innovation
Nature’s way: Bionics make engines quieter and more efficient
Engineers are developing bionic components for tomorrow’s aircraft engines.
author: Monika Weiner | 9 mins reading time published on: 01.02.2019
author:
Monika Weiner
has been working as a science journalist since 1985. A geology graduate, she is especially interested in new developments in research and technology, and in their impact on society.
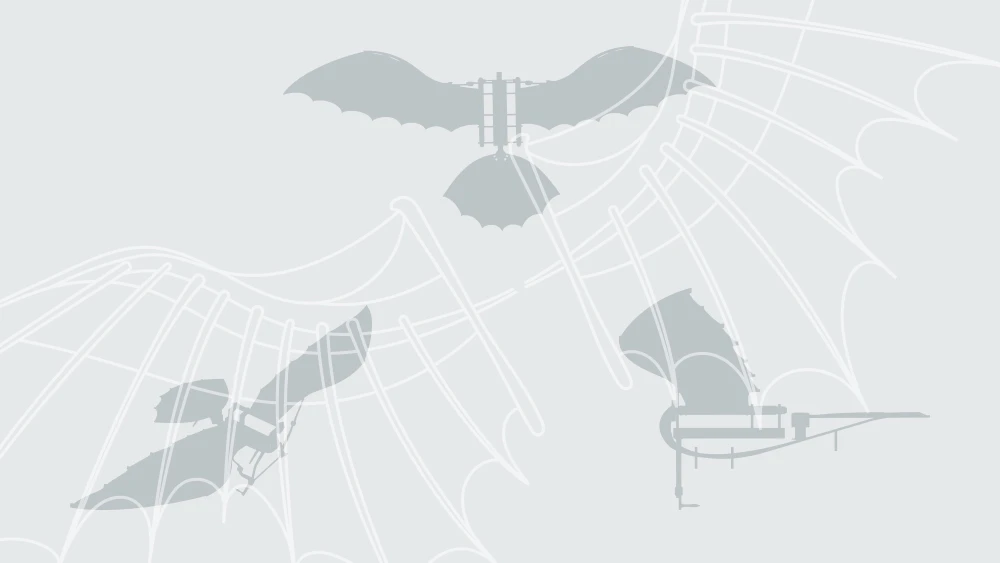
Nature had several billion years to evolve and develop the perfect solutions for its needs. Wood, for example, gets its rigidity and strength from its cell walls. Bones have a lightweight structure and yet are incredibly strong. Reeds have different layers of cells that make them tough as well as flexible. And thanks to their structured surface, the leaves of the lotus flower can repel water and dirt, while shark scales have denticles that help reduce drag in the water.
Examples from nature such as these have been sparking creativity and inspiration for human inventions for years. Even Leonardo da Vinci studied the flight of birds prior to building his flying machines—even if his first attempts at flying failed because they relied on human strength alone to generate the necessary lift. But the concept of creating lift through propulsion is still found onboard all aircraft to this day. Following in da Vinci’s footsteps, engineers today also take inspiration and apply principles from nature when they develop materials and components.
From development to manufacturing
Additive manufacturing Numerical simulation is used to develop the bionic structure of a component, which is then reproduced in metal by means of additive manufacturing.
Huge innovation potential
Bionics, a portmanteau of “biology” and “electronics,” has become a field of research in its own right. As the founder and CEO of German company die Bioniker GbR and a consultant at Altran Deutschland, Markus Hollermann is a firm believer in the huge innovation potential that bionics offers. “Bionics isn’t about copying nature but about learning from it—applying its principles to electronic products and processes and developing new functionalities. Using examples from nature, we can create components for aviation applications that are lightweight, exceptionally strong and that absorb sound.”
Bionic structures can be used as a basis for lighter, quieter and more efficient engine designs—at least theoretically. For a long time, however, this appeared impossible to translate into practice. That’s because conventional components are forged or cast, which makes it difficult to integrate cavities or designs based on nature. But now, additive manufacturing processes are opening up a world of new opportunities for design engineers. A year ago, MTU Aero Engines formed its own bionic design team as part of its Center of Excellence for additive manufacturing.
Headed by Dr. Mark Welling, the team has now developed a bionic component: a bracket for oil lines. Given that the component is critical to safe engine operation, it must meet stringent requirements to obtain approval from the aviation authorities. Unlike the conventional, straight-edged brackets that are milled, this new bracket is curved and takes a shape not dissimilar to a bone. “The new design enabled us to cut the weight of the component in half, without interfering with the strength or damping characteristics,” says Welling. It’s no coincidence that the design resembles a bone: “Nature is extremely economical; it doesn’t invest any more than what is required. If you look at bones, extra material is present only in places where it’s absolutely necessary for stability. We used a similar principle to optimize our brackets—you could say that they’re the result of accelerated evolution.”
