good-to-know
Engine materials
Engine materials have to meet extraordinarily demanding requirements. But what are the most important materials today—and which ones will be in the future? AEROREPORT provides a list.
author: Isabel Henrich | 8 mins reading time published on: 04.10.2022
author:
Isabel Henrich
studied political science and communications. At MTU, she coordinates the editorial process of AEROREPORT and is responsible for the conception and development of its content.
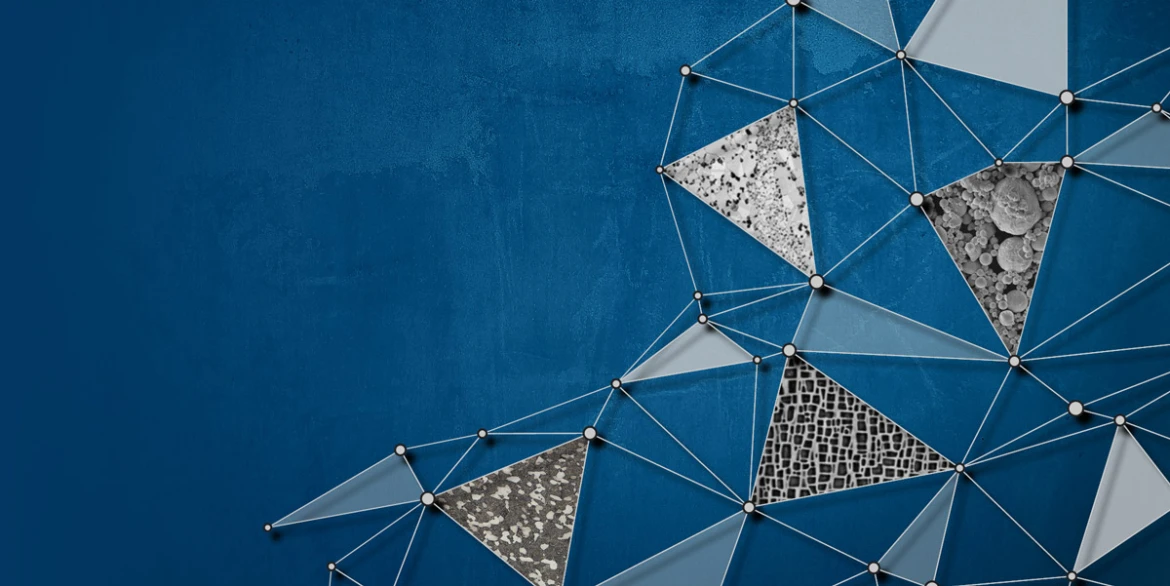
For several decades, metallic materials such as nickel and titanium have been part and parcel of engine components. These tried-and-tested materials are continuously being optimized to make engines lighter and more cost-efficient.
The second-generation geared turbofan, which is set to take off at the beginning of the next decade, and the Next European Fighter Engine (NEFE for short), a future military engine, require components that are even more lightweight, durable and heat-resistant. What’s more, the materials are set to become more robust in terms of both manufacturing and operation. Here, the focus will be on improved nickel superalloys and coatings, manufacturing processes such as monocrystalline casting and powder metallurgy as well as additive manufacturing and fiber-reinforced materials. These help reduce weight while allowing for a longer service life at higher use temperatures.
In commercial engines, future challenges also include the new atmospheres the components will find themselves in. In MTU’s water-enhanced turbofan, a gas turbine engine with energy recovery and wet combustion, as well as in direct hydrogen combustion, the components are exposed to an environment with a high water vapor content and come into contact with more molecular hydrogen than in conventional gas turbines. This calls for special coatings to sufficiently protect the materials against accelerated oxidation as well as corrosion and embrittlement. For the flying fuel cell (FFC), another revolutionary MTU propulsion concept, additional, completely new materials with new functions are needed in engine construction. This calls for novel components such as hydrogen fuel cells, cooling systems and high-performance electric engines complete with sophisticated power electronics for the propulsion system. Electrification of the powertrain, meanwhile, gives a key role to functional materials with specific electrical, chemical, magnetic and catalytic properties.
To reduce the effort required for development, to continuously optimize the materials and to enable more efficient quality assessments, it is essential to employ further improved computer simulations.
AEROREPORT introduces the most important engine materials and related methods—whether they are already in use or still a long way off.
