innovation
At DigiLab, MTU is bringing digital innovations to life
DigiLab is a space for experimentation in which employees can try out new technologies. This is where technology acronyms like AR, VR, KI and IoT are brought to life.
author: Tobias Weidemann | 5 mins reading time published on: 06.05.2022
author:
Tobias Weidemann
has been working as a journalist and content consultant for more than 20 years. He writes about technology and business topics, often with a focus on business IT, digitalization and future technologies.
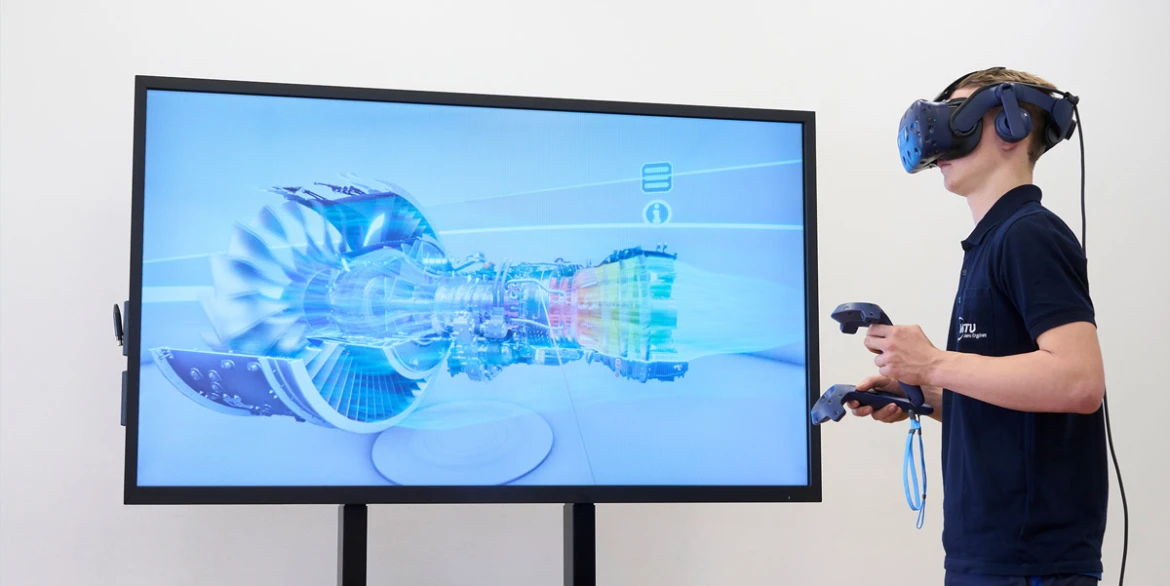
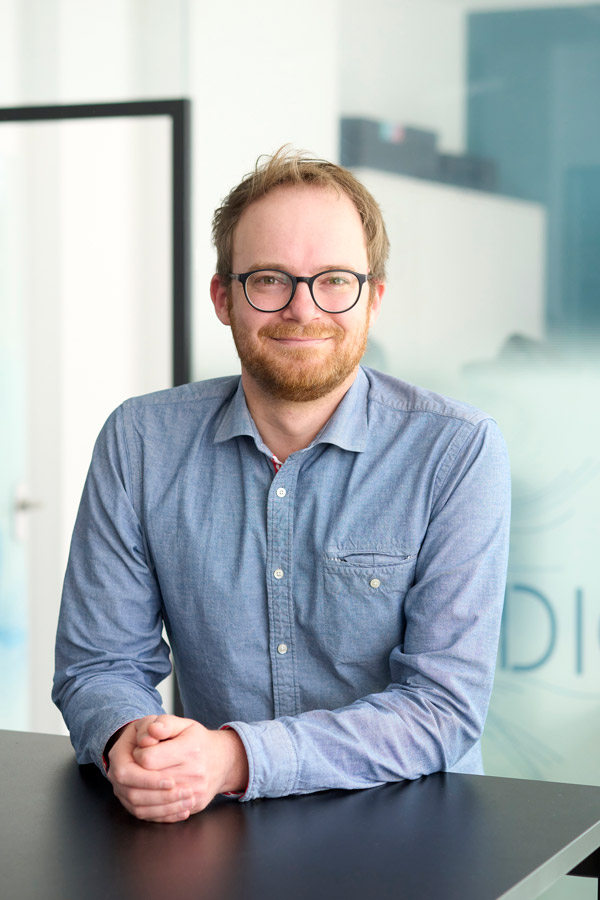
“This allows us to build up experience with new technologies and trends so that we can then decide whether to roll them out on an industrial scale in the relevant department,” says Martin Roth, Head of DigiLab at MTU Aero Engines.”
