicht mehr als nötig. Beim Knochen wird Material nur dort eingebaut, wo dies für die Stabilität unbedingt erforderlich ist. Die Brackets haben wir nach einem ähnlichen Prinzip optimiert. Sie sind sozusagen das Ergebnis einer Evolution im Zeitraffer.“
Entwicklung mit numerischer Simulation
Die numerische Simulation beginnt mit einem Modell aus Hexaedern, einem Finite-Elemente-Modell, das Lasten und Temperaturen ausgesetzt wird. Das Computerprogramm ermittelt, welche Hexaeder Belastungen standhalten müssen und welche nicht. Die unbelasteten werden nach und nach entfernt, bis nur noch die unverzichtbaren Strukturen übrig sind. Dann simuliert der Computer dynamische Belastungen, wie sie während vieler tausend Starts und Landungen auftreten. Das Modell zeigt, wo Schwachstellen sind, dort muss das Hexaedernetz angepasst werden.
Im nächsten Schritt gilt es, das Design für die additive Fertigung zu optimieren: Beim Selektiven Laserschmelzen werden dünne Lagen von IN718-Pulver, einer hochwarmfesten Eisen-Nickel-Legierung, aufgetragen und dort, wo massive Strukturen entstehen sollen, mit Laserlicht verschmolzen. Prinzipiell lässt sich auf diese Weise jede Geometrie fertigen, allerdings müssen Stützstrukturen und überhängende Teile anschließend entfernt beziehungsweise nachbearbeitet werden. Um diesen Aufwand zu minimieren, durchläuft das Modell einen Optimierungsprozess.
Die CAD-Daten aus der Simulation lassen sich nun direkt für die additive Fertigung nutzen. Zur Qualitätssicherung haben die Ingenieure bei der MTU ein eigenes Verfahren entwickelt, das schon während des Schweißprozesses Schwachstellen aufspürt: Ein Sensor registriert, wie lange es dauert, bis das Pulver, das der Laser aufgeschmolzen hat, wieder erstarrt und abkühlt. Ein langes Nachglühen deutet auf eine unvollständige Verbindung mit der darunterliegenden Schicht hin.
Die Fertigung des Bracket-Rohlings dauert nur wenige Stunden. Vor dem Einbau durchläuft er noch weitere Qualitätsprüfungen, die einen sicheren Einsatz im Triebwerk garantieren.
Die neuen bionischen Halterungen werden jetzt in ein Testtriebwerk eingebaut. Sobald sie den Langzeittest dort bestanden haben und die Zulassungsanforderungen nachgewiesen sind, können sie in Serie gehen. „Damit haben wir wieder einen wichtigen Meilenstein erreicht und den Weg geebnet für künftige Entwicklungen“, so Welling. „Bis 2030 wollen wir 15 bis 30 Prozent der Triebwerksbauteile additiv fertigen. Wir wissen allerdings, dass dafür weitere Herausforderungen zu meistern sind, die wir jetzt konsequent angehen.“
Welche Komponenten eigenen sich dafür? Die Liste der potenziellen Einsatzmöglichkeiten ist lang. Denkbar wären ein Gehäuse mit integrierter Kühlung, leichte Triebwerksschaufeln oder eine neu designte Verstellmechanik für Schaufeln – bisher besteht diese aus vielen kleinen Teilen, die von Hand montiert werden müssen. „Die additive Fertigung kann dazu beitragen, die Ziele der Luftfahrt zur Reduzierung von Treibstoffverbrauch und Emissionen zu erreichen“, resümiert Welling. „Nach dem Vorbild der Natur können wir leichter, leiser und effizienter werden.“
GEWICHTSREDUZIERUNG DURCH BIONISCHE FORMEN
Additiv gefertigte Halterungen für Ölleitungen sind halb so schwer wie konventionell gefräste Bauteile
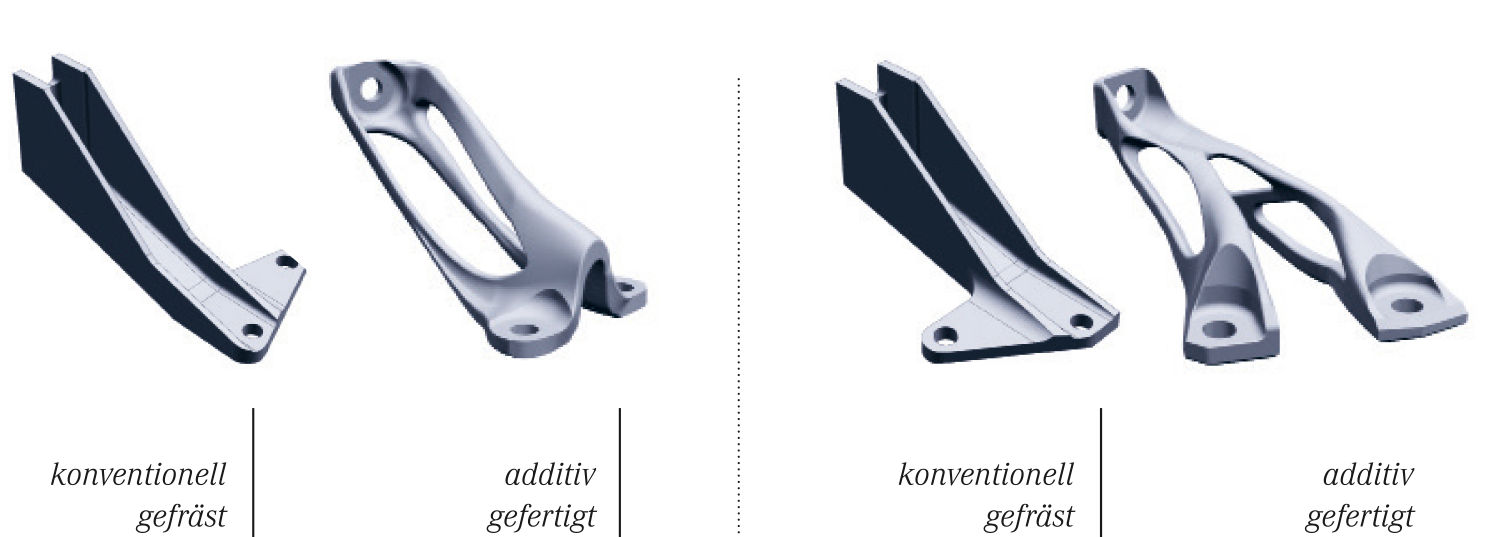