innovation
Geared turbofan development: Still room for improvement
Cleaner, quieter and more fuel-efficient—the first GTF generation was already considered a technical masterpiece. But this engine architecture still has much to offer.
author: Denis Dilba | 5 mins reading time published on: 06.10.2021
author:
Denis Dilba
holds a degree in mechatronics, is a graduate of the German School of Journalism, and founded the “Substanz” digital science magazine. He writes articles about a wide variety of technical and business themes.
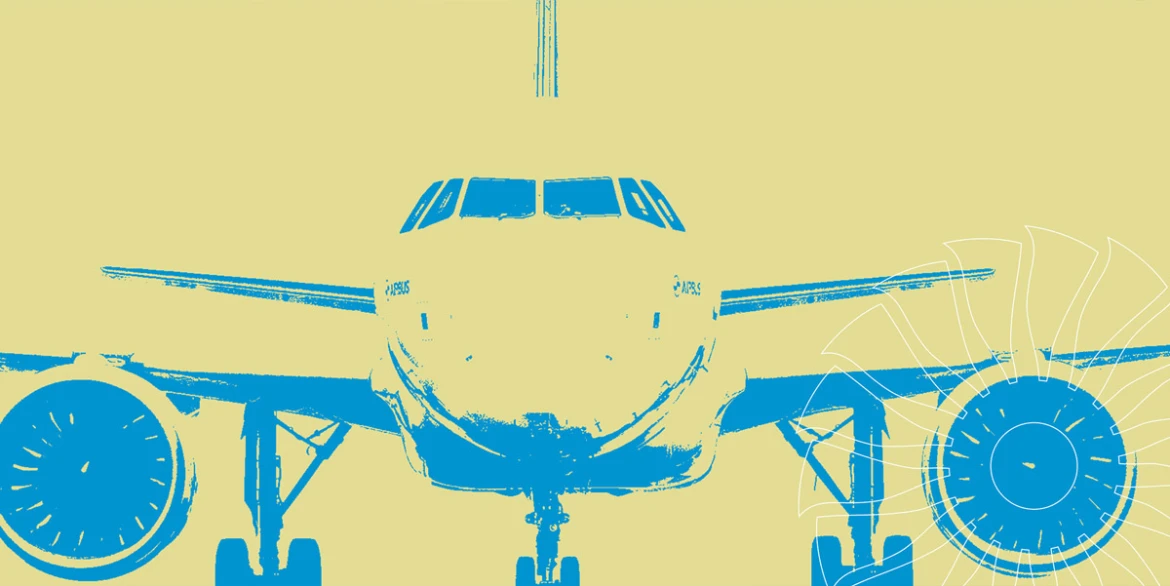
A gearbox transmits power, converting torque and speeds. No wonder, then, that the component made its way into the engines of various aircraft long before 2008. Helicopters, for example, can’t function at all without this mechanical component, and in turboprop engines, too, gears have always ensured that the propellers turn at the right speed. Since the introduction of the geared turbofan program 13 years ago, gearboxes have also played a role in commercial aircraft—with significantly higher performance requirements. “The novelty of this so-called planetary gear was and indeed is the enormous requirement in terms of the power to be transferred,” says Dr. Stephan Bock, Director Engineering Commercial Programs at MTU Aero Engines. “Over an area no larger than a manhole cover, the gearbox has to transfer about 20 megawatts of power—that’s as much as a small stationary power plant.”
In addition to the high performance, the highest demands are placed on the reliability of the geared turbofan’s entire technology. “In this power class, even a tiny percentage of heat loss is so great that cooling must always be ensured—otherwise the gearbox will heat up to the melting point of its constituent materials in no time at all and then, to put it bluntly, simply won’t be there,” Bock explains. The “G” in “geared turbofan,” or GTF, thus remains an outstanding feat of engineering, because this new architecture lets all components run at their optimum speed: the large-diameter fan slower, and the low-pressure compressor and low-pressure turbine considerably faster. In the absence of a gearbox, compromises have to be made in terms of speeds, which then come at the expense of component efficiencies. To date, no other competitor besides GTF manufacturer Pratt & Whitney has managed to bring such a planetary gear train into the world of aviation.
Leveraging potential with MTU engineering expertise
Other key technological highlights and milestones that are central to the geared turbofan’s functioning include the two main MTU components: the high-speed low-pressure turbine and the first four stages of the eight-stage high-pressure compressor engineered in blisk design. As a result, the geared turbofan achieves a very high degree of efficiency, which, from a purely mathematical point of view, is already impressive: fuel consumption and carbon dioxide emissions are reduced by 16 percent each, and the noise footprint by 75 percent. The GTF also brings significant improvements in terms of NOx emissions, which are 50 percent lower than those of its predecessor. Operators currently report fuel savings of as much as 20 percent compared to aircraft of the previous generation, according to Tom Pelland, Senior Vice President, Commercial Engine Programs at GTF manufacturer Pratt & Whitney.
This success is due in no small part to the high-speed low-pressure turbine in particular, with its higher efficiencies. MTU won two German innovation awards for this key GTF component. The high rotational speeds that result from the GTF’s reduction gearbox mean the stages can work harder. That’s why the engine needs just three stages. As a result, the space, weight, maintenance costs, fuel consumption and CO2 emissions of the entire engine all decrease. And as if this weren’t impressive enough, the MTU low-pressure turbine goes a long way toward achieving the aim of reducing noise emissions. It is much quieter than conventional models because its noise emissions are at higher frequencies; these are better absorbed by the atmosphere, to the point where the human ear can barely detect them.
