aviation
MTU and German Armed Forces celebrate their 20-year EJ200 collaboration
This successful maintenance collaboration between MTU and the German Air Force integrates both military personnel and MTU employees into the workflows.
author: Thorsten Rienth | 5 mins reading time published on: 04.05.2022
author:
Thorsten Rienth
writes as a freelance journalist for AEROREPORT. In addition to the aerospace industry, his technical writing focuses on rail traffic and the transportation industry.
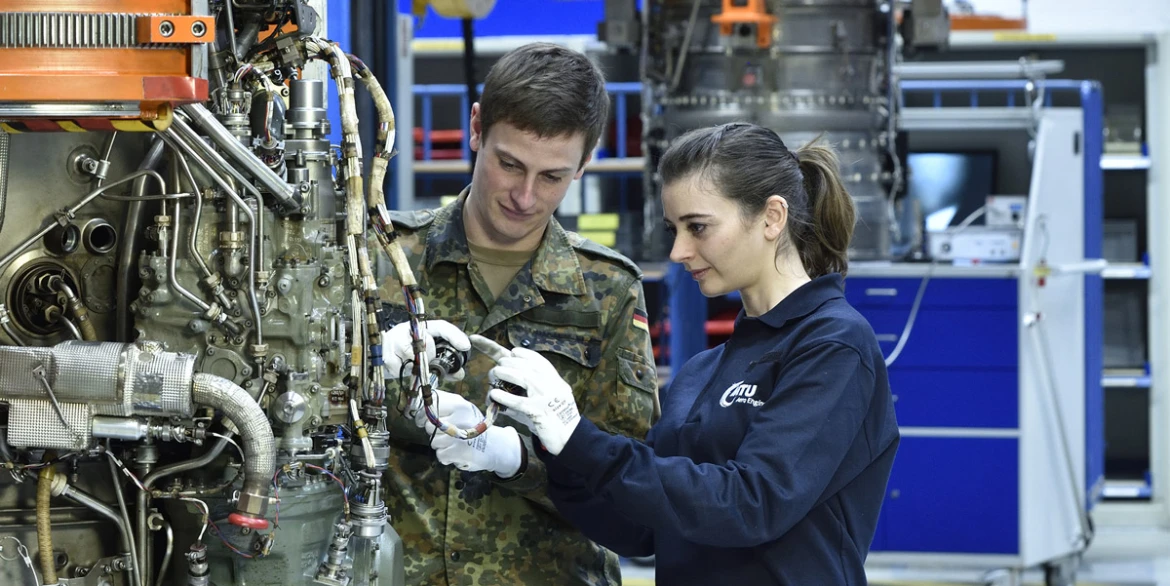
The two men are colleagues, that much is clear. One controls the hoist, while the other stands at eye level with the gap that is about to close between the high- and low-pressure compressors. These two modules were separated for repair; now it’s a question of aligning the fixing points to join them back together. A couple of finger gestures are all that’s needed to communicate what’s required. The collaboration taking place in the MTU Aero Engines operational facility at the Erding airbase might be seamless, but the people involved are fundamentally different: one is wearing German military gear, the other MTU coveralls.
20 years of successful collaboration
“A good 20 years ago, this kind of collaboration was virtually unthinkable,” says Lieutenant Colonel Stephan Schmidt. “Military and industry were understood as customer and service provider. One paid and the other delivered.” But in 2002, the lines separating the two shifted and a new chapter began—at least in the history of repairing the EJ200 engine for the Eurofighter. The EJ200 marked the dawn of a new kind of collaboration between the German Armed Forces and MTU, one that integrated military personnel alongside MTU employees into the company’s workflows. Today, Lieutenant Colonel Schmidt is the military coordinator for this collaboration, which is unique in Europe.
Schmidt’s “civilian” counterpart is Mario Külgen, who manages the agreement between the engine manufacturer and the German Armed Forces and oversees the systematic integration of military personnel into MTU processes. “Although MTU bears the overall responsibility for the repair package, the military personnel—predominantly technical officers and engine mechanics—still report to the German Air Force,” Külgen explains.
Completing the trio is Michael Hergeth, who heads MTU’s operation facility in Erding and is responsible for ensuring the repair work is performed. “In addition to actual engine repairs, the work package covers spare parts management and forecasting, damage inspections, product monitoring, and quality assurance,” Hergeth explains. “But these take place at MTU’s location in Munich, where military personnel assigned to the collaboration are also integrated into the relevant teams.” Besides the switching out of engines at the aircraft, the only other tasks handled by military personnel at German Air Force locations are smaller checks and the exchange of accessories.