1. Nickel, titanium and their manufacturing options
1.1 Nickel-based superalloys:
Nickel-based superalloys are materials that are almost two-thirds nickel. They are typically alloyed with a great number of additional elements that enable the reticulate microstructure that is characteristic for these metals. Different processes are used to manufacture these materials, including casting (as monocrystals or otherwise), forging, powder processes, additive manufacturing and injection molding.
Benefits: The most prominent characteristic of nickel-based superalloys is their high strength, which remains unimpaired even at very high temperatures. This is due to their special, fine microstructure. They also have good corrosion resistance. These two qualities are the primary reason why they are favored over steels in engine construction.
Areas of application in the engine: All component types, especially in the hot area of the engine, for instance in the rear compressor, the combustor and the turbine.
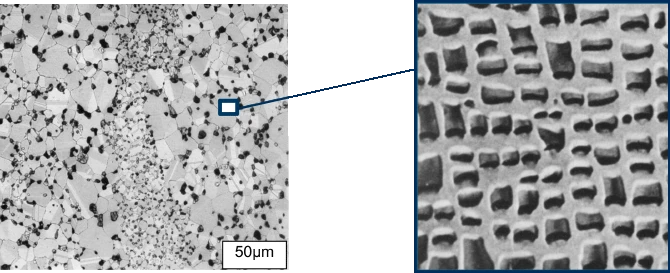
Typical material structure of a nickel-based superalloy. The magnified image shows the characteristic, microstructural property of the cuboid γ‘ precipitate (precipitation: an intermetallic phase) in the metallic γ matrix. In addition to heavy alloying elements, this special structure enables high strengths even at high temperatures.
1.2 Monocrystalline nickel-based superalloys:
These materials are manufactured in special casting procedures without grain boundaries, that is, as a single crystal. This is why they behave anisotropically—meaning their behavior is direction-dependent. Typically, they are intended for use at ultra-high temperatures and therefore require protective coatings. They also owe their properties to some particularly expensive and heavy alloy elements.
Benefits: With no grain boundaries to weaken them, through the addition of special, heavier elements, and with the option to purposefully exploit their anisotropic behavior, monocrystals can be used at ultra-high temperatures close to their melting point.
Areas of application in the engine: Components exposed to ultra-high temperatures in the front part of the turbine, especially as rotating and static airfoils.
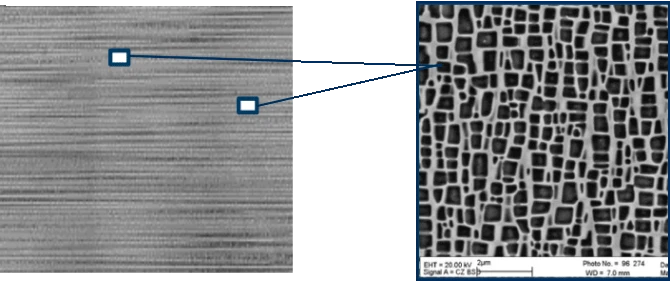
As a special case of nickel-based superalloys, the images show the structure of a single-crystal material. On the left, the absence of grain boundaries is apparent; on the right, the reticulate microstructure of the γ‘ precipitates, which is particularly distinct in monocrystalline nickel alloys.
1.3 Titanium alloys:
The main component of titanium alloys is titanium. The alloy elements added in engine construction and the manufacturing parameters chosen enable the creation of very different, typically lamellar or globular microstructures with different benefits. The forms and relative proportions of the microscopic phases involved play the key role in this. While titanium is an element commonly found in the Earth’s crust, it reacts readily with oxygen. This makes the extraction of pure titanium expensive, a factor that needs to be considered in manufacturing and operation. The manufacturing processes for titanium alloys are the same as the ones mentioned in connection with nickel alloys, with the exception of monocrystalline casting.
Benefits: Titanium alloys are about as strong as nickel-based alloys but only half as heavy. And they are highly processable as well as corrosion-resistant. Their maximum use temperature, however, is much lower than that of nickel alloys. Due to their corrosion resistance and strength, titanium alloys have an advantage over steels and aluminum.
Areas of application in the engine: All component types, especially in the front part of the engine all the way to the intermediate-pressure compressor.
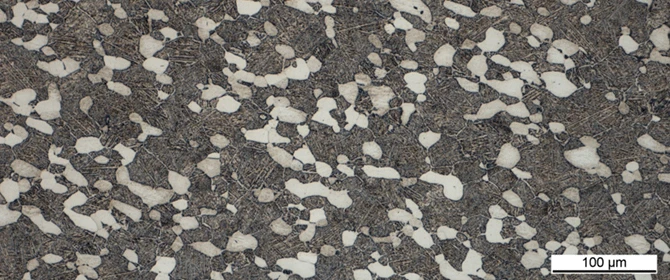
The structures of titanium alloys in aircraft engines are distinguished by the ratio and structure of two phases (α/white und β/dark). Typically, these structures are lamellar and globular. The image shows a mix of both manifestations known as a bimodal structure.
