people
Michael Schreyögg talks about current trends within the engine maintenance world
In this exclusive interview with AEROREPORT, Michael Schreyögg, Chief Program Officer at MTU Aero Engines, talks about current trends and market influences within the engine maintenance world as well as flexibility, growth and pressure.
author: Victoria Nicholls | 7 mins reading time published on: 14.05.2024
author:
Victoria Nicholls
is an international communications expert. At MTU, she specializes in engine programs and market trends.
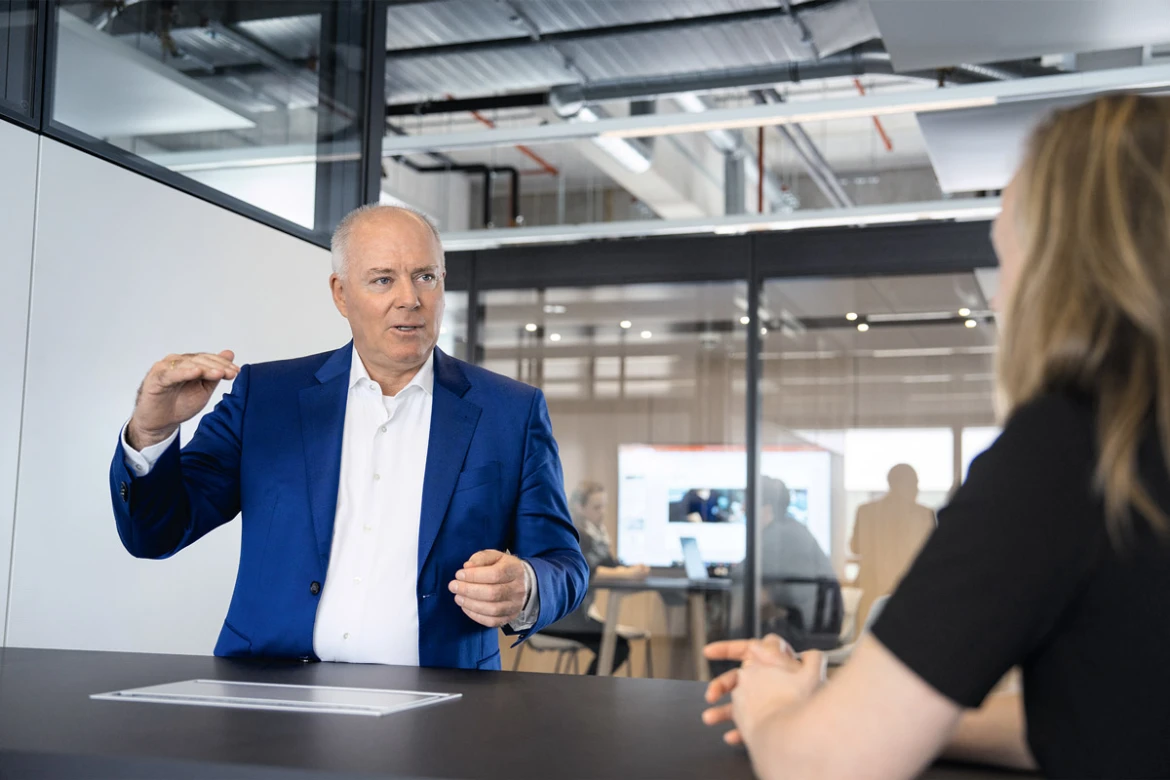
- Michael Schreyögg talks about current trends within the engine maintenance world
- On-site service: Mobile teams for urgent engine repairs
- MTU Maintenance: Training Programs Worldwide
- Technical customer training: trust through transparency and expertise
AEROREPORT: Following on from the pandemic, the aviation industry is back in full swing. Growth is occurring across the board and there is more demand than capacity in the market – from the backlogs of original equipment manufacturers to maintenance providers. And MTU, of course, is both. Where is this growth coming from?
