aviation
Aeroderivative IGTs – the flexible, lightweight option
Aeroderivative industrial gas turbines (IGTs) are in a class of their own: compact and lightweight, these IGTs offer quick start-up capabilities in power generation.
author: Nicole Geffert | 8 mins reading time published on: 20.03.2024
author:
Nicole Geffert
has been working as a freelance journalist covering topics such as research and science, money and taxes, and education and careers since 1999.
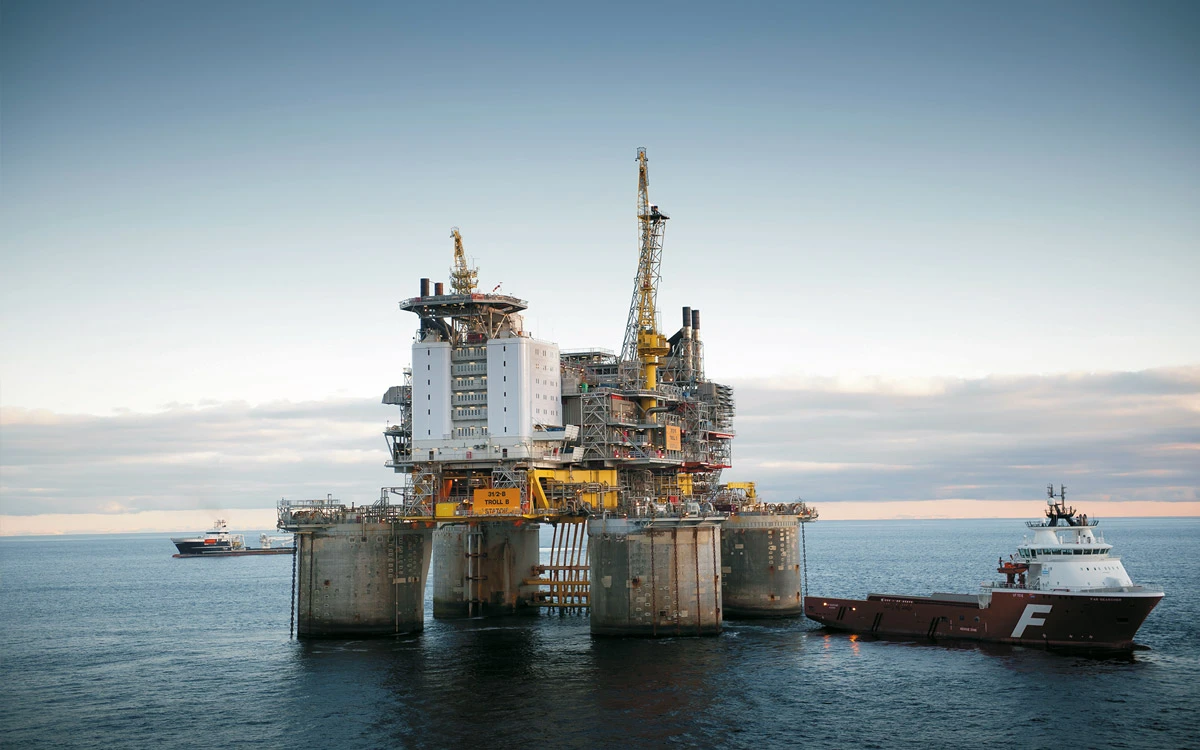
©Øyvind Hagen/Equinor
Physical fitness and nerves of steel are part of the job description for Matthias Witt and his team. As experts in industrial gas turbines (IGTs) at MTU, they can find themselves called away at a moment’s notice—whether to a windswept oil platform in the North Sea or to the hot and humid jungles of Brazil. There are plenty of other workplaces that are more comfortable, but few that are quite as exciting.
Witt heads the Field Services and Package Services business units at MTU Power, the MTU Aero Engines brand for services and solutions in the field of IGTs. MTU Power is based in Ludwigsfelde at the MTU Maintenance Berlin-Brandenburg site. Since 1995, this has been the hub of MTU expertise in IGTs, with a focus on maintaining the LM™ series of IGTs manufactured by GE Power (GE). To date, MTU’s specialists have completed more than 1,400 shop visits for LM2500™ and LM6000™ IGTs, including on-site services at operators’ premises.
MTU Power’s international customers are as varied and diverse as the array of IGT applications, which ranges from energy supply and marine propulsion systems to pumps and compressors for oil platforms and pipelines. “Demand is consistently high,” says Henrik Harksen, who is responsible for sales of IGT services at MTU. Business is booming thanks to the construction of new terminals for liquefied natural gas (LNG) and the switch to renewables. Demand also comes from the turbine-powered frigates, cruise ships and modern high-speed ferries that sail the world’s oceans.