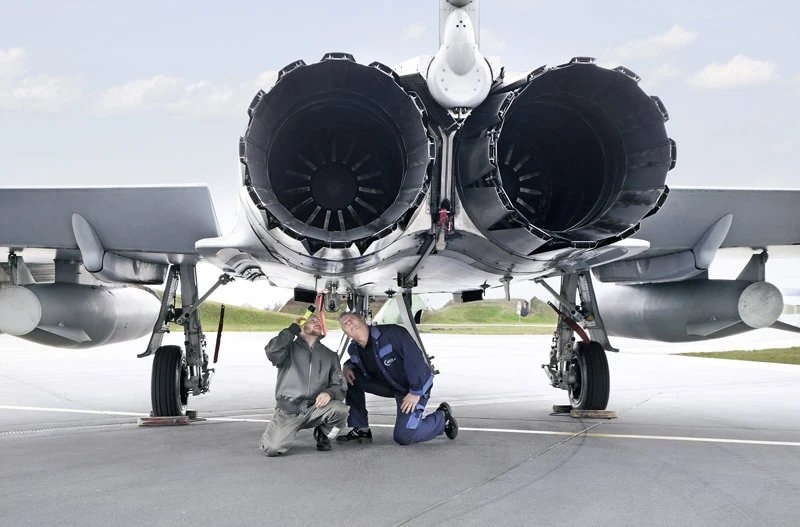
Engine specialist: As a rule, MTU’s involvement in the German Air Force’s military engines stretches back to their development—as here with the EJ200 for the Eurofighter.
When looking for an industrial partner, MTU is the first choice for the German Armed Forces
Back in the late 1990s, the German Federal Ministry of Defence, the German Air Force, the BWB (which was then the procurement office for the German Armed Forces), and the German Aerospace Industries Association (BDLI) laid the foundations for the collaboration. From then on, it was not just the fighter’s price tag that was relevant: its operating costs were now also being examined. Engine maintenance represents a large portion of those costs.
Up to that point, the German Armed Forces had always maintained some of its engines itself, with the others going to its industry partner. This meant that two separate infrastructures existed for the same job—one in the MTU shops, the other at Air Force locations. Wouldn’t it be better to consolidate operations at a single location, to pool expertise instead of everyone doing their own thing?
“Of course,” answers Lieutenant Colonel Schmidt. He highlights what the priorities of the German Armed Forces are: “It relinquishes the maintenance work, but not the skills. It is still involved in the engine types and remains a knowledgeable customer.” This is important because the German Armed Forces must possess the skills it needs to get the job done in any situation at any time, even in remote places.
When looking for an industrial partner, MTU is the first choice for the German Armed Forces. The company’s collaboration with the German Armed Forces dates back to 1959, the same year that the J79 engine for the Starfighter was first produced under license. Then came the RB199 for the Tornado, the Tyne engine for the Transall and the TP400-D6 engines for its successor, the Airbus A400M. There was also another factor that impacted the selection: as a rule, MTU was already involved in developing these engines. “And who could be more suitable to maintain the engines than the manufacturer itself?” Hergeth says.
A partnership of convenience to one of excellence
Hergeth, Schmidt and Külgen all agree that the collaboration provides the German Armed Forces with plannability and cost-effective maintenance, and MTU with a system partnership and a stable contractual arrangement.
Beyond the EJ200, this also now applies to the RB199 as well as the MTR390 for the Tiger helicopter, which were incorporated into the collaboration in subsequent years. Every month, the repair collaboration handles up to nine EJ200 engines, up to five RB199 engines and up to three MTR390 engines.
It’s no secret that the collaboration started out essentially as one of convenience. “But we’ve long since become real partners—not just in the way we act, but also in the way we think,” Hergeth explains. “Our goals are absolutely in sync: to get the engines back on the wings—or, in the case of the Tiger, back under the blades—as quickly and cost-effectively as possible and in the best quality we can achieve.” What’s more, the collaboration can also claim to be measurably successful: “In the first ten years, for instance, we doubled the RB199’s on-wing time,” Hergeth reports. “Its reliability increased by 20 percent over the same period. And these values have remained stable to this day.”
“We always arrive at a joint solution.”
Touring the hangars at Erding airbase with Schmidt and Hergeth, it quickly becomes clear that much of the collaboration’s success lies in the chemistry between the partners. “I’ve known the German Armed Forces since I did my own military service. I like the mutual respect and the pragmatic mentality that you encounter there,” Hergeth says. For his part, Schmidt values Hergeth’s appreciation of how the German Armed Forces works and that he understands why a military operation sometimes has to follow different rules than an industrial one. Their offices are within hailing distance of one another. Not that anyone’s barking orders here.
Külgen also sees the close ties between MTU and the German Armed Forces as being one of the collaboration’s key success factors: “I’ve had one foot in the military for 25 years now as a reserve officer. Here we just really know where we stand with each other.”
Meanwhile, the two modules the German Armed Forces airman and the MTU engine mechanic were working on have been reconnected. These are then joined by the other engine modules: fan, combustor, turbine, afterburner—one after another until the engine is reassembled. On their way back to the Eurofighters, the engines just have to make one minor detour. The newly repaired engines still have to go through acceptance testing at the EJ200 test stand at MTU in Munich.