Head of DigiLab at MTU Aero Engines
“DigiLab is where we can run practical experiments designed to put digital innovations through their paces. This allows us to build up experience with new technologies and trends so that we can then decide whether to roll them out on an industrial scale in the relevant department,” says Martin Roth, Head of DigiLab at MTU Aero Engines. He’s describing the ethos of the digitalization lab, which MTU established at its Munich site around two years ago.
DigiLab is packed full of high-tech devices: a few computers, multiple large displays, a flatscreen for presentations, several pairs of smart glasses and other peripherals. There is also a rack containing a SINUMERIK CNC system for simulating manufacturing machinery. DigiLab’s equipment can be used for a host of applications, offering realistic representations for production and Industry 4.0 topics. These include the testing of new security tools and cloud connections, the digitalization of older machines through IoT devices and open source software solutions, and the analysis of errors that occur in a production environment.
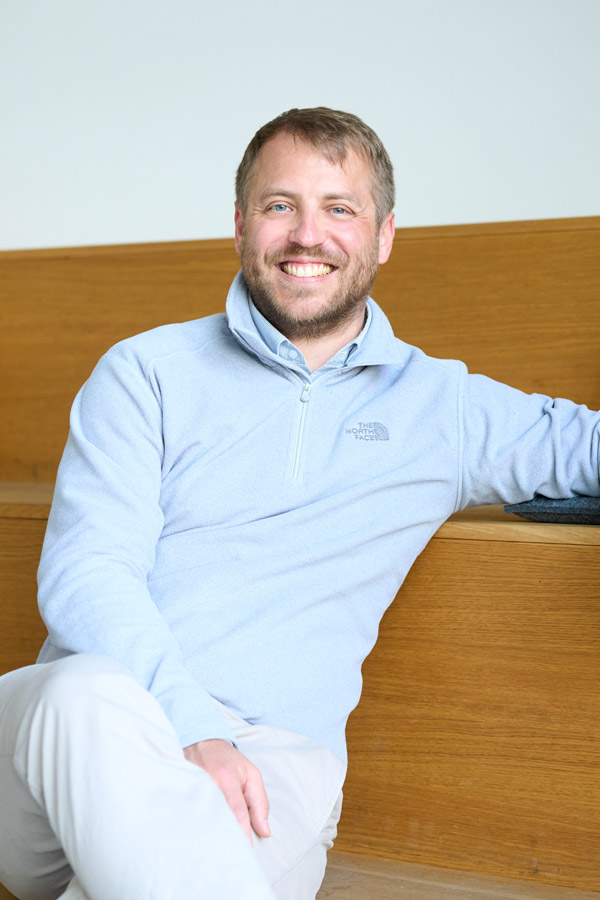
“Working in a kind of safe mode, we can try out any future-defining technology that’s on the market”
Deputy Head of DigiLab at MTU Aero Engines
Experimenting in a safe environment
By design, DigiLab is not connected to MTU systems and does not use corporate data. This means DigiLab does not have to comply with all the regulations that apply to the rest of MTU, so it can execute experiments and projects faster and more flexibly. DigiLab sometimes uses dummy data sets and simulations. “Working in a kind of safe mode, we can try out any future-defining technology that’s on the market—augmented reality, virtual reality, and a host of applications based on AI or related to the Internet of Things,” says Roth’s deputy Michael Bender. Although he uses a lot of buzzwords, he also makes it clear that DigiLab provides everyday infrastructure and IT resources. In this way, its mission is to bring technology to life while also allaying people’s concerns about it.