IGT services all over the world
Always available: Whether in the Americas, Asia, or Europe: the IGT experts at MTU Maintenance can support their customers quickly and flexibly. This is thanks to the service centers in Germany (Ludwigsfelde), Brazil (São Paulo), Australia (Perth), the U.S. (Dallas), Thailand (Ayutthaya), and Norway (Mongstad).
Worldwide support
“We have customers on every continent,” Harksen says. To support these customers, MTU operates a worldwide network of IGT service centers, including sites in Australia, Brazil, Thailand and the United States. Its field service teams can reach any location in the world within 24 hours. Speed can be crucial, particularly in the case of unplanned repairs that require a fast response. One of the reasons reliable service is so important is that downtime is expensive.
Not every call-out is an emergency, however. “We also offer scheduled maintenance services,” Harksen says. Once an IGT has clocked up around 50,000 operating hours, it heads to the maintenance shop for basic maintenance. MTU’s IGT specialists are experts in what they do: from disassembly and repairs to assembly, installation and commissioning. They are also responsible for regular inspections, remote monitoring, vibration analysis, technical consulting and customer training.
MTU in Ludwigsfelde is also home to one of the world’s largest and most modern IGT test stands. “If the operator needs a replacement gas turbine during the shop visit to keep their operations running smoothly, we can help by leasing them an IGT,” Harksen says.
MTU’s specialists are also in demand for their expertise in package services. The term “package” refers to the complete gas turbine system and all its components. As well as the control, air, oil and fire-extinguishing systems, it includes the electrical generators, fuel supply and in some cases a water-injection system to reduce nitrogen oxides, plus various other components. Package services sometimes take the team to surprising places—for example, one of the jobs Witt and his team had to tackle involved the complete overhaul of a gas-fired power plant for an energy provider in the Manaus rainforest, all while braving temperatures of 40 degrees Celsius, 95 percent humidity and torrential rain. The result was a successfully upgraded LM6000 – and a very satisfied customer.
An unusual mission
Myanmar has been under a state of emergency since the military seized power in February 2021. Located in Southeast Asia, the country is bordered by Thailand, Laos, China, India and Bangladesh. Last year, a team comprising field service technicians from the MTU Maintenance Service Center Ayutthaya in Thailand, the MTU Maintenance Service Centre Australia and MTU Maintenance Berlin-Brandenburg carried out a joint assignment there under stringent security arrangements.
Their destination was a power station in Yangon, formerly known as Rangoon. This facility supplies 50 percent of the city’s energy—so the pressure was on to come up with a solution. Such missions are only possible if volunteers can be found and if MTU decides to grant approval for the trip based on the security situation. The safety of MTU’s employees is always the paramount concern.
The team was deployed to Myanmar during the rainy season and had to battle extreme heat, high humidity and many other adversities. After 15 days, they succeeded in restoring the electricity supply to Yangon. “Once we entered Myanmar, we found that the road to the facility had been partially blocked by an earthquake, so all the material had to be unloaded from the large truck onto small pick-up trucks and driven through the jungle. We spent the entire first day cleaning and sorting our dirty tools, some of which had been damaged, and getting them back into working order,” says Marvin Kuhlbrodt, a field service mechanic at MTU Maintenance Berlin-Brandenburg.
The team then unloaded the IGT, which was driven to the power station’s workshop via a circuitous route to avoid a nearby river. Despite the difficult circumstances, the team ultimately managed to carry out “one of the most complex repairs you can perform on a low-pressure turbine outside the shop,” Kuhlbrodt says. This required additional spare parts from Germany, which were airfreighted to Bangkok and then couriered to the workshop in just five days.
Derived from aircraft engines
IGTs are divided into different power categories. For example, LM series IGTs are derived from various versions of the CF6 aircraft engines used to power the Boeing 747. Known as aeroderivative IGTs, these are a lightweight class of gas turbine. They work on the same principle as their airborne counterparts. Unlike aircraft engines, however, they do not have fans; instead, they harness rotational energy and convert it into electrical energy or mechanical propulsion.
The client base in this sector is very different to that of the aviation industry. “The IGT market is heavily fragmented,” says Daniel Giesecke, an expert in strategy and market analysis at MTU Aero Engines. “Airlines will often order dozens of identical engines, while IGT customers usually only buy one gas turbine, or a few at most.”
MTU has been providing maintenance services for the LM2500 since 1981. It is the most widely used gas turbine in the 20–25 megawatt power category, with enhanced versions available up to almost 37 megawatts. More than half of these powerhouses are used in the oil and gas industry.
