aviation
King Stallion flexes its muscles over the Atlantic
MTU has codeveloped the engine for one of the world’s most advanced and powerful helicopters: the Sikorsky CH-53K, nicknamed King Stallion. During endurance trials at sea, its three T408-GE-400 power turbines won approval from the US Marine Corps. They have ordered 200 of the helicopters designed for heavy lifting and marine operations.
author: Peter Sommerfeld | 4 mins reading time updated on: 03.07.2025
author:
Peter Sommerfeld
writes for AEROREPORT as a freelance journalist. He is especially interested in aviation topics and covers events and personalities from the farthest corners of the globe.
Pure power over the Atlantic
For a helicopter pilot, there’s almost no challenge greater than landing on a ship at night. When it’s dark, the pilot can’t use the horizon as a point of reference for above and below. And if the helicopter carrier is only dimly lit, touching down becomes almost a game of chance.
„The CH-53K’s flight control and stabilization systems meant the approach could be fully automated. I’ve never felt so safe in this scenario.“
Throughout his career, Major Joshua Foxton of the United States Marine Corps has trained for landings under these conditions onboard a Sikorsky CH-53E—a helicopter nicknamed Super Stallion that entered into service back in 1981. His training meant Foxton was well prepared when, a few weeks ago, he sat in the cockpit for an extensive test series in the North Atlantic to demonstrate the operational readiness of the helicopter’s successor: the brand-new CH-53K, or King Stallion. As part of the campaign, Foxton also landed the new helicopter in the dark. This time, however, something was different: the landing was surprisingly easy. Foxton barely had to do a thing. “The CH-53K’s flight control and stabilization systems meant the approach could be fully automated,” Foxton explained, clearly impressed. “I’ve never felt so safe in this scenario.”
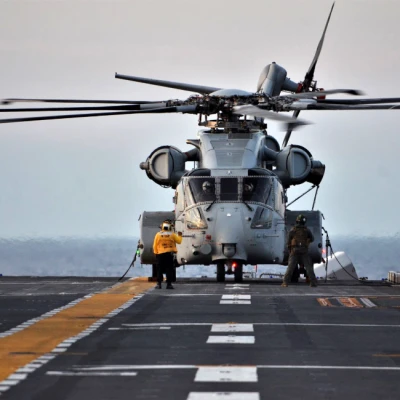
©U.S. Navy photo
„Fly-by-Wire": The CH-53K’s flight control and stabilization systems mean the approach can be fully automated.
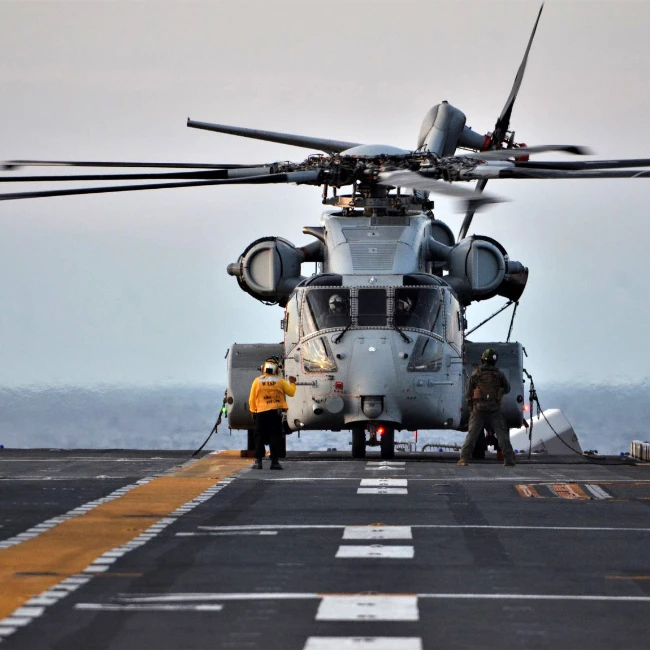
©U.S. Navy photo
„Fly-by-Wire": The CH-53K’s flight control and stabilization systems mean the approach can be fully automated.
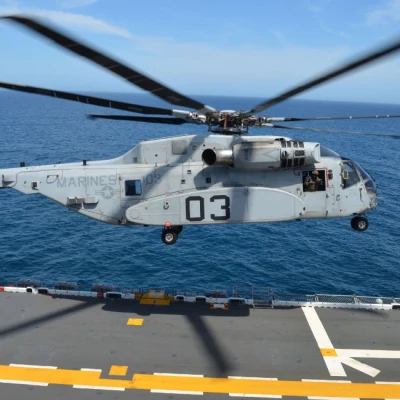
©U.S. Navy photo
Sea Trials: A total of more than 360 takeoffs and landings were completed on the USS Wasp helicopter carrier.