In addition to being in charge of DigiLab, Roth and Bender are also the contacts for people interested in using the space. They have another colleague who handles the IT security and infrastructure behind the scenes. DigiLab is open to MTU employees as well as to external project partners—on-site, online and free of charge. Over the past two years, DigiLab has received around 60 inquiries of all different kinds. Some were from employees looking to test how new hardware and software fit into their workflows. Others were from departments wanting to test elements of machine control before launching major projects or investing precious time in production. Then there were works councils that wanted to see a future technology in real life and have it explained to them instead of discussing it in the abstract.
Support for a quality management tool
Despite the pandemic, DigiLab can boast a number of successes in the two years since it opened. For instance, the lab helped introduce a new quality management system for all production activities at all sites. This uniform quality platform is being systematically rolled out across all MTU locations. Integrated Quality Planning (IQP) was selected as a lighthouse project in the area of digitalization, one that will enhance MTU’s efficiency in the future.
As part of the project, a number of existing software solutions were evaluated and tested to determine their suitability for MTU. Given the size of MTU as an industrial company, and the sheer range of specifications and compliance rules it must follow, this task was anything but trivial. “DigiLab carried out exhaustive tests on a demo version provided by the vendor to ensure that IQP delivered what it promised, met the company’s requirements and not least demonstrated the necessary adaptability,” says project manager Alexandra Wacker. It was even possible to perform tests while working from home, which was “very fortunate in terms of keeping the project on schedule,” she adds.
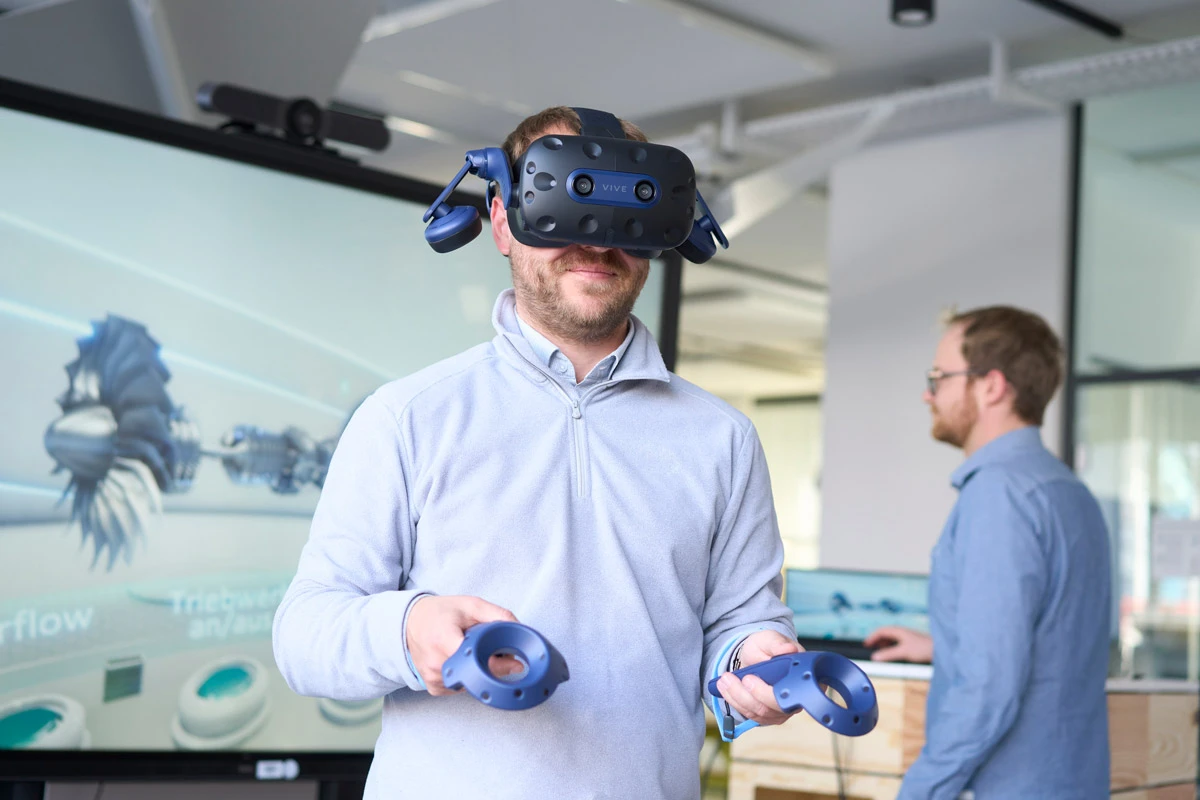
An introduction to technical terms
The term artificial intelligence (AI) applies to applications in which machines generate results similar to those produced by human thought, learn to better understand human behavior, and develop problem-solving skills. This includes machine learning as well as deep learning, which uses neural networks that help machines execute complex active learning tasks.