Its “big sister”—the LM6000—produces up to 54 megawatts of power; in 90 percent of cases, it is used to generate electricity. Both these aeroderivative IGTs achieve high efficiencies of over 40 percent. They are lightweight, compact and efficient. At the other end of the scale are heavy-duty turbines, which are specifically designed for stationary continuous operation in large power stations. These deliver up to 340 megawatts of power.
Under control
Once an IGT has completed around 50,000 operating hours, it heads to the shop for basic maintenance, where MTU’s specialists also conduct regular inspections, remote monitoring, technical consulting, and customer training.
LM6000
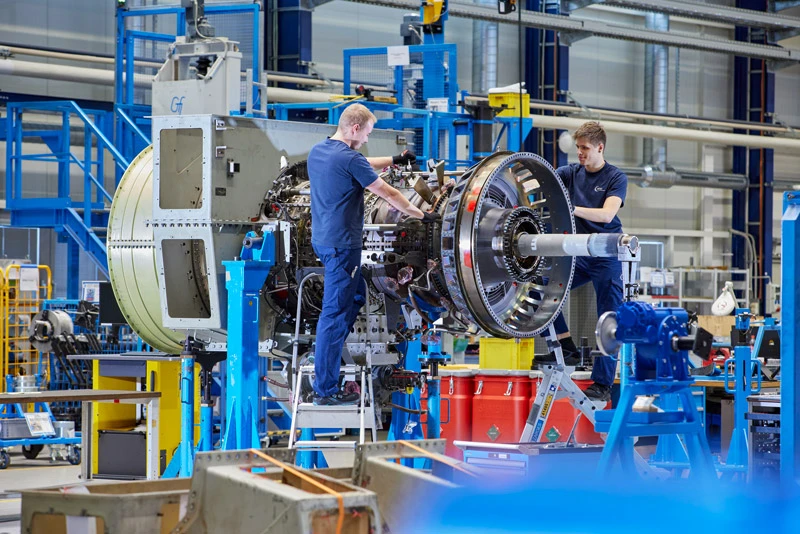
The LM6000™ industrial gas turbine derives from GE’s CF6-80 aircraft engine. This industrial gas turbine is used primarily for power generation applications, but also as a direct mechanical drive, for instance, to power pumps. MTU has been providing maintenance services for this type of gas turbine since 1996.
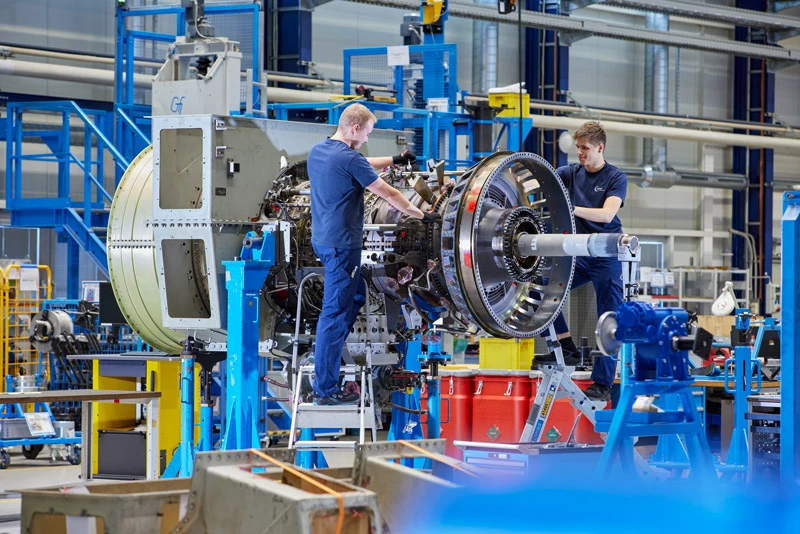
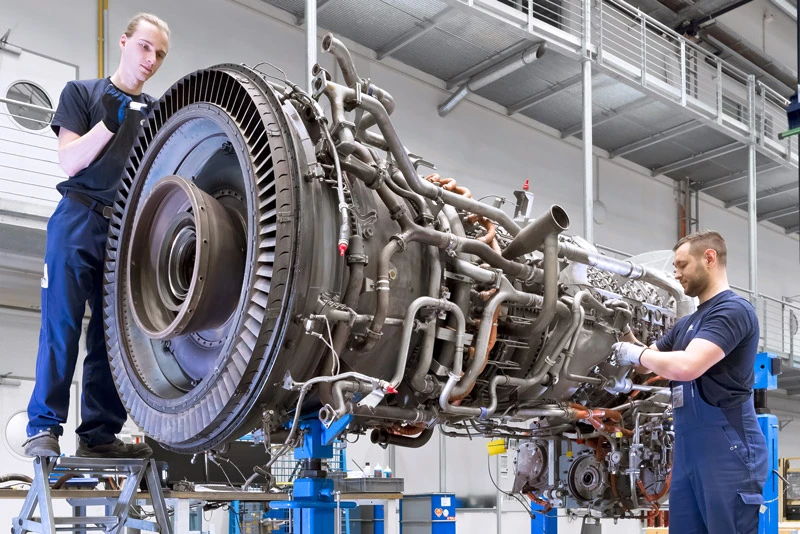
Quick start-up capabilities
Heavy-duty turbines cannot match aeroderivative IGTs when it comes to flexibility, however, which is why aeroderivative IGTs now play such an important role in power generation. “Aeroderivative IGTs can be started up and shut down quickly to respond to fluctuations in electricity demand,” Giesecke says. “This makes them a key part of the system, especially now that the share of renewables is on the rise.”