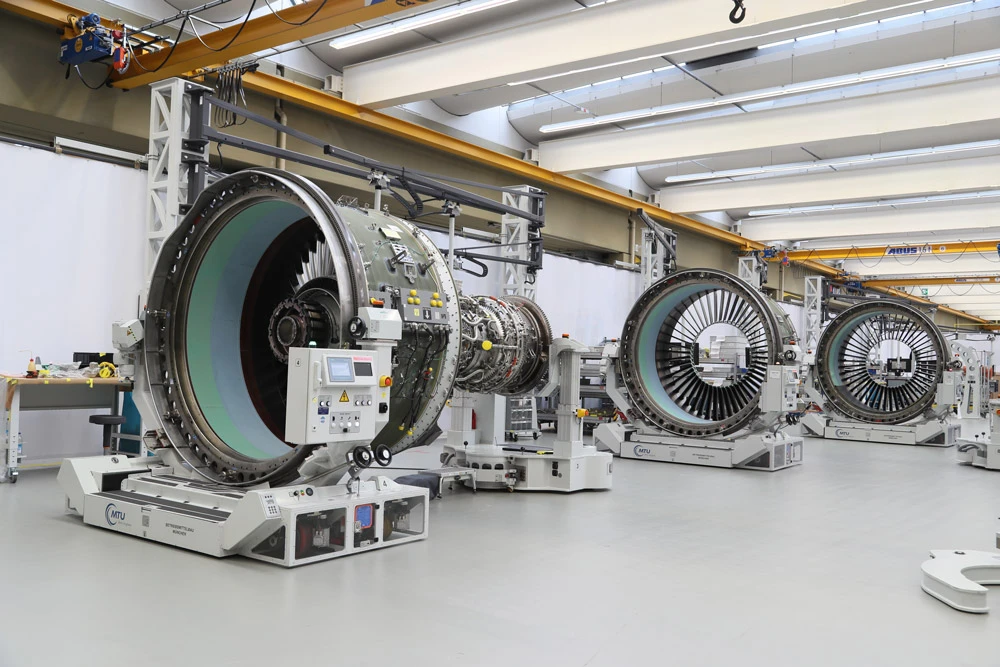
GTF engine family: The new engines offer double-digit improvements in fuel burn, pollutant and noise emissions, and operating costs.
No end to the GTF success story in sight
What does “bypass ratio” actually mean?
In modern engines, also known as turbofan engines, the core engine is a gas turbine that drives a fan, which in turn accelerates air past the core engine in the bypass flow. The ratio between this airflow and a second airflow that passes through the turbine itself is known as the bypass ratio.
What makes an engine efficient is when it moves large air masses at a speed as close as possible to the airspeed—in other words, while demonstrating a high bypass ratio. This in turn lowers fuel consumption and emissions, including noise.
Ultra-high bypass ratio for the future
Since the 1960s, bypass ratios have increased from 2:1 to 6:1 for the V2500, the classic 1980s engine, and on to the current record of 12:1 set by the latest geared turbofan (GTF). Developers aim to refine the GTF engine to achieve a bypass ratio greater than 12:1. Experts describe this as an ultra-high bypass ration (UHBR).
With this world-class low-pressure turbine, today MTU is in a league of its own. But even this exceptional turbine has room for improvement. “We’re working on new materials, even more powerful computer simulations, and newly optimized aerodynamics to create the next generation of low-pressure turbines,” Bock says. MTU is the only company in the world to have mastered this technology in large-scale production. The company’s staying power and meticulous development efforts have also paid off: as well as representing a technological quantum leap, the geared turbofan concept developed together with Pratt & Whitney has also been a major commercial success. Today, Airbus offers the GTF for the A320neo family and the A220 (formerly the Bombardier C Series), Mitsubishi has selected the engine exclusively for its SpaceJet regional jet, and Embraer uses it to power the new E-Jets of the E-170 and E-190 families. Irkut will also equip its MC-21 with the GTF. Currently, Pratt & Whitney can boast a total of more than 10,000 orders and options for geared turbofan engines worldwide.
MTU innovations have gone into the current version, such as the first additively manufactured components, called borescope bosses, and brush seals. The latter, together with new blisk compressor stages, improve the performance of the high-pressure compressor. “The technological developments and successes to date naturally make us proud,” says Dr. Martin Stadlbauer, Senior Vice President for Advanced Commercial and Military Programs. For instance, GTF technology has avoided more than five million tons of CO2 emissions to date. “But we can and must make more savings and improvements in the future,” Stadlbauer says. The next GTF generation, which MTU expects to be launched at the beginning of the next decade, is expected to deliver further savings of up to 10 percent in fuel consumption and CO2 emissions. For instance, it should be possible to achieve even lower fan pressure ratios over the coming years, which would further increase the bypass ratio—from the current 12:1 to somewhere in the region of 15:1.
Moreover, MTU’s engineers are working on further improving the core engine’s thermal efficiency by increasing the pressure ratios. To achieve this, they want to push the efficiency of the low-pressure turbine and the high-pressure compressor even higher. “Using new virtual design processes and simulation tools, we know we can increase the speed of the necessary developments while reducing costs,” Stadlbauer says.
Climate neutrality with SAFs and “wet” combustion
Future GTF versions can be operated with higher proportions of sustainable aviation fuels (SAFs). Currently, a 50 percent SAF admixture is possible, but the aim is to get as close as possible to 100 percent, Stadlbauer says. “With larger gearboxes, you can adjust the power output and, if the market demands it, build even larger engines,” Bock explains. He adds that Pratt & Whitney is already pushing forward with this development. “Together with developments on engines that burn hydrogen directly and, above all, on the flying fuel cell, we feel that the coming GTF generations are well prepared to meet increasing demands,” Bock says. “We have our sights firmly set on the climate-neutral future of aviation.”