The Internet of Things (IoT) is the collective term for connected devices, machines and systems. It provides an automated way of gathering and linking relevant information and operating data from the real world in order to generate value and support users.
There is also the Industrial IoT (IIoT), which—instead of dealing with applications concerning individual people—focuses on industrial systems. Here it’s about process optimization, cost-effectiveness and production monitoring.
Virtual reality (VR) enables users to experience a virtual world in 360 degrees, to view it from every angle, to move around within it and to interact with it. Users feel removed from their actual environment, as if they have been transported into the virtual world.
Augmented reality (AR) simply enriches the real world with virtual content, which means users need to be present where the action is taking place. AR then overlays their perceptions of their real-world environment with real-time information in the form of text and graphics. This means, in contrast to VR, that AR users remain grounded in physical reality.
“Building on our preventative and reactive quality methods, in the future we want to set up a systematic comparison between errors that are predictable and those that actually occurred. We expect that as a result, the production errors employees document now can be avoided altogether in the future,” Wacker continues. The new software supports failure modes and effects analysis (FMEA), a strategy for detecting and assessing potential errors in design and production processes before they happen. “In the past, we had a whole range of complementary tools and workarounds, some of which we developed in-house. But now we are replacing these island solutions with comprehensive software from a single source,” she says.
Explaining the basic functions of engine technology
Not quite as comprehensive and extensive, but considerably more tangible, is another project that was completed only a few weeks ago in collaboration with MTU’s training program. In the future, the company’s apprentices in engine technology will be trained using a dynamic virtual engine model of a turbofan engine. This is made possible by virtual reality headsets and the corresponding VR model, which was converted into a dynamic model with the help of the MTU DigiLab as part of a master’s thesis.
The VR model is based on the PW1100G-JM—a member of the state-of-the-art Pratt & Whitney GTF™ engine family—which powers the A320neo. Fundamentally, it’s about making basic functions understandable and allowing apprentices to grasp the technical concept behind them. Apprentices can turn the engine on to study the way the air flows and the parts move, and can take out the individual modules. The exploded-view diagram showing the separate components also features infoboxes containing detailed technical data. The headset adjusts the 3D image with each head movement, revealing further technical details about the engine.
The model has been used in the MTU training shop since March. “It would simply be too expensive to have a real one of these engines available for training purposes,” explains trainer Markus Voag. He also acknowledges the 3D model’s educational value: “Allowing young people to experience the benefits of this kind of technology might make them more open toward virtual reality applications later on in their career.”
For Martin Roth, bringing the inner workings of an engine to life is a perfect example of what DigiLab can do in the race for the best and the brightest: “Given the lack of qualified engineers in a variety of specialties, DigiLab is a valuable tool in demonstrating MTU’s attractiveness and innovative strength to the next generation, and it underscores that we offer exciting career options.”