aviation
Geared for more power
All around the world MTU sites are involved in the successful GTF engine. Each location brings its own unique strengths to the table.
author: Isabel Henrich | 6 mins reading time published on: 06.10.2021
author:
Isabel Henrich
studied political science and communications. At MTU, she coordinates the editorial process of AEROREPORT and is responsible for the conception and development of its content.
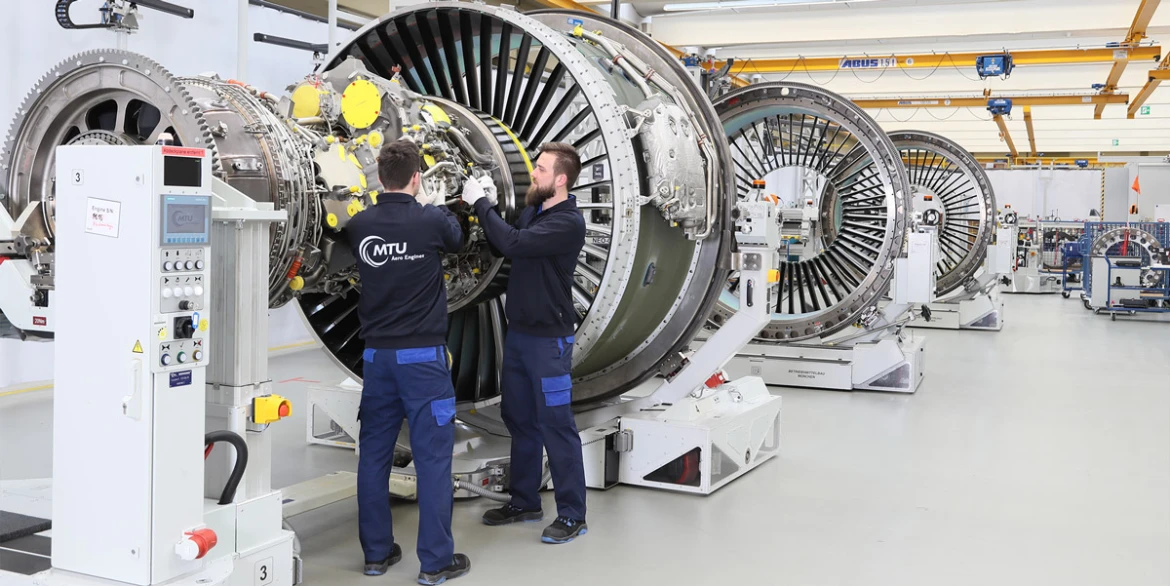
It took just 18 months to turn this greenfield site into one of the world’s largest and most cutting-edge shops for the Pratt & Whitney GTF™ engine family. EME Aero is developing at an astounding pace—and it’s not about to slow down: the second GTF family member, the PW1500G, was launched in August 2021.
EME Aero is only one of several MTU locations whose development, manufacturing and maintenance expertise make a key contribution to the GTF engine program.
Depending on the application, MTU’s share of the GTF™ engine family is between 15 and 18 percent: in addition to responsibility for the high-speed low-pressure turbine and the first four stages of the high-pressure compressor, MTU also manufactures brush seals and nickel blisks for high-pressure compressor components, for which it does not have development responsibility. Moreover, MTU is responsible for the final assembly of one-third of the production PW1100G-JM for the A320neo. Development work on key GTF components is being carried out at MTU in Munich, in Rzeszów and at MTU Aero Engines North America.
MTU Maintenance has more than 40 years of experience and expertise in the independent MRO business and benefits from a broadly diversified engine portfolio. MTU is ideally positioned for the successful PW1100G-JM engine in particular, which powers the Airbus A320neo. MTU Maintenance Berlin-Brandenburg repairs individual stages of the high-pressure compressor and the low-pressure turbine. MTU Maintenance Zhuhai, EME Aero in Poland and MTU Maintenance Hannover have full disassembly, assembly and test capabilities for this engine type. And in addition to manufacturing GTF components, MTU Aero Engines in Munich and MTU Aero Engines Polska also carry out parts repairs for the PW1100G-JM.
Here we present six sites and the part they play in making the geared turbofan such a success:
MTU Aero Engines, Munich
It was more than 20 years ago at MTU Aero Engines’ technology hub, together with its partner Pratt & Whitney, that the first ideas for a geared turbofan were born. Today, MTU’s Munich facility manufactures the high-speed low-pressure turbine, several stages of the high-pressure compressor in blisk design, and brush seals developed in-house for all GTF engine family members. In addition to carrying out parts repairs, since 2016 the site has also been responsible for final assembly of one-third of production PW1100G-JM engines. To this end, the MTU project team developed a track-guided assembly system with 16 remote-controlled carts that, coupled together depending on the stage of assembly, move forward along the assembly line as though on a conveyor belt.