1.4 Powder metallurgy materials:
Powder metallurgy produces powder particles from smelt by way of atomization. Aviation employs different processes such as hot isostatic pressing (HIP) followed by forging, additive manufacturing (AM) or metal injection molding (MIM) to make components from these particles. Many of the metals described above—or modifications of these metals—lend themselves to chemical compositions.
Benefits: Powder metal manufacturing allows for compositions and qualities that are simply out of reach for other manufacturing methods. This leads, for instance, to fine-grained, homogenous materials with particularly desirable mechanical and thermal properties. Those techniques that no longer forge the powder but give it the shape of the end product straight away come with an additional benefit: by being near net shape, they save expensive material and processing time.
Areas of application in the engine: Powder metallurgy is suitable for various constituent parts of different components due to the range of materials and processing techniques that can be employed. Depending on the process, it is typically used to make components with a complex geometry or particularly high requirements.
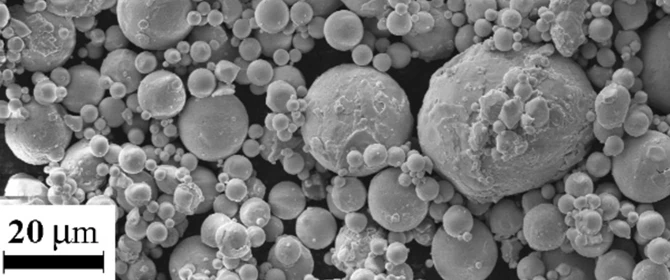
Metallic powder particles (here: nickel-based superalloy). Quality characteristics include, above all, purity from foreign particles, diameter distribution, shape and surface texture as well as the chemical distribution and structure inside the particles.
1.5 Additively manufactured materials:
In additive component manufacturing, material is gradually positioned and combined with the material already present. This can be done by melting wire or powder particles using a laser or an electron beam, and it requires special attention in terms of quality control. The materials used cover a broad spectrum, including in particular the metals described above as well as plastics for demonstration purposes.
Benefits: This process enables complex geometries that are mostly near net shape and can achieve a high material yield, provided adequate recycling arrangements are in place. If needed, it can also be used to manufacture alloys that cannot be processed any other way as well as to modify and adjust the quality of the materials in the component depending on position and exposure.
Areas of application in the engine: Due to the range of materials that can be employed, additively manufactured materials are fundamentally suitable for a wide range of constituent parts across various components. When it comes to complex geometries, their relatively low cost and weight compared to conventionally manufactured materials make them an attractive choice. Moreover, additive techniques make it possible to prepare and modify small batches at short notice, for example in demonstrators.
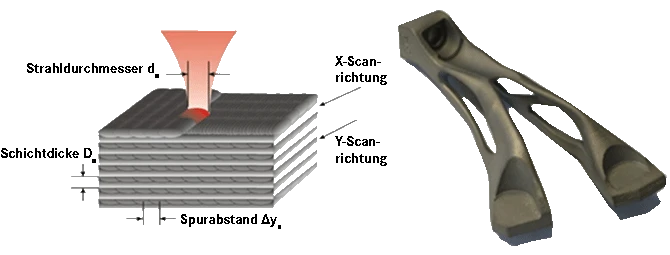
Left: Additive material buildup: in this example, a laser is used to melt successive layers of locally applied powder.
Right: Additive manufacturing offers high degrees of freedom when it comes to manufacturing complex structures for lightweight construction.
2. Fiber-reinforced polymers as an example of composite materials:
Fiber-reinforced polymers are composite materials, which means they consist of two completely different components. High-strength fibers made from different materials, such as carbon, that have been woven together in different ways are embedded in a polymer matrix. These materials are highly anisotropic and, despite their complex manufacturing process, usually no more expensive than the special metallic alternative materials in the engine.
Benefits: Very low weight, high anisotropic strength, high damage tolerance in terms of the matrix itself—but less plasticity than metals.
Areas of application in the engine: Lower-temperature components whose geometries can be manufactured using the usual technique. This means that the target components are located in the front part of the compressor and the surrounding components. Additional measures must be taken to protect the components against foreign particles and the effects of great stress.