Development by numerical simulation
Numerical simulation begins with a hexahedral model, a finite element model that is subjected to specific loads and temperatures. A computer program then identifies which of the hexahedrons are critical for withstanding the stresses and which ones are not. The non-critical ones are removed one by one until only the essential structures remain. Next, the computer simulates dynamic stresses and their impact over thousands of takeoffs and landings. The model exposes any weak points where the hexahedral mesh needs to be modified.
In the next step, the design is optimized for additive manufacturing. Selective laser melting. In this process, thin layers of the high-temperature iron-nickel alloy Inconel 718 are applied to the substrate in powder form. A laser then melts the powder, fusing the layers together to create solid structures. In principle, this method is suitable for producing any geometry, but it does require any support structures and overhangs to be removed or reworked afterwards. Optimizing the model minimizes the amount of work involved.
The CAD data from the simulation can now be used for additive manufacturing without further processing. For quality assurance purposes, MTU’s engineers developed their own method for identifying any structural weak points as early as possible. During the welding process, a sensor records the time it takes for the powder melted by the laser to resolidify and cool down. If this is unusually long, it’s a sign that the powder has not fused properly with the layer below.
Production of the blank for the bracket takes only a few hours. Before the bracket is mounted, it undergoes further quality inspections to ensure it is safe to use in the engine.
The new bionic brackets are now being installed in a test engine. Once they have passed endurance testing and demonstrated they meet the requirements for approval, they can be rolled out into large-scale production. “Then we’ll have another important milestone under our belt, paving the way for more developments of this kind in the future,” Welling says. “Our plan is to produce 15 to 30 percent of our engine components using additive technologies by 2030. That’s no mean feat, and we know we’ve still got some challenges to overcome. But we’re working through them systematically to find solutions.”
There is a long list of components that would be suitable for additive manufacturing. Among the potential candidates are a housing with integrated cooling, lightweight engine blades or a redesigned variable guide vane actuator—a mechanism currently made up of many small parts that have to be assembled manually.
“Additive manufacturing can also help achieve the targets for reducing fuel consumption and emissions in aviation,” Welling says. “Following nature’s example, we can make aircraft engines lighter, quieter and more efficient.”
Bionic structures reduce weight
Additively manufactured brackets for oil lines weigh half as much as those made using conventional milling
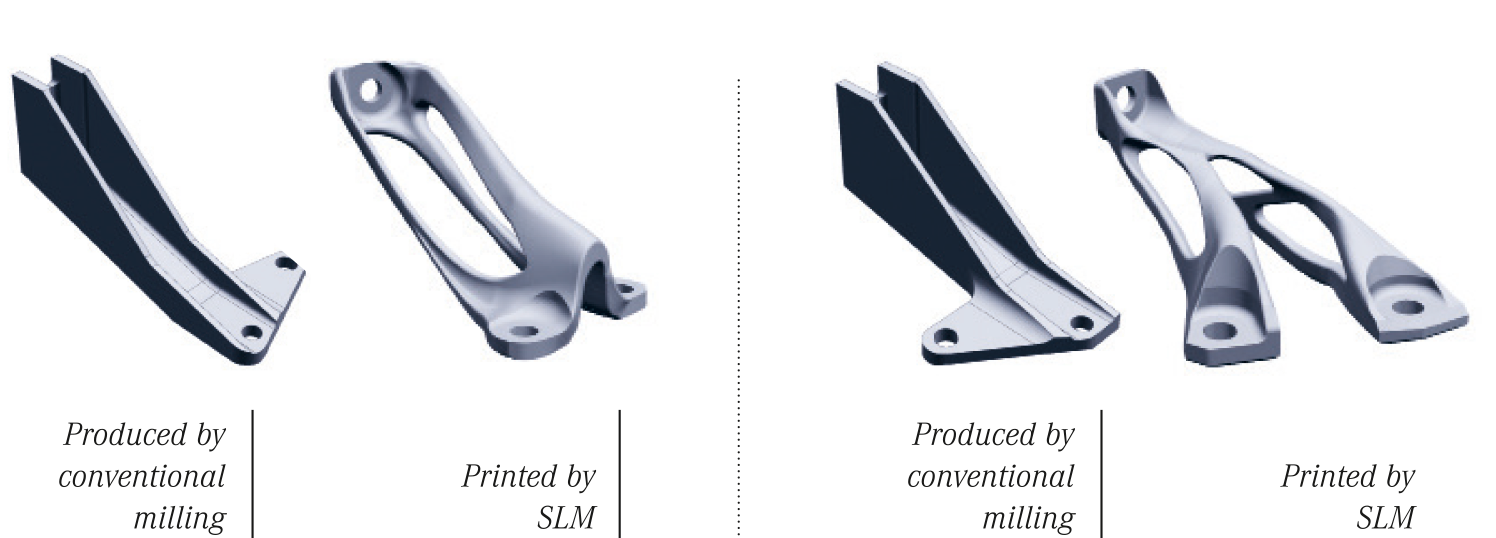