Focus on the next generation
The engineers in Munich are already working intensively on a further development of the GTF engine. The second generation is set to save more fuel and be even quieter and more efficient: the high-speed low-pressure turbine is being further optimized and new processes and materials are being used to get the most out of geared turbofan technology. These engines are ex-pected be flying by the start of the coming decade.
MTU Aero Engines Polska
MTU Aero Engines Polska has been involved in the GTF almost since the beginning. The site in Rzeszów supplies high-quality components for five of the six applications. It supports the GTF program in various phases of engine production, from development to large-scale production. As of July 2021, 522 employees—more than 60 percent of the workforce—were involved in GTF projects.
GTF production ramp-up
MTU Aero Engines Polska can present some impressive figures: in 2015, the engineers in Rzeszów began assembling the first low-pressure turbine for the PW1100G-JM, the engine for the Airbus A320neo. Six years later, the site is now approaching 2,500 assemblies of this module. As of 2021, nearly 800,000 GTF parts in total have been delivered, including more than 600,000 for the PW1100G-JM model.
MTU Maintenance Hannover
As the heart of the Maintenance Group and MTU’s first maintenance facility, the MTU site in Langenhagen is indispensable for MRO services for GTF engines, too. Many years of expertise and a breadth of know-how gained through various engine programs (including the V2500, GE90 and CF6) provide the necessary MRO experience and skills. MTU Maintenance Hannover offers the full range of disassembly, assembly and test capabilities for the PW1100G-JM engine.
Up to speed in no time
The workforce in Hannover had to prepare for the PW1100G-JM in a hurry. But that was no problem for these engine experts: thanks to their many years of MRO experience, the company was ready for the new engine program in next to no time. The employees received strong support from Ludwigsfelde, too: a team from MTU Maintenance Berlin-Brandenburg provided valuable GTF know-how in the form of a PW1100G-JM crash course.
MTU Maintenance Zhuhai
The joint venture between MTU and China Southern Airlines Company Limited is the newest member of MTU’s GTF network. September 2021, the first PW1100G-JM approached the shop—with plans for 1,000 shop visits over the next ten years. A second site is already under construction, a 65,000 pound thrust capacity and is scheduled to go into operation in 2024. As in Hannover and at EME Aero, the Zhuhai site is fully equipped for (dis)assembly and testing of the PW1100G-JM engines.
Firmly established
As the largest MRO provider for narrowbody engines in the whole of Asia, MTU Maintenance Zhuhai has made a name for itself in the region. With the addition of the PW1100G-JM engine to its portfolio, the site is continuing its growth strategy and can now offer excellent service to its customers as a narrowbody expert in this region for the latest generation of engines.
EME Aero
As one of the world’s largest MRO shops for the GTF engine family, the joint venture between MTU and Lufthansa Technik forms the heart of MTU's GTF network. It started repairing PW1100G-JM engines in January 2020; this was followed by the PW1500G in August 2021, with the PW1900G set to follow soon. To ensure it provides the highest standard of repairs, EME Aero’s shop is state of the art—which is only fitting for the most advanced and efficient engine family on the market today. With 450 shop visits planned per year, the site has big ambitions and is set for rapid growth.
Pure high-tech
With a flowline designed specifically for the site, EME Aero has one of the world’s most advanced assembly systems in engine maintenance. Specialists from MTU’s production and facilities service in Munich worked with the EME Aero team to develop a standardized assembly and tooling concept for the various engine types in the GTF family.
MTU Maintenance Berlin-Brandenburg
The MTU site in Ludwigsfelde has been involved right from the outset. This is where individual stages of the PW1100G-JM’s high-pressure compressor and low-pressure turbine are repaired. In 2020, it added the PW1500G and the PW1900G. As true repair specialists, the experts in Ludwigsfelde are the only company in the global market to provide the full range of repairs for the low-pressure turbine and the second stage of the high-pressure turbine.
From the first moment
This location had already procured the required repair facilities back when its application to become a repair site for GTF engines was still being processed—a not entirely risk-free strategy, but one that proved its worth: this proactive effort secured the contract for the repair work and means that to this day, the site is an expert in MRO services for the GTF family.