The availability of wind and sun varies minute by minute, so power grids need strategies to help them cope with the intermittency of supply. Extended periods of low wind and limited sunshine pose a particular challenge. “Peaking power plants are necessary to ensure a reliable electricity supply,” Giesecke says. “Peakers are brought online during periods of peak demand, and the quick-start capabilities of aeroderivative IGTs make them the ideal candidate for this task.” The LM2500 and LM6000 can both be stepped up to maximum output in a matter of minutes, delivering electricity almost at the touch of a button.
Long-term service agreements
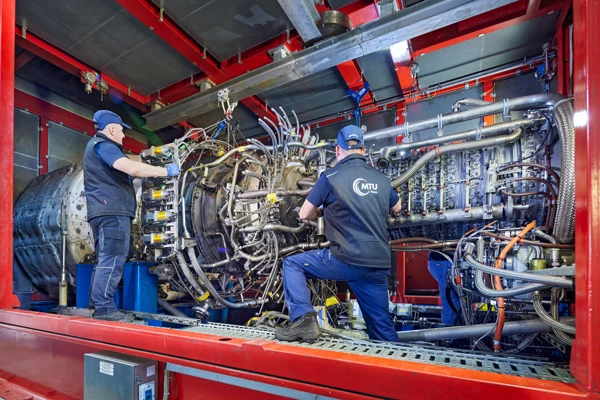
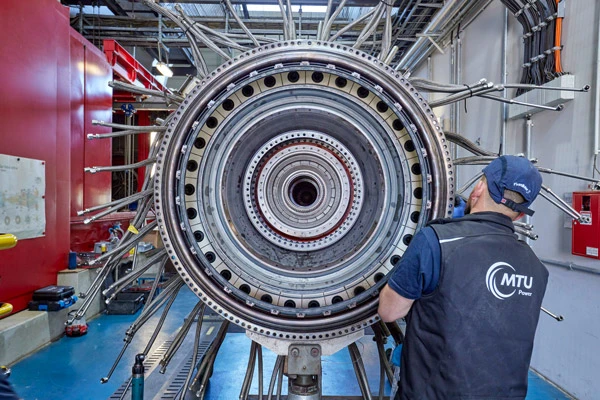
MTU Power also offers extensive on-site capabilities, scheduled and preventative maintenance. The services range from removal, installation and commissioning, on-site repair, periodic inspections, remote monitoring and vibration analysis all the way to engineering consulting and customer training for LM2500 and LM6000 series gas turbines.
In this respect, they are similar to aircraft engines, which are designed to deliver maximum thrust on takeoff. “Peaker plants are used in conjunction with baseload power plants, which provide a continuous supply of electricity and district heating but offer less flexibility,” Giesecke says. Since peaker plants are not in continuous use, they reach a maximum of perhaps 1,000 operating hours a year. These IGTs can be in operation for up to 30 years.
Hydrogen-ready gas-fired power plants
The future of IGTs is also closely tied to the goal of decarbonization. Hydrogen is increasingly being used as an alternative fuel as part of efforts to reduce CO₂ emissions in the energy supply. Hydrogen-ready gas-fired power plants are gaining traction, with new facilities being built and existing plants being converted. Their job is to ensure a reliable supply of electricity at times of low wind or solar output. “As long as we continue to see bottlenecks in hydrogen supply, hydrogen will need to be mixed with natural gas and burned to power IGTs,” Giesecke says.
Whether the transition to 100 percent hydrogen ultimately succeeds will also depend on whether enough climate-neutral hydrogen is available in the future. This is a challenge that the IGT sector shares with aviation, which is also relying on sustainable fuels and green hydrogen as it moves toward emissions-free flight.