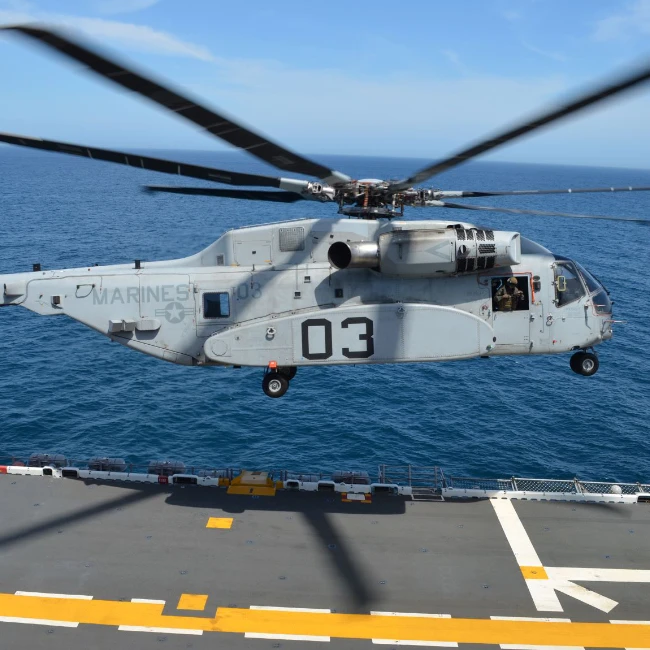
©U.S. Navy photo
Sea Trials: A total of more than 360 takeoffs and landings were completed on the USS Wasp helicopter carrier.
The electronic helicopter control system that made Foxton’s work so much easier is known as a fly-by-wire system. Even in extremely windy conditions, it proved to be a great help to him, as did the CH-53K’s tremendous power delivered by three T408-GE-400 power turbines. MTU developed the engine in partnership with GE Aviation.
The three T408s give the King Stallion the power to carry a 27,000 – pound external load over a mission radius of 110 nautical miles—at high altitude and in hot weather conditions. “Its external load capacity is three times greater than that of the current model, the CH-53E Super Stallion, which is powered by legacy T64 engines,” says Wolf Baenkler, T408 program manager at MTU. Compared with the T64, the T408 delivers 57 percent more power; its specific fuel consumption is 18 percent lower and it has 63 percent fewer parts. It also has a more robust design to increase durability and resistance to sand erosion and salt water corrosion, thus offering the optimum properties for withstanding the tough operating conditions the US Marine Corps will subject it to.
Collaboration between MTU and GE Aviation on the Sikorsky CH-53 helicopter dates back to the 1970s. On July 26, 1972, the German Armed Forces took delivery of its first helicopter from a total order of 112 units. CH-53G is the designation for the variant developed exclusively for the German market and manufactured under license solely by German companies. Ever since then, MTU has been responsible for producing and maintaining the T64 engine that powers Germany’s CH-53s. MTU engineers have worked on optimizing the T64s deployed in Germany over the years and now, the upgraded engines powering the German fleet are flying with MTU modifications.
When the Marine Corps decided to fundamentally upgrade the Sikorsky CH-53, including a completely new engine, GE Aviation brought MTU onboard as a development partner in 2008, not least given their successful collaboration in the past. This was the first time that MTU entered into a risk-sharing partnership (RSP) with GE in the military sector.
Although the CH-53K King Stallion is a clean-sheet development, from the outside it looks almost identical to its predecessor and even has the same dimensions. The reason is that the Americans wanted to continue using the helicopter on their carriers without having to make any major modifications, Baenkler explains.
The Marine Corps has ordered 200 of the helicopters from Sikorsky. Each unit has three active engines and one replacement, which corresponds to a total order volume of 800 power turbines for MTU to manufacture. “MTU is proud to be supporting GE Aviation and the US Marine Corps with this pioneering engine,” said Wolfgang Gärtner, who heads up engine programs for military helicopters at MTU. During the sea trials, Foxton and his fellow test pilots completed more than 360 takeoffs and landings on the USS Wasp helicopter carrier. “The helicopter is fit for purpose and delivers,” Gärtner says. “It has passed all the key milestones in flight testing and to demonstrate its mission capability. The CH-53K has proven what it can do.” Its performance has long since won approval from the US Marine Corps, which plans to put the first of its 200 helicopters into service in late 2023 or early 2024.
T408 turboshaft engine
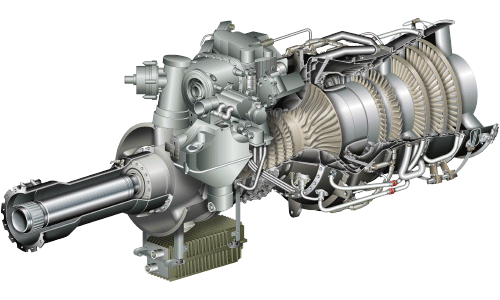
FEATURES:
- Turbo-shaft engine with free power turbine
- Five-stage axial compressor, single-stage centrifugal compressor
- Annular combustor
- Two-stage gas generator turbine
- Three-stage power turbine
- FADEC (Full Authority Digital Electronic Control) with health monitoring functions