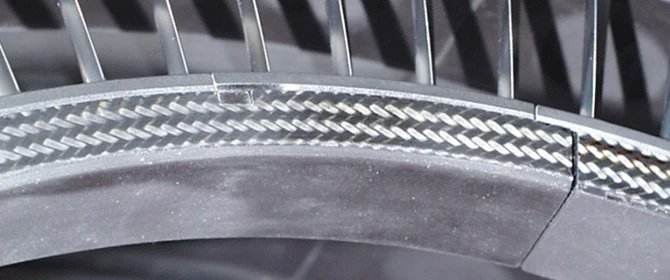
Fiber-reinforced polymers consist of two completely different components: strong, interwoven fibers that are embedded in a polymer matrix. This structure can be observed on the surface of an inner ring, as in this example.
3. Functional materials:
Functional materials are a broad field. These are materials that—unlike structural materials—are valued not so much for their load-bearing capacity or their form but for the function they perform for neighboring materials or the system as a whole. Coatings, for instance, are functional materials, as are engine materials and components that perform electrochemical, magnetic or acoustic functions.
3.1 Coatings as an example of functional materials:
The coatings in engines are especially diverse in their materials, manufacturing processes, structure and function. For example, polymers, metals and ceramics are sometimes used in combination. Coatings are applied by diffusion, spraying, vapor deposition or in semi-liquid form; under the microscope, they can look homogenous or highly structured. Over 60 percent of engine components are coated.
Benefits: Coatings increase the service life of engine components by a large factor, protecting them in a variety of ways: they improve the components’ resistance to mechanical abrasion caused by foreign particles or neighboring components, prevent chemical attacks such as corrosion and oxidation, insulate against thermal loss and retard fire. Coatings can also compensate for material lost to abrasion.
Areas of application in the engine: Almost anywhere within the engine as well as for all components according to the functions described.
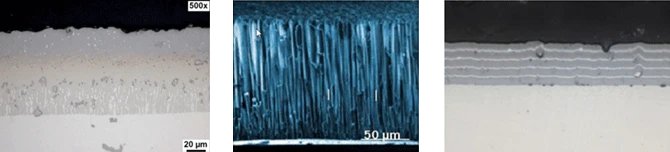
Protective coatings in aircraft engines feature a great variety of materials and structures. By way of example, the image on the left shows an aluminous protective coating against corrosion brought about by diffusion into the base material; depicted in the middle is an evaporation-deposited ceramic insulation layer that has taken on a rod-like structure; and the image on the right shows a protective coating against erosion applied in layers with alternating hard and more damage-tolerant coating components.
4. The cross-material approach of simulations:
Materials simulations encompass all computer-aided analyses concerning the creation of a material and the description of its properties. Since a material’s behavior is determined by a combination of structures at different, microscopic scales—right down to the atomic level—different mathematical physics methods are necessary. The development of these methods remains extremely dynamic today, not least because of the many different material classes and long computing times. Terminologically, materials simulations belong to the digital material technologies and are associated with the field of integrated computational materials engineering (ICME) because of the way they link chemistry and manufacturing.
Benefits: When it comes to developing a material and its manufacturing process, materials simulations significantly shorten the iteration phase by reducing the number of tests that need to be run on sample materials. Furthermore, they help achieve the optimum between the material’s potential and cost-efficient manufacturing. Ultimately, they make quality assessments for design, manufacturing and operation faster and more accurate.
Areas of application in the engine: Basically, all materials and positions, but not yet available for all materials and issues due to the current state of development.
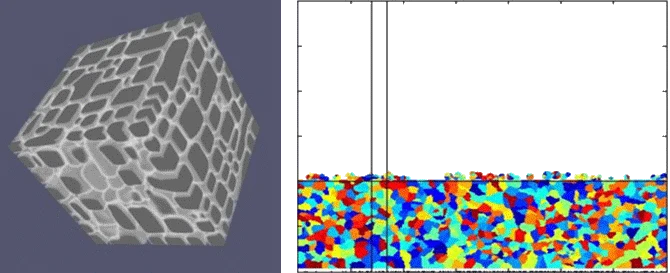
Materials simulations help predict the structure of a material. The image on the left shows the computer-generated γ/γ‘ microstructure of a nickel-based monocrystal; the image on the right depicts the formation of an additively manufactured grain structure by means of a laser hitting the powder bed on the surface at a vertical angle. The colors mark the different orientations of the monocrystalline grains.