Michael Schreyögg: The aviation industry is international, and at its core, it enables mobility – in the fastest and safest way worldwide. But more than that, it connects people. The growth of the industry essentially comes down to lots of people, wanting to travel and connect.
This was particularly apparent during the pandemic years, when travel was limited or non-existent. It’s something we all experienced, myself included. After weeks and months of isolation, we wanted to see our friends and family, and experience the world again.
Luckily, we are now back to pre-Covid levels. But the pandemic also had consequences for business, from the workforce to the supply chain. The world ground to a halt across the board, and many companies let go of staff. That wasn’t a switch that could just be turned on again.
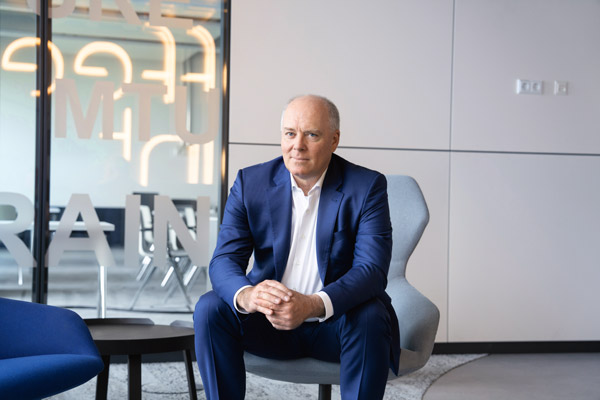
“We always believed in the fundamental strength of our industry. So we used every option at our disposal to retain our talented workforce and continue to invest in our facilities worldwide.”
Chief Program Officer at MTU Aero Engines
AEROREPORT: How did MTU deal with the situation?
Schreyögg: We always believed in the fundamental strength of our industry. So we used every option at our disposal to retain our talented workforce and continue to invest in our facilities worldwide. For instance, our new repair facility, MTU Maintenance Serbia, was built through the pandemic and opened in 2022.
And now that the industry is back on track, we’re working extremely hard to ramp-up at all levels. From our delivery of new engines and spare parts to serving our maintenance customers as efficiently as we can.
AEROREPORT: With so much going on, what is your focus for the rest of 2024?
Schreyögg: In a word: flexibility.
AEROREPORT: Meaning …
Schreyögg: Demand being higher than capacity is a “good” problem for companies. But it is also a tightrope when it comes to keeping customers and partners happy. So as an organization, we need to be flexible and find the best solution to meet all our commitments.
AEROREPORT: There is a fair bit of business jargon in that answer. Can you give us a concrete example of what you mean?
Schreyögg: For instance, the supply chain is under a lot of pressure. On the maintenance, repair and overhaul (MRO) side, that can mean, sourcing used serviceable material (USM) – in simple terms “used parts” – to fulfill part requirements when the engine is in the shop for an overhaul, instead of relying on new parts while there are persistent bottlenecks in the supply chain.
This sounds easier than it is, though, as the market for USM is very volatile and there is high demand at the moment. The team needs to be quick and it needs a good technical, financial, and market understanding.
“MTU Maintenance is many things: first, it’s an expert MRO organization that not only carries out necessary checks and repairs of aircraft engines, but also goes above and beyond to get the most performance and life out of the engine.”
Chief Program Officer at MTU Aero Engines
AEROREPORT: You just mentioned MRO. How would you describe MTU Maintenance in simple terms?
Schreyögg: Flexible. (laughs)
All jokes aside, MTU Maintenance is many things: first, it’s an expert MRO organization that not only carries out necessary checks and repairs of aircraft engines, but also goes above and beyond to get the most performance and life out of the engine. The team is the best at overhauling engines in the most efficient and cost-effective way for the customer.
Second, it’s a global network of facilities and on-site service centers. So it is international, fast and available 24/7. And it offers services for over 30 engine types – more than any MRO provider worldwide.
Third, it’s entrepreneurial. The teams are close to the customers and find innovative solutions to any problem – whether technical, in fleet management, or on the asset side, as a lessor.
AEROREPORT: MTU Maintenance will be turning 45 this year. What do you think is the secret to its growth and success?
Schreyögg: The people. It’s no coincidence that “expert”, “international”, “fast”, and “entrepreneurial” are all words you can use to describe a person or a team as well as an organization.
You may also be interested in following content
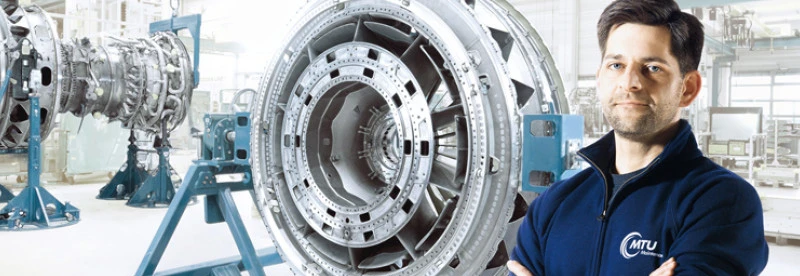
Customized service solutions for aero engines
MTU Maintenance is the global market leader in customized service solutions for aero engines.
AEROREPORT: What surprised you most when the MRO division of MTU Aero Engines became part of your program responsibilities back in 2016?
Schreyögg: The mindset. I have an engineering background, and I spent the lion’s share of my career on the OEM side of the business. MRO is a very different kettle of fish.
There’s a speed and urgency in MRO because it’s customer-facing. Every day that an engine isn’t flying costs a customer money. If they can’t use it, they need to find a spare engine from their pool or source a lease engine. In turn, the customer is very interested in the status of their engine and how soon they can have it back.
My experience has always been that our MRO colleagues always go that extra mile to make the customer happy.
AEROREPORT: Speaking of going the extra mile. MTU is focusing even more on its on-site service network, correct?
Schreyögg: Yes. We have an expert team who carried out well over 1,000 on-site events for over 500 customers last year across the MTU organization. Our aim is to significantly expand this offering in the coming years.
To do this, we’re consistently investing in the network, increasing capabilities such as the introduction of new engine types, tooling, certifications and authority approvals as well as facilities. For instance, MTU Maintenance Dallas moved to a new 41,000 square meter facility in 2023, which significantly increases our ability to support airlines in the region. MTU Maintenance Berlin-Brandenburg will introduce PW812D capabilities in 2024 and MTU Maintenance Service Centre Australia started work on CF34-10E engines last year, to name just a few examples.
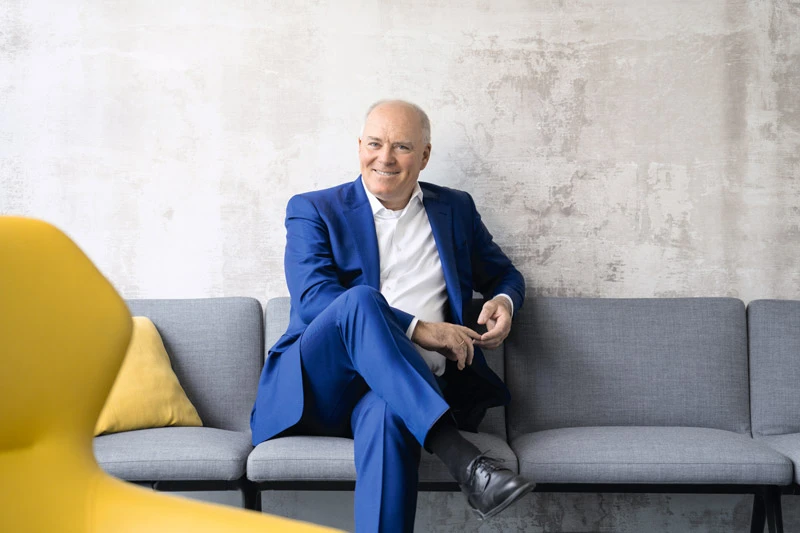
Going the extra-mile: MTU consistently invests in the MRO-network, increasing capabilities such as the introduction of new engine types, tooling, certifications, and authority approvals as well as facilities.
AEROREPORT: Could you explain the background to these growth plans?
Schreyögg: Of course. There are various factors that come into play here. One is the technology. The current generation of engines, such as the V2500 and CFM56, were designed and built to enable more on- or nearwing workscopes for faster and better maintenance for operators and more efficient repair processes have also been developed since they entered service. And this trend has continued in the newer generation of engines, such as the PW1100G-JM and the LEAP – with even more maintenance expected to take place in the field.
In addition, there are market influences. The pandemic created an increased focus on on-site services for cost reasons, as airlines were looking to avoid shop visits and keep their engines on wing for as long as possible. These were essentially “quick fixes” to delay more time- and cost-intensive shop visits.
It’s important to note though, that this is a balancing act. Due to life-limited parts, which are parts that have to be exchanged after a certain number of flight hours or cycles, a shop visit can’t be postponed forever. Also, if parts stay on wing too long, they can become worn to the point of no repair and need replacing, which can, in turn, also increase costs.
AEROREPORT: How can airlines manage this balancing act?
Schreyögg: The most important thing here is the dialogue between the customer and the MRO provider. The more transparency over requirements, status of engines and fleet plans, the better. We have a proprietary fleet management planning tool, CORTEX, which can create MRO shop visit scenarios for an entire fleet at the click of a button, and plan right down to the life-limited part level (parts with a restricted number of flight cycles before they need exchanging). It’s an extremely powerful and helpful tool that our customer support and engineering teams use in these discussions.
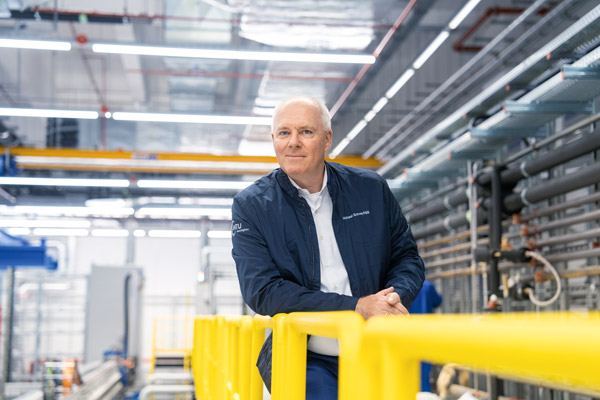
“Quality isn’t optional in our industry. It’s the basis of it.”
Chief Program Officer at MTU Aero Engines
AEROREPORT: But even a tool can’t help, when there is more demand than capacity in the market …
Schreyögg: Yes and no. MTU has an incredible range of services at its disposal. So while we might not be able to perform miracles at the drop of a hat, at least in the current environment, we can look at green-time [cycles remaining before parts must be exchanged and the engine needs to come into the shop], for instance. We then make a suggestion to a customer of perhaps switching engines to different aircraft in their fleet to maximize engine usage – in essence, winning additional time. Or we’ll look at leasing options, to give a customer immediate power and lift. Or on-wing maintenance to prolong time out of the shop. It all comes down to what I was saying before, flexibility is the key.
AEROREPORT: With all this pressure and growth, how can you ensure quality standards?
Schreyögg: Quality isn’t optional in our industry. It’s the basis of it. At MTU, we focus on structure and processes. For instance, on the on-site service side, we recently introduced a central organization unit. We also place huge importance on training, qualification, and knowledge sharing across our entire global network.
The passenger never sees us, and they may never know who we are. But they sure as hell rely on us to do our job properly. Their